New milling, grinding and size-reduction equipment helps processors obtain better efficiencies and develop new products
Although milling and size-reduction equipment may be mature — some technologies date back to the 1800s — evolving needs of chemical processors, including the demand for better efficiency, new applications and materials and other trends, require milling and size-reduction equipment manufacturers to constantly innovate. Here’s a look at what’s new in modern milling and size-reduction equipment, as well the driving forces behind today’s offerings.
“We work hard at improving our products and are still coming out with new and patented features that add value for our customers,” says Chris Nawalaniec, vice president of sales and marketing with Stedman Machine (Aurora, Ind.; www.stedman-machine.com). “Everything we do today targets improving either product quality, lowering operating costs or designing a new process for our customers to help optimize their specific projects. We study different metallurgy for wear parts and use computational fluid dynamics (CFD) to model material flow through machines so we better understand where we need to improve parts from a wear standpoint and equipment from an energy-consumption standpoint. We’ve had success in terms of coming out with feature improvements that help customers.”
Increasing efficiencies
Energy and space efficiency are some of the most crucial considerations when chemical processors seek milling and size-reduction equipment, and mill providers are responding in a variety of ways.
Bühler AG (Uzwil, Switzerland; www.buhlergroup.com), for example, is offering a solution for wet grinding that includes the MacroMedia pre-dispersing unit and the MicroMedia bead mill, says Norbert Kern, director of product management and process engineering at Bühler. The combination of the pre-dispersing unit for pre-conditioning with the bead mill for fine grinding and fine conditioning of material results in higher-quality product in a shorter period of time, with less energy consumption.
Due to the improved process control of the MacroMedia (Figure 1, left) in the pre-grinding stage, fluctuating raw material qualities can be balanced out, achieving uniform properties for intermediate products, allowing an optimization of the fine grinding process with the MicroMedia bead mill (Figure 1, right). “Our bead mills employ beads that are used to grind the product into smaller sizes. Using smaller beads in the same size grinding machine allows more contact points and more efficient grinding, resulting in faster throughput and improved quality levels,” says Kern.
Not only does this create more efficiency in the grinding process itself, but the use of smaller beads also boosts energy and space efficiency because less energy is required to achieve higher output performance in the same equipment footprint, explains Kern.
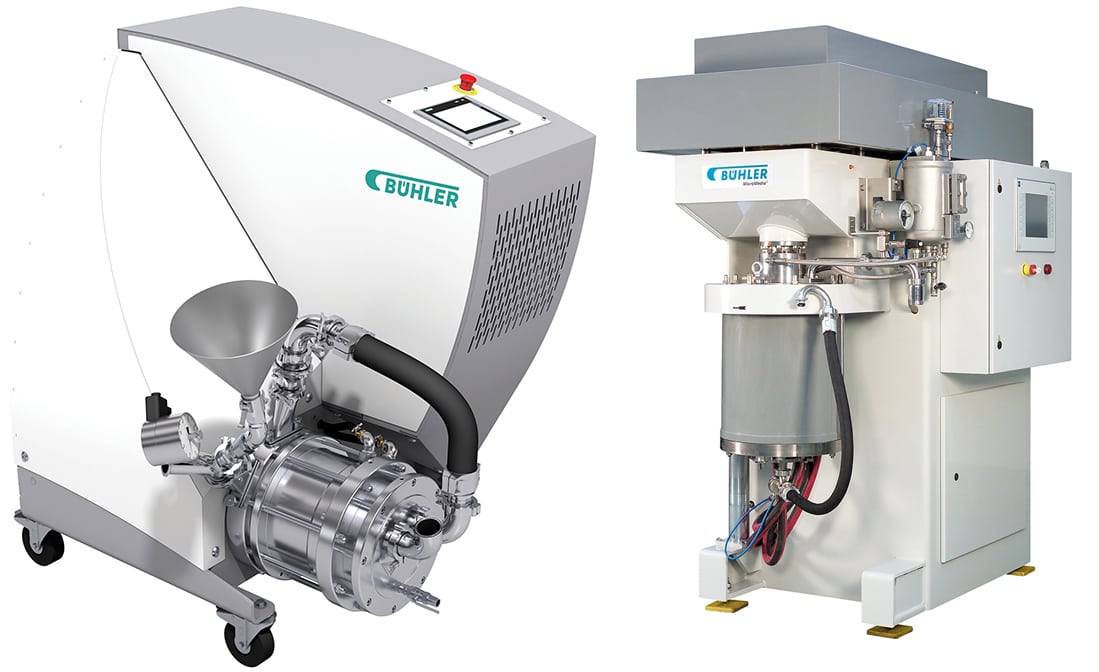
Figure 1. Due to the improved process control of the MacroMedia (left) in the pre-grinding stage, fluctuating raw material qualities can be balanced out, achieving uniform properties for intermediate products, allowing an optimization of the fine grinding process with the MicroMedia bead mill (right)
Bühler
Extending to broader areas
While material size reduction has long been an integral unit operation in the chemical process industries (CPI), there is growing interest in the processing of heat- or oxidation-sensitive and impact-resistant materials. Examples of these include nutraceuticals and pharmaceuticals or tough polymers used in 3-D printing and powder coatings. These emerging, high-tech materials present size-reduction challenges that can be addressed by Air Products’ PolarFit cryogenic grinding technology (Figure 2), which uses liquid nitrogen to super-cool the materials being ground.
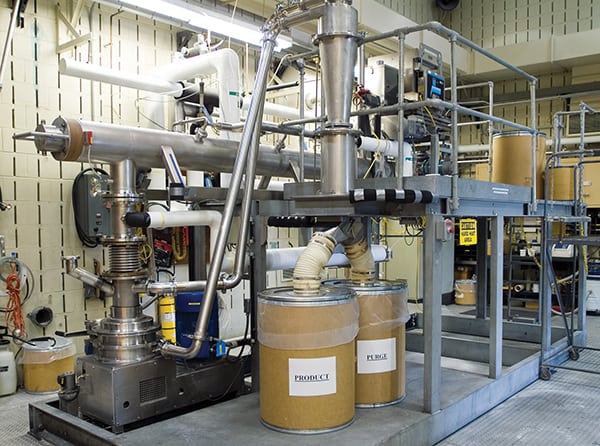
Figure 2. Air Products’ PolarFit cryogenic grinding technology uses liquid nitrogen to super-cool the materials being ground, which temporarily changes the physical properties of difficult- or impossible-to-grind materials, making them easier to grind
Air Products
As Tim Boland, principal equipment engineer with Air Products (Lehigh Valley, Pa.; www.airproducts.com), explains, “Processors may be dealing with materials that are difficult or impossible to grind in an economical fashion using traditional, ambient-temperature grinding technology. With cryogenic grinding, liquid nitrogen is used to super-cool these materials and temporarily change their physical properties, making them easier to grind.”
Another advantage of using liquid N 2 in cryogenic grinding is the generation of inert N 2 gas. “Any time you process combustible materials there is the potential for a dust explosion. Nitrogen gas, either generated during cryogenic grinding or intentionally introduced as a gas into the solids processing equipment, helps mitigate the risk of dust explosions,” Boland says.
Processing specialty products
While the trend had been for U.S. manufacturing and processing industries to move overseas in an effort to compete on a cost basis, during the past five or six years, the cost of production in many overseas countries began to rise, bridging the cost gap and causing a shift in some processing back to the U.S. “While it is still more expensive to manufacture in the U.S, it is closer in cost than it had been. Currently, a lot of U.S.-based processors are bringing production of specialty, higher-value products back to the states. However, they need to do so in a more efficient manner,” says Bill Brown, director of sales and marketing with Hosokawa Micron Powder Systems (Summit, N.J.; www.hmicronpowder.com). “To meet this need, we added more sophisticated controls so less human interface is required, increased process efficiency of the milling and classification systems and fine-tuned these processes for tighter, more efficient control of airflow to reduce energy consumption.”
In specialty product processing, providing systems that address efficiency needs, as well as versatility, is a necessity. Hosokawa’s Mikro UMP Universal Milling System, a compact, high-speed impact mill capable of coarse granulation or fine size reduction with interchangeable rotor configurations, fits the bill (Figure 3). The system provides the same grind as a traditional hammer- and-screen setup while adding the flexibility of converting to a pin mill for fine size reduction or a rigid rotor for de-agglomeration.
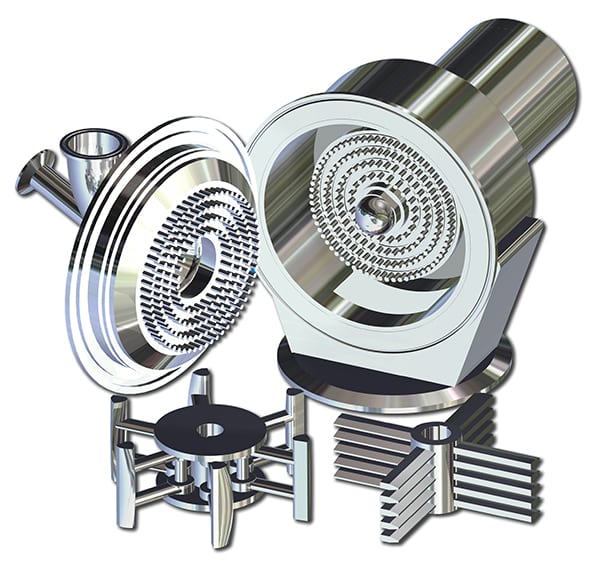
Figure 3. Hosokawa’s Mikro UMP Universal Milling System, a compact, high-speed impact mill, is capable of coarse granulation or fine size reduction thanks to interchangeable rotor configurations. The system provides the same grind as a traditional hammer-and-screen setup while adding the flexibility of converting to a pin mill for fine size reduction or a rigid rotor for de-agglomeration
Hosokawa
While the system provides flexibility across the food, pharmaceutical and chemical industries, one of the latest applications for this technology is in polymers and plastics. “Processors are producing polymers down to 30-, 40- and 50-mesh particle sizes and often produce a wide range of materials, which requires frequent changeovers,” notes Brown. “This milling system allows them to get a smaller and finer product and quickly change rotors out to produce different materials, which means they can get into new markets and sell products of a much higher value into specialty applications at a higher profit.”
Smaller particles
A decade ago, laboratory milling process capability ended somewhere with particles in the micrometer range, but, recently, the need for smaller particles is growing. “Everyone wants to know how fine we can get with our particles, with customers requesting sizes into the nanometer range,” says Wolfgang Simon, sales director with Fritsch International (Idar-Oberstein, Germany; www.fritsch-international.com).
The interest in nanomaterials, says Simon, is because, as particles get smaller, they have completely different physical and chemical properties. For example, in the solar cell industry, if zinc oxide is milled into the nanometer range, it changes from a yellow powder to a transparent powder, yet retains the same electrical properties, allowing users to coat a solar cell with this clear nano-powder and maintain the electrical properties needed to conduct the electricity. And, in the pharmaceutical industry, the finer the active pharmaceutical ingredient (API), the lesser the amount of substance required. “When the API is in the finer nanometer range, the effects inside the body will be faster, meaning you need less active API for the same result and with less side effects,” explains Simon.
And, getting to the nanometer range on a laboratory scale is of utmost importance in research and development (R&D) of new products, such as those for lithium ion batteries and medicinal cannabis, according to Simon. However, while smaller particle sizes are a growing trend in R&D, mills capable of producing smaller particles must still be viable for daily use in the laboratory. This means they must be as safe, efficient and easy to clean as mills designed to produce larger particle sizes. To satisfy this need, Fritsch developed its Planetary Mill Pulverisette 5 premium line with two grinding stations for fast wet and dry grinding of hard, medium-hard, soft, brittle and moist samples, as well as for mechanical alloying, mixing and homogenizing of larger sample quantities with reliable results down to the nanometer range (Figure 4).
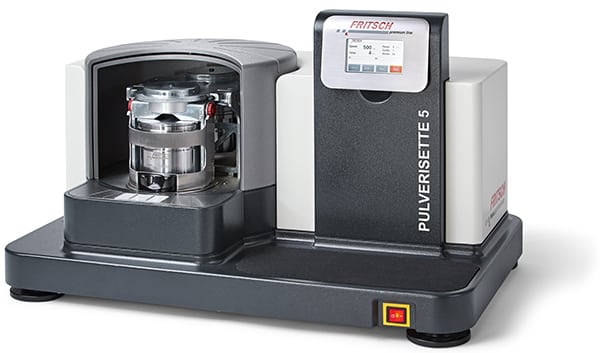
Figure 4. Fritsch’s Planetary Mill Pulverisette 5 premium line features two grinding stations for fast wet and dry grinding of hard, medium-hard, soft, brittle and moist samples, as well as for mechanical alloying, mixing and homogenizing of larger sample quantities with reliable results down to the nanometer range
Fritsch
The mill works on the planetary principle, which employs the high-energy impact of grinding balls, as well as friction between grinding balls and the grinding bowl wall. The grinding bowl, containing the material to be ground and grinding balls, rotates around its own axis on a main disk rotating in the opposite direction. At a certain speed, the centrifugal force causes the ground sample material and the grinding balls to bounce off the inner wall of the grinding bowl, cross the bowl diagonally at an extremely high speed and impact the material to be ground on the opposite wall of the bowl. The grinding bowls reach twice the speed of the main disk during this process. Due to the 2.2-kW drive power and centrifugal acceleration, high-performance grindings down into the nanometer range are possible.
Smaller particles are also frequently requested on the process scale, where a balancing act between ultrafine grinding and energy efficiency is often a challenge, according to Peter M. Koenig, product manager for particle processing at Bepex International LLC (Minneapolis, Minn.; www.bepex.com). “There’s been a shift in the process industry to get finer and finer grinds. In addition to smaller particles, users also want the particles created specifically for their end use. This means they don’t want them finer than they have to be and they want to control the top size, as well, which requires controlling the overall distribution.”
However, the desire for reduced and specific sizing can have consequences on energy efficiency. Achieving smaller-sized particles requires a higher impact velocity, necessitating more energy; conversely, if less energy is used to fracture the particle, it may be necessary to run materials through multiple times, ultimately using more energy. “With this in mind, we strove to produce a finer particle at a lower impact velocity,” he says.
While the equipment Bepex developed does not reach the nanometer range, the Pulvocron Air Swept Pulverizer (Figure 5) provides high-speed material impact and internal classification for ultrafine grinding of powders and cakes. It is well suited to applications requiring moderate moisture reduction and fine-size reduction in a single step. The short residence time and intense milling action inside the chamber offer high-efficiency processing of the material in a compact system.
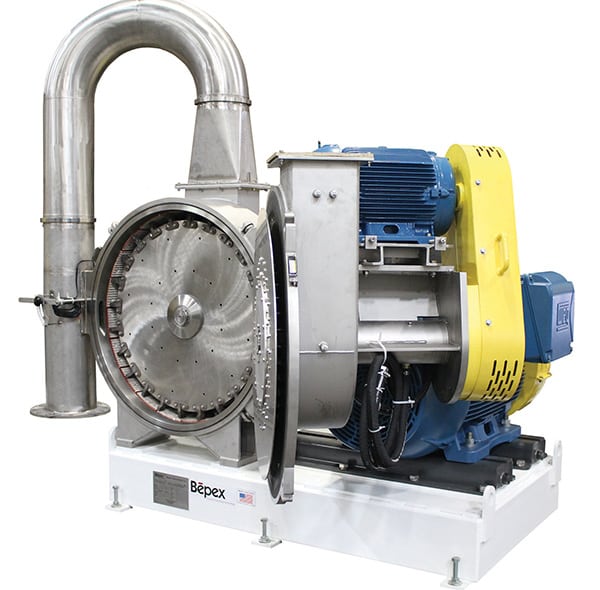
Figure 5. Bepex’s Pulvocron Air Swept Pulverizer provides high-speed material impact and internal classification for ultrafine grinding of powders and cakes. It is well suited to applications requiring moderate moisture reduction and fine size reduction in a single step
Bepex
“We can achieve and control very high impact velocities, as well as the tolerance between the impact surface and the liner, which prevents bypassing of coarser particles,” explains Koenig. “These very tight tolerances at high impact speeds allow the equipment to grind both crystalline materials that shatter on impact, as well as tough materials that require shredding. On exit, the material goes through an air classifier, which, by centrifugal speed, performs separation of fine and coarse materials. Coarse materials are reintroduced to a return stream and back to the mill, while the fine classified material is collected.”
This system not only provides ultrafine grinding, but also boosts energy efficiency because only material that is too coarse gets reintroduced. “We grind only the parts that need grinding, so it can produce more product on specification at lower energy consumption,” Koenig says.
‘Green’ markets
There is a big push for green, sustainable and landfill-free processing, according to Steve Knauth, marketing and technology manager with Munson Machinery (Utica, N.Y.; www.munsonmachinery.com). “We are seeing the trend toward recapture and reuse accelerate among our customers,” he says. “In addition, they are also looking for equipment that is going to minimize the amount of material that must be sent into the atmosphere or landfill. This means processors need size-reduction equipment that can handle these green applications while producing less fines.”
As a result, Knauth says his company is seeing a shift away from hammer mills and toward the company’s SCC Screen Classifying Cutter in many applications, because it’s designed to reduce hard and semi-hard particles into fairly precise sizes. It is also easily controllable, which means it produces less fines, reducing the amount of material captured in the dust collection system.
The SCC Cutter performs like a knife cutter, but handles a greater diversity of materials, including friable, semi-friable, fibrous, semi-hard and hard materials, and retains sharpness. At medium to high speeds, it impacts material similar to a hammer mill, but adds the flexibility of variable speed for greater control of particle sizes. The rapid throughput with less impact results in minimal fines. “All this lends itself well to the green industry trend. The SCC Cutter is capable of recapture and reuse/recycle applications due to the variety of materials it can handle, and minimal fines means there is less material in the dust collection system for disposal,” notes Knauth.