Clarity about the requirements for digital twin technology is essential for any organization’s digital transformation
As manufacturers in the chemical process industries (CPI) begin the digital transformation process for their plants and assets, the need for technology to support this change to their plants’ operations is also growing. A significant opportunity for digital transformation is found in the digital twin. Teams hoping to drive the most value from digital twin technology should look to seven essential criteria (Figure 1) in order to ensure implementation of a system that will help drive improvement across the operations lifecycle and across the entire organization.
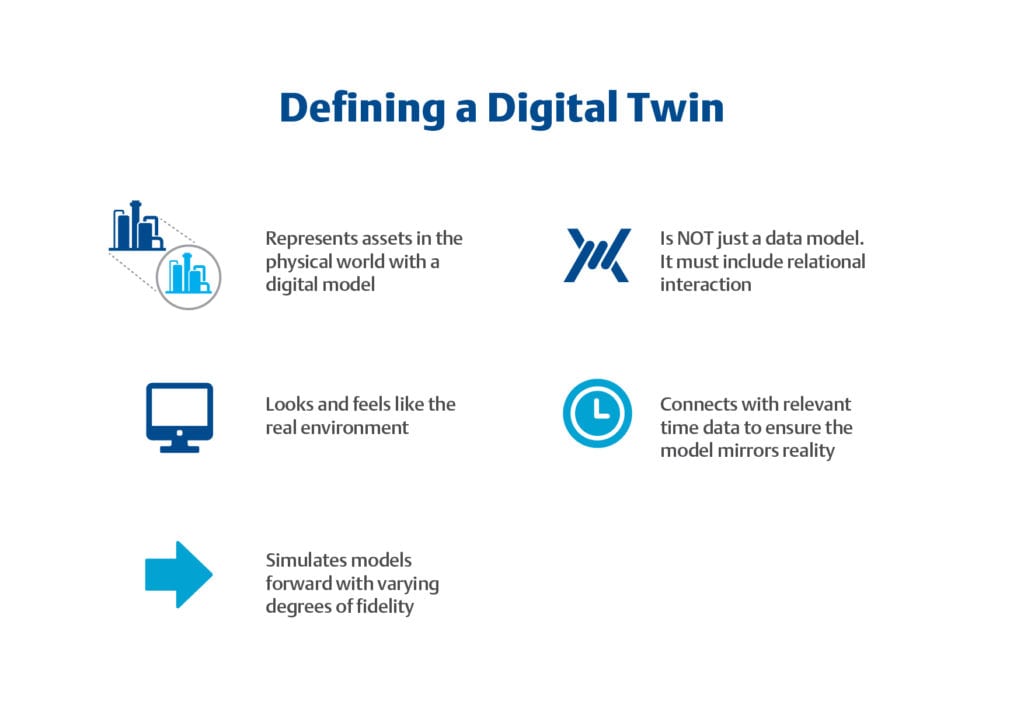
FIGURE 1. Versatile digital twin technology supports a wide array of functionality across the plant lifecycle
1. A digital twin should be a practical investment
Digital twin architecture can be a practical investment to make, regardless of the size of the plant or industry where it will be used. To help drive better projects and operations, the digital twin simulation functions as a flexible, scalable and holistic lifecycle tool. Organizations and projects of any size can realize value by using digital twin simulation to clarify the cost and risk associated with making operational improvements and improve control of the plant, as well as support upskilling of the workforce.
2. A digital twin should support distributed control-system engineering
A holistic approach to the digital twin can improve process and control-system engineering from the earliest stages of project design. The most advanced simulation technologies can leverage existing project assets by taking advantage of the project engineering team’s steady-state design models and integrating them — as dynamic process models — into a realtime dynamic simulation to speed and support process engineering execution (Figure 2).
A highly accurate digital twin built on engineering data also allows a project team to perform virtual commissioning to streamline projects. Virtualizing the commissioning steps can simplify factory acceptance testing (FAT), making the process more efficient and taking it off the critical path, ultimately helping ensure projects stay on schedule.
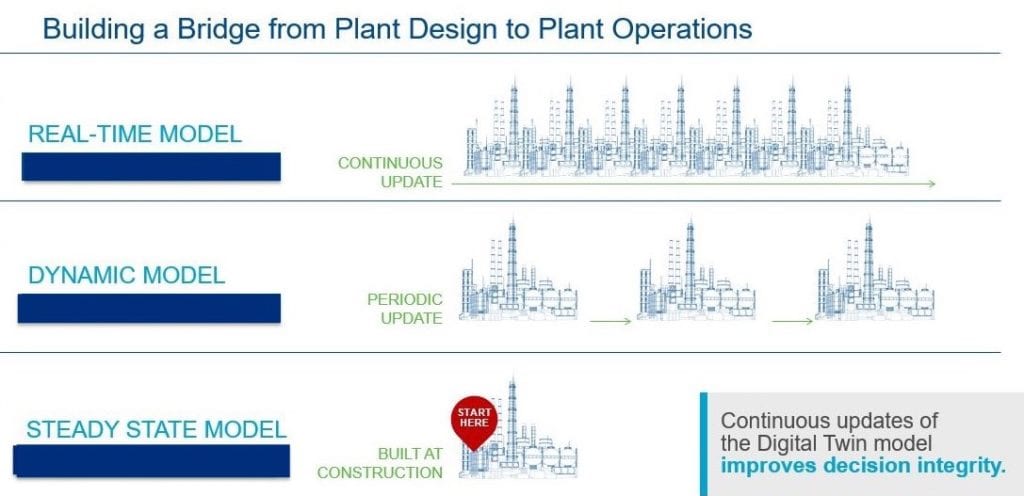
FIGURE 2. An effective digital twin must leverage advanced simulation tools and ensure that relevant data is integrated during the appropriate project phase
3. A digital twin should be designed with a best-cost basis, supporting the goals of projects and processes
To gain the most benefit as plants, processes and assets change over time, digital twin technology takes advantage of scalability to provide greater flexibility across a variety of assets and processes. To accommodate this scalability, selective approaches to model fidelity help organizations drive the most value over the longest time.
A rigid approach limited only to high-fidelity modeling will leave out some equipment and operations due to the investment required and the lack of accurate device models. In contrast, the selective fidelity approach to digital twin simulation provides flexibility to change fidelity as necessary, allowing organizations to build a structure that can evolve and change with the plant’s needs.
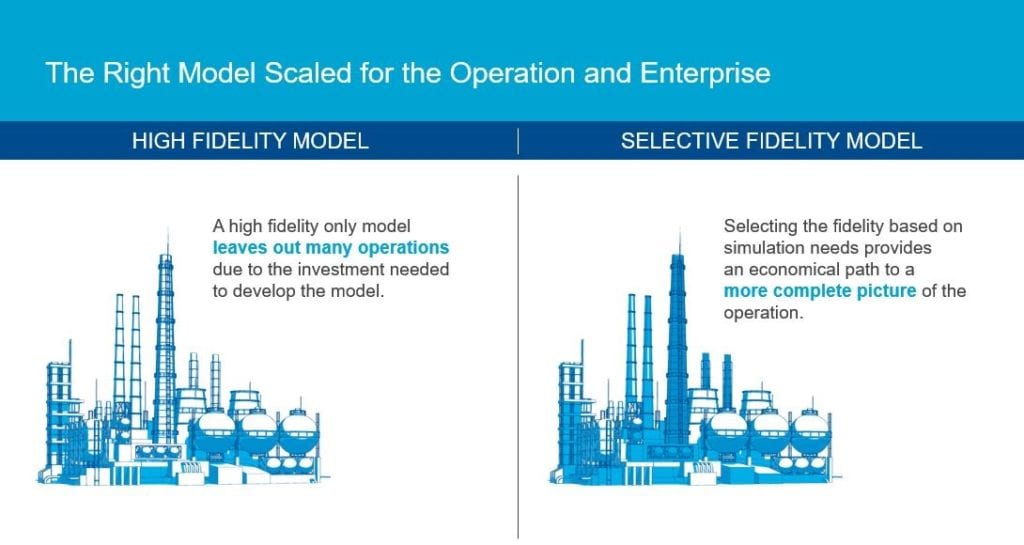
FIGURE 3. An effective digital twin may use a selective approach to model fidelity — low, medium and high — to provide a more complete picture of the operation of the plant
4. A digital twin should enable safe testing of process updates and changes
The same digital twin that allows for improving capital project execution also should provide organizations with the tools they need to evaluate new control and operations strategies, as well as to develop and deploy advanced process control schemes. Using a digital twin can allow plant management to see the impacts that process control improvement will have on processes and performance — which helps to continually keep the plant safe, efficient and competitive without any risk to current operations.
5. A digital twin should enable comprehensive training
It can take six to seven years to properly prepare a plant operator to make good decisions. A digital twin solution can cut this time dramatically, offering a solution to improve the skills of operators, even before a plant begins operation. On a digital twin simulation, years of plant experiences can be compressed into months. As the engineering and construction phases of a project are being completed, operators can use that time to safely and accurately train in preparation for the operations phase.
Using a digital twin, operators can experience accurate representations of plant transitions and transient operations, such as process events, startups and abnormal situations — operations that are the most dangerous and least profitable to personnel and processes, but also rarely seen — allowing personnel to enter production with more confidence and experience.
6. A digital twin should be an accurate digital representation of physical-world assets.
Digital twin technology can help organizations safely and securely test and train new operating environments, but only if the users are provided with an accurate simulation. The most advanced digital twin simulations present an exact, complete replica of the control system configuration, ensuring that users interact with control system interfaces that are identical to those they will experience in the real world.
7. A digital twin should be easy to use
In a properly implemented digital twin, the interactions between control data, historical data and design data should all be integrated in an elegant, intuitive structure that can evolve and change with the needs of the operation. These solutions combine realtime dynamic process and I/O simulation, as well as operator training options with industry-leading process modeling and high-fidelity dynamic simulation platforms. When designed and integrated properly, these solutions can easily integrate a variety of distributed control systems, programmable logic controllers and emergency shutdown systems, while still delivering a seamless experience that mimics the plant floor.
Usability is key to successful digital transformations. The organizations that see the most benefit from digital transformation technologies are those that use them to improve plant operations, making it easier for personnel to quickly and confidently make the best decisions. Digital twin technology is an effective tool to support capital project execution, as well as operational excellence initiatives for the lifecycle of the plant, and can be the foundation on which to support overall digital transformation.
Author
Mart Berutti is vice president of process simulation at Emerson (390 S. Woods Rd., Chesterfield, MO, 63017; 1-636-728-2000; Email: [email protected]). Berutti leads Emerson’s Process Simulation Center of Excellence, based in Chesterfield, Missouri. He previously held the role of president and chief operating officer of MYNAH Technologies LLC, from its founding in 2002 until the acquisition by Emerson in 2017. Prior to Emerson and MYNAH, Berutti worked for Experitec and Munger Company, holding positions of systems engineer, performance consultant, project manager, director of performance technology and director of business development. Previous experience includes Fisher Controls, Rosemount and Applied Automation. Berutti holds a B.S.Ch.E. from the Missouri University of Science and Technology. He also serves on the Academy of Chemical Engineers at Missouri University of Science and Technology.