Understanding material characteristics is important in designing and defining process criteria for optimal performance of rotary and fluidized-bed dryers
The ability to efficiently, reliably and consistently dry bulk solids in an industrial setting relies largely on tailoring the dryer’s design to the unique characteristics of the material to be dried (Figure 1). In other words, material characteristics can have a significant impact on the drying process, with the potential to influence factors such as equipment sizing, configuration, retention time and more. As such, material characteristics must be considered during the early dryer design stages.
This article looks at essential material characteristics to consider when it comes to two common types of industrial dryers: rotary and fluidized-bed dryers.
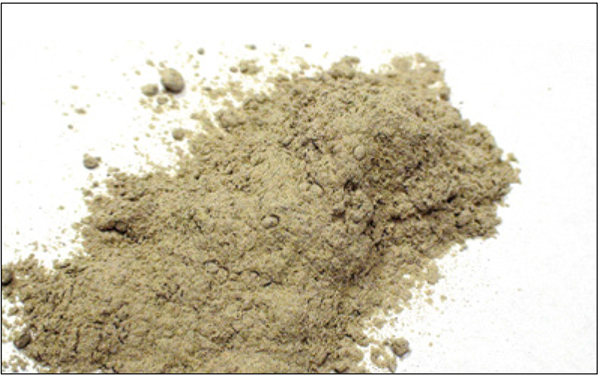
FIGURE 1. Bulk solids’ characteristics, such as bulk density, heat transfer properties, particle size and more, influence a dryer’s efficiency and optimal operating parameters
Rotary and fluidized-bed dryers
In order to understand how material characteristics influence their design, it is first important to understand how each type of dryer works.
Rotary dryers. Rotary dryers work by dropping material through a stream of hot air by tempering combustion gases (Figure 2). Material is passed through a rotating horizontal drum, through which a burner provides drying air either co-currently (parallel flow) or counter-currently to the material. Flights, or material lifters, pick up the material and drop it during rotation, creating a cascade of material in the drum’s cross section, which maximizes heat transfer between material and gas. Indirect rotary dryers, which are heated externally and dry material via contact with the heated shell, are also available.
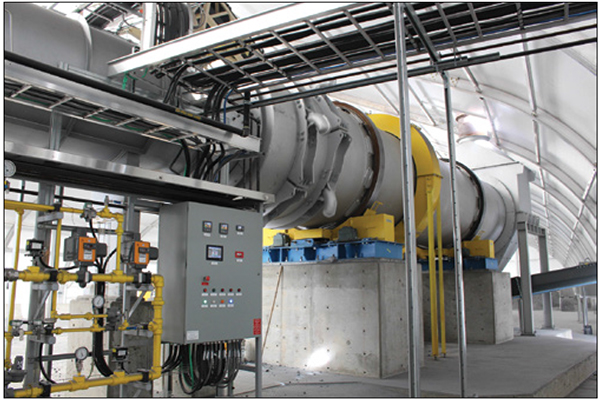
FIGURE 2. Rotary dryers work by dropping material through a stream of hot air in a rotating drum
Fluidized-bed dryers. Fluidized-bed dryers work by suspending a bed of material in air via a perforated plate through which combustion gases are passed in an enclosed vessel (Figure 3). This fluidization increases the surface area available to drying by surrounding each and every particle with air. Different fluidization “regimes” or patterns of fluidization can be used to tailor the drying process to the material’s specific challenges.
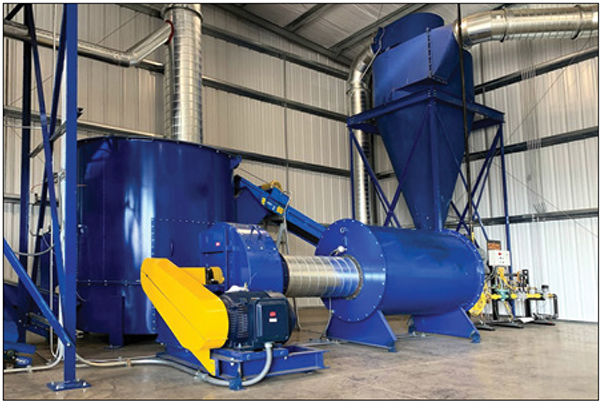
FIGURE 3. Fluidized-bed dryers work by suspending a bed of material in air via a perforated plate through which hot gases are passed in an enclosed vessel
Both dryer types utilize convective heat transfer and rely on how well solids and gas are in direct contact.
Material characteristics
A number of different characteristics of the solids to be dried ultimately play a role in dryer design, the most important of which are outlined here. Combined, these characteristics influence dryer design and process criteria such as the following:
- Temperature profiles
- Airflow velocity
- Retention (residence) time
- System pressures
- Unit size
- Percent fill
- Feed and product flowrates
- Rotational speed (rotary dryers only)
It’s important to note that in addition to impacting the equipment and process parameters, material characteristics may also, in some cases, influence the choice between which dryer is most appropriate for the application at hand.
Inlet and outlet moisture. The inlet (existing) and outlet (desired) moisture content of the material sets the overall drying objective: the amount of moisture the dryer will be tasked with removing.
The inlet moisture will also determine whether or not any sort of moisture-reduction pretreatment will be necessary. An additional pretreatment step may also be desirable if the difference between inlet and outlet moisture is considerable. While both rotary and fluidized-bed dryers offer effective moisture removal, removing a substantial amount of moisture in a single unit is often inefficient or impossible.
An especially high moisture content can also affect the flowability of the solids, which in turn influences their behavior in the dryer. A moisture content that promotes a free-flowing consistency is ideal in all settings, no matter the type of dryer.
An appropriate moisture content is critical to the effectiveness of both dryer types, but is particularly important in the fluidized-bed dryer, because of its influence on minimum fluidization velocity. A high-moisture material will require significantly more airflow and energy to fluidize, making the process inefficient.
Rotary dryers are perhaps slightly more tolerant of a high-moisture material, but could still experience challenges that must be designed around, most notably sticking at the inlet.
As a result, whether utilizing a rotary dryer or fluidized-bed dryer, materials with a high moisture content will often require some level of pretreatment prior to the drying unit.
Bulk density. A material’s bulk density defines the volumetric capacity of the rotary dryer. In rotary dryers, this expected load helps determine the sizing of mechanical and drive components.
In a fluidized-bed dryer, as with moisture content, which adds weight, the bulk density will influence the minimum fluidization velocity, or the airflow velocity required to achieve baseline fluidization.
Specific heat. The specific heat (the amount of energy required to raise the temperature of the material) influences how much energy will be required, in this case to bring the material up to the temperature required for moisture removal.
Along with the heat of evaporation for water, this will in turn determine the overall heat input required.
Heat transfer properties. How a material holds its moisture (internally or on the surface) also has ramifications for the dryer design process, again playing into the amount of energy that will be required to reach the target moisture content.
In the case of rotary dryers, heat transfer properties also influence whether the dryer should be designed for co-current or counter-current operation. For example, when a material holds its moisture internally, the counter-current design is beneficial, because it puts the hot material in contact with the hottest gases at its driest state, just prior to discharge, which can help to draw out any remaining moisture.
In contrast, the counter-current design would not be suitable for a heat-sensitive material. Exposing the material to the hottest combustion gases while in its driest state could result in overdrying and product degradation.
Also in the case of rotary dryers, a heat-sensitive material may require the incorporation of a combustion chamber in order to prevent direct contact between the burner flame and material, thereby reducing potential for product breakdown.
Fragility. A material’s propensity for degradation is also important to consider.
In a rotary dryer, a material prone to breakage may require a rolling section without flights at the dryer inlet to give material time to harden before being introduced to the lifting/dropping action imparted by the flights.
In a fluidized-bed dryer, a friable material may require a more gentle fluidization regime in order to minimize breakage that can be caused by particles rubbing against each other while suspended.
Particle size and shape. Particle size distribution and shape are also important characteristics to consider in designing a drying process.
Depending on a material’s bulk density and moisture content, particle size typically becomes an issue once it exceeds around 0.5–1 inch in fluidized-bed dryers, due to the energy required to fluidize the material.
In a rotary dryer, particle size has an impact on the airflow velocity, which in turn has ramifications on drum diameter.
Larger particles also generally require a longer retention time to remove the desired amount of moisture, though how the material holds its moisture also plays into this.
Irregularly shaped particles are also harder to dry than uniform ones. With both dryer types, this could mean pretreatment to reduce the particle size distribution (PSD) or make the particle shape more uniform. Fibrous materials can also present problems, “netting” smaller particles together into a larger mass.
Abrasion and corrosion. Materials with abrasive or corrosive qualities must be considered in terms of materials of construction for both dryer types. Further, since the rotary dryer shell is consistently in contact with the material in motion, shell thickness may also be used as a tool to deter wear.
When the material is corrosive, dryer manufacturers should minimize potential points of buildup through design and fabrication, as buildup can promote corrosive wear. This might mean grinding welds smooth, changing feed-hopper design or taking other measures.
End use. While not as commonly influential as some other material characteristics, the intended end use of the product can also factor into the drying process.
In the case of rotary dryers, a material’s end use may dictate whether the dryer is of the direct or indirect configuration. While most rotary dryers utilize the direct design, in special cases where material must remain sterile or where a fine particle size risks material entrainment in the gas flow, the indirect dryer can offer an effective alternative.
Feedstock uniformity. The importance of feedstock uniformity cannot be stressed enough. Non-uniform feedstock is often the culprit behind unexplained product quality issues, inefficiencies and process upsets.
While rotary dryers are recognized for their tolerance of slight variations in feedstock parameters, it is still true that the more uniform the material going into the dryer, the more uniform the material that will come out.
In fluidized-bed dryers, feedstock uniformity is of the utmost importance. Fluidized-bed dryers are intolerant to even the slightest variation in parameters, resulting in upset. For this reason, operations expecting some level of variation may be better served by a rotary dryer or other drying technology.
Establishing drying parameters
Due to the variation that can exist across materials and even among the same material from different sources, process development testing is often an essential step in developing a successful drying process and de-risking the path to commercial-scale production.
Batch- and pilot-scale testing services give producers the opportunity to gain a familiarity with their unique source of material and how it responds to the drying process.
Producers can evaluate the characteristics listed above (among others) alongside various process conditions and equipment configurations in order to achieve the most efficient design possible.
These types of services can also be used to troubleshoot or optimize an existing process, a trend becoming increasingly common as producers look to mitigate even the smallest inefficiencies.
Influencing factors such as airflow velocity, dryer size, percent fill, and more, material characteristics form the foundation of the bulk-solids drying process, in the case of both fluidized-bed and rotary dryers. Ensuring a system is designed with characteristics, such as bulk density, heat transfer, particle size and more in mind, will help to achieve a system optimized for efficiency and longevity. As such, process development testing is often an essential step in developing or optimizing a commercial-scale drying system. n
Edited by Dorothy Lozowski
Acknowledgements
All figures have been supplied courtesy of FEECO.
Author
Nick Reckinger has been in Process & Bioresources sales for more than 17 years at FEECO (3913 Algoma Road, Green Bay, WI 54311; Tel: 920-468-1000; Website: www.feeco.com). He holds an M.S. degree in environmental science and policy. Reckinger specializes in developing equipment and systems designed to maximize value from organic wastes, assisting clients with everything from initial concept and feasibility testing through to project completion.