A routes-by-exception reliability strategy helps improve safety and efficiency, while preserving competitive advantage in a changing marketplace
In recent years, maintenance and reliability experts have often talked about the massive wave of retirements leaving chemical plants, creating a shortage of expert personnel able to collect and analyze the data needed to run the plant at peak performance. They are not wrong. However, while a shortage of personnel and an increased focus on productivity have recently changed the way process manufacturers must operate, there has long been a push to collect data more efficiently. The solution — wireless data collection and analysis — has been available for many years. But now, a manufacturing landscape changed by the COVID-19 pandemic and a global marketplace has simply accelerated the need.
Today’s wireless sensing devices use powerful software to turn reliability personnel into digital workers. These tools eliminate the need for maintenance and reliability personnel, and, in many cases, even operators, to spend precious time roaming the plant collecting data, entering it into a centralized system, and then sitting down to analyze it. Wireless technologies not only bring data directly to the personnel who need it, they are also affordable and easy to install, making it possible for plant personnel to monitor and make decisions about the health of any plant assets, no matter their level of experience.
Problem 1: Data chasing
Traditional maintenance strategies require two key resources — personnel and time — and many modern plants are short on both. Today’s large specialty chemical plants often have many more assets than they have personnel to monitor and service them. In the largest plants, these assets are often significant in size and distant from one another.
Collecting asset-health data manually means sending personnel out into the field or plant floor with handheld analyzers to manually check each piece of equipment. This process is not only time-consuming; it also frequently puts personnel at risk. It is not unusual for the data-collection process to take six to eight hours or more for a large asset, and often requires personnel to scale tall equipment or extend a handheld analyzer into hard-to-reach places.
In many cases, the majority of data collected indicates that assets are generally healthy — which means time and resources may have been spent examining equipment that would have performed well without supervision. Moreover, when technicians return from collecting data, they must then enter those data into a centralized system, where the data can be used. Finally, someone — often that same worker — must analyze the data.
As a result of these and other hurdles to efficient and safe data collection, plants typically try to spread rounds out over as long a period of time as possible. It is not unusual for plants to space manual-maintenance rounds weeks or months apart. And when the plant’s already limited personnel are unavailable, it is common for rounds to be postponed. But mechanical failures do not wait for observation. If a bearing checks out today, but begins developing a malfunction tomorrow, it could be months before maintenance staff identifies the problem. In the worst-case scenario, a failure causing unexpected downtime could result.
Solution: Data where needed
Instead of tying up essential plant personnel on the low-value task of walking around the plant collecting data, today’s forward-thinking reliability teams are harnessing the power of wireless technology and software dashboards to bring critical plant data directly to them, on demand, wherever they may be. Today’s wireless vibration sensors can help plant personnel quickly and easily determine the source of a problem via intuitive dashboards, eliminating the need to examine the asset locally and identify malfunctions.
Innovative reliability teams are installing small-form-factor wireless sensing and edge-analytics devices right at each asset (Figure 1), then connecting these devices to wireless networks, which transmit data to asset-management systems. These devices require no cabling, which both eliminates the high cost of installing sensors, and makes it far easier to gather critical data from remote equipment where running cables can be expensive, difficult, or both. Typically, plant personnel can install these devices to deliver detailed triaxial sensing data for most plant equipment.
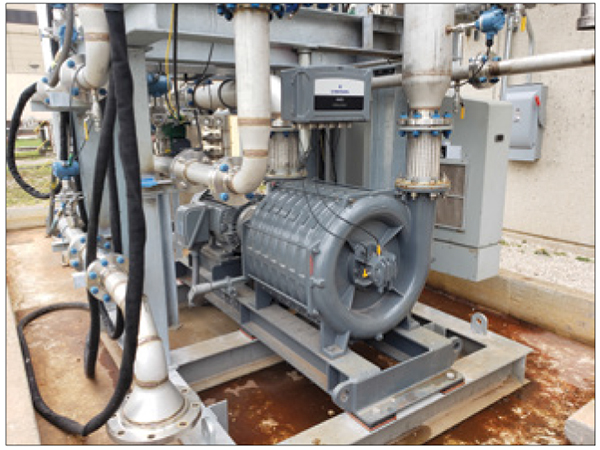
FIGURE 1. Wireless edge devices, such as the one shown here, are easy to install right at the asset, and can send machinery-health data to personnel wherever they may be
By eliminating the need for personnel to perform manual rounds, reliability teams free them up for other essential plant tasks, helping the plant do more with fewer people. Personnel are not only safer, but also more mobile, as many wireless sensing devices can deliver data directly to software on a handheld device, such as a tablet or mobile phone. This untethers digital workers from manual rounds, and even from the control room.
Instead of collecting data every couple of weeks or months, wireless sensing technologies enable plants to collect critical data every few minutes or hours. Reliability teams can maintain constant vigilance over assets, regardless of their criticality, helping to eliminate unplanned outages and unexpected emissions for more reliable, sustainable operations.
Small sensors bring big results
For one large North American power producer, small wireless sensors installed on a cooling water pump avoided a big hassle.
The plant had moved from manual maintenance rounds to wireless vibration monitors, which delivered spectrum, waveform, and embedded analytics to maintenance personnel and operators in the control room. Shortly after installation of the wireless sensors, maintenance personnel were notified of a critical alert status regarding lubrication of a cooling-water pump motor.
The waveform data indicated there was a problem with impacting, and a lubrication display in the red zone showed the cooling-water pump likely had a dry motor bearing. Technicians greased the bearing and collected vibration data on demand, this time with the impacting eliminated and lubrication status in the green zone due to dramatically lower vibration levels.
By setting up their reliability equipment to deliver actionable information to the right people at the right time, the plant avoided a potentially costly equipment failure and extended downtime.
Problem 2: Upskilling personnel
One of the key metrics by which reliability teams judge their success is response time. When there is a problem in the plant, teams should be able to respond quickly and effectively — a task that was much easier ten or fifteen years ago, when plants often had a “deep bench” of expert personnel to identify, analyze and solve equipment issues.
Today, however, plants are running with far fewer personnel, and those people often have far less experience. Most vibration-related equipment problems will fall into one of a few common categories:
• Balance
• Alignment
• Looseness
• Blade pass
• Bearing
• Lubrication
However, identifying those problems from just raw spectrum and waveform data can be a complex undertaking (Figure 2).
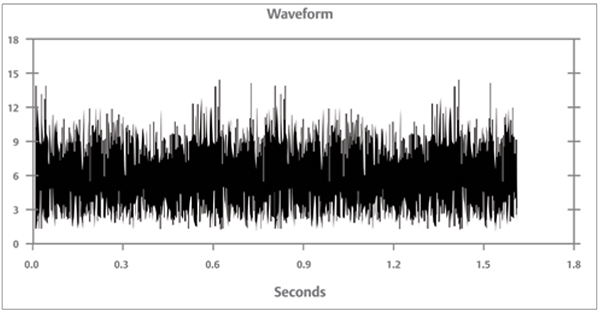
FIGURE 2. Reading waveform data, such as the spectrum shown here, can be a complex task for inexperienced personnel
A new technician typically needs two to three years of experience before he or she can analyze raw data and identify the root cause of a problem. Waveform data identifies the severity of a problem, but without an identified source, that information is difficult to use.
Severity and source are interlinked, and manually making that connection using spectrum and waveform data to identify the most common equipment problems will be difficult for new personnel. Waiting two to three years for them to gain these skills has the potential to result in significant downtime and loss.
Solution: Decision support
Instead of waiting for new technicians to come up to speed over several years, today’s reliability teams are implementing decision support through edge-analytics software to more rapidly upskill and assist personnel. Many of today’s wireless edge devices contain embedded prescriptive analytics tools, effectively building expert knowledge into the device.
Instead of spending hours evaluating and manually analyzing raw data, digital workers simply access the report provided by the software on the edge device. In the most advanced edge devices, these tools are intuitive enough to be used by a person with no analytics experience whatsoever. For example, equipment health can be identified by color — green, yellow or red, based on severity of defects — and the software can inherently identify the most common equipment faults (Figure 3).
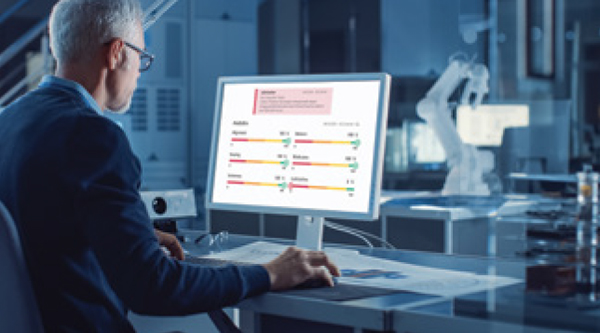
FIGURE 3. Analytics tools for machinery analysis, provide a simple and reliable indication of equipment health
Using the intuitive screens instantly displayed on their console or web device, personnel can address problems immediately (when possible), flag them for maintenance during a scheduled outage, or travel to the asset with a handheld analyzer to gather more information for deeper troubleshooting. Traveling to the machine with an analyzer is the exception, not the standard, ensuring the time spent manually investigating equipment only occurs on the small number of failing machines.
Routes-by-exception
One North American manufacturer was producing products that became very popular during the COVID-19 pandemic, forcing them to rapidly increase production. Upping production increased the potential for problems, and it also meant less room for error because any downtime caused by equipment outages would result in lost production of critical supplies.
An edge device with embedded analytics software detected and identified lubrication issues on six assets, enabling the maintenance team to intervene before failure. Moreover, it also triggered vibration alarms as supply fans began experiencing problems during production increases. Immediately following up on the vibration alarm not only helped the maintenance team identify clogged filters at the facility before they caused damage, but also prompted personnel to proactively clean and check filters in other facilities as their production ramped up as well.
Problem 3: Unplanned outages
Equipment breakdowns are very expensive. Estimates from the author’s company suggest breakdowns generate five to ten times the repair cost of planned maintenance, and those estimates do not include the revenue lost to interrupted production (Figure 4).
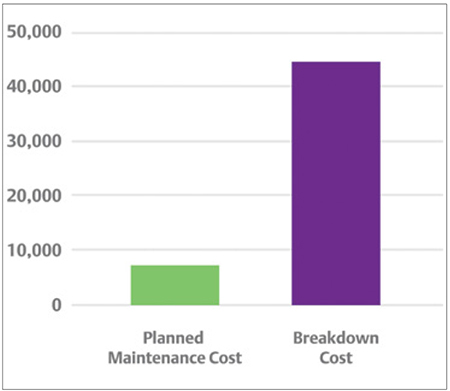
FIGURE 4. Repairing equipment that has broken down can cost 5–10 times more than performing planned maintenance before failure
Beyond financial cost, however, many organizations also experience opportunity loss when equipment breaks down. When an important machine is down, product is not manufactured, leaving a gap in market supply. These gaps are the opportunities competitors need to capture market share.
In the best scenarios, machines will not need repair until there is an opportune time to shut down the processes, but even planned outages are not without risk. Maintenance activities are time-consuming and subject to all manner of potential setbacks, including out-of-stock parts, malfunctioning tools, machines that are difficult to access or move, and more. If scheduled outages are not properly planned, they can easily run over time and budget, with costly consequences.
Solution: Preparing resources
To offset the risk of equipment breakdowns leading to outages, reliability teams are taking advantage of edge devices with embedded analytics software to unlock predictive maintenance information. When asset-health information is delivered in real time to the control room, or to the mobile devices of operators and technicians — in either case, using intuitive health scoring — reliability teams are aware of impending failures long before they become breakdowns. This type of warning is critical for properly scheduling maintenance activities during planned outage periods.
The most effective reliability teams, however, are using predictive maintenance via wireless sensing technologies to do more than just predict the time to failure. These teams are using all the digital tools at their disposal to prepare for planned outages that are as efficient as possible.
The analytical data provided by edge devices and sensing technologies helps teams plan their resources properly for maintenance windows. Before a machine stops running, teams can know what they need and have those items on site and ready to go. This can be as simple as having the right parts on hand, or as complex as ensuring a crane is in place and ready to get large parts into and out of a building.
Edge analytics
For one reliability and maintenance team that put an edge-analytics device on a forced-draft fan motor, embedded analytics software not only helped identify an issue and its severity, but also prepared them to perform repairs on schedule.
When their edge device identified a lubrication problem inside a sealed bearing, the team could not simply add grease while the machine ran. Knowing a true internal lubrication issue would likely mean fully replacing the motor, the team used handheld analyzers to collect raw data for a second opinion. When spectrum and waveform data from route-by-exception collection supported the dry-internal-bearing analysis, the maintenance team made the decision to replace the motor.
Knowing the replacement was a large job, and that the technicians would only have a short maintenance window, the reliability and maintenance teams had the replacement motor and all spare parts, the crane, and all necessary tools and staff ready the moment the machine was shut down during a scheduled outage. By ensuring that everything was ready before undertaking the project, the team likely saved ten to fifteen hours of maintenance time, and was able to complete the replacement well within the scheduled outage.
Making data work for you
Competing in today’s global economy means making the most of every production moment. Savvy organizations know their reliability teams are key to ensuring that production is the best it can be, but they also know those teams cannot perform at a high level without the right tools.
Wireless sensing and edge analytics technologies are affordable and more powerful than they ever have been, providing reliability teams with the digital tools they need to transform the way they operate, so they can reduce downtime while increasing safety, availability, and productivity. Instead of chasing reliability data around the plant, the best teams bring the reliability data to the right people wherever they are. These teams use this information to make impactful decisions, upskill personnel, and get the most value from every moment spent in the plant.
Edited by Scott Jenkins
Acknowledgement
All figures courtesy of Emerson
Author
Asad Malik has been working in the field of maintenance and reliability, condition-based maintenance, application engineering, training, services and business development for the last 25 years. He is a senior manager of reliability solutions and services at Emerson Electric Co. (835 Innovation Drive, Knoxville, TN 37932; Phone: 865.368.8571; Email: [email protected]), where he has worked for over 14 years. Malik is a certified maintenance & reliability professional (CMRP) from the Society of Maintenance & Reliability Professionals and a certified reliability leader (CRL) by the Association of Asset Management Professionals. He is also Vibration Analyst Category-III and Oil Analyst level II certified. He has conducted several training courses and workshops in the field of reliability and condition monitoring, particularly in vibration analysis. He presented several technical papers in Europe, MEA and North America and published articles in multiple trade magazines. Malik holds a bachelor’s degree in mechanical engineering and an Executive MBA.