In their own words, sustainability leaders from the chemical process industries provide insight about their practical success and ongoing goals in improving environmental performance
Considerations about environmental sustainability are permeating all levels of the global economy, as companies realize that change is necessary for the resilience of their businesses, as well as society as a whole. Indeed, the activities of the chemical process industries (CPI) have traditionally involved the consumption of non-renewable resources and in many cases, the generation of large amounts of atmospheric emissions, but the materials produced by the CPI are also essential to countless products across global supply chains. This article outlines some of the practical progress and ongoing work of the CPI toward advancing sustainable manufacturing practices.
“If we accept that the human impact on the environment and climate has to be addressed, then every aspect of life will have to change in some way,” says Ron Gerrard, corporate sustainability officer at Huntsman Corp. (The Woodlands, Tex.; www.huntsman.com). “The science of chemistry and the chemical industry itself are major sources of potential solutions to address many of these needs. But we are not complacent, and we recognize we will also need to change and adapt our feedstocks, energy sources, technologies and supply-chain solutions in the decades ahead,” he emphasizes.
The adoption of sustainable practices is not simply a compulsory action dictated by government regulations — the transition to more sustainable manufacturing models is complex, and also opens the door for paradigm-shifting innovation in the CPI and beyond. “We need to work across the value chain in collaboration with other industries and governments, if the right policies, funding, infrastructure and innovation are to be delivered,” continues Gerrard. At this stage, he points out that sustainability momentum is continuing to build, but that in many cases, the steps being taken in the CPI are self-initiated and somewhat independent. However, as the sustainability interests of consumers, manufacturers and regulatory bodies coalesce, the transition will rapidly accelerate. “Growing consumer and media attention, coupled with new regulatory drivers, are prompting companies to take a closer look at how the drive for a more circular economy may impact their strategy. With the right support, collaboration, incentives and adjustment to consumer demands and expectations, the industry will be capable of much more to support global sustainability and the development of a real circular economy in the years ahead,” adds Gerrard.
Defining the circular economy
With a unique position in the global supply chains of countless products, the CPI are poised to be a critical part of the ongoing push toward more circular, sustainable products and processes. “The chemical industry and its innovations will be crucial to drive change, since chemistry plays a key role in many value chains of the mobility, packaging, construction and agricultural industries. By developing circular approaches with different industries, the chemical sector can contribute more to circularity,” says Mitchell Toomey, director of sustainability, BASF Corp. (Florham Park, N.J.; www.basf.com). Toomey describes the circular economy as “moving away from the linear model of ‘take-make-dispose’ to a system of closed loops powered by renewable energy.”
To realize this model, companies must take action at all levels. From ambitious measures to decrease atmospheric emissions and reduce resource consumption to designing new products and processes with circularity and renewable energy in mind, CPI companies are actively working toward improving their environmental footprint (Figure 1). “Circular economy solutions require more durable and more resource-efficient products, as well as new business models to support an increase in reuse, repair and recycling,” says Toomey.
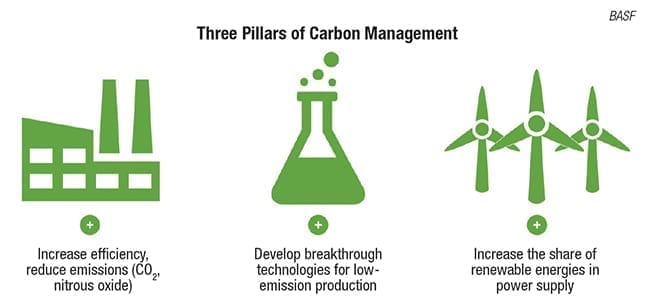
FIGURE 1. Major drivers for sustainable innovations include reducing CO2 emissions, waste production and the consumption of energy and water
“We believe that our future license to operate and by extension, commercial success, depends on ensuring that all parts of our portfolio are driven by the transition from a linear to a circular economy,” says Tony Kingsbury, director of sustainability EMEA, Dow (Midland, Mich.; www.dow.com). In the case of plastic, its low cost and ease of use have become environmental liabilities in many applications, says Kingsbury: “Plastic’s everyday presence in our lives means we often take it for granted, resulting in it being too easy to use and then needlessly thrown away.” According to Kingsbury, realizing plastic circularity means collaboration with industry partners and customers in evaluating infrastructure to better enable collecting and sorting, as well as finding opportunities to stimulate new markets for recovered materials. Open discussion and transparency are also essential elements in advancing circularity. “We need to recognize that reducing our environmental impact in a meaningful way requires careful consideration. Issues like mass balance and carbon emissions need to be debated in an open and transparent manner. We must look at proper lifecycle analyses for different types of materials,” adds Kingsbury.
Nella Baerents, global sustainability director at Kraton Corp. (Houston; www.kraton.com) also lists collaboration and transparency as two key pillars of any company’s environmental strategy. “We collaborate with customers to develop lifecycle assessments to offer data about a product’s overall sustainability footprint,” she explains. The company aims to complete 12 such lifecycle assessments in 2020. The transparency enabled through comprehensive sustainability reporting and data management regarding product sustainability also promotes opportunities for renewable and recyclable products to substitute existing materials, she adds.
Making success measurable
To preserve environmental sustainability, the concept of sustainability itself must transition beyond an abstract concept into tangible best practices and goals. “In the past, this industry didn’t really know what we were talking about when we were talking about sustainability, because it was not measurable,” explains Stefan Haver, head of corporate responsibility at Evonik Industries AG (Essen, Germany; www.evonik.com). “About five years ago, Evonik integrated a facts-based approach to sustainability into our strategy process,” adds Haver. Examining customer needs, regulatory requirements, exposure hazards and more, Evonik has targeted areas of its portfolio where sustainable solutions make sense for product development, including the development of mineral-based, recyclable, non-flammable insulation materials and customized hollow-fiber membranes designed for biogas separation (Figure 2). For product areas that are deemed sustainability-challenged, Evonik aims to find substitutes or alternative ways of production. “Our customers want us to help them improve their sustainability record. There is a strong market need, and this is why we must make our impacts measurable,” he emphasizes. Social movements related to climate change are also putting pressure on manufacturers. “For many years, people perceived the chemicals industry as part of the environmental problem, but today, there is at least some understanding that the chemicals industry is also a part of the solution.”
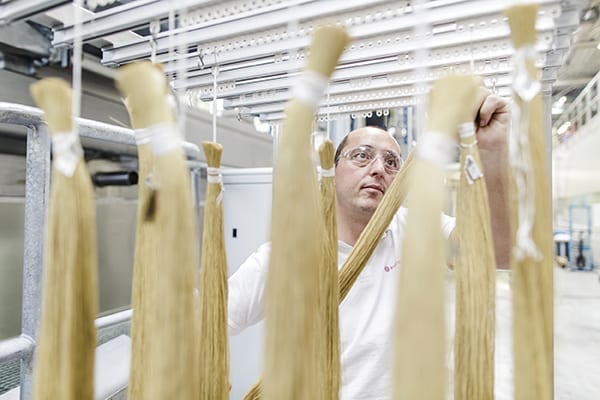
FIGURE 2. Products aimed at advancing renewable energy sources, such as biogas, are major innovation areas in the CPI. Evonik
“Ecological, economic and social targets must be brought together to achieve clearly traceable, measurable and reproducible results. Sustainability remains an indispensable prerequisite of creating value and growth,” says Martin Vollmer, chief technology officer at Clariant AG (Muttenz, Switzerland; www.clariant.com). However, overarching sustainability goals cannot be achieved by one company alone — cooperation along the value chain is crucial for advancing circular technologies and business models, and also meeting consumer demands. “Consumers have become better informed over recent years and are increasingly demanding sustainable products and ingredients. Most players along the value chain today understand that climate protection has become indispensable for a sustainable future,” says Richard Haldimann, Clariant’s head of innovation excellence, citing energy and water consumption, CO2 emissions and waste as major drivers for sustainability advancement.
With the intensified global focus on product lifecycles, sustainability considerations come into play even in the early-development phase of a product’s life. At 3M (St. Paul, Minn.; www.3m.com), every new product that enters the company’s commercialization process is evaluated to demonstrate its sustainability value, in terms of recyclability, energy and water savings, responsible sourcing, renewable materials and more. “By reducing the amount of raw materials and total energy required to make a product, we are improving our operational footprint while improving our portfolio,” says Gayle Schueller, vice president and chief sustainability officer at 3M. “We aim to make our customers become more sustainable, including a goal to help them reduce their greenhouse gas (GHG) emissions by 250 million tons of CO2 equivalent emissions through the use of our products,” adds Schueller.
Underlining the importance of environmental considerations to business objectives, Lanxess AG (Cologne, Germany; www.lanxess.com) directly connected its finances to sustainability performance when it signed a new revolving credit line that links interest rate terms to the fulfillment of ESG (environment, social and governance) criteria. Some of the company’s sustainability goals have included optimization of its portfolio toward products that are less emissions-intensive over their entire lifecycle. “A complete lifecycle approach is a key component of achieving a successful transition to a sustainable, low-carbon and circular economy. The end of a product’s life can go through several cycles — the mechanical and chemical recycling of waste, as well as energy recovery,” says Hubert Fink, member of the board of management at Lanxess. “To this end, we are constantly developing sustainable material solutions and also relying on the new possibilities of digitalization.”
Feedstock efficiency
Shifts in feedstock sourcing are a core part of gaining ground in a circular economy. However, achieving circularity is a more nuanced endeavor than simply swapping a traditional feedstock for a renewable one. “If you only switch to renewable materials without resolving a product’s recyclability, you will end up disappointing consumers, because you will never be able to make everything fully circular due to the huge losses in the recycling process,” says Tom van Aken, chief executive officer of Avantium N.V. (Amsterdam, the Netherlands; www.avantium.com). Converging these two trends will require not only bio-based “drop-in” replacement chemicals that are identical to their petroleum-based counterparts, but also the development of brand-new materials and process technologies. “With the trend toward renewable feedstocks, different types of monomers will be coming onto the market,” adds Van Aken.
Avantium has developed several new technology platforms based around sugar feedstocks, bringing together drop-in replacements for commodity chemicals and novel molecules to yield new resins. The company is currently working on a 5,000-ton/yr demonstration facility for its catalytic process to produce furandicarboxylic acid (FDCA) from plant-based sugars. Avantium intends to combine the FDCA monomer with renewable monoethylene glycol (MEG), for which the company opened a demonstration plant last year (Figure 3), to yield the polyester resin polyethylene furanoate (PEF). “PEF can be made completely from plant-based materials, but is also fully recyclable,” says Van Aken. “We can start moving toward renewable feedstocks and stop relying on fossil feedstocks, and in parallel switch to circular products,” he continues. He observes that consumers are currently the strongest driving force, more so than industries or governments, to promote circular economy goals. “I think the quickest transition will be driven by consumers. Consumer demand will steer the supply chain in a more renewable, circular direction, and that will accelerate the transition.”
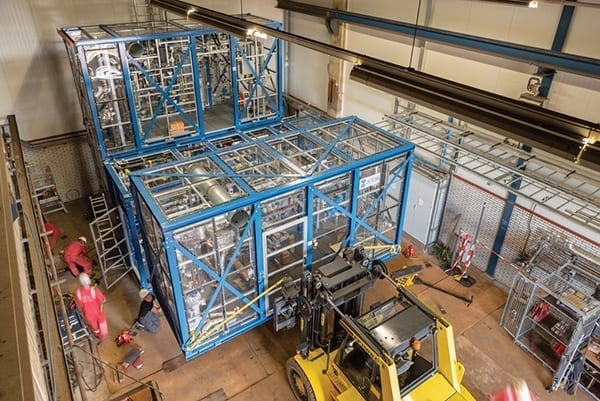
FIGURE 3. The search for renewable feedstock has led to the development of brand-new chemical technologies, and brought innovation to the molecular level. Avantium
Last year, Avantium and beverage manufacturer Carlsberg debuted a beer bottle made of PEF and paper (Figure 4), and additional PEF packaging applications are expected to launch soon. “We have high expectations for how consumers and brands will respond to a sustainable circular product like the paper bottle,” adds Van Aken. Avantium is also beginning to look at manufacturing chemicals using CO2 as a feedstock, and also integrating electrolysis processes alongside catalytic platforms. “We are realistic that this will take years to optimize and scale. I absolutely believe that in the coming ten to fifteen years, these are the types of technologies we will see coming onto the market. People will be building electrolyzers and using CO2 as feedstock,” he explains.
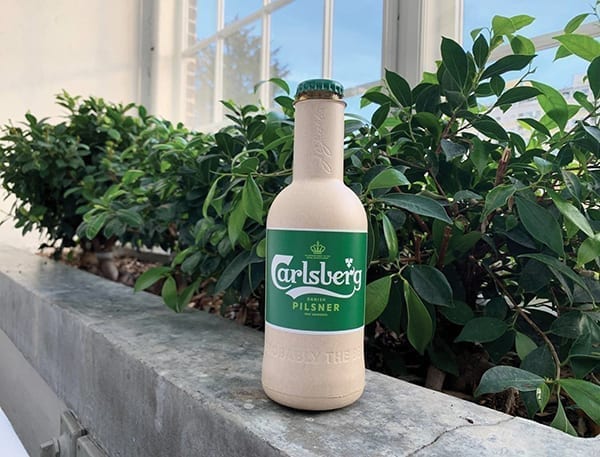
FIGURE 4. Increasingly, a “design for recylcability” mindset is driven by consumer interest, such as with Avantium’s PEF-based beer bottle. Avantium
In this same vein, Evonik has worked with Siemens AG (Munich, Germany; www.siemens.com) on the Rheticus project, which is piloting the manufacture of hexanol and butanol from CO2. “For this kind of circularity, you can no longer find solutions in isolation, but rather in close relationships with other businesses with different competencies. We will also see a deeper integration of the chemicals industry into the business of our customers,” says Evonik’s Stefan Haver.
Like CO2, finding use for other waste streams is also instrumental in the circular economy. For instance, Clariant’s sunliquid process utilizes agricultural residues, such as wheat or corn straw, to produce bio-based products, including biofuels. “Further long-term sustainability goals include the use of CO2 as a raw material, and we are also developing catalysts for Power-to-X technologies, such as producing methanol from CO2,” adds Clariant’s Martin Vollmer.
Manufacturers of products like catalysts and batteries, which use expensive and scarce raw materials, are faced with some unique circular economy challenges. The supply chains for these materials are complex and, in some cases, can potentially be entangled in international conflicts and unsavory practices — particularly the elements that are used in battery cathode materials.
“The use of precious metals, such as platinum and palladium, cannot be avoided for certain classes of products, but we have considerable expertise in designing and developing products that minimize the amounts of precious metals needed while still delivering expected performance,” says Philip Blakeman, sustainability director at Johnson Matthey (JM; London; www.matthey.com). “We are also experienced in recycling these metals once products have reached the end of their useful life.”
For these types of materials, sustainability challenges stretch across all parts of the supply chain, and widespread collaboration and transparency are becoming increasingly critical. “Focus on ensuring the whole supply chain is operating ethically toward people and the wider environment will continue. Upstream companies are increasingly looking for ways to source responsibly,” explains Blakeman. Furthermore, he emphasizes that manufacturing companies who take an active role in reducing GHG emissions will see better opportunities in the market, as downstream customers also try to minimize their own environmental impacts. “Investors, employees, governments and customers increasingly expect companies to execute meaningful activities to improve their environmental impacts throughout the whole supply chain and product lifecycle,” he adds. “Being able to source renewable energy and implement effective carbon-capture technologies are vital for the industry to successfully meet expectations.”
Globally, JM has reduced its carbon intensity per ton of product produced by 20% since 2017 and is active in developing renewable products for emerging areas, including the hydrogen economy and electric vehicles. The company has developed fuel-cell components that convert hydrogen gas into zero-emissions electricity (Figure 5), and is in the process of commercializing its eLNO ultra-high-energy-density battery cathode material, which enables lower cobalt content for electric vehicle manufacturers.
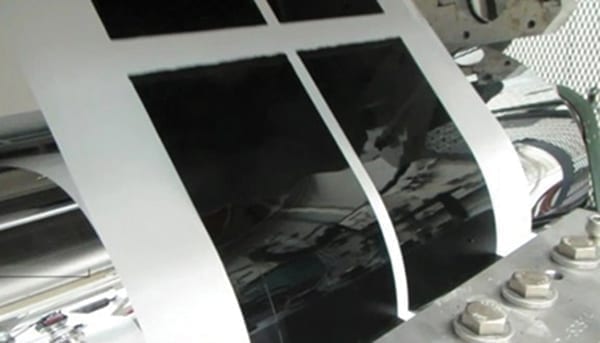
FIGURE 5. Advanced fuel-cell components are enabling the production of zero-emission electricity from hydrogen. Johnson Matthey
Operational and energy gains
Companies can introduce sustainability measures into manufacturing operations not only through the use of renewable materials as feedstock, but also through various tactics to improve operational efficiency. “We work to increase resource efficiency by decreasing our plants’ energy use, switching to cleaner-burning fuels, improving spill and leak prevention, enhancing wastewater treatment and increasing production consistency,” says Kraton’s Baerents. As an example, she highlights the company’s manufacturing plant in Sandarne, Sweden, which has developed a mixture of purified pitch oil to power the facility’s heaters. This oil is obtained as a byproduct from the site’s distillation unit for bio-based crude tail oil. “This sustainable fuel powers normal operations, and fossil fuels are only used to start up and shut down the process,” explains Baerents. “This improvement reduced the use of fossil fuels and increased our resource efficiency by allowing the steam boilers and heaters to run with our operations’ byproducts,” she adds. Globally, the company is targeting a 25% reduction in GHG emissions intensity by 2030.
As a cornerstone of corporate sustainability plans, many chemical companies are seeking out renewable energy sources to power their operations. “For instance, we now utilize landfill-gas boiler fuel as a replacement for natural gas,” says Cassidy Carlile, director of environment and sustainability for the chemical division of Milliken & Company (Spartanburg, S.C.; www.milliken.com). The company has also installed solar panels at its corporate headquarters as a measure to reduce environmental footprint. “Additionally, Milliken is currently installing a combined heat and power system to supply power and steam to two of our largest plants. This project will further reduce our GHG emissions,” adds Carlile.
Alongside renewable energy, Carlile also sees an increased focus on product lifecycle considerations and waste reduction, pointing out that over 90% of Milliken’s manufacturing locations operate with zero waste sent to landfills. Along with a tenfold increase in renewable energy use, among the company’s sustainability goals are plans for a 25% reduction in GHG emissions, water usage and solid waste by 2025.
3M has improved upon its own GHG emissions through the use of renewable electricity — the company has installed multiple solar arrays to power its manufacturing sites in Corona, Calif. (Figure 6) and Tuas, Singapore. In Singapore, 3M has created one of the country’s largest solar farms. Moving forward, 3M has set its sights on 100% renewable electricity usage by its global operations by 2050, with an interim goal of 50% by 2025.
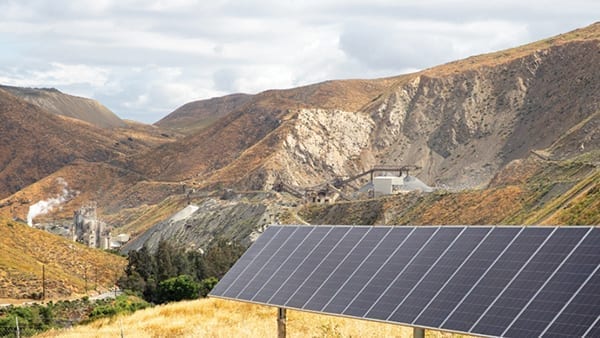
FIGURE 6. The share of renewable energy powering CPI manufacturing plants is set to skyrocket in the coming years, as companies begin to execute their longterm sustainability goals. 3M
To halve its GHG emissions between 2004 and 2018, Lanxess focused not only on reducing CO2 emissions, but also on nitrous oxide (N2O) by constructing a N2O-reduction plant at the Chempark in Krefeld-Uerdingen, Germany. According to the company, this plant reduces emissions of CO2 equivalents by about 1.5 million metric tons per year (m.t./yr). Furthermore, as part of its over-arching approach to become climate-neutral by 2040, the company is building another N2O-reduction plant in Antwerp, Belgium, which will start up in 2020 and will reduce CO2 equivalents emissions by some 150,000 m.t./yr.
Also in Antwerp, Lanxess is part of a shared steam network, which started up in 2019. “The steam network in Antwerp is used in conjunction with other chemicals companies. The system helps reduce energy costs, and is expected to reduce CO2 emissions by about 10,000 m.t./yr for Lanxess. Reductions will likely be 100,000 m.t./yr across all participating companies,” says Hubert Fink, member of the board of management of Lanxess. At its site in Porto Feliz, Brazil, Lanxess operates a biomass-powered cogeneration plant for the production of electricity and steam. “Thanks to the use of biomass raw materials, energy can be produced on a CO2 -neutral basis,” emphasizes Fink. The company is also in the process of switching to renewable energy sources at its sites in India. “In India, we are massively expanding the supply of biomass and solar power, and will no longer use coal or gas,” adds Fink. With these projects and other measures, Lanxess plans to decrease its CO2 emissions by a total of 800,000 m.t. by 2025, investing up to €100 million in the process.
On the operational side, Braskem America (Philadelphia, Pa.; www.braskem.com/usa) has installed automated monitoring systems for cooling-tower treatment chemicals, reducing the amount of blowdown to the sewer systems — this change has saved over 83 million gal/yr of water since 2013, says Geoffrey Inch, circular economy and sustainability director, Braskem North America. Another notable project that is currently underway at Braskem’s Marcus Hook, Pa. location addresses hydrocarbon losses to flare from vent-recovery compressors. “After analyzing the losses, it was determined that through the modifications implemented in this project, there is potential to reduce up to 10 million pounds of hydrocarbon losses to flare each year,” explains Inch. This project is expected to be completed in mid-2020. Other sustainability-focused projects underway at Braskem seek to reduce monomer losses, control water usage, minimize additive consumption and find renewable pathways for new products. Braskem currently offers bio-based versions of polyethylene and ethylene vinyl acetate, and the company is working on a demonstration plant with Haldor Topsoe A/S (Lyngby, Denmark; www.topsoe.com) to manufacture renewable MEG.
A keen focus on waste reduction has been the driving force behind several larger-scale projects at Huntsman. “At our methylene diphenyl diisocyanate (MDI) production facility in Shanghai, China, we built a new plant to chemically recycle a high-volume byproduct — anhydrous hydrogen chloride — to produce chlorine, which is re-used as a raw material for new MDI production,” explains Huntsman’s Gerrard. Also, at the company’s site in Conroe, Tex., an evaluation of equipment washdown procedures revealed an opportunity to isolate the hazardous cyclohexane within a process waste stream and recover this material for commercial sale. “After this change, the Conroe plant went from producing 3.7 million pounds of hazardous waste to zero,” adds Gerrard.
Practical progress
The steps being taken to improve sustainability performance in the CPI range from small housekeeping tasks to large-scale capital projects to the development of brand-new chemical technologies. For Huntsman, some of the smaller-scale initiatives have included recovering and re-using pallets, treating and re-using intermediate bulk containers (IBCs) in shipping and converting from diesel-powered to electric forklifts. At Huntsman’s Deggendorf, Germany site, production storage tanks were equipped with new insulated housing, which considerably reduced natural gas consumption. In addition, the company has begun rainwater-recovery activities to improve water usage at sites in India, Indonesia and Italy.
Corporate sustainability measures are certainly not limited to operational improvements. At Braskem, updating lighting systems to LED equipment and offering recycling receptacles have served to reduce the company’s environmental footprint. Drilling even deeper into sustainable practices at all levels of the enterprise, Braskem began monitoring its GHG emissions per Scope 3 of the Greenhouse Gas Protocol’s (www.ghgprotocol.org) Corporate Value Chain Standard. “Areas measured in Scope 3 include business travel, downstream and upstream transportation and distribution, use of sold products, team member commutes and so on. Many organizations don’t yet monitor Scope 3 items,” notes Inch. Overall, Braskem has set a goal to reduce its carbon footprint to 0.6 kg/ton of product produced.
One particular focus area for PPG (Pittsburgh, Pa.; www.ppg.com) is reducing spills and releases. “One of our key sustainability milestones in 2018 was a 28% improvement in spill and release rate, with our overall goal being to achieve at least a 65% improvement by 2025,” explains Tim Knavish, PPG executive vice president. Intensively tackling spills and releases not only improves resource efficiency, but also reduces costs and hazards associated with waste disposal and environmental cleanup. “We work first toward absolute material utilization throughout our manufacturing processes followed by eliminating, minimizing, reusing and recycling the waste we do produce,” says Knavish. To meet waste-reduction goals, PPG has initiated spill-prevention procedures that require operators to walk along production lines prior to liquid transfer, visually checking for any potential spill risks, such as open drain valves or pumps feeding into already full tanks. Although much of PPG’s water consumption is for equipment cleaning rather than for production, Knavish notes that the company still takes advantage of opportunities to optimize water use in all facilities. “We are improving our processes to require less cleaning and are working toward a 20% reduction in water intensity by 2025,” he adds. At PPG’s manufacturing facility in Huntsville, Ala., a project that switched an emissions-filtering unit from an open-loop to a closed-loop design has reduced water use by 4.6 million gal/yr.
The plastics problem
An undeniable area of concern for chemical manufacturers is mitigating waste — particularly, the accumulation of plastic waste. One way that manufacturers are improving their environmental footprint is through efforts to reduce waste from their own operations, including plastic pellets and powders, which have many detrimental effects when released. The Operation Clean Sweep (OCS; www.opcleansweep.org) program provides guidelines to help companies prevent plastic pellets, flakes and powders from entering marine ecosystems. “Since our founding, we have been a member of OCS, with established practices in our plants to make sure that pellets are fully contained and do not leave the site,” says Jim Becker, vice president of polymers and sustainability at Chevron Philips Chemical Co. (CP Chem; The Woodlands, Tex.; www.cpchem.com). Obviously, handling plastic waste also goes beyond a plant’s boundaries, and global recycling efforts must be bolstered to handle the accumulation of post-consumer plastics. “In many countries, the infrastructure for waste collection and management is missing. One of the things we’re going to see over the next five years is a great deal of investment and work on developing that infrastructure,” says Becker. He believes that chemical recycling — treating plastics to break them back into their constituent molecules — will be a key part of tackling plastics waste worldwide: “Chemical recycling is a very circular solution. It turns plastic waste into a feedstock for virgin resins,” he adds.
He mentions a project in India where the Alliance to End Plastic Waste is working to set up small chemical-recycling units along tributaries of the Ganges River with the vision that people will deposit their plastic waste to the units, which will in turn generate fuel. “This creates an economic incentive for people to recycle their waste rather than leave it unmanaged,” emphasizes Becker.
CP Chem is in the early phases of development on a variety of chemical-recycling projects, including its combination with existing mechanical recycling techniques to greatly expand the breadth of materials that can be efficiently handled. “The combination of chemical and mechanical recycling is going to be a bigger part of the picture over the next 3–5 years. It is difficult to mechanically recycle everything, and there can be barriers to convert mechanically recycled resins back into useful products,” says Becker. For instance, mechanical recycling usually requires finely separated waste streams, whereas chemical recycling processes are suited to handle mixed streams. Also, chemical recycling opens the door for recycling multilayer packaging, and other traditionally challenging materials like polystyrene.
CP Chem’s American Styrenics joint venture with Trinseo produces circular polystyrene through a chemical recycling process, but Becker notes that there is still much work to be done to scale chemical recycling to handle massive amounts of unmanaged plastic waste. “We have to get the whole supply chain working properly. There will be many innovations in order to make chemical recycling viable and the industry is working on efficiencies, catalyst technologies and other improvements,” he continues.
Clariant is also working with partners in the field of chemical recycling to secure future access to reclaimed raw materials, such as ethylene and propylene, and working toward tackling some of the challenges associated with the utilization of post-consumer and post-industrial recycled (PCR/PIR) materials. “Among our longer-term sustainability projects, we are investigating the chemical recycling or upcycling of plastic waste from either clean-grade or mixed material streams for reuse in new virgin-quality plastics for fuels. A special focus within this work is on fundamental absorption mechanisms for removing harmful impurities,” says Clariant’s Haldimann.
Eastman Chemical Co. (Kingsport, Tenn.; www.eastman.com) has launched two chemical recycling technologies — one focused on polyester and the other tackling mixed plastics streams. The company’s Polyester Renewal Technology (PRT) reclaims waste polyesters from landfill and recycles them via glycolysis or methanolysis, reducing the polyesters to monomers, which are then fed back into the polyester manufacturing process. Eastman expects to begin operation of a commercial PRT unit in the next 2–3 years.
To implement the mixed-plastics-recycling process, which began commercial operation in 2019, Eastman modified the front end of a cellulosics production unit to handle mixed-plastic feedstock. The process partially oxidizes the plastic and efficiently converts it into basic building blocks for other chemicals. In 2020, the company anticipates processing up to 50 million pounds of waste-plastic feedstock. “Our advanced circular recycling technologies give us an opportunity to develop partnerships across the value chain to provide solutions, including better end-of-life options that will have an impact on the global waste problem. It’s extremely important that we succeed here, as we can help pave the way for the entire industry to make a material difference for a global issue,” emphasizes Steve Crawford, chief technology and sustainability officer at Eastman. “We see chemical recycling as a vital complement to mechanical recycling. Chemical recycling can now properly deal with the more complex plastics that mechanical recycling was not designed to process. We are focused on the vast amount of materials that are not suitable for basic recycling,” adds Crawford.
Other efforts to curb plastic waste include designing end products themselves to be intrinsically more recyclable. According to Becker, CP Chem is working with its customers to re-design packaging structures with recyclability in mind, and also to incorporate more post-consumer recycled materials. “There’s a lot of work going on in packaging design, because the industry as a whole needs to have packaging that is more easily recycled. We’re going to see more of that in the coming years. We are certainly seeing consumer preference drive sustainable product development, but this is also reflected from a regulatory standpoint,” Becker concludes.
One part of Clariant’s plastics strategy has taken the form of dedicated additives that are intended to improve the compatibility of plastics in current and future recycling processes. “The development of customer-tailored additives will enable brand owners to significantly increase the share of recycled material in the packaging of their products,” explains Haldimann. “We must put an end to the throw-away mentality, and a stronger circular economy with recycled plastics will help accomplish this change. We see an enormous innovation potential in appropriate end-of-life product strategies,” he adds.
Milliken has also developed performance-modifying chemicals that allow for recycled polypropylene to be better utilized in end products without sacrificing physical properties. “We are analyzing new products using lifecycle analysis principles. Our sustainability efforts include convening scientists and thought leaders to take action on solving plastics’ end-of-life challenges,” says Cassidy Carlile of Milliken. Looking ahead, this type of collaboration — between industry, academia and regulatory bodies — will surely be an instrumental element to accelerate circularity in the CPI.