The Valve World Americas Expo and Conference (www.valveworldexpoamericas.com) will take place at the George R. Brown Convention Center in Houston (June 19–20, 2019). Organized by KCI World and Messe Düsseldorf North America, the 2019 edition of the bi-annual event will serve as the meeting point for the flow control industry, with a technologically in-depth conference program, product showcases on the expo floor and numerous networking opportunities. Attendees will get a broad overview of the latest technologies, components and systems in the field of industrial flow control presented by over 324 exhibitors from the U.S., Asia, Canada, Europe, India, Mexico and more.
In addition to the exhibition, the Valve World Americas event will cover a variety of valve and valve-related topics. There will be plenary presentations on a number of hot themes in the valve industry, including the future of shale gas and the outlook on the energy industry.
For attendees looking to obtain professional development hours, conference delegates will be awarded certificates of completion for participation. Certificates will be available for pick up during the event Closing Ceremony. Workshop topics include: valve technology for cryogenic applications; valve design; valve testing for emissions; materials specification & casting; supply chain; valve asset management; control valve reliability prediction; performance and validation; actuation & automation; maintenance & repair; and ESDV (emergency shut-down valve) reliability.
A sample of products being exhibited is given below.
Flange inserts for vacuum applications
This company is introducing the new Vacuum Flange Insert (VI: photo) for rough- to high-vacuum systems, systems requiring frequent cleaning or modification, roughing and foreline plumbing, research and teaching laboratory applications, and more. The VI is designed to fit between ISO/NW/KF/QF vacuum flanges designed in accordance with DIN 28403, DIN 28404, ISO 1609 and ISO 2861. It is both a centering ring and a check valve, and therefore requires no additional space in the line. Its size makes it extremely economical when compared to full-bodied check valves. The VI can also be used as a low-pressure relief valve under either positive pressure or vacuum conditions by using the desired spring setting. Stand 1218 — Check-All Valve, Des Moines, Iowa
These check valves are engineered to avoid slamming
This company manufactures seven different types of check valves. The portfolio includes the Dual Disc, Foot Valve, Silent Check, Swing Check, Swing-Flex, Surgebuster and Tilted Disc, which are highly engineered to provide long life and trouble-free performance to meet the valve needs of users. Engineers weigh the importance of slamming characteristics as one of the factors when selecting a check valve. All of this company’s check valves are designed with non-slam characteristics, such as the seat angle of the Swing-Flex and Tilted Disc. The Surgebuster uses the addition of the Disc Accelerator to prevent slamming in the most severe applications. The versatile Foot Valve can provide positive seating action at both low and high pressure without slamming. And if you are not sure which check valve to use for your application, the company has redesigned its white paper “Design and Selection of Check Valves” to learn which valve is your best option. This white paper will help you understand basic valve principles and the functions of various types of check valves used in pumping systems. Engineering parameters associated with check-valve selection, such as flow characteristics, are discussed, along with headloss, reliability and costs. The combined characteristics of the pumps, check valve, air valve, control valve and surge equipment should be considered for successful pumping system design. With this knowledge, engineers can better select check valves and understand some pitfalls common to valve selection. Stand 534 — Val-Matic Valve, Elmhurst, Ill.
These valve actuators support Ethernet/IP
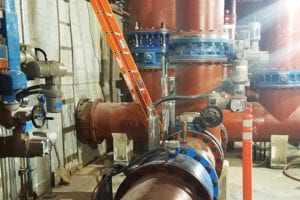
AUMA Actuators
This company’s electric valve actuators now support the Ethernet/IP Industrial Ethernet communication standard, in addition to Profinet and Modbus TCP/IP. With bandwidths up to 100 Mbit/s, Ethernet/IP provides reliable and rapid exchange of both cyclic process data and acyclic diagnostic data from the actuators. The company recently supplied and commissioned 49 actuators with Ethernet/IP communications to the Santan Vista water treatment plant in Arizona (photo). “Integrating the actuators into the Ethernet/IP system proved to be easy and straightforward,” says Lido Flores, regional sales manager in the U.S. “Many of our customers already use Ethernet/IP for their sensors and meter devices. We are happy to now also provide electric actuators that use this future-proof technology.” Stand 926 — AUMA Actuators, Inc., Canonsburg, Pa.
Manual ball valves with integrated position feedback
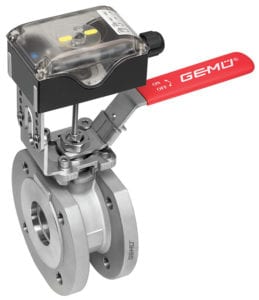
GEMÜ Valves
This company offers a technically advanced solution for ball valves for manual operation with suitable position feedback. And these are already pre-assembled, preset and tested. At first glance, there are a multitude of ball-valve and electrical position-indicator providers. However, many of these providers offer either one or the other. As a result, the individual components often have to be acquired from two different suppliers. This means that the two components must be assembled locally on the construction site before they can be placed in the plant — a process that is very time consuming. This company is reducing the effort required on site and offering manually operated ball valves with an integrated electrical position indicator. The pre-assembled valves save on the time and effort required for logistics and documentation and enable faster and simpler installation of the plant on site. For the GEMÜ 711 and GEMÜ 740 three-piece ball valves, the GEMÜ 762 one-piece compact flange ball valve (photo) and the GEMÜ 797 high-pressure ball valve, the company is offering the LSF inductive dual sensors or the LSC limit switch box. Stand 435 — GEMÜ Valves, Atlanta, Ga.
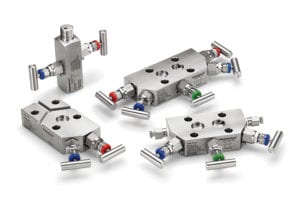
Emerson Automation Solutions
New manifold valve design for pressure transmitters
Manifolds shut off or equalize pressure at the transmitter and provide the critical mounting mechanisms required in many installations. The Rosemount R305 Integral Manifolds and Rosemount R306 In-line Manifolds (photo) have been designed to offer significant user improvements on these basic functions. The most important improvement for both manifolds is the new Pressure-Lock Valve design, which simplifies high-pressure operation, increases safety and enhances reliability. New features include: two-piece stem does not rotate in the seat, providing solid closure with minimal wear; easy to turn while delivering positive shut-off; adjustable packing nut simplifies valve maintenance; back seating prevents blowouts for increased user safety; stem and bonnet threads are fully isolated from the process fluid to minimize potential corrosion; modular packing ensures only the stem and body are exposed to the process fluid. Stand 1303 — Emerson Automation Solutions, Houston
This control valve is now available in PN 63 and ANSI Class 600
The Ecotrol 8C control valve features a unique cage retainer/clamping seat system that enables simple maintenance without special tools, and a wide range of process-tailored valve internals, including standard parabolic plugs (either metal seated or with the patented Arca soft seal system), multistage low-noise perforated and even double-guided valve plugs. The gland packing system is certified according to TA Luft and ISO15848 Class B for a temperature range from –46 up to 200°C. Recently the Ecotrol 8C product range has been extended to valves with PN 63 as well as ANSI Class 600 with flanges or butt-welded ends. Especially for the U.S. market, a version fully designed to ASTM and ASME standards has been developed. Stand 1433 — ARCA Flow Controls, Houston