From the impact of globalization to variable crude oil prices, environmental concerns and changes due to advancing technology, the chemical process industries (CPI) are in a state of flux. Companies based in some regions have experienced impressive growth thanks to where they are positioned, but as we look to the future, that heyday won’t necessarily continue. For many CPI companies — especially those operating with legacy systems and sites — efficiency is more important than ever. Slower demand growth, less predictable feedstocks and a changing global backdrop mean companies are likely to have to look at their core efficiencies and their capabilities to increase productivity. On top of this, the drive to reduce greenhouse gas (GHG) emissions in line with — and ahead of — the United Nations’s (UN) 2030 targets mean that CPI plants across the globe need to ensure that their critical-system processes meet or exceed industry best practices.
This focus on efficiency means that control-loop engineering and optimization and the use of digital and advanced analytics are more important than ever. Automation in proportional–integral–derivative (PID) control loops typically has a half-life of six months, meaning that half of all loops undergo some degradation in performance within their first year of deployment. These untuned loops can lead to many unfavorable circumstances, including unstable processes, inefficient production, ineffective use of capital and product-quality problems, all of which could result in catastrophic effects within a CPI facility.
Each industry presents its own challenges
Petrochemical plants and other large industrial facilities consist of a multitude of components and sub-processes that all work together to drive optimal production processes. This is made possible with hundreds, sometimes tens of thousands, of control loops. The plant can only run optimally if all control loops are aligned (Figure 1). However, the half-life of these loops and constant changes within the processes mean that the loops require constant re-optimization. This requirement makes it very difficult for plants run at an optimal level. In some industries, slightly sub-optimal performance may not be too much of an issue, but in the CPI, sub-optimal system settings and conditions can lead to hard-to-diagnose issues, points of failure, system overload and gradual performance degradation, as well as efficiency losses — not to mention safety issues, if the facility is working with pressurized or volatile chemical substances.

Figure 1. The alignment of a massive number of control loops is essential for ensuring efficient operations at large chemical-manufacturing facilities
Troubleshooting is also inherently difficult at CPI plants. Control-system vendors are often limited in their ability to troubleshoot, and the burden is often on the end user to communicate what the problem is. But all the user may see is the symptom, leaving the vendor to act on the symptom. But if the issue’s actual root source was not the symptom, then the team has lost a whole cycle trying to find the proper party who can fix the problem. That initial fix time is the key. The collection of pre-visit intelligence prior to vendor troubleshooting is crucial to reducing the fix time required.
Legacy infrastructure and control-loop optimization
For many companies, legacy infrastructure leads to the need for difficult choices. For some petrochemical producers, aging infrastructure and the loss of skilled workers as they reach retirement age can lead to the potential for facility closure due to the costs needed to make an outdated plant productive again. With production efficiencies, financial considerations, safety and emissions concerns all playing their part, it is often difficult to identify the best solution.
For many companies, while upgrading a sub-optimal facility with new infrastructure, such as distillation columns or furnaces, would be the ideal, a more cost-effective solution to improve efficiency can be a switch in maintenance strategy from reactive to predictive (Figure 2). On top of this, plants may also struggle with finding the best resources to hire, whether that is someone with expertise in control systems, cybersecurity or the alarm spheres. The following section details a real-life example of a CPI plant facing such difficult scenarios.
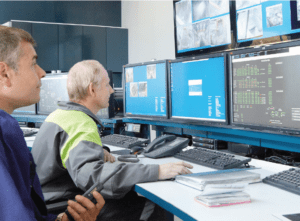
Predictive digital technologies can help plants optimize production, even as infrastructure assets age
Applying control-loop optimization
In 2015, the management team of a CPI facility were considering shutting down the facility as a more cost-effective operation than trying to make the aging plant productive again. The decision came against the backdrop of health and safety concerns, strict standards within the petrochemicals sector and the need to maximize efficiencies, and therefore finances.
Like many large petrochemical plants, the facility consisted of a multitude of components and sub-processes that all work together to drive optimal production processes, using hundreds, or sometimes thousands, of control loops. Plants like these can only run optimally if all control loops are perfectly aligned and undergo regular re-optimization. This is often a time-consuming task.
The producer in question was dealing with the effects of manual data collection and analysis from functionally siloed systems, which had led to data inaccuracy and inconsistencies, and the management team’s decisions were being made based on that inaccurate information. Rather than try to upgrade the facility with costly new technology, a decision was made to optimize the control system and move from a reactive maintenance strategy to one that was more predictive, using automated intelligent devices and systems.
Developing key performance indicators (KPIs) for a number of assets, processes and risks was completed by evaluating issues, categorizing them, and prioritizing them in order of severity and criticality. KPIs can be visualized using a Pareto format to highlight which issues need attention first.
To identify the sources of issues limiting performance in the plant, the decision was taken to invest in digital services employing a secure edge device to maximize the use of limited resources onsite. Such a device can provide assessments of equipment and process performance by identifying, categorizing and prioritizing KPIs so that experts can help find and mitigate productivity variables, ensure maximum performance and improve efficiency.
Additionally, the plant implemented services for continuous monitoring of control-loop performance issues. Control loops are designed to improve quality, performance and production, but if they are not properly tuned, they can actually cause more harm than good.
In this case, the initial loop-monitoring data reports showed that more than 40% of loops were operating in manual mode and numerous loops were having control problems. Once repaired, the decision was made to increase the existing maintenance schedule to include additional monitoring, including reviewing the tuning parameters and the control structure for the three main plant units.
Solutions don’t have to be a dream
By switching to automated intelligent devices, control-loop optimization does not have to be an unobtainable dream for companies — they can achieve accuracy, high productivity and cost savings through the use of advanced plug-and-play solutions.
The benefits of such digital solutions are more predictable maintenance costs, increased convenience (by reducing time and cost of manual identification of issues) and higher user confidence in system and process performance, cybersecurity defenses and control system health by helping to quickly identify system-optimization opportunities.
These solutions give plants’ control systems the capability to monitor and report on critical system settings and parameters to ensure they are configured according to established industry best practices. By managing process operation conditions, customers can use predictive analysis to know when modification is needed for their process control and PID tuning parameters.
The overall benefit is the ability to employ a predictive maintenance approach that proactively addresses a plant’s equipment issues, avoiding lost production, managing life cycle costs and ensuring continuous process optimization.
As the fundamental building blocks of industrial control systems, control-loop optimization sits at the center not only of efficiency, but safety. However, that doesn’t mean that a siloed approach is the way forward. Sticking solely in the silo of loops means ignoring the impact of all the other elements that can affect that loop. Being aware of that ecosystem can provide invaluable information on the source of the issues that may affect those loops, from alarm management and cybersecurity to power consumption.
The best solutions involve getting the right person at the right time with the right skill set. Effective troubleshooting teams don’t send people in to fix symptoms — they need to fix the source itself. This can be most effectively achieved with a properly instrumented, analytical solution set. The best control-loop optimization schemes take account of that and provide solutions to problems, not just symptoms. ♦
Edited by Mary Page Bailey
Author
Kevin Starr (kevin.starr