Vinyl acetate (also known as vinyl acetate monomer; VAM) is important in the manufacture of many polymers and resins. The greatest demand for vinyl acetate is associated with the production of polymers and copolymers, mainly poly(vinyl acetates) used in papermaking, textiles, sealants, binders and coatings; ethylene vinyl acetate, used as a film, in hot-melt coatings and adhesives; as polyvinyl chloride (PVC) alternative; and ethylene-vinyl alcohol, used in food packing and medical applications.
VAM is a colorless liquid with a sweet, fruity smell, soluble in most organic solvents, but only slightly soluble in water. On an industrial scale, the dominant production route of vinyl acetate is based on the reaction of ethylene with acetic acid and oxygen in the gas phase over heterogeneous catalysts that contain palladium.
The main grades of vinyl acetate are technical grade; grade A (99.8%, diphenylamine inhibited); and grade H (99.8%, hydroquinone inhibited).
Production process
The production of VAM from acetic acid and ethylene (Figure 1) comprises three major sections: (1) reaction; (2) separation; and (3) purification.
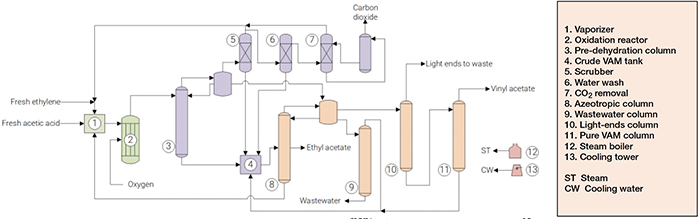
FIGURE 1. The diagram shows the process for manufacturing vinyl acetate monomer from acetic acid and ethylene
Reaction. Make-up and recycled acetic acid pass through a vaporizer, along with fresh and recycled ethylene. The feed stream, containing excess of ethylene over acetic acid, is mixed with oxygen, preheated and fed to multi-tube reactors. The reaction occurs over palladium and gold catalysts. Heat is removed by evaporative cooling on the reactor shells. At the end, 8–10 wt.% of ethylene and 15–35 wt.% of acetic acid are converted to vinyl acetate. Water, CO2 and small quantities of ethyl acetate, ethylidene diacetate and glycol acetates are the main byproducts.
Separation. The reactor effluent is cooled and fed to the pre-dehydration column, where a crude VAM stream is withdrawn from the bottom and stored. The overhead stream is separated into an organic phase, recycled to the column, and an aqueous phase, directed to a decanter downstream. Uncondensed gases are washed by acetic acid. The solution formed is routed to the crude VAM tank, while gases from the scrubber are recycled to the reaction. Part of this gas mixture is washed with water to remove residual acetic acid, and also directed to the crude VAM tank. After water wash, gases are directed to an absorption column, for CO2 removal by a potassium carbonate solution.
Purification. In the azeotropic column, a VAM-water mixture is distilled and fed to a decanter, along with the aqueous phase separated in the pre-dehydration. Here, an organic phase containing VAM is separated and directed to the light-ends column, while an aqueous phase is routed to the wastewater column, which separates residual VAM from wastewater. Ethyl acetate is withdrawn and discharged, and acetic acid is recycled to the vaporizer. The light ends column strips off acetaldehyde and other volatile compounds from the crude vinyl acetate. Finally, residual acetic acid and heavy-ends are removed in the pure VAM column, yielding a vinyl acetate with 99.9 wt.%.
Production pathways
In addition to the route discussed here (the most common one), VAM may also be produced by the addition of acetic acid to acetylene, addition of acetic anhydride to acetaldehyde, reaction of ethylene with acetic acid and oxygen and the reaction of methyl acetate or dimethyl ether with carbon monoxide and hydrogen. Different pathways for VAM production are presented in Figure 2.
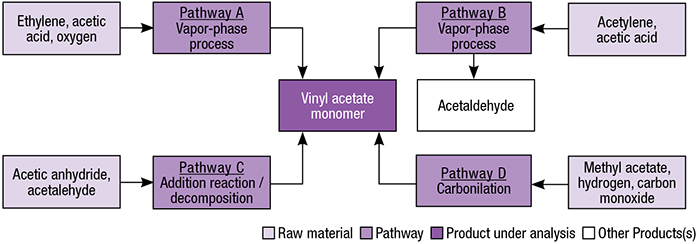
FIGURE 2. Shown here are several pathways for the production of VAM
Editor’s note: The content for this column is developed by Intratec Solutions LLC (Houston; www.intratec.us) and edited by Chemical Engineering. The analyses and models presented are based on publicly available and non-confidential information. The content represents the opinions of Intratec only.