Adipic acid (hexanedioic acid; Figure 1) is among the most important aliphatic dicarboxylic acids, with about 2.5 billion kg produced annually. It is isolated as odorless, colorless crystals with an acidic taste. Adipic acid undergoes the reactions of carboxylic acids, reacting at one or both carboxylic acid groups to form salts, esters, amides, nitriles and so on. Because of the bifunctional nature of this acid (Figure 1), it is used in a number of industrial polymerization processes.
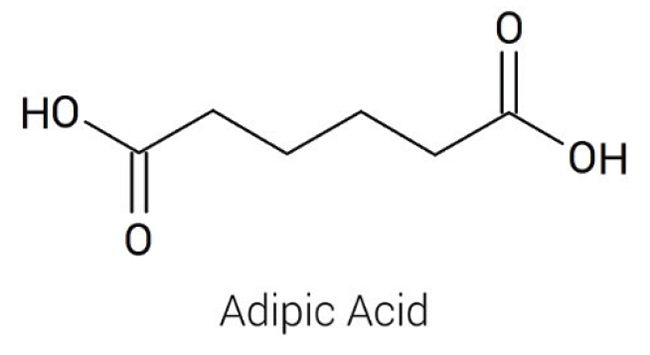
Figure 1. Adipic acid is an industrially important 6-carbon dicarboxylic acid
Most adipic acid is used captively by the producer in the manufacture of nylon-6,6 polyamide, prepared by reaction of adipic acid with 1,6-hexanediamine. Adipic acid is also used for a wide range of applications, including: conversion to esters; in placticizers, lubricants and polyurethane resins; as an acidulant for gelatins and jams; as a food additive for buffering or neutralizing; to make insect repellent; as a starch crosslinking agent; and as an intermediate for paints.
Commercial production of adipic acid has been predominantly based on cyclohexane and, to a lesser extent, phenol. In light of shifts in hydrocarbon pricing, alternative adipic acid production routes have been researched, mainly based on butadiene and cyclohexene feedstocks. Adipic acid may also be produced from renewable sources (bio-adipic acid).
Adipic acid, when dispersed as a dust, is subject to dust explosion, so the acid is conveyed pneumatically (or mechanically) from the drying equipment to the shipping or storage container. The material should be stored in corrosion-resistant containers, away from alkaline or strong oxidizing materials. The containers can be made of aluminum or stainless steel, and the quantities range from 50-lb. bags to 200,000-lb hopper cars. In storage, adipic acid tends to cake, depending on particle size and moisture content, so it is recommended to use hermetically closed containers in storage.
Process
The process for production of adipic acid from cyclohexane comprises two major sections: A first oxidation step; and a second oxidation step (Figure 2).
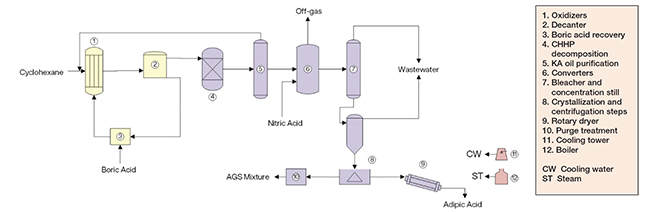
Figure 2. The process diagram shows the production of adipic acid from cyclohexane
First oxidation step. Initially, cyclohexane is fed to the first of several staged air oxidation vessels, along with metaboric acid. In the presence of cobalt naphthenate catalysts, the cyclohexane is oxidized in the liquid-phase to cyclohexylhydroperoxide (CHHP). In the presence of boric acid, the CHHP is trapped as cyclohexylperborate ester, which in turn reacts with cyclohexane, yielding borate ester and cyclohexanol. The borate ester formed is relatively stable, so the generation of undesired byproducts is minimized. Next, the ester is hydrolyzed, yielding cyclohexanol and boric acid, which is dehydrated and recycled to the oxidation step. Subsequently, the CHHP still present in the oxidation product is decomposed by another oxidation reaction over a fixed bed of cobalt catalysts, yielding a cyclohexanol-cyclohexanone mixture known as KA oil.
Second oxidation step. The KA oil is then reacted with nitric acid in the presence of copper/vanadium catalysts to form adipic acid. While this second oxidation step is very exothermic, a high ratio of nitric acid to KA oil is established, so that the nitric acid also works as a heat sink, avoiding uncontrollable reactions. This oxidation reaction is extremely quick. It is carried out in two converters, operating at different temperatures. Most of the KA oil is oxidized in the first, low-temperature converter, with the remainder being converted in the high-temperature converter downstream. Nitrogen oxides and nitrogen are released from the reaction. While N2O and nitrogen can be viewed as nitric acid losses, NO2 and NO are further oxidized and recycled as nitric acid. After separation of water and monobasic acids from the oxidation product, then crystallization under vacuum and centrifugation, crude adipic acid is obtained. Finally, the crude adipic acid is re-dissolved in water, recrystallized, centrifuged and dried to yield fiber-grade adipic acid.
Editor’s note: The content for this column is developed by Intratec Solutions LLC (Houston; www.intratec.us) and edited by Chemical Engineering. The analyses and models presented are based on publicly available and non-confidential information. The content represents the opinions of Intratec only.