Citric acid is a naturally occurring tricarboxylic acid commonly found in plants and animals (Figure 1). In its pure form, it is a colorless compound readily soluble in water. Citric acid is mainly used to add taste to food and soft drinks, and as acidulant for dietary supplements and pharmaceuticals. It is also used as the following: an anticoagulant; mineral flotation agent; industrial cleaning/electroplating/anodizing reagent; animal food additive (digestion aid); and water treatment agent. Citric acid can be used in the manufacture of other products, including: dibasic ammonium citrate; ammonium ferric citrate; calcium citrate; citrazinic acid; citrated fatty acid glycerides; lithium citrate; potassium citrate; sodium citrate; tri-n-butyl citrate; and triethyl citrate
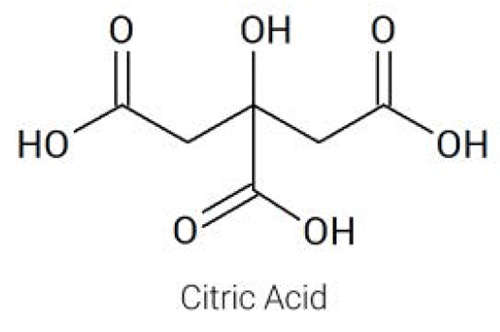
FIGURE 1. Citric acid is used in a variety of applications, including for taste in foods and beverages
Citric acid can be obtained from natural sources (for example, lemons, limes and oranges) and can be synthetically produced either via chemical reaction or microbial fermentation. Large-volume industrial production of citric acid, however, is based almost exclusively on microbial fermentation of a carbohydrate substrate, in which a strain of Aspergillus niger is employed to convert sugar to citric acid. Raw materials commonly used are molasses, sugar (raw beet, refined beet), cane sugars, syrups (prepared from wheat, corn, potato or other starch).
Production process
Citric acid production from corn starch comprises three major sections: (1) corn starch saccharification; (2) fermentation; and (3) products treatment (Figure 2).
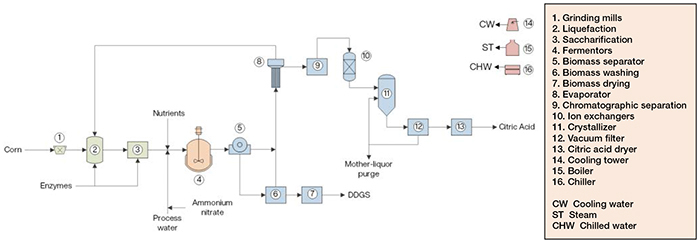
FIGURE 2. The diagram shows a process for making citric acid by fermenting corn sugars
Corn starch saccharification. Corn is fed to hammer mills to be crushed into a coarse grind meal containing all kernel components. This meal is routed to a liquefaction vessel, along with hot process condensate and alpha-amylase enzymes. The corn starch is enzymatically hydrolyzed, producing maltose and higher oligomers. The slurry from this step is sent to a saccharification tank, where it is mixed with gluco-amylase enzymes, which cleave the maltose and higher oligomers into glucose.
Fermentation. Glucose is mixed with process water, nutrients and ammonium nitrate, and fed to the fermenters. Fermentation is performed in fed-batch mode and under aerobic process conditions in agitated, jacketed fermentors. After glucose exhaustion, the batch phase is finished, and the fed-batch phase is started. During the fed-batch phase, glucose and nutrients are continuously supplied.
Products treatment. After the fermentation step, the fermentation broth is sent to a rotary vacuum filter, separating non-fermented biomass (which is sent to a wash step) from a liquid stream containing citric acid that is routed to the evaporation stage. The biomass is centrifuged and washed for citric acid recovery, which is sent to evaporation, while the biomass cake is dried in a rotary dryer, generating dried distiller’s grains with solubles (DDGS) byproduct. In the evaporation step, the broth is concentrated, and then sent to chromatographic separation equipment to remove biomass residues, while the vapor is condensed and recycled to the liquefaction area. The citric acid solution is then fed to ion-exchange column for separation of magnesium and potassium ions, and to a crystallizer, forming citric acid crystals, which are routed to a vacuum filter to be separated from the mother liquor. Most of this liquor is returned to crystallization upstream, but a fraction of it is purged to avoid impurities build-up. The solid citric acid cake is directed to a rotary dryer to remove residual water, then sent to blending silos and packaging, from which bulk and bagged citric acid are obtained, respectively.
Product grades
The uses and applications of citric acid vary according to the product grade. The main forms of citric acid are: U.S. Pharmacopeia (USP) grade; reagent grade; and monohydrate grade. This organic acid may be produced in crystalline form, anhydrous, with several granulations; or in solutions with different concentrations (for example, 50% w/w), with grades varying in appearance, purity and color.
Editor’s note: The content for this column is developed by Intratec Solutions LLC (Houston; www.intratec.us) and edited by Chemical Engineering. The analyses and models presented are based on publicly available and non-confidential information. The content represents the opinions of Intratec only.