New industry standards aimed at reducing fugitive emissions have necessitated updates to valve-testing procedures and a renewed focus on high-performance sealing and packing technologies
While reducing fugitive emissions is a leading concern in the fight against climate change, emissions continue to be released via leakage of process equipment in manufacturing plants and other operations in many industrial sectors. Valve leakage is reportedly responsible for more than 65% of total fugitive emissions, by some estimates. As a result, valves have been a considerable area of focus in the effort to reduce fugitive emissions.
So, where are the chemical process industries (CPI) headed in the quest to achieve reductions in fugitive emissions? Regulators and end users are currently working on developing, expanding and improving several industry standards for fugitive emissions and valve seals (Figure 1), as summarized below:
- ISO 15848: Measurement, Test and Qualification Procedures for Fugitive Emissions
- API 622: Type Testing of Process Valve Packing for Fugitive Emissions
- API 624: Type Testing of Rising Stem Valves Equipped with Graphite Packing for Fugitive Emissions
- API 641: Type Testing of Quarter-turn Valves for Fugitive Emissions
- Additional user-defined fugitive-emission reduction requirements
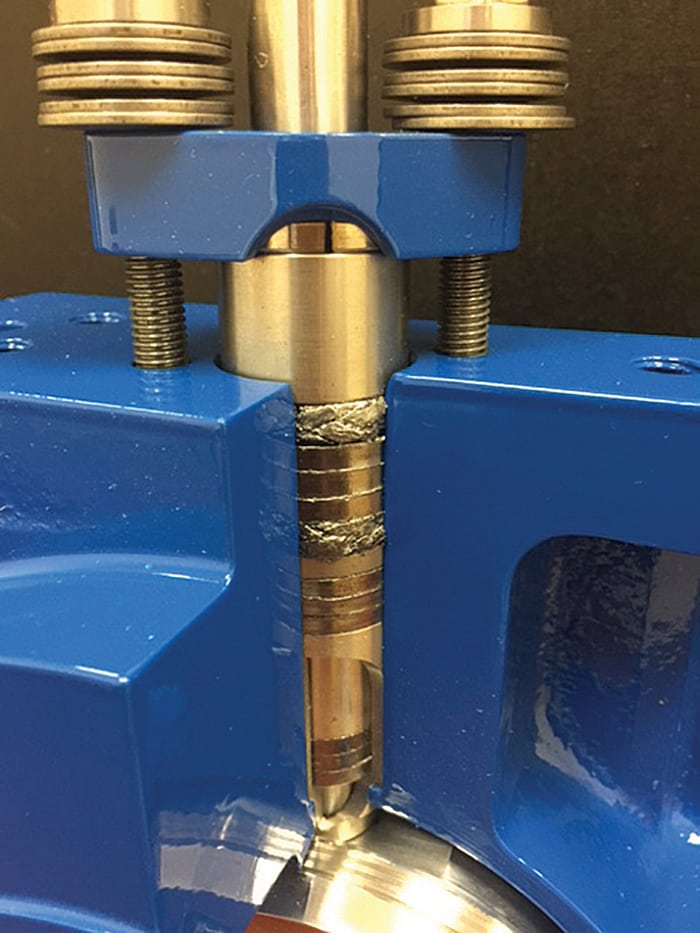
FIGURE 1. A great deal of effort has gone into developing industry standards aimed at reducing fugitive emissions from valve seals Zwick GmbH
Testing and implementation
API 624 was developed to cover multi-turn valves, such as gate, globe and control valves used in operating plants. The API 624 Task Force worked for over two years to incorporate members’ views, as well as the requirements of regulators and manufacturers, and came up with a reasonable standard, which is summarized below. Note that this standard applies to rising and rising-rotating stem valves up to 24 in. in diameter.
- ANSI Class 1500 valves are not covered.
- The test medium is methane.
- In total, 310 test cycles are required with three thermal cycles.
- The temperature application range is from –29 to 538°C with the last 10 cycles defined by the user (can be as low as –45°C).
- Retightening of gland bolts is not permitted during testing.
- The proper test orientation for valve stems is vertical.
- To comply with API 624, several valves are required to be tested. Similar industry principles applied to test valves qualify two nominal sizes smaller and one size larger and one pressure class below.
- The allowable leakage is 100 parts per million (ppm) maximum or below when performing a fugitive emissions test on a valve.
- Gate and globe valves need to be tested separately. For example, according to API 602, globe valves require four tests, whereas gate valves require four tests per API 602, eights tests per API 600 (for valves up to 20 in. in diameter) and eight tests according to API 603.
- Test valves should be production valves, rather than specially manufactured test valves.
As a result of the release of API 624, testing companies have been preparing for the increased amount of valve testing that will be required. To this end, new test facilities are being planned and opened.
Implementation of API 624 needs to be carefully monitored, and users should validate claims from valve manufacturers by requesting to view test results, as is advised by key reputable test facilities.
Below are some considerations to take into account when evaluating testing procedures and results:
- Number of cycles on some valves. Too many cycles could be tortuous to packing, as certain smaller-size valves do not come with grease ports to keep stems lubricated all the time
- Failure of valve stem threads, yokes and glands during the test
- Grease becoming trapped in the packing, which can cause leakage
- At higher temperatures, some greases create volatile organic compounds (VOCs) and burnoff
- Vertical testing has been known to generate more heat in the yoke area
Certain challenges require a good testing company that has experience in fugitive-emissions testing and provides guidelines to manufacturers in terms of the use of packing, valves, grease, testing requirements and so on. In addition, the industry currently is discussing the challenges in conducting these more rigorous tests. As most testing companies do not provide a great deal of information or operational guidelines beyond whether a valve passes or fails a given test, the responsibility falls to valve manufacturers to provide recommendations in many areas (for instance, suggesting a certain amount of torquing, followed by 5–10 dry-run cycles and then re-torquing.)
An additional challenge for valve manufacturers is re-qualifying valves that were previously qualified to ISO 15848-1 standards, although ISO 15848 Class BH is more difficult to comply with than the 100 ppm of API 624 and API 641. Still, these new qualifications require time, effort and costs from valve manufacturers.
The shift in testing media (from helium to methane) also presented some new considerations. The molecular weight of helium is significantly lighter than methane, and hence more permeable. Therefore, if a valve complies with ISO 15848 Class BH, it will comply with API 624/641, but not vice versa, necessarily.
Designing for reduced emissions
Some leading manufacturers of these types of valves have taken initiative in the reduction of fugitive emissions with the development of advanced technologies, including enhanced stem designs, packing solutions for high-cycle operations and fast-acting valves that meet stringent fugitive-emissions requirements. A few leading manufacturers who provide severe-service valves (Figure 2) have taken these requirements seriously, and have begun testing their valves with verification by an independent agency to demonstrate that their designs not only meet, but exceed, endurance testing standards and possess the ability to perform 500,000 cycles while retaining a maximum leakage rate equivalent to the stringent requirements dictated by the ISO 15848-1 2006 Class BH standard for the entirety of the test. For more information about severe-service valves, please see Getting the Most from Severe Service Valves, Chem. Eng., June 2017, pp. 52–58.
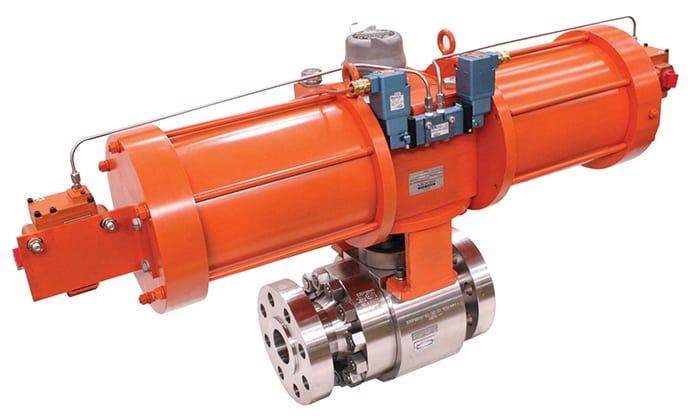
FIGURE 2. Severe-service valves may undergo specific tests and additional verification in order to ensure that they meet endurance requirements
ValvTechnologies Inc., USA
Typical stem-sealing technology requires packing adjustment. For high-cycle valves, these adjustments would have to occur very often, causing disruptions in plant operation, safety concerns and non-compliance with tightening emissions regulations. As no gland adjustments can take place during the test, in order to guarantee that the valve will comply with the 100-ppm emissions requirement, packing manufacturers have begun to increase the packing sealing stress required at the time of installation. API 624 gland torques with low-emissions packings are significantly higher than the torques applied on these valves previously. With new, more environmentally friendly packing solutions, laboratory-tested results have shown that some seals are capable of more than 500,000 cycles, all with stem packing that requires no maintenance and adjustment. This solution is suitable for end users that require a rapidly rotating valve that must complete many cycles annually (for instance, 100 or more cycles per day continuously) and must also meet fugitive-emissions requirements.
In addition to making sure that packing requires zero adjustment or maintenance, and is capable of 500,000 or more cycles, the packing should be durable for extremely high pressures, high temperatures and fast cycle speeds, such as less than 0.5 s. In addition, the packings must meet the reduced emissions requirements to comply with the recommended fugitive-emissions standard of 100 ppm or less recommended by the U.S. Environmental Protection Agency (EPA; Washington D.C.; www.epa.gov).
These beneficial features will lead to longer intervals of plant operation between maintenance schedules and provide safer plant operations, as plant personnel are not required to access the valve to undergo packing adjustments. These factors ultimately result in longer valve seal life (Figure 3).
Consider a trunnion-mounted ball valve capable of 90- or 180-deg rotation with cycle speeds as low as 0.5 s — this fast actuation speed is what creates a gas “pulse” through a pipeline system. Pulse-jet systems can be used to clean system filters, spray chemicals in an injection-type system or pulse debris or media through a pipeline to prevent clogging. These systems cycle many thousands of times per day. Conventional packing systems cannot handle the abuse of the fast cycle speed, combined with the high cycle count. These challenges have been addressed by valve manufacturers through the use of newer, more environmentally efficient design solutions. In these cases, the packing seals were laboratory-tested at high pressures and line temperatures up to 450°F for over 500,000 cycles, requiring no adjustments or maintenance. This equals longer plant operation between intervals, improved site safety and less emissions from thestem packing.
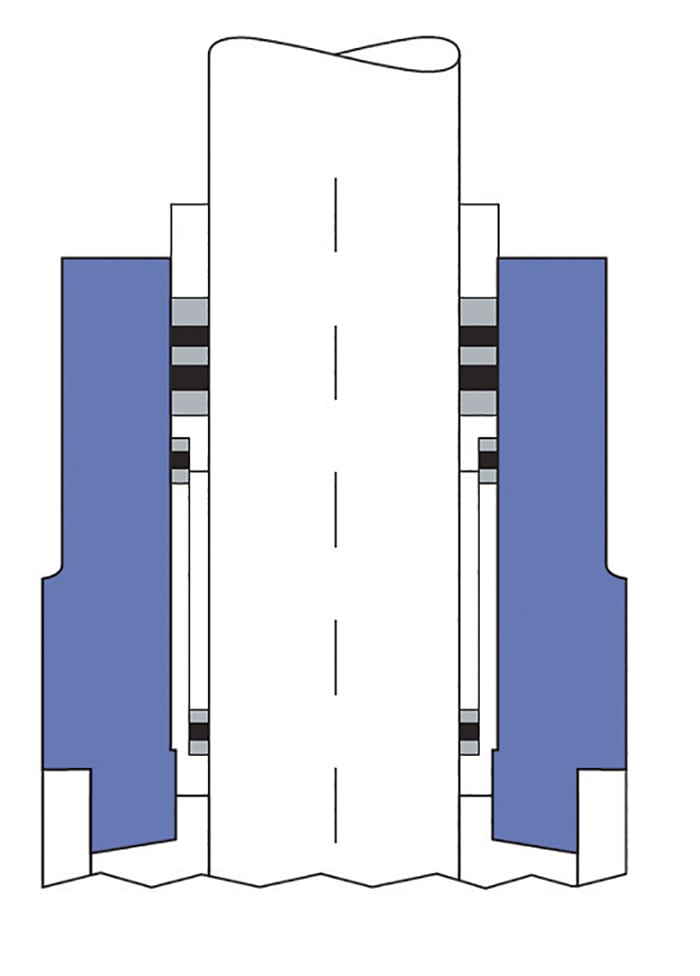
FIGURE 3. New valve-sealing configurations reduce maintenance requirements and increase personnel safety
Zwick GmbH
Final considerations
As design engineers begin to consider API 624 and API 641, there are several important factors that they should take into account when specifying valves:
- Packing selection
- Packing sealing stress
- Finish or tolerance of mating materials
- A full review should be conducted to investigate bonnet and gasket leaks during testing (this is not actually covered by the current edition of API 624, but a taskforce is working on revisions, and this may be addressed in future versions)
Through new and innovative technologies from valve manufacturers, emissions coming out of valves will be better controlled and more effectively reduced. Furthermore, the laboratory testing and certification procedures dictated by industry standards help engineers to establish tighter design tolerances and properly specify and install low-emissions packing materials. ■
Edited by Mary Page Bailey
Author
Gobind Khiani is a technical fellow in the area of piping valves for the Energy & Chemicals Group of Fluor Canada Ltd. (Phone: 403-537-5020; Email: gobind.khiani@fluor.com). He has served in engineering and project management roles for both operating and EPC companies. He is a chairman of the Calgary Branch Executive Committee at the Association of Professional Engineers and Geoscientists of Alberta and the Valve Users Group. Khiani has experience in piping and pipelines, valves, surge and control valve selection and sizing, modularization in valves, safety integrity of piping systems, fugitive emissions and material selection. He has a B.S. degree in civil engineering from the University of Pune in India and an M.S. degree in engineering from the University of Calgary.