Linear alpha olefins (LAOs) are hydrocarbons with the chemical formula CnH2n, characterized by linear chains and one double bond at the alpha position (Figure 1). Such hydrocarbons are important chemical intermediates, widely used in several industrial and consumer products according to carbon number and chemical structure.

Figure 1. LAOs are hydrocarbons with a double bond in the alpha position
C4–C8 olefins are used as co-monomers in the production of linear low-density polyethylene (LLDPE) and high-density polyethylene (HDPE), while C12–C16 olefins are used in manufacturing detergents, sanitizers and personal care products.
The copolymerization of LAO with ethylene in the production of HDPE impart properties like toughness and stress-crack resistance, required for several applications. When used as a comonomer in the production of LLDPE, LAO enhances the polymer’s toughness, tear strength and impact resistance, making it suitable for end uses like toys, grocery bags, and food and beverage containers.
LAOs are also the raw material for several surfactants, such as primary alcohols, alcohol derivatives, alcohol ethoxylates and alpha-olefin sulfonates. Other applications for LAO are synthetic lubricants, oilfield chemicals and plasticizer alcohols.
Most commercial LAO production is based on ethylene oligomerization, carried out by a number of processes. Ethylene oligomerization typically produces a broad range of even-numbered alpha-olefins, with the distribution of olefins produced largely influenced by the catalysts used. Some processes, in turn, target specific olefins — mainly 1-butene, 1-hexene and 1-octene. These are called “on-purpose” technologies.
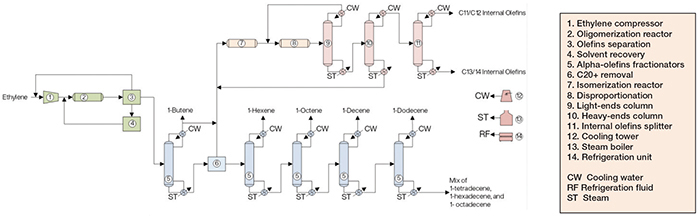
Figure 2. The diagram shows a process for the production of linear alpha olefins
Process
LAO production from ethylene comprises three major sections: ethylene oligomerization; alpha-olefins fractionation; and internal olefins formation and fractionation.
Ethylene oligomerization. Fresh ethylene and unreacted ethylene recovered downstream are compressed and fed, along with a catalyst mixture, to a plug-flow reactor, where oligomerization takes place. The reactor effluent is sent to the olefins separation stage, where unreacted ethylene is recovered to the compressor upstream, and an alpha-olefin stream is sent to the C4 column downstream. Also, a stream is routed to the solvent recovery area, where solvent is removed and returned to the reactor.
Alpha-olefins fractionation. The alpha olefins are sent to subsequent columns, starting at the C4 column. Each column removes the lightest olefin as an overhead stream, which is condensed and stored. The bottom stream from each column, containing heavier olefins, is routed to the next column. The overhead of the C4 column is partially sent to storage, with the remainder being sent to an isomerization reactor downstream. The column bottom is sent to a section where a C20+ stream is obtained and sent to the isomerization reactor, and a C6+ stream is routed to the C6 column. In this section, 1-hexene, 1-octene, 1-decene, 1-dodecene and a mix of heavy alpha olefins are also obtained.
Internal olefins formation and fractionation. The 1-butene stream from the C4 column is mixed with a C20 + stream from upstream and fed to the isomerization reactor, where alpha olefins are converted into internal olefins. The isomerization products are sent to a disproportionation reactor, where lower-molecular-weight olefins react with higher-molecular-weight olefins, yielding olefins of intermediate molecular weight. These compounds are routed to a heavy-ends column, which separates C15+ olefins (which are returned to isomerization) from C11–C14 olefins, which are routed to a splitter and divided into C11/C12 and C13/C14 streams. These streams are directed to storage vessels.
Production routes
First prepared by wax cracking in the 1960s, LAOs can be now produced from different routes. Globally, the largest volume of LAO has been produced from ethylene oligomerization, Fischer-Tropsch synthesis followed by purification and, to a lesser extent, alcohols dehydration. There is also research focusing on the production of LAO from renewable sources.
Editor’s note: The content for this column is developed by Intratec Solutions LLC (Houston; www.intratec.us) and edited by Chemical Engineering. The analyses and models presented are based on publicly available and non-confidential information. The content represents the opinions of Intratec only.