Sodium hydroxide (NaOH) is a white, translucent crystalline solid that is widely used in the chemical process industries (CPI). NaOH is often referred to as caustic soda, due to its corrosive action on many substances: it decomposes proteins at room temperatures and may cause chemical burns to human bodies. Although it does not occur in nature, NaOH has been manufactured at large scale for many years from readily obtainable raw materials and is used in numerous industrial processes (Figure 1).
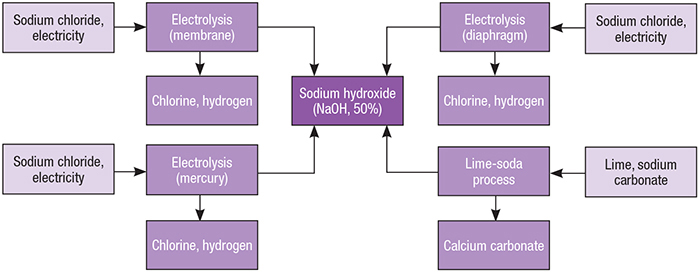
Figure 1. Several processes involving the electrolysis of salt brine, along with one using lime soda and sodium carbonate, can be used to produce sodium hydroxide
Sodium hydroxide is mainly used in pulp and paper manufacturing, alumina extraction from bauxite in aluminum production, as well as in the textiles industry and drinking water production. NaOH is also an important compound in the manufacture of soaps and detergents, in waste gases scrubbing, saponification and etherification and esterfication reactions; as well as in basic catalysis.
Pure NaOH has a high affinity for water and may form hydrates depending on the concentration. Since some hydrates have melting points greater than 0°C, insulation or heating during storage and transportation considerations may be required. Additional care is required because in the presence of moisture, NaOH readily reacts with atmospheric carbon dioxide to form sodium carbonate. Shipping NaOH can be accomplished in steel drums for concentrations up to 50%. For higher concentrations, pure nickel drums are required due to corrosion effects.
NaOH production process
The production of NaOH from sodium chloride (NaCl) comprises three major sections: (1) brine purification; (2) electrolysis; and (3) product recovery (Figure 2).
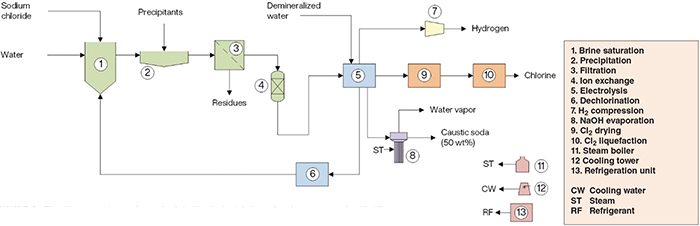
Figure 2. The diagram shown here depicts the industrial production process for NaOH
Brine purification. Initially, recycled depleted brine is mixed with water and re-saturated with fresh NaCl. Heavy metal ions (for example, Ca2+ and Mg2+) present in the brine would be harmful to the membranes. So the brine is treated with precipitants in such a way that the metals precipitate, forming a sludge, which is removed by settling in a clarifier. Subsequently, the clarified solution is filtered and then purified by ion-exchange resins to remove residual hardness and achieve acceptable levels.
Electrolysis. The ultrapure brine and electricity are the main inputs to the electrolysis area. The brine is fed into the anolyte compartments of the cells, separated from the catholyte by cation-exchange membranes. Chlorine gas is generated at the anodes and sodium ions migrate through the membranes into the catholytes. The depleted brine from the anode compartments is dechlorinated downstream and then returned to the brine saturation stage. On the catholyte side, water is electrolyzed, generating hydrogen gas and hydroxyl ions. The membranes prevent the migration of such hydroxyl ions into the anolytes in such a way that hydroxyl ions combine with the sodium ions, forming caustic soda. The addition of demineralized water keeps the catholytes concentration at the desired level.
Products recovery. Hydrogen from the electrolysis process is compressed and directed to consumers. The caustic soda solution is concentrated to a saturated 50 wt.% NaOH solution — the commercialized form. The chlorine gas produced is sent to a drying system, consisting of drying towers, where concentrated sulfuric acid circulates as a dehydrating agent. The dry chlorine gas is compressed and then liquefied before being send to storage vessels.
Edited by Scott Jenkins
Editor’s note: Content for this column was originally developed by Intratec Solutions LLC (Houston; www.intratec.us) and is edited by Chemical Engineering. The analyses presented are based on publicly available and non-confidential information. The content represents the opinions of Intratec only. More information about the methodology for preparing the analyses can be found, along with terms of use, at www.intratec.us/che.