Taking a system approach to find the root cause of a problem can be more beneficial than simply replacing a problematic pump. This article explains why
We want the best reliability with anything that we work with. In a plant operation context, how many times do operators find themselves fixing problems and think they are improving reliability by simply buying a “better” pump, valve, process unit and so on? This only treats the symptom and not the root cause and is likely to result in the same problems as before.
There are many opportunities to dramatically improve reliability that are often overlooked. When the plant crew is working tirelessly to maintain day-to-day operation, it is easy to miss critical points that lead to poor system performance, maintenance issues, higher power consumption, downtime, product losses, lower profitability and higher costs. Taking a system approach to reliability improvement has many more benefits than a component approach.
Pump system reliability
If a system approach is so helpful, why might it not be considered? Individual system components are often designed without considering system interactions. Also, the effect of changing system requirements or operation changes may not be fully explored or understood for individual components. Relationships between various system components can be complex and unexpected. Cause and effect may be hard to define, and all parts of the system need to be considered together. More data are often needed for system analysis rather than component analysis.
The U.S. Dept. of Energy with Oak Ridge National Laboratory and Xenergy, Inc. conducted a survey in 1998 in the “U.S. Industrial Motor Systems Opportunities Market Assessment” to determine economically feasible opportunities to improve efficiency and reduce energy costs in industrial systems. The survey found that pump systems account for about 25% of the consumed energy in electric motors. Also, pump systems account for 20–60% of the electrical energy used in various industrial, water, and wastewater treatment facilities [1]. As you can see in Figure 1, pump systems have the greatest potential for electrical energy savings.
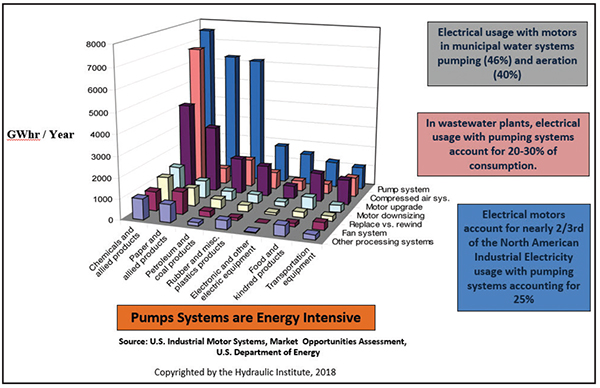
Figure 1. Electrical energy consumption of various industrial systems across multiple industries is shown here. Pump systems have greatest potential for electrical energy savings [1]
Pump-system reliability and electrical energy efficiency are closely related to each other. Improvements to pump-system efficiency will have a strong payoff in the electrical energy costs that can be saved. But the dramatic impact on reliability is significant and will be even more appreciated.
According to a Finnish Technical Research Center Report that evaluated close to 1,700 pumps across 20 process plants, the average pumping efficiency was below 40%. In the evaluation, 10% of the pumps operated below 10% efficiency [2]. This is alarming, but probably not surprising. Major contributing factors to minimal efficiency included throttled valves and pump over-sizing. That said, the efficiency value of the pump itself is not the most critical parameter. The best efficiency point (BEP) is of much more importance and is directly related to reliability.
The BEP for a pump is the specific flowrate at which the pump operates where it is most efficient. The primary goal of operation should be to operate as close to this flowrate as possible. When operating at flowrates away from the BEP flowrate, not only will the pump become less efficient, but it will also become less reliable due to various problems that will begin to present themselves.
Figure 2 presents a graph known as the Barringer curve, which relates a pump’s efficiency to its reliability. A typical example of a pump curve is plotted with its efficiency curve, which comes directly from the pump manufacturer. The BEP flowrate is identified with a vertical dotted line that crosses the efficiency curve at its maximum value. The reliability curve represents a qualitative measure of a pump’s mean time between failure (MTBF). The MTBF is equal to one at the BEP and represents the most amount of time that a pump will be able to operate until a failure of some sort. There are operating envelopes known as the preferred operating region (POR) and the allowable operating region (AOR). The POR is usually dictated by various standards such as ANSI/HI Standard 9.6.3-2017 or ANSI/API 610 11th Edition (2010). The POR brackets the flowrates at which it is desired to operate for as much as possible. Typically, the POR will range from 80% of BEP to 110% of BEP. Note that operating at the boundaries of the POR may reduce the MTBF of the pump by half.
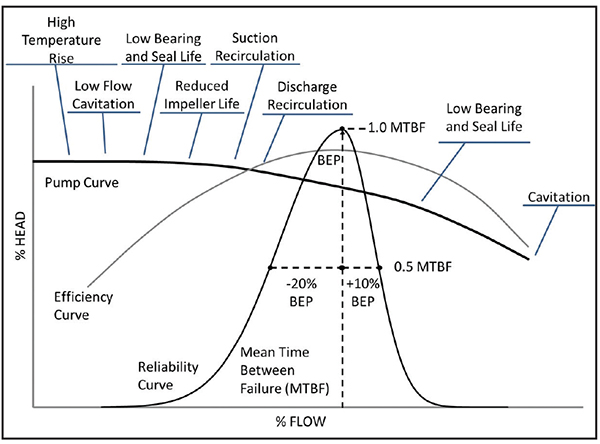
Figure 2. The Barringer curve relates pump performance to efficiency and reliability. Pump problems are highlighted in areas when operating outside the preferred operating region (POR) of 80 to 110% of the pump’s best efficiency point (BEP)
The AOR tends to be a wider envelope where operation is allowed but should be minimized. Typical AOR envelopes might range from 70% of BEP to 120% of BEP.
As you can see on the Barringer curve, significant problems start to occur when operating outside the POR. Issues like higher temperatures, cavitation, recirculation and so on will very quickly take a heavy toll on the pump, seals, bearings and more. Parts start to wear out and repair and maintenance costs become very expensive.
Finding root causes
The problem is that simply replacing these parts or fixing them will only address the symptoms and will never evaluate the root cause that brings these issues about. Why is the pump operating so far away from its BEP? So much is lost when only examining issues on a component-by-component basis. This is where system-level analysis is critical to determining root cause so that these issues can be resolved on a more permanent basis.
How do pumping systems become unreliable and inefficient? Standards for designing pump systems can seem lacking. This tends to cause an over-sizing of pumps, control valves and other pieces of equipment to ensure individual components will work. The engineer adds in a safety factor. Then the reviewer or manager adds on a safety factor, followed by the client, then the pump manufacturer and so on. Now you have an oversized pump with unnecessary safety factors and valves will need to be throttled to meet current demands.
Another cause of a lack of reliability and efficiency is that systems are sometimes designed to meet future requirements, but are operated to meet current market needs. When the pumps are sized for larger flow demands, the operation needs to be modified to meet current demands and this can cause pumps to operate away from their BEP.
System aging and equipment wear also take their toll on reliability and efficiency. Process changes and modifications will have a similar effect that can introduce reliability issues.
Applying a system approach
When applying a system approach of evaluation to pumps and the piping system together, a better understanding is available for complex relationships across all system components. Cause and effect is easier to define. An example would be determining where there are significant pressure drops in the system that affect pump performance. The best part is the ability to consider all parts of the system together to consider all system interactions. This is especially beneficial when evaluating other operating scenarios.
A system approach is greatly streamlined with flow-analysis software. There are many advantages to flow-analysis software to provide better understanding of complex system interactions, including the evaluation of the following:
- Multiple load cases
- Seasonal considerations
- Different operating configurations and requirements
- Waterhammer and cavitation issues
- Choked flow considerations in gas flows
Flow-analysis software also helps with system sizing for pumps, pipes, valves, orifice plates, heat exchangers and so on. Other tasks you can accomplish involve system scale-up evaluation, pressure/flow/temperature distribution, design feasibility analysis, heat transfer, system operation troubleshooting and more. It is also important to quantify pipe system scaling/fouling, pump degradation, code compliance, cost analysis, slurry modeling, pulsation analysis, and more.
What type of information is needed to build a flow analysis model of a pump and piping system? The easy answer is that if it’s in the system, include it in the model.
Let’s start with the fluid properties. To capture the system hydraulics, the fluid density and viscosity are needed as a minimum. Vapor pressure is important to identify if cavitation is happening anywhere in the system when compared to the static pressure that changes throughout the system. To evaluate heat transfer in the system, thermodynamic properties such as heat capacity, thermal conductivity and enthalpy are needed. If you are modeling compressible-flow situations, other parameters are needed like the universal gas constant, compressibility factor, specific heat ratio, entropy and sonic speed. For a waterhammer simulation, you also need the bulk modulus of elasticity of the fluid, which is an important parameter in the calculation of the wave speed. The wave speed dictates how fast a transient pressure wave in a surge event will propagate through the system. Overall, fluid properties are important, and they need to be accurate.
Information needed to model piping includes the inner diameter, length, frictional information such as roughness, Hazen-Williams factor and elevation changes. This is minimal detail needed for hydraulic calculations. More sophistication can be included where the inner diameter can be determined from a type of material (like steel, HDE, ductile, iron and so on), nominal size, and the schedule or type that is coupled with the wall thickness. This helps match a model to reality a bit more and may be easier than entering an inner diameter directly.
Boundary condition information is required so that the system of fluid dynamic equations can be solved for the piping network. In simplest terms, either a known flow rate boundary OR a known pressure boundary is required. Temperature would be needed for heat transfer calculations. In a flow simulation, it is not possible to specify both flow and pressure at a boundary, because this would over-constrain the system and the fluid dynamic equations would have nothing to solve for. Therefore, if you specify a pressure boundary, the flowrate from it will be calculated. If you specify a flowrate boundary, then the pressure at that location will be calculated.
One example of a pressure boundary could be of a large tank. The liquid level and pressure acting on the surface of the liquid is defined, as well as the elevation level of where the pipes are connected. This will allow the pressure to be calculated at the pipe connections, which then gets fed into the system. Doing this can be easier than specifying the pressure directly. Another pressure boundary example would simply be atmospheric pressure, such as if the discharge is flowing into ambient conditions.
Pumps can be modeled in a variety of ways and the data needed depends on the desired information needed. The simplest way is to simulate a pump with a fixed flowrate. The increase in pressure or head that is needed to deliver the specified flow to overcome system resistance and elevation change is calculated. This is very helpful for calculating the operating point needed to size and select a pump. A pump curve provides more information about how the pump will operate. To compare a pump’s net positive suction head required (NPSHR) to the net positive suction head available (NPSHA), then the pump’s NPSHR as a function of flow is needed from the pump manufacturer. To determine the pump operation proximity to the BEP, or calculate the pump’s efficiency, horsepower and so on, an efficiency versus flow, or power versus flow curve is needed from the manufacturer. If a pump is operating with a variable-speed drive (VSD) or variable-frequency drive (VFD), then the speed of the pump can be entered. If a setpoint for flow or discharge pressure applies, then this can be entered as well. Either way, the pump’s curve will then be adjusted via the affinity laws.
Large pieces of equipment such as heat exchangers, filters, and others can be modeled in a variety of ways to account for their pressure drop. The most useful is to model a resistance curve where the pressure drop as a function of flow is entered. This will allow the pressure drop across the device to change based upon the flowrate and the behavior often follows a quadratic relationship.
Valves can be modeled in a variety of ways but the input needed often is as simple as a K factor or Cv value. The Cv versus open-percentage data for a valve can also be entered and this provides better understanding of how far open the valves may be. Also, the Cv versus open-percentage data allows one to model the loss across a valve based upon open percentage rather than directly specifying the Cv value.
Minor losses for fittings such as elbows, area changes, orifice plates, and so on, can easily be accounted for with K factors. There are lots of methods available that calculate K factors for these types of fittings and in most flow simulation software tools, these methods are built in. That way K factors can easily be calculated based upon simple input such as upstream and downstream pipe areas for area change fittings, standard of smooth flanged elbows, long radius elbows and so on.
The more information that is specified, the more accurate the results will be. There are many ways that things can be effectively simplified. However, modeling the system as close to reality as possible is best practice. Even better when test or measured data are available to calibrate a model. A calibrated model that matches data very closely will provide more confidence when it comes to using the model to predict how system changes will impact results and operation.
An example
Figure 3 demonstrates an example of a piping system flow model for a raw brine injection system. There were five vertical pumps in parallel operation and five other horizontal pumps scattered elsewhere throughout the system. The vertical pumps in parallel competed with each other hydraulically and each pump provided significantly different flow than the others. Ideally, the flow distribution should be similar to help all pumps operate close to BEP rather than some pumps operating close to BEP and some operating further away. Within a five-year period, there were a total of 41 repairs, costing near $1.23 million. The MTBF was roughly 15 months.
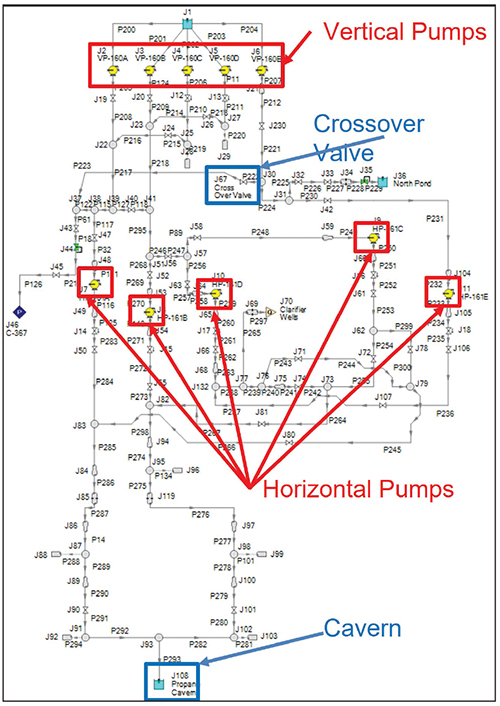
Figure 3. Shown here is a piping system flow-analysis model of a raw brine injection system with five vertical pumps in parallel and five horizontal pumps located elsewhere throughout the system
The consultants on this project were tasked to improve reliability of the system to mitigate the constant repair issues. After the model was built and calibrated, many scenarios were reviewed. The major problem is that the normal operation of the vertical pumps in parallel were operating between 23 and 58% of BEP. Each pump delivered much less flow than its designed capacity. Several scenarios were run that included various system changes such as only operating two of the vertical pumps in parallel instead of three in parallel or more. Other mitigation attempts included closing off a crossover valve as well as increasing the discharge pressure of the cavern.
After all the test scenarios were evaluated, the consultants determined that the combination of only operating two of the vertical pumps in parallel at a time, as well as closing the crossover valve and increasing the cavern pressure, had a dramatic improvement in each pumps’ operating proximity to BEP. After these changes, the pumps would then operate at about 75% of their BEP, the flow demands were easily met with only two out of the five vertical pumps and this resolved the many operational problems the facility had.
Final remarks
In conclusion, a system-wide approach for design and analysis of new and existing piping systems can help engineers and owner and operators better understand system interactions and what steps can be made to improve reliability. This is much more useful than a component-by-component approach of constantly repairing parts that wear out or break. Flow-analysis software greatly aids in treating the root cause of the problem rather than the symptom. The flow analysis sheds more light on why pumps, control valves and other pieces of equipment are operating poorly and have problems. The impact of this approach is massive with improved reliability, minimized maintenance and repair costs, downtime, production losses, and increased profits.
Edited by Gerald Ondrey
References
1. “Optimizing Pumping Systems: A Guide For Improved Energy Efficiency, Reliability, & Profitability”, First Edition, Hydraulic Institute & Pump Systems Matter, 2008.
2. Jantunen, E. and Itaranta, H. Expert System for the Diagnosis of the Condition and Pumping Efficiency of Centrifugal Pumps, Proceedings of the 53rd meeting of the Society for Machinery Failure Prevention Technology, April 19–22, Virginia, 1999.
Author
Ben Keiser is a technical sales consultant for Applied Flow Technology (AFT; 2955 Professional Place, Suite 301 Colorado Springs, CO 80904; Phone: 719-686-1000; Email: [email protected]; Website: www.aft.com), a leading dynamic fluid flow analysis and waterhammer mitigation software company. Keiser helps engineers understand how to design safe and efficient piping and ducting systems. His passion and expertise can be accessed around the world as he trains engineering teams how to efficiently preform flow analysis simulations to find optimized solutions. Prior to joining AFT, he worked for Eaton Corp. and WellbornYX Corp. Keiser holds a B.S.Ch.E. degree from the Colorado School of Mines.