Plug-and-produce concepts for automating modular skids may solve integration challenges for modular construction projects
Modular construction — both of facilities and process skids — has gained popularity due to its benefits, including speed of delivery and predictability of cost and schedule (see Box 1 below and Chem. Eng., June 2017, pp. 44–50; www.chemengonline.com/practical-solutions-modular-project-execution). However, with the process industry embracing big data, Industry 4.0 and the industrial internet of things (IIoT; www.chemengonline.com/category/iiot-2), reliance on automation is also growing, which sometimes is at odds with modularity, as the automation of modular skids can, at times, be difficult to integrate with higher-level, plant-wide control systems. Fortunately, the automation industry is making strides to overcome these difficulties via the development of modular automation systems based on Lego-like and plug-and-produce concepts.
The term “modular” can apply to anything from a simple, pre-assembled process unit to larger skid modules that form entire production lines to multiple container modules joined together to construct an entire facility. Modules can be simple, off-the-shelf units or complex custom-engineered solutions. But in all of these scenarios, if the module is not a stand-alone unit, it must be integrated into the higher-level control system of the plant, and this is where things get tricky.
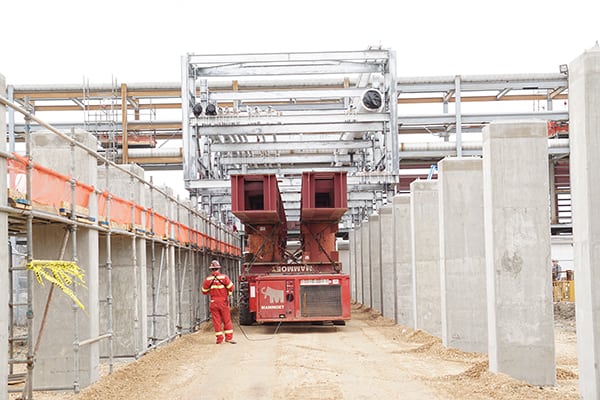
Figure 1. Lubrizol’s highly reactive poly-isobutylene production unit from Jacobs’ EPC project site in Deer Park, Texas
Jacobs
Impact on automation
Process module automation is commonly accomplished in one of three ways, according to Tim-Peter Henrichs, marketing manager (chemical industry), with Yokogawa Deutschland GmbH (Ratingen, Germany; www.yokogawa-blog.de/en):
- The module has no automation system and control is accomplished via the plant’s automation system, which is common with simple modules. In this scenario, wiring must be run from the plant’s automation system to the module’s field devices via hardwiring or a multiplexing system.
- The plant’s existing automation system connects to the module’s I/O (input/output) via a digital connection, common with more complex modules. This approach allows the module builder to prewire all I/O to field devices, so the plant’s automation system only needs to connect to the I/O via a digital data link.
- The module has its own automation controller, which is linked to the plant’s automation system via a digital connection, common with more complex modules, allowing the module builder to test module and automation system operation prior to shipment. The module’s automation system may not be familiar to plant personnel. Plants can specify the type of automation system, but this may drive up costs and delivery time.
“Often, the mechanical exchange of a process module requires less time than the integration of the module and plant automation systems,” says Henrichs. Common problems include difficulties in establishing digital connection, incompatibilities between the plant’s automation system and the module’s I/O, lack of plant personnel’s familiarity with the module’s automation system and different naming conventions for tag names, alarms, events and commands. Modular automation allows module vendors to include and protect their intellectual property and also helps their end users by reducing the costs and time required to build and operate flexible production plants.
Integration problems magnify when there are multiple skids manufactured and delivered by different vendors, explains Gordon Bordelon, chemical industry lead, with Rockwell Automation (Milwaukee, Wis.; www.rockwellautomation.com). “One of the biggest issues is that it creates project risk,” he says. “When implementing a project, there are often different systems with different automation technologies, so you have to make sure upfront that they are going to be consistent. If you get to the startup and commissioning stage and then realize that one system can’t communicate with another or that the skid can’t be integrated, the costs are much higher as the remediation occurs on site, delaying startup and ultimately missing production schedules.”
Operational readiness can also be negatively impacted. “Whether you have one module or an entire modular facility, it is a problem if the automation is inconsistent,” says Bordelon. “The operations staff at the facility must know how to operate all the systems, which is problematic if the automation is inconsistent.” In addition, the modules usually need to be tied into business systems such as laboratory information-management systems (LIMS), enterprise resource-planning systems (ERP) and computerized maintenance-management systems (CMMS). “These modular plants not only have to be able to operate, but they also require the ability to share data and communicate with other business systems in order to be operational- ready,” notes Bordelon.
And, information sharing is more important than ever in the current data-centric environment, says Greg Turner, global OEM process segment business leader, with Rockwell Automation. “Not only are we changing how we build plants, but at the same time, we are increasingly relying on automation to accommodate Industry 4.0 principles, big data and the industrial internet of things, so plants and processes are becoming more complex and interconnected.” Proper integration of the automation system permits situational awareness for the people running the plant and allows them to use data to plan predictive maintenance, examine alarm conditions and understand the health and efficiency of the equipment and processes. “This type of situational awareness falls under asset utilization and can be adversely affected if automation is inconsistent in a modular environment,” says Turner.
Safety can be another issue in modular plants. “In the environment of the chemical industry, safety is very important. There are emergency shutdown systems and safety instrumented systems (SIS) and modules have to be consistent with those systems,” notes Craig Correia, director of process industries for North America with Festo (Islandia, N.Y.; www.festo.com). “If there is an emergency shutdown, the module can’t go rogue. It must cooperate with the safety system. You can’t have a module with a safety protocol or shutdown system that isn’t consistent with the equipment in other areas. In addition, it’s important that the interfaces look the same from skid to skid. In layman’s terms: you can’t have one emergency stop that’s a round, red button that you physically push and another that’s on a touchscreen because this could confuse operators. Consistency in safety is crucial.”
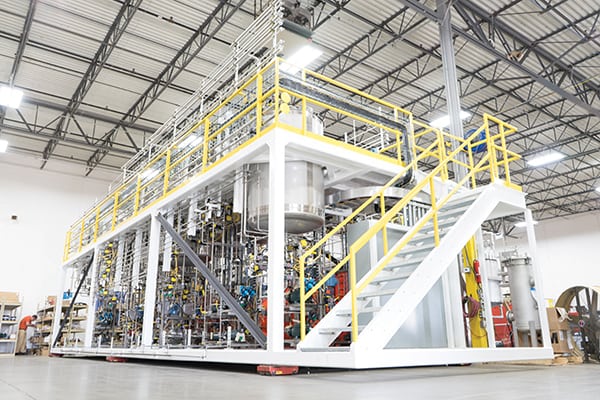
Figure 3. The modular approach provides schedule and cost certainty because module systems are built in a shop so contractors aren’t on the facility site
EPIC Process Systems
The Many Benefits of Going Modular
Modular construction, whether it’s a simple skid-mounted filtration system, an entire process line containing mixers, reactors, heat exchangers, pumps and the like, or a complete facility, constructed of multiple process modules or containers that are connected together at the user’s location, provides a host of benefits and cost savings when done correctly. The modular concept means all the necessary components, both process and ancillary equipment such as piping, instrumentation and electrical wiring, are installed in a structural steel frame or mounted on a skid in a modular shop. Everything is tested before delivery, the module is shipped via truck or barge and, finally, installed on site. While there may be various levels of modularization, all modules are pre-fabricated to the maximum level of completion at a yard that is remotely located from the customer’s plant site. Modular yards are often indoors and operate on an assembly-line-type premise, which provides many benefits.
“The objective of modular plants and process skids is to support faster and easier commissioning during startup of a process plant and during changes of production in the lifecycle of a process plant,” says Tim-Peter Henrichs, marketing manager (chemical industry) at Yokogawa Deutschland GmbH (Ratingen, Germany; www.yokogawa-blog.de/en). “This is a significant prerequisite for flexible production, which is a big trend in specialty chemicals, pharmaceuticals and life science, as well as in LNG and marine markets.”
The biggest benefit, according to Jim Flake, director of module consulting with Jacobs Engineering (Dallas, Texas; www.jacobs.com), is mitigation of labor availability at the sites where large projects are being installed. “Especially in the U.S. and the Gulf Coast area, there is a strain on labor and we continue to see the available skilled craft labor pool erode,” he says. “Being able to move work off site and out of the area means you aren’t competing for the same labor pool, which is a huge benefit” (Figure 2).
The modular approach also provides schedule and cost certainty, according to Jason Baron, power and controls group manager, with EPIC Process Systems (St. Louis, Mo.; www.epicmodularprocess.com). “We are building the system in our shop so contractors aren’t on the facility site. Not only can on-site construction be inconvenient, sometimes it’s impossible for a plant to operate during large-scale construction,” he says (Figure 3).
In addition, site prep work, such as preparing foundations and getting ready for the modules to arrive, can be done in tandem with the module’s construction, greatly accelerating the project timeline. Also, says Baron, building within a controlled-environment modular yard provides a cost savings when compared to having contractors onsite, where they may be subject to weather and permitting delays, which can increase labor and project costs.
“Also helping to speed up schedule and delivery is the fact that when building the whole system modularly in-house, we can fully test the system before it gets to the site,” says Baron. “That reduces time spent with on-site startup and troubleshooting because the system is already tested and ready to go.”
Other benefits of going modular include increased safety and quality, says Preston Wendel, global director of fabrication, with Fluor Corp. (Irving, Texas; www.fluor.com). “Usually there are multiple levels to a plant and a lot of critical activities for a project include working at heights, but when we modularize a job, we can take some of that work and bring it down to grade which removes many of the hazards associated with working at heights,” he says. “There’s also safety improvements due to the repeatability of work performed in the same location using the same standards.”
This repeatability also yields quality improvements, says Wendel. “Moving from a stick-built environment, where everything is new, to a manufactured modular approach, where there is repeatability, provides increased quality. We see better rejection rates on welding and overall better quality coming out of modular yards compared to what we see on stick-built jobs” (Figure 4).
Modular construction, especially process skids, can also provide flexibility, says Craig Correia, director of process industries for North America, with Festo (Islandia, N.Y.; www.festo.com).
“Modularity allows processors to be more flexible with production because modules can be moved or placed in series. They can scale up certain sections of the plant if they need to fix a bottleneck or increase production without having to duplicate or redesign,” he says. “Ten or fifteen years ago, the plant was designed for a particular purpose and if a change was necessary, you had to interrupt the process to expand equipment that was currently in use. Modules are designed to be used in series and moved around as capacities increase or the product changes.”
A modern module approach
While a remedy is necessary, integration of modular components is still a work in progress. However, component providers, module builders and automation suppliers are all working toward the common goal of simplifying integration between module automation and higher-level control systems.
On the component level, manufacturers like Festo are embedding controllers on instruments and devices so they can be tested when used in a modular process skid and are making sure that the control is neutral so their controller can “handshake on the supervisory level with the ‘big boys’ in the marketplace,” says Correia. “It is our responsibility that our controller can pass all the relevant information and handle all the safety protocols being exchanged between the skid and the automation system. We are continually evolving and getting better at this.”
On the module side, builders are simplifying the physical connection, says Ted Faiella, senior director of Honeywell UOP’s (Des Plaines, Ill.; www.uop.com) Applied Process Excellence Center. Traditionally, modular units were automated by installing junction boxes within the modules. “All the instrumentation on the module was connected to junction boxes at the module-fabrication shop so continuity checks could occur before shipment. At the plant, this junction box connected to a marshalling rack, which connected to the actual I/O cards,” Faiella explains. “But, within the last five years, this has changed. We now provide universal process-control cabinets (UPCs) that contain I/O cards. This eliminates the traditional wiring method,” he says. “Instead, the I/O cards are in the field and you only need to run fiber optic cabling from the UPC box to the control room.”
“This simplifies field wiring and the associated check out and reduces the size of the control room, while also reducing costs and allowing fewer things to go wrong,” adds Amy Gavin, senior marketing product line manager for modular with Honeywell UOP.
Meanwhile, automation suppliers are making progress in the areas of open architecture and modular automation concepts. “Chemical and pharmaceutical-related industrial associations are discussing a technology concept to support easy integration of any type of controller,” says Yokogawa’s Henrichs. “This is called a Module Type Package (MTP) and is based on Automation Markup Language (AML) technology in which the significant information of the process module automation application can be exported for easy integration with any upper automation system” (Figure 2).
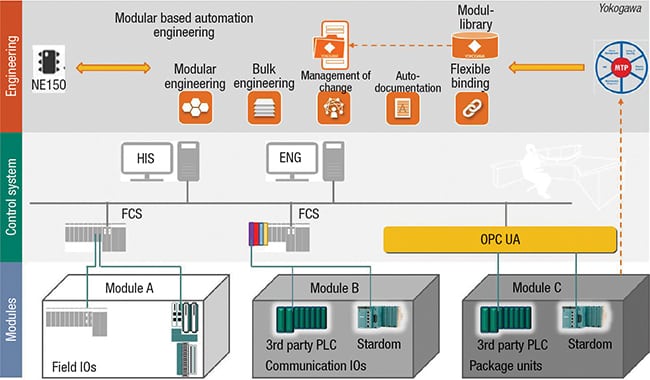
Figure 2. Chemical and pharmaceutical-related industrial associations are discussing a technology concept, called a Modular Type Package (MTP), to support easy integration of any type of controller. MTPs are based on Automation Markup Language (AML) technology in which the significant information of the process module automation application can be exported for easy integration with any upper automation system
Currently, says Henrichs, modular-type automation packages do exist. “They cover the HMI (human machine interface) and communications use cases,” he says. “The orchestration and other needed functions are on the way and will complete the full MTP concept step-by-step.”
David Funderburg, global technology manager, product group, chemicals and refining, and industrial automation for oil, gas and chemicals, with ABB, Inc. (Cleveland, Ohio; www.abb.com), agrees that MTPs are the current working solution to the problem. “They provide a standard way to integrate skids,” he explains. “The skids come configured and part of the delivery includes a standardized XML packet, or a modular type package, that integrates into the HMI system and automation platform, so we don’t have to worry about rebuilding displays for consistency. Even if you have 20 skids from 20 different vendors, as long as they all have this module type package, the communication and HMI will look and act the same. Even if I take the same MTP and import it into a competitor’s HMI package, it will still look the same and the layout will still be the same and the performance will be the same. This allows reduced engineering costs because integration is simplified.”
Rockwell Automation is focused on creating customizable off-the-shelf packages that have “pre-tested fundamental building blocks,” known as Process Object Libraries, which vendors would use to develop their skid control systems. “By using these building blocks with the vendor’s IP to design the controls, it provides consistency,” says Rockwell’s Bordelon. “If a processor used multiple skid vendors and our application libraries, the complexity of applications, complexity of maintaining the systems and the data flows and constructs would be consistent enough to cut down on integration issues. It all fits together because of the standardization of these library objects and the way they hang together.”
“These open approaches and standardized applications mean we, as automation suppliers, are moving down the path to provide business advantages to the end users,” says Rockwell’s Turner. “They want and need to shorten startup time and reduce integration costs associated with putting different skids together. They are looking not only to get consistency within the plant, but also from plant to plant so they can move skids from place to place throughout their organization without creating an integration nightmare.”
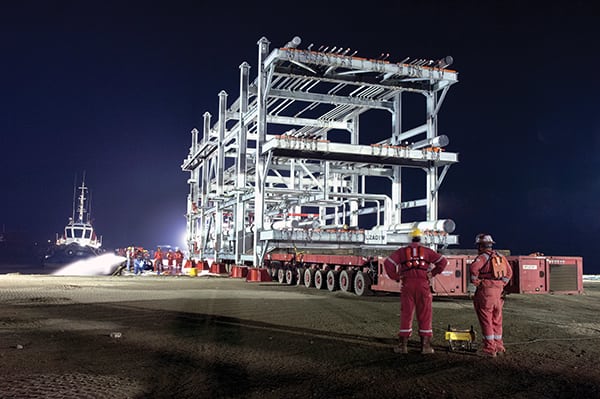
Figure 4. Fluor used modular execution while building Dow’s ethylene production facility in Freeport, Texas
Fluor
Guiding the Way to Modular Automation
The User Association of Automation Technology in the Process Industries, (NAMUR; Leverkusen, Germany; www.namur.net) is an international association of user companies with interests concerning automation technology. With over 140 member companies, the organization conducts dialogue with manufacturers, creates working groups in the areas of measurement, controls, automation, communications, process management and electrical engineering and publishes recommendations.
The Automation of Modular Plants working group is involved in national and international standardization. As such, NAMUR published recommendation NE 148, “Automation Requirements Relating to Modularization of Process Plants.”
The recommendation aims to reduce time between idea and product launch via process engineering new designs, using modular components. According to the recommendation, “plug-and-produce” plant components increase flexibility and shorten project duration.
The group states, “During the last decades, a lot of standards for traditionally designed plants were created. Within the process industry, modular plant design and its standardization have just started. The introduction of modular-composed process plants must not be slowed down by insufficient automation technology. Instead, automation is supposed to be a driver and innovator. Furthermore, many of the required developments can become a competitive advantage in traditional installation. NE 148 provides a respective frame for automation in modular designed plants.”
The main concepts included in NE 148 are decentralized automation, with individual modules being fully automated, as well as flexible integration into higher-level, plant-wide control systems and vendor-independent integration of modules.