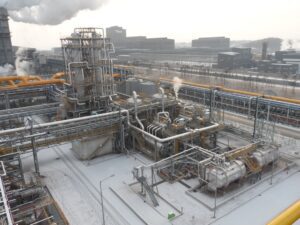
Source: thyssenkrupp
ArcelorMittal Belgium (Ghent, Belgium) has awarded thyssenkrupp Uhde GmbH (Dortmund, Germany) an order for a desulphurization plant to be installed at its Ghent site. The main aim of this brownfield project is to enhance the existing coke-oven-gas treatment plant with a state-of-the art sulfur removal and recovery unit. The new units are planned to go into operation in July 2023.
“This project marks another milestone in making our plant in Ghent more environmentally friendly. It is a major effort for the whole industry, and we are taking diligent steps towards our aim to reduce SOx emissions”, says Jeroen Van Lishout, COO Primary of ArcelorMittal Belgium.
The original coke plant was built by thyssenkrupp Uhde’s coke plant specialists 25 years ago, then under the name of Thyssen Still Otto company. “We are glad for the continued trust of our customer ArcelorMittal” says Michael Petzinna, executive director of the Coke Plant & Inorganic Acids operating unit. “With our advanced technologies and project execution capabilities we can deliver a technical solution that is tailor-made for their needs.” thyssenkrupp Uhde will install its proprietary processes Cyclasulf for desulfurization, as well as the Monoclaus for a highly efficient sulfur recovery.
As in all brownfield projects, specific requirements had to be met. In this case, the existing gas-treatment unit also required a new back-up system for the existing part. Thyssenkrupp Uhde was able to offer a smart solution which links existing and new process trains of the Cyclasulf process. This well-established, advanced solution for coke oven gas desulfurization removes hydrogen sulfide and ammonia from coke-oven gas very efficiently. The acid gas stream is concentrated and prepared for further processing, either to sulfur or sulfuric acid. In Ghent, elemental sulfur will be recovered. Modern mass transfer elements significantly reduce the size of the required equipment, keeping the footprint low.
The same is true for the state-of-the-art Monoclaus process for sulfur recovery and ammonia decomposition. It enables the production of liquid pure sulfur utilizing a minimum number of equipment and pipelines compared to conventional Claus plants, which results in a very compact arrangement and footprint. One could say that the Monoclaus principle is: the simpler, the better — but with the same high product quality and process safety. By realizing this new back-up plant, ArcelorMittal Ghent will be able to operate a low-emission desulfurization plant during maintenance or inspection shutdowns, effectively replacing the former recovery plant which had a lower desulfurization capacity.