Accurate water-monitoring technologies support short- and long-term sustainability goals in both municipalities and the industrial sector
In recent years, São Paulo, Cape Town and other major world cities have come dangerously close to running out of water, and the criticality of water as a key business asset has never been clearer. Indeed, managing water risk is now identified as a chief priority by industrial giants around the world. But, what about the industrial sector’s municipal bedfellows on which they often rely for supply? Beyond the industrial sector’s monitoring and strategizing headlines, the day-to-day business of identifying leaks and bursts and reducing their occurrence in the first place is an emerging area for minimizing water loss and meeting environmental, social and governance (ESG) goals. For leak and burst management and reduction, copying some pages from the municipal playbook could well pay dividends for the manufacturing sector (Figure 1). This article provides some success stories in leak and burst monitoring from municipal water organizations, and discusses the key takeaways for industrial water users.
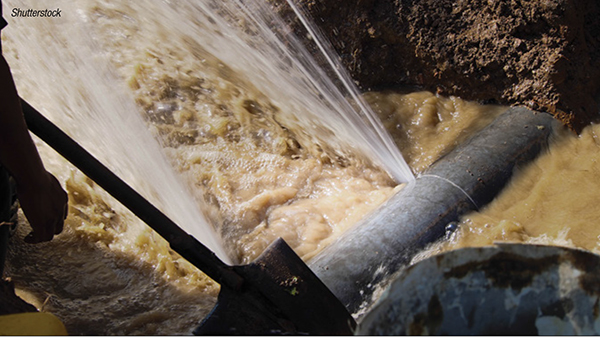
FIGURE 1. Burst and leak monitoring systems can help water utilities and industrial users make great strides in their water-conservation efforts
Water loss in a municipal system
Aging infrastructure and shrinking freshwater sources are challenging water utilities and pushing them to take every available step to protect treated water from loss. Providing clean water for a price that consumers can absorb is in the crosshairs of strategy for water utilities, even while daily residential demand has been increasing due to a dramatic rise in people working from home. Additionally, utilities are facing growing pressure from regulators to step up water conservation and environmental protection measures. In response to those pressures, municipalities have been focusing on the following key areas, which are also applicable to the management of any industrial water process:
- Leak detection — both to save water and because a significant proportion of bursts on larger pipes start as small leaks
- Instantaneous burst locating so that the damage caused by bursts, which can be significant, is minimized
- Identifying and removing the pressure spikes that occur on the network from operations and usage. Such spikes can significantly accelerate the failure of a pipeline
Detect surges and avoid bursts
At the heart of leak detection and response strategies are pressure- and acoustic-monitoring technologies. Small monitoring units may, for example, contain a precise pressure sensor, with network timestamping, and a hydrophone for leak detection. Such a system can fit easily into hydrants and chambers and collect data that can be analyzed to detect leaks and pressure spikes (also called “transients”) and also to locate a burst. Monitoring units may also include a corresponding software to generate alerts and alarms to inform operators of critical events, such as when pressure valves are above or below desired limits. Modern, cloud-based data platforms can automatically track the source location of bursts and major pressure events.
High-resolution monitoring allows users to detect and identify the source of pressure spikes that can, over time, cause significant wear and tear on pipes and other assets. Pressure spikes can be caused by irregular pumping and valve operations and also major offtakes being turned on and off quickly without any dampening. If a burst does occur, the monitoring technology should also be configured to locate the burst quickly (within seconds), allowing immediate mitigating actions to be implemented to minimize water loss, damage and system downtime.
Alongside those measures, acoustic leak-detection technology allows users either to survey or permanently monitor pipelines. With the units acting in pairs, the vibro-acoustic signature of leaks can be detected — ideally, with external noises filtered out. From there, the exact location of a leak can be identified, allowing for monitoring and repair before the leak deteriorates into a burst.
Industrial water use and loss
It is estimated that industrial water use represents about 5% of total direct water withdrawals (surface and groundwater sources) in the U.S. (around 18.2 billion gal) and 12% of the public water supply. Among the most water-intensive industries are agriculture, biotechnology and pharmaceuticals, metals and mining and forest products.
Leaks can represent a significant economic factor for an industrial facility. For plants relying on public water supply, the cost of water includes not only the price of incoming water and the sewage fee for discharge, but also the cost incurred through any treatment or processing (typically for chemicals and energy) that a plant carries out for its own purposes, plus associated labor and other costs. The full cost of water can end up being three to four times the cost charged by the utility.
Moreover, industries operating in water-stressed areas of the world — the southwestern U.S., for example — likely will be facing a changing regulatory landscape with regard to acceptable water use and loss, making leak detection and elimination a critical element in any industrial water strategy.
Companies can begin the process of determining water loss and potential leaks with a water-balance calculation, or a comparison of input versus output, considering such factors as evaporative loss, input to product streams and wastewater discharge requirements. When output is shown to be less than input, a leak may be the culprit. Effective pressure and acoustic monitoring can help industrial facilities to avoid the loss of a tremendous amount of water and associated expense.
Use case: EVWD
East Valley Water District (EVWD; www.eastvalley.org) provides water and wastewater services to 103,000 residents of San Bernardino County, Calif. (Figure 2). EVWD staff felt that evaluating the existence and severity of pressure transients was a prudent step in actively managing its water-distribution system. The main goal was to reduce line breaks caused by pressure transients, aging assets, bedding failures and corrosion. With the cost of repairing a single break ranging from $10,000 to $25,000, reducing these events can generate significant savings. EVWD decided to deploy a network-calming project using smart pressure monitors.
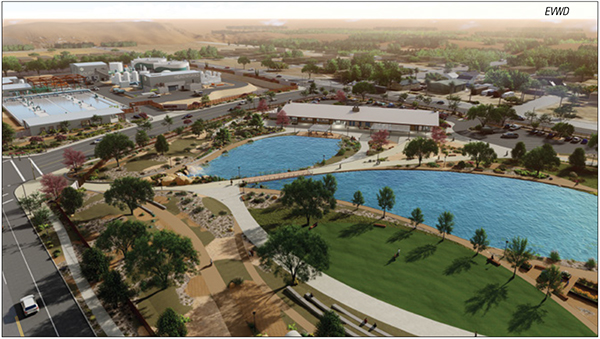
FIGURE 2. Municipal water providers certainly serve many different end users than the industrial sector, but the key lessons related to conserving water and minimizing system bursts and leaks are crucial for all water suppliers and users
To identify critical areas, the team imported EVWD’s historical data on breaks and combined this with geographic information system (GIS) data using open-source GIS software to create a map of “hot spots” of concern associated with specific pressure zones. Possible transient sources — such as pumps, valves and user points — were then identified near each hot spot. Using this water-main-break heat map, pressure monitors were deployed at pumping stations and on hydrants across the network to confirm transient propagation across the monitoring area.
To cover the entire service area, the monitoring project was undertaken in phases, focusing on the most critical areas on the heat map first. To identify transients of concern, two types of data were analyzed, as described below.
Summary pressure data. This is a summary of the minimum, mean and maximum pressure values registered over a period of 1 or 15 min based on constant readings at 128 samples per second, also known as high-sample-rate data.
Pressure sensitivity data. A pressure sensitivity threshold, known as an S3 score, was set in each pressure monitor to alert when transient events occur. S3 scores are a non-dimensional measure of pressure-transient activity calculated within the unit itself. Large and sudden changes result in a high score; small changes over a longer period result in a lower score. Tracking and profiling pressure sensitivity data is a good measure of the pipeline’s transient activity, indicating if the activity level has increased or if mitigation work has been successful in reducing it.
A summary of pertinent data can be sent multiple times per day and high-sample-rate data are typically only sent when the pressure sensitivity threshold in each unit is breached.
At EVWD, the collected pressure data were then analyzed to identify the root source of the transients via triangulation. First, similar transient wave shapes from all monitored sites were grouped to identify clusters of recurrent transient events produced by different sources. The analysis then focused on identifying the source of these events. Locations of automatic triangulation results were plotted on the water-main-break heat map and matched with the transient clusters previously identified, pinpointing the source of the recurrent transient event.
During the first phase of monitoring, the analysis found that the aggressive starts and stops of a specific pump station created transient events that added additional stress to the pipe. The insights revealed by the analysis enabled EVWD to identify the specific assets that produced these transients and take action to mitigate the transients to calm the flow.
One benefit of high-resolution monitoring is that it identifies smaller, more frequent transient “noise” that can, over time, cause significant wear and tear on the pipes and other assets. These can often be remedied more quickly and less expensively than larger transient situations, improving the overall network health.
Based on this project, EVWD has now initiated a process of relocating the monitors to different locations on a rotating basis to provide ongoing analysis of hot spots throughout its service area. They continue to monitor trouble spots, line-break events and user pressure concerns to assess the results of the calming.
With thousands of assets spread over a wide geographic area, EVWD gained access to actionable data to guide their troubleshooting and network-optimization efforts.
Use case: South East Water
For South East Water (www.southeastwater.co.uk), the utility serving the U.K.’s South East region, residential use spiked in 2020, with per-person water use increasing by a staggering 16% due to the rush of people newly working from home. That increased the utility’s focus on minimizing leaks and main breaks.
Recognizing that pressure transients are a major source of damage to pipes and other network assets, leading to leaks and breaks, South East Water initiated a pilot program to assess how leak detection and intelligent pressure monitoring could help it identify and reduce the causes of leakage. They chose a compact system that combined standard pressure monitoring with acoustic monitoring to support both leak detection and network calming. Detailed monitoring data could be sent in real time to a cloud-based platform for analysis.
The pilot monitored a stretch of water main running alongside a busy road. Three monitoring sites covered a total distance of 1,376 m. At each location, a pressure monitor was installed in an existing fire hydrant. Built-in network time protocol (NTP) clock synchronization facilitated accurate global positioning system (GPS) locations without requiring site modifications. The three units were installed as a string to confirm the distance over which the leak noise could be observed and to assess the performance of using GPS time-synchronized correlations with NTP.
The team conducted a daytime test, opening a hydrant to simulate a leak when busy road traffic was observed. The pressure monitors generated the hydrophone data (Figure 3) that enabled them to locate the simulated leak to within 1 m. In opening the hydrant, they triggered a pressure event on the valve opening analogous to a burst, which was also captured by the monitors — a valuable finding to support network-calming efforts.
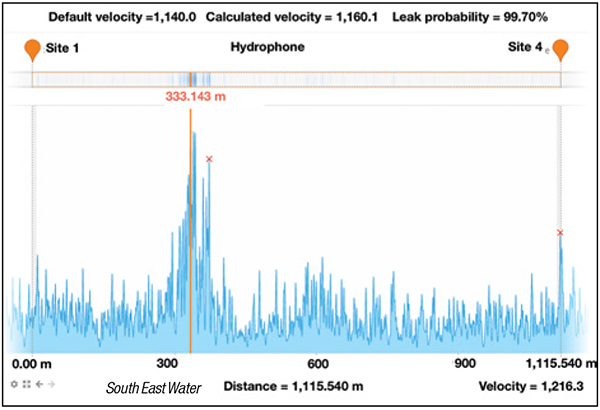
FIGURE 3. Pressure monitoring data were used to pinpoint the location of a simulated leak
Figure 4 indicates the pressure drop at the moment the leak was started. Real-time datasets from the three pressure monitors were analyzed by software to triangulate the location of the leak. With an integrated GPS receiver recording the unit’s position, an algorithm was applied to the data, the exact location was pinpointed, and the user immediately alerted. The triangulated result, as shown by the red flag in the map in Figure 4, indicated the location of the simulated leak to within 1 m. Since the outcome of the trial was positive, helping South East Water extend its record of hitting its yearly leakage targets, the group now plans to do a larger-scale project.
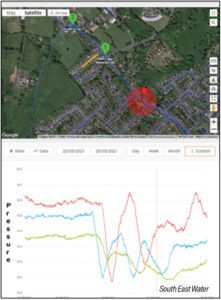
FIGURE 4. The pressure drop related to the simulated leak is seen in the analysis graph. The map shows the location of the leak
Applying learnings
As water-system operation and water preservation falls under greater scrutiny, for companies’ own internal ESG goals and for external environmental regulation, taking care to identify leaks and bursts early, and also reducing the activities exacerbating them, is a logical and cost-effective step. As the cost of water increases, eliminating leaks represents a growing economic opportunity as well. Technology used effectively for large, pressurized water-distribution systems in municipalities works just as well for water systems in manufacturing applications, and with the same benefits.
Author
James Dunning is the general manager of Syrinix (Email: [email protected]). With more than 25 years of experience in the utility sector, Dunning joined Syrinix as CEO in 2010, leading its growth as an award-winning global market leader in providing high-resolution data-led insights for water utility networks. Prior to Syrinix, he served as a lawyer and is a graduate of the London Business School, as well as holding senior positions within the corporate utility sphere and as an entrepreneur in the renewable energy sector.