Coupled with advanced analytics and networking capabilities, today’s smart sensors help processors optimize the facility
Picture a piece of equipment not just monitoring its own health, but also automatically ordering the part it requires and, when it notes that the part has been received, sending an alert to the maintenance technician to come fix it, while also providing detailed visual instructions on how to perform the repair virtually via a handheld device. Or, imagine management in a petroleum refinery using realtime data and information to determine, on the fly, whether they can take advantage of bargain-priced opportunity crude or low-cost natural gas to positively impact the profitability of the plant. Both these scenarios — and many others like them — portray the ultimate vision of Industry 4.0, and are the anticipated result of integration between machines and humans. Workers will be armed with realtime data that has been analyzed and contextualized to provide actionable information which can be used to positively impact the profitability of the process, facility or entire enterprise. And, at the heart of it all are smart sensors, which are evolving, alongside other technologies, such as data analytics and connectivity, to provide meaningful data to those who can use it to make well-informed business decisions.
The future of Industry 4.0
Whether you call it Industry 4.0, big data or the industrial internet of things (IIoT), the future undoubtedly includes the integration of ground-level data that can be shared with appropriate parties, from maintenance technicians all the way up to top-level management, and used to make decisions that impact the overall performance of the business, says Marcus Trygstad, consultant, Advanced Analytical Technology, with Yokogawa Corp. of America (Sugar Land, Tex.; www.yokogawa.com). “The key to Industry 4.0 is not just getting data, but taking this abundance of data and converting it into useful, understandable information that we can use to control the process and the business properly,” says Trygstad. “We’ve had the ability to collect data for a long time, but what is changing is the quantity of data and the ability to transform it into actionable information at the same time as we are becoming more sophisticated in the use of machine learning, artificial intelligence and digitization. Once we begin to really integrate and harness all the information and technologies, the future of Industry 4.0 will include the integration of data and informed decision making from top to bottom in an organization” (Figure 1).
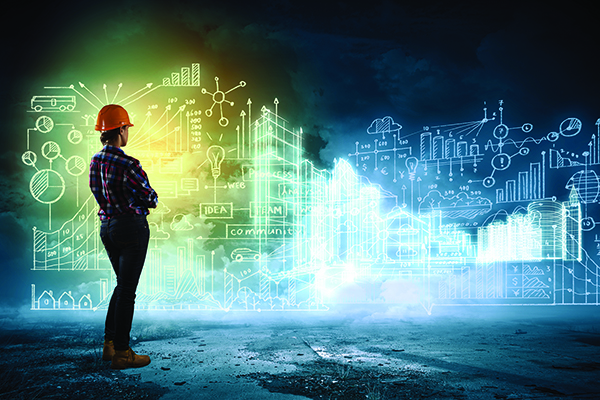
Figure 1. “The key to Industry 4.0 is not just getting data, but taking this abundance of data and converting it into useful, understandable information that can be used to control the process and the business,” says Yokogawa’s Trygstad
Gordon Bordelon, chemical industry lead, with Rockwell Automation (Milwaukee, Wis.; www.rockwellautomation.com) adds that this type of visibility will also allow chemical processors to become more responsive, which will be necessary to keep up with the competition in the future. “There is a massive amount of pressure on chemical processors to become more flexible and agile. They will need to make chemicals that are construed as more environmentally friendly or begin sourcing more materials that are environmentally friendly in an effort to say they produce sustainable-based chemicals. Digitization helps create more flexible operations, allowing processors to produce different products on existing equipment and modify raw materials to meet sustainability goals, market demand and cost pressures.”
Industry 4.0 is also being looked at as a means to gather more data out of the plant to assist with regulatory compliance. Bordelon continues, “Having smart sensors, analytics and digital data sharing via Industry 4.0 will allow management, in real time, to understand how they are performing from a sustainability and regulatory standpoint and get answers to questions like, ‘What’s my carbon footprint? What can we do to run more efficiently using fewer or different resources and have lower emissions with fewer releases?’”
Eric Heilveil, marketing manager for Process Instrumentation with Siemens (Harleysville, Pa.; www.siemens.com) summarizes these ideas. “The vision for Industry 4.0 includes a fully integrated organization from management down to engineering to operators and maintenance staff,” he says. “The large data pond that they all swim in will be a single data hub or point of contact for the entire operation, from human resources to engineering to manufacturing and distribution, to ensure a very concise and consistent workflow that allows teams to work together at the same time to reach common goals rather than having each department work in isolation or in sequence.”
The benefits of this are many. “This type of integration reduces the possibility of error created when just a single set of eyes is looking at it and provides a check and balance for perfection,” explains Heilveil. “Time to market can also be reduced by the integrated workflow and it will provide a superior means to reducing quality issues and increasing accuracy while producing goods and distributing them using less energy while optimizing the use of human and raw material resources.”
The current situation
While intense and enterprise-wide integration is several years down the road for most processors, many are already beginning to embrace the technology on a smaller scale and reaping benefits. For instance, this type of information sharing is already assisting processors coping with a retiring workforce, while initiating a new breed of millennial employees, says Asheesh Arora, vice president of the Field Instrument Business within Honeywell Process Solutions (Houston; www.honeywellprocess.com). “Industry 4.0 technologies allow us to capture information from the aging workforce while fulfilling the needs of the new millennials who would like to have data at their fingertips,” he says. “Younger engineers want to spend time using available data rather than questioning what the data means. On the other side, we can capture the knowledge of the seasoned engineer, digitize and model it to provide knowledge to the new workforce before those industry veterans walk out the door.”
Increased safety is another huge win currently available thanks to early Industry 4.0 capabilities. “Safety is a critical benefit of embracing 4.0 technology,” says Artur Rdzanek, global product manager for Sensored Products with ABB Motors and Mechanical (Greenville, S.C.; www.abb.com). “Especially in a chemical plant, there can be dangerous equipment and processes where you don’t want operators and maintenance staff going if they don’t have to. Today’s sensing technologies coupled with the ability to send information to computers and handheld devices reduces the amount of time that employees need to be in these hazardous locations, because they can check the data related to the machine or the process from the safety of their PC or device, as well as know what needs to be done before they enter the area when it does become necessary.”
New Smart Sensors Providers of smart sensors continue to innovate based on the needs of the chemical process industries, so product launches are happening frequently. Here’s a roundup of the latest in the space. Pepperl+Fuchs is launching a new IIoT-ready system, dubbed Wilsen. “The idea behind the Wilsen concept is that we provide sensors that are self-contained, battery-powered and can communicate via one of many networks,” says the company’s Hornis. “We can take one of these sensors, attach it to a tank in the middle of nowhere and, as long as there’s a cell tower in the vicinity, transmit data.” While there will be an entire family of Wilsen sensors, Wilsen.sonic.level, a wireless sensor with integrated ultrasonic module for fill level detection, will be the first technology available in the U.S. this year from this line (Figure 2). ![]() Figure 2. Wilsen.sonic.level, a wireless sensor with integrated ultrasonic module for fill level detection, will be the first technology available in the U.S. this year from this line of IIoT-ready sensors Emerson recently launched a new Location Awareness system (Figure 3) that provides realtime, safety-focused monitoring of employees. Enabled by WirelessHART Anchors and battery-operated personnel and asset tags, the system includes geofencing, safety mustering and man-down alerts. “It allows management to understand where assets and people are in the plant at any given time to make sure that employees are safe and that management can send help if there’s an issue,” says Emerson’s Karschnia. ![]() Figure 3. Enabled by WirelessHART Anchors and battery-operated personnel and asset tags, the Location Awareness system includes geofencing, safety mustering and man-down alerts Yokogawa recently announced the release of its Sencom Smart Adapter SA11 (Figure 4). The data gathered by the adapter, through an interface mechanism, can be uploaded to the cloud and used for optimization of plant operations, efficiency and asset management. ![]() Figure 4. The data gathered by the Sencom Smart Adapter, through an interface mechanism, can be uploaded to the cloud and used for optimization of plant operations, efficiency and asset management ABB Ability Digital Powertrain is a recently launched suite of digital solutions, including sensors, software and services, combining connectivity and data analytics (Figure 5). “The Digital Powertrain combines our existing sensing technologies for monitoring motors, bearings, pumps and drives all in the same portal where users can either analyze a particular element of the system or take a look from a high level at the complete powertrain,” says ABB’s Rdzanek. ![]() Figure 5. ABB Ability Digital Powertrain is a suite of digital solutions, including sensors, software and services, combining connectivity and data analytics Honeywell introduced the SmartLine Wireless Pressure Transmitter (Figure 6), which offers a flexible, scalable, secure and cost-effective solution for both pressure monitoring and control when combined with the company’s wireless network technology. The OneWireless Network infrastructure supports two of the leading industrial wireless protocols — ISA100 Wireless and WirelessHART, providing flexibility when implementing wireless systems. ![]() Figure 6. The SmartLine Wireless Pressure Transmitter offers a flexible, scalable, secure and cost-effective solution for both pressure monitoring and control |
Today’s available technologies are also being applied to improve maintenance. “The question we are regularly asked is: ‘How can the value proposition of IIoT be implemented in daily maintenance and asset management?’” says Anupam Durani, BU manager sales and marketing for Analytical Instruments with Yokogawa Europe. “IIoT has the potential to have a dramatic effect in how maintenance is carried out. It can allow technicians to diagnose a device from any location and access the valuable information to troubleshoot and solve a problem. Operators can be notified immediately whenever an asset fails to operate within a normal range and receive all necessary instructions for returning the asset back into operation.”
In a similar vain, Industry 4.0 is also shining in the arena of overall plant optimization. Rockwell’s Bordelon says the technology is currently being used to improve product quality and asset utilization. “Today’s connected chemical plants have an entirely new way of doing business. They know, in real time, when a process isn’t where it needs to be or if there’s a problem with equipment or unskilled operators causing quality issues. They have the data to support continuous improvement engagements and root cause analysis, as well as real-time alarms that tell them how to modify the process to remove the quality issue or safety concern. We call it asset utilization and by using digitization to optimize equipment and processes, benefits like reduced downtime and improved product quality are being realized.”
Bob Karschnia, vice president and general manager of Wireless for Emerson Automation Solutions (Shakopee, Minn.; www.emerson.com) agrees. “The premise of Industry 4.0 is using the available technologies — smart sensors, data analytics and connectivity — to improve operations. We already have the sensors and other technologies in place and are using them to give us the information we need to improve the efficiency of the plant, increase reliability of equipment and process, boost safety and reduce the environmental impact of the plant.”
As an example, he points to monitoring the efficiency and reliability of heat exchangers — a common practice in today’s process environments. “In a 250,000 barrel refinery, just by monitoring heat exchangers for efficiency and fouling via currently existing sensing and analytics technologies, it is very likely that they can save about $3 million a year between energy savings and maintenance costs, which provides a return on investment that can be measured in months.”
Driving toward Industry 4.0
Most experts agree that implementation of currently available technologies in an effort to tackle current issues within the facility is the best way to start embracing Industry 4.0. “When we begin to help our customers optimize the performance of the plant, we ask what their consistent problems are across the plant or enterprise,” says Karschnia. “We give our customers a list of equipment that we recommend starting with — about eight to ten possible applications, such as heat exchangers and steam traps, in which pervasive sensing provides tangible results — and then suggest building on the momentum of that success. In addition, it is often possible to use the success of the first application to pay for the next one and so on until, eventually, they all pay for themselves and it becomes almost self funding.”
Honeywell’s Arora agrees: “While the long-term goal of Industry 4.0 is a connected enterprise view, the practical approach to beginning the journey is to start with a sublevel or subsection view before attempting the end-to-end journey.
“We encourage our customers to sit down and talk about their current challenges, such as which units cause what problems and then begin to build an optimization model around one of those issues or units, using currently available data and technology to gather information and provide context around the data to help them improve that process or better use the asset,” he explains. “Once that journey starts, we can identify the next challenge and add more sensors to more equipment until the entire organization is involved. And, the ultimate goal is that, eventually, all views come together in one place after they have been massaged, analyzed and personalized for each person who needs to see them.”
Sensors: the heart of Industry 4.0
“The interesting part of this is that all the base technologies are already available,” says Helge Hornis, technical director of Factory Automation with Pepperl+Fuchs Americas (Twinsburg, Ohio; www.us.pepperl-fuchs.com). “We have sensors that are smart. We have ways to transfer information wirelessly. We have software with data analytics, artificial intelligence and machine learning. We have hardware to set up the necessary networks. We just need to put it all together and are really just waiting for the applications to be invented. This means it will be a swifter journey to this, the fourth industrial revolution, than to the previous ones because nothing needs to be invented to make it happen.”
But at the very heart of it all is the increasingly smart sensor. “The phrase I like to use is that you can’t manage what you cannot measure,” says Siemens’s Heilveil. “There is no improvement in process or product quality without measurement. There is no management without data that comes from a measurement, so this means instrumentation — the sensors and gadgets in the trenches doing the measuring — are key to Industry 4.0.”
Yes, in addition to the sensors you need a way to move the data from the sensors (usually a gateway of some sort) to a location (often the cloud or a historian) for storage and number crunching via analytics and, of course, connectivity to move this now actionable data to the people who can use it for optimizing the process. “These are all necessary components and there isn’t any one component that’s more important than another, but, that being said, the process instruments and sensors are where the rubber hits the road. Just as you can’t tell if someone has a temperature without a thermometer, you can’t collect data without a sensor,” says Heilveil.
So what’s going on with today’s smart sensors that is making data collection easier than ever? A lot. “We currently have high-quality data and sensors and the innovation continues, so I guess you could say we have ‘smarter’ smart sensors,” says Honeywell’s Arora. The first development, he says, is the combination of sensor measurements. “What we are seeing is there is much effort and expense required to install multiple sensors in places where there are constraints. In a location like an offshore platform, any one device saved, multiplied by hundreds, it is a gain. In a process plant, fewer numbers of sensors mean less tapping points and inserts into the piping. So we are seeing the development of sensors that can pull multiple measurements and provide data from one installation.”
Another improvement is that more and more sensors are going to wireless, battery-powered technologies, says Emerson’s Karschnia. “We have wireless, battery-operated transmitters that are driving toward non-intrusive measurements for almost everything, including pressure, temperature, level, flow corrosion monitoring, acoustic monitoring, gas sensing, electrical noise and so on. This allows users to connect them quickly and easily and at a much lower cost. This is the reason why people are able to add sensors more pervasively.”
In addition, today’s sensors offer a much richer array of options and opportunities to improve the process they are interfacing with, says Siemens’s Heilveil. “They offer robust diagnostics, alarming features and safety functions. Some measure as many as four or six variables,” he says. “If you take all of the diagnostics, safety functions and multivariable measurements and pair that up with robust digital protocols, it enables today’s sensors to quickly and reliably provide critical and significant amounts of quality data, differentiating them from earlier sensors.”
In the end, whether starting small with monitoring one piece of equipment or beginning on the journey to an integrated enterprise, embracing Industry 4.0 now is imperative to staying competitive. “I don’t think processors stand any chance of surviving if they don’t embrace it,” says Pepperl+Fuchs’s Hornis. “Costs will go up, quality will go down and efficiency will plummet in comparison to their competitors who are likely employing Industry 4.0 technologies. It will be hard for a business to remain competitive when a large fraction of their market moves in that direction and they do not. There aren’t too many typewriters around today and there’s a reason for that.”
Joy LePree