While the explosion risk of certain hazardous or toxic materials may seem readily apparent, the potential explosivity of otherwise benign materials — flour, cocoa, starch, grains, and coal dust, for instance — often goes unrecognized. In reality, almost any combustible solid with a particle diameter less than 420 micrometers (40 mesh) can explode under the right conditions, as has been tragically demonstrated by several catastrophic dust explosions that have occurred over the past several years.
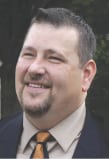
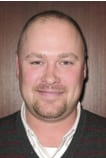
“The use of both proper maintenance, prevention and add-on engineered controls cannot be stated strenuously enough,” says Vince Barreto, Fike global product manager for explosion-protection systems (Booth 521, Blue Springs, Mo.). Procedural measures include efforts to minimize dust buildup in the plant environment, maintain oxygen levels below critical thresholds in enclosed spaces that may contain airborne particles, and eliminate ignition sources. Active explosion-protection methods include the use of advanced devices that monitor potentially hazardous conditions and respond within milliseconds to quench the event, explosion-relief venting that directs an enclosed explosion to a safe location, fast-acting mechanical-isolation and diverter valves to halt flame propagation through piping and ductwork, and chemical-suppression systems that are able to detect an incipient explosion at its earliest stages.
In his workshop, entitled “Safely Venting Explosions Inside Your Facility,” which will be presented Wednesday November 18, at 3:00 p.m. in Theater B, Barreto will focus on one particular aspect of dust explosion protection — the need to properly vent potential explosions that can occur within equipment components located inside process plants.
“Facilities that decide not to employ active suppression systems tend to rely on the use of vents and ductwork — a passive approach that aims to safely release hot gases, pressure and flames associated with an explosion. When the protected vessel is located inside the facility, the combustion constituents must be directed to a safe location outside,” says Barreto. “Unfortunately, this approach is not optimal and ductwork must be directed to exterior areas where personnel are not present.” Other safety problems often arise in terms of back-pressure hazards, the risk of secondary combustion inside longer ducts, and the risk that ductwork may collapse if not designed and constructed to hold the appropriate pressures and temperatures. Barreto also notes that the latest revision of NFPA 68 (Standard on Explosion Protection by Deflagration Venting, Section 6.8, Revision 2007, from the National Fire Protection Assn.) “severely restricts the ability to use the passive ducting option for explosion mitigation.”
In addition to reviewing the latest applicable NFPA standards, combustible dust hazards, and effective venting options, Barreto will discuss flameless venting devices. Flameless venting devices rely on a series of densely packed screens, and when attached to the explosion vents on baghouses, spray dryers, storage silos, grinders, bucket elevators and other vessels that are susceptible to dust explosions, they “pull heat from the flame ball, quench the flame and relieve the pressure” inside the enclosed apparatus.
Showcasing an advanced rupture disc
The need to protect against overpressure conditions in systems handling liquids and gases is equally important. In a workshop entitled “Axius: The Most Advanced in Rupture Disc Technology,” ( Wednesday November 18, 1:00 p.m., Theater B), Michael Zitariuk, Fike’s global product manager for pressure relief, will showcase some of the inherent advantages of the company’s ASME-certified Axius series rupture discs (for both liquid and gas service) for overpressure protection.
The Axius disc is manufactured using Fike’s patented G2 technology (an alternative to the conventional scoring or coining processes that involve no hard-tooling). The result is a rupture disc “with improved performance, accuracy and opening characteristics,” says Zitariuk. “With no score marks or stress zones that can fatigue prematurely, Axius has unsurpassed cycling capability, and provides the best-in-class combination of cycle life, 95% operating ratio and KR (flow-resistance) values,” he says.
The Axius has been cycle tested from full vacuum to 95% of the marked burst pressure in excess of 100,000 times and then burst within tolerance, even at the lowest burst pressures available. “Many other discs will simply fatigue and fail prematurely under such conditions,” says Zitariuk. A sanitary version — the Axius SC — is available for installation directly between standard ASME BPE ferrule configurations and features the same performance capabilities as the non-sanitary version.
He will also discuss how proper rupture disc selection can provide long-term cost savings by extending the preventive maintenance schedule and reducing unplanned downtime, unwanted product losses, and fugitive emissions.
Suzanne Shelley
For a recent related article, see Preventing Dust Explosions, Chemical Engineering, October 2009, pp. 49–51.