Good troubleshooting skills are invaluable in chemical engineering practice. While their value is clearly gleaned from the impact they have on plant performance, it is also a reflection of the intangible process of learning them. Last month, at the AIChE Spring meeting in Chicago, Ruth Sands, former CE author and mass transfer consultant at DuPont Engineering Research & Technology, presented attendees of the Distillation Topical Conference with troubleshooting tips from those who do it best*. They just so happen to amount to ten, and have relevance across the profession.
1. Safety first: Assess the SHE (safety, health and environment) issues and implement a temporary solution to give time for troubleshooting. Rushing can lead to safety hazards.
2. Good troubleshooters understand the basics well. Use calculations, models, experiments and so on to check your theories. Know what is important and what is not.
3. Know what to expect before you start. What temperature, pressure profile should you expect? What quality of separation should you expect? Have a feel for what is reasonable based on a variety of experiences. And, last, but not least, “Don’t ever be afraid to do a simple material and energy balance. It will tell you a million things.”
4. Do not overlook the obvious. However, correcting obvious problems does not necessarily solve the whole issue. Be patient.
5. The so-called mental model both helps and hurts the troubleshooting process. “Good troubleshooters have a willingness to accept the data rather than their own theories.” But, “Don’t let the data get in the way of a good theory.”
6. Think of ways to challenge the mental model. Is the process at steady state? Visualize what is happening. Imagine yourself as a pocket of liquid or vapor looking for the easiest path. Think of everyday analogies. Processes are the same that occur in the kitchen, bathroom or yard. And as Izak Nievwoudt, R&D director, Koch-Glitsch, commented, “A lot of troubleshooters look for the smoking gun, but it can be a cluster problem.”
7. Testing strategy advice varies considerably, and depends on your situation. Testing should begin with the easiest to prove or disprove and not be based on how likely the theory is. Do all practical tests before making a permanent change.
8. Believe your instruments, unless you have a good reason not to. Don’t start by questioning your instruments. What scenario could cause these data to be true? Instruments report information as they see it.
9. Use people as sources of information. Operators can be powerful resources. They know how to make their own equipment work. What do you see? What do you do in response? What do you do to fix it? Listen to all sources. See value from different viewpoints (level, experience, function personalities). Seek out unsolicited opinions and contrary views. Listen more than talk. Use a learning attitude. Implying that someone screwed up is a sure way to get no cooperation.
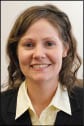
10. Learn through examples. Incident investigations give ideas for modes of failure. Good investigations cover people, equipment and the system. Participate in startups, especially in new plants. It compresses the learning. Startups from shutdowns are also opportunities. A person that learns from others’ failures is wise.
Rebekkah Marshall
* Sands pulled suggestions from three books (see references in the online version) and interviewed the following troubleshooting experts: Jose Bravo, chief scientist, Shell Global Solutions; Henry Kister, director of Fractionation Technology, Fluor Corp.; and several of her DuPont colleagues: Ed Longwell, principal engineer, Jeff Loomis, senior engineer, Nick Sands, technology fellow, Teresa Thomas, senior engineer, Jean Trotter, consultant and Bob Trotter, engineering fellow (retired).