Different oxidizer technologies are used on various applications in the chemical process industries (CPI) for the destruction of volatile organic compounds (VOCs), hazardous air pollutants (HAPs) and odorous emissions. Selecting the proper oxidizer technology is no longer just a function of regulatory compliance. With cap-and-trade legislation and higher fuel prices looming, it is critical that facilities know which type of oxidizer will keep their carbon footprint to a minimum and lower operating costs, says Kevin Summ, marketing manager with Anguil Environmental Systems, Inc. (Booth 858; Milwaukee, Wisc.).
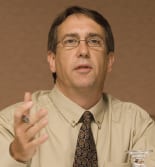
Rich Grzanka, a regional vice president of sales and a degreed engineer with Anguil Environmental, will be leading a workshop, which will discuss the pros and cons of three oxidizer technologies, including thermal, catalytic and regenerative thermal (RTO) oxidizers, on Tuesday from 2 to 2:30 p.m. in Theater A.
Summ mentions that some experts argue that while oxidizer systems prevent hazardous chemicals from being released into the atmosphere, they also emit significant amounts of CO2 and NOx. The presentation will explore this possibility and discuss how newer technologies and certain features can help oxidizers achieve self-sustaining, fuel-free destruction. RTO technology will be a strong focus of the workshop, as it is generally considered the most energy-efficient control technology due to its ability to capture heat from the purified exhaust air and pre-heat incoming airflow.
The presentation will also examine the typical emission streams found at chemical facilities and evaluate each oxidizer type for those specific applications. In addition, Anguil’s engineer will focus on operating cost-reduction strategies and the different options that plants should consider in an effort to reduce greenhouse gas emissions. According to Summ, some of the techniques to be discussed include making modifications, turning off the oxidizer burner, concentrating high-volume, low-VOC airstreams prior to the oxidizer, improving primary heat recovery, considering secondary heat recovery and proper maintenance of existing systems.
“Making modifications or efficiency improvements to process equipment such as re-circulation or heat recovery is an excellent way to not only reduce your operating costs, but also your carbon footprint,” explains Summ.
Also discussed will be the use of a concentrator, which can help reduce the heat input required by oxidizers. As a result of recent regulations, many U.S. facilities have been forced to improve localized VOC capture, as well as prove high-destruction efficiency in systems. In many cases, this has led to the installation of additional capture hoods or enclosures and increased the amount of air to be treated by a particular oxidizer system. A concentrator can take exhaust streams at or near ambient temperatures and concentrate them so that the airflow actually sent to the oxidizer is reduced. “This greatly reduced stream is typically rich in VOCs and much less of an operating cost burden on the oxidizer system,” notes Summ.
The workshop will also stress the importance of maintenance. “No matter how well an overall system is designed, it cannot continue to operate at a high efficiency level without proper maintenance. A handful of small inefficiencies in system operation can lead to large operating costs over the course of a year,” he says.
How to remove these inefficiencies, make necessary modifications and other solutions that will reduce operating costs and emissions is a topic that chemical facility environmental, health and safety managers, plant managers and compliance personnel should not miss, says Summ.
Joy LePree