In order to accommodate higher production volumes of acrylic acid and the associated superabsorbent polymers (SAPs), LG Chem plans to build additional acrylic acid purification units to increase the capacity of its complex in Yeosu, South Korea, to 160,000 tons of high-purity acrylic acid annually.
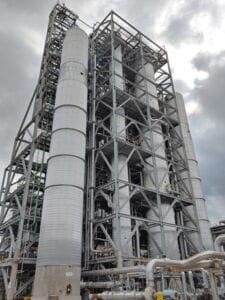
LG Chem is installing crystallization technologies from Sulzer for its acrylic acid expansion project (Source: Sulzer)
To realize the planned production increase, LG Chem contacted Sulzer Ltd. (Winterthur, Switzerland) to deliver the required acrylic-acid crystallization equipment. Having already completed similar upgrade projects with Sulzer, LG Chem asked the company to design a new glacial acrylic acid purification solution.
The processes are based on fractional crystallization. These can remove impurities at low process temperatures while avoiding the use of solvents and eliminating the risk of acrylic acid polymerization that can occur during distillation. To obtain high-purity glacial acrylic acid in the fastest and most efficient way, Sulzer’s design consists of two falling-film crystallizers, which remove the impurities to reach the specifications, and a static crystallizer as a stripping fractionator to increase the yield.
LG Chem needed the new unit to be operational quickly, as this would help the company support the increased demand for acrylic acid from its customers. The use of an existing Sulzer design helped to streamline the project, as no basic engineering study was required. However, a few modifications to the system were needed. As a mirror image of LG Chem’s existing purification unit, the position of the inlet and outlet nozzles needed to be rotated.
Sulzer was able to reduce its lead time and deliver the equipment onsite in less than 14 months. To do so, the company relied on its global network of specialized facilities.
As part of the installation, Sulzer’s teams integrated the purification unit into the existing plant. This was crucial to ensure that the different parts would work well together without causing bottlenecks. In particular, one falling-film crystallizer needed to be coupled, at its bottom, with a component provided by LG Chem. After the assembly of the purification equipment and initial inspection were completed, Sulzer’s specialized teams supported the commissioning and start-up activities.