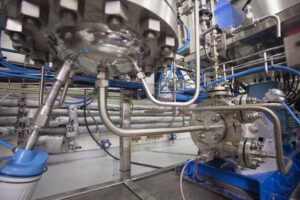
Source: thyssenkrupp Uhde
Thyssenkrupp Uhde Thailand has been awarded a contract by BASF SE (Ludwigshafen, Germany) for engineering services and proprietary equipment supply for its new non-ionic surfactant (NIS) plant at its Zhanjiang Verbund Site Project, Guangdong Province, China. The plant will employ thyssenkrupp Uhde GmbH’s (Dortmund, Germany) proprietary jet loop reactor technology. Non-ionic surfactants are typically produced from an alcohol starter and oxides by alkoxylation. Surfactants are widely used as emulsifiers in cosmetics, pharmaceuticals, and many other applications such as grease removers, household cleaners, washing-up liquid or herbicides.
“We are very proud that BASF has selected thyssenkrupp Uhde as the technology provider based on our advanced jet loop reactor technology and expert know-how. Thyssenkrupp Uhde feels honored to contribute to BASF’s success story in China”, says Brian Cameron, CEO thyssenkrupp Uhde Thailand. The Thailand branch of thyssenkrupp Uhde combines strong technical expertise in the field of alkoxylation, esterification and amination with comprehensive services: R&D in its own laboratory and pilot plant facility as well as licensing, engineering, procurement, modularization, and construction.
Thyssenkrupp Uhde’s jet loop reactor (photo) represents advanced reactor technology specifically suitable for heterogeneous and highly exothermic reactions. The absence of moving parts in the reactor brings with it superior features in terms of safety. The venturi-type jet mixer has been optimized to ensure intimate contact and a superior interface between reactants. The continuous circulation of both liquid and gas phase results in perfect mixture homogeneity and avoidance of hot spots. This offers significant sustainability, safety, batch time and product quality advantages over stirred reactor technology. The proprietary jet loop reactor is already in operation in over 50 plants worldwide, delivering top quality products all over the world.
thyssenkrupp Uhde also provides a modularized plant concept. This means that the complete plant would come in prefabricated skids which are delivered to the construction site and installed in complete blocks. As these blocks are manufactured in a highly controlled environment in thyssenkrupp-supervised module yards, this approach significantly improves quality and safety while reducing overall risk to the project’s schedule by minimizing site construction activities.