Crossflow (CF) filtration is widely used for separating substances with poor filtration properties. As the method’s name implies, a crossflow of the feed continuously flows across the filter membrane in order to wash away material accumulations that clog the membrane pores. Nevertheless, conventional methods rely on a pump to adjust the feed overflow rate, which requires substantial energy, even for feeds with low viscosity, says Bruno Hegnauer, process engineer at KMPT AG (Vierkirchen, Germany; Booth 628). And at higher viscosities, heat generated by flow resistance has to be removed by heat exchangers to prevent thermal degradation of sensitive products, he says.
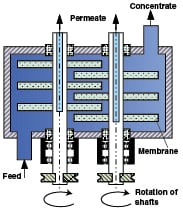
KMPT has recently developed a new process for dynamic crossflow filtration that achieves energy savings of up to 80% compared to conventional CF systems, says Hegnauer. The dynamic CF system also makes possible the “up-concentration” of retentate to viscosities of 700 cP compared to the 20–50 cP limitation of classical tubular designs; this opens up new fields of application, he says.
In KMPT’s process, the mixture to be separated is fed to a filter module (diagram) consisting of two hollow shafts on which circular ceramic-filter disks are attached. The shafts are positioned to maximize overlap of the disks, which are separated by a few millimeters. As the shafts are rotated, a turbulent flow is generated between the disks, thereby preventing the formation of clogging layers. Inside the filtration module, there is a uniform pressure, resulting in a constant trans-membrane pressure, which is supplied by the feed pump. Concentrate is discharged at the outlet.
The dynamic CF filtration system was commercialized in June 2007, and systems can be built to handle feedrates from 1 to 2,500 L/h per CF module. Ceramic membranes are available with pore sizes from 7 nm to 2 µm.
Gerald Ondrey