Interphex 2020, originally scheduled for April 28–30, has been postponed to July 15–17. Taking place at the Javits Center in New York City, the biopharmaceuticals-focused event offers a full technical conference with dedicated session tracks covering compliance, inspection, automation and much more; and an exhibit hall featuring over 600 exhibitors, many of whom are debuting new equipment and technologies. For 2020, Interphex is co-locating with Chemspec USA, a new event focused on fine, specialty and custom chemicals for use in several market verticals, including pharmaceuticals, biologics, agrochemicals and biocatalysts. After its debut in 2019, Interphex will bring back the Innophex space within its show floor. Innophex will highlight disruptive technologies, including gene therapy, cell processing and more. Furthermore, a new Exhibitor Spotlight Zone will welcome Interphex’s newest exhibitors with special highlights. This Show Preview covers a small selection of the products and services that will be on display at Interphex 2020.
Use these robots in processes
with stringent decontamination
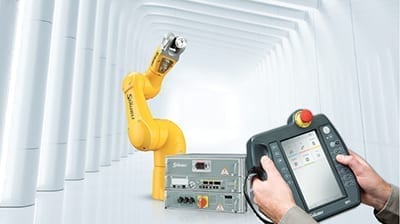
Stäubli North America
The Stericlean range of fully encapsulated robots (photo) are compatible with decontamination processes using vaporized and liquid hydrogen peroxide, at concentrations up to 35% H 2 O 2. Designed with cleanroom operation in mind, the robots feature special seals and surface treatments, as well as a proprietary food-grade lubrication oil to safely lubricate each axis. Theses axes are put in motion by this company’s proprietary JCS drive technology on all models, which facilitates high-speed motion and high repeatability for ultra-short cycle times. The special seals and surface treatment, combined with the ability to pass all connections through the base and inside the arm, enable for shorter decontamination cycles in controlled or aseptic environments, as well as laboratory integration of all four- and six-axis Stericlean models. Booth 2159 — Stäubli North America, Duncan, S.C.
These sensors feature a
standardized adapter system
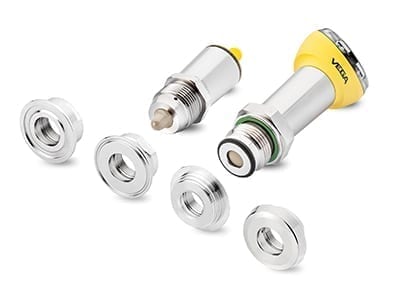
VEGA Americas
This company has recently launched its line of VegaBar pressure sensors and VegaPoint point-level switches. The compact instrument series is tailored for applications requiring high levels of quality control and strict hygiene. The standardized, hygienic adapter system and process fittings (photo) provide the flexibility needed to keep installation efforts and parts inventory to a minimum. Also, sensor setup is simplified with secure Bluetooth connectivity. All VegaBar and VegaPoint sensors can be configured using a smartphone or tablet. The new sensors also feature universal communication. Standard IO-Link protocol offers intelligent data transfer and simple integration into any system. Booth 3847 — VEGA Americas, Inc., Cincinnati, Ohio
Advanced dry-granulation
system for reliable containment
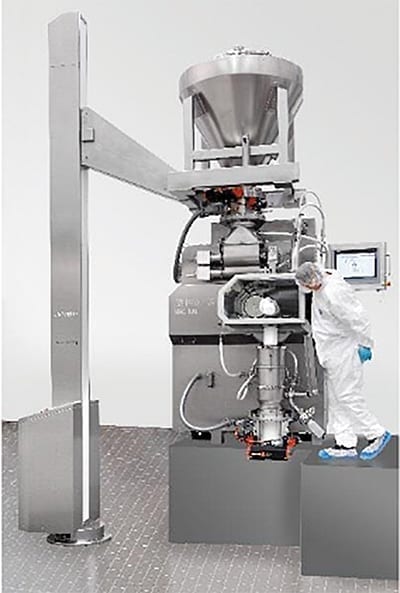
L.B. Bohle Maschinen + Verfahren
The BRC Series of dry granulators now includes the new BRC 100 Containment model (photo). Along with a standard mechanical drive, which eliminates the need for hydraulics, this new model is equipped with fast controls that enable fully automated operation. The unit includes a glovebox with security prompts and dedicated containment ports for sample collection, as well as containment ports underneath the sieve unit for the removal of granules. An integrated insulator unit features corresponding vacuum monitoring, and also provides convenient access, since there is no complete insulator installed around the entire compactor. Booth 2954 — L.B. Bohle Maschinen + Verfahren GmbH, Ennigerloh, Germany
Hygienic dosing for
two-component systems
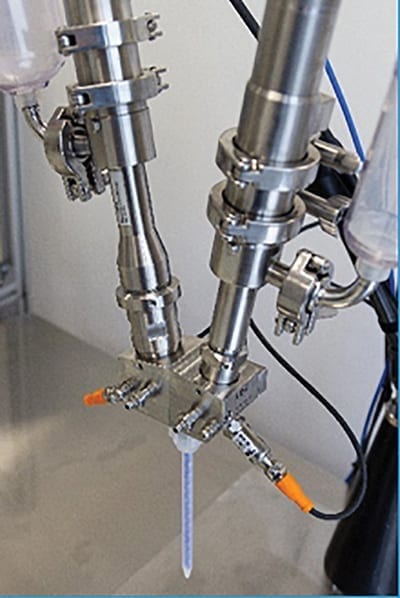
ViscoTec America
The new ViscoDUO-VM HD dosing system (photo) is designed to process two-component fluids and pastes in hygienic processes. The new dosing system offers continuous mixing and dosing of two low- to high-viscosity materials with the same or different viscosities and guarantees precise, repeatable and process-safe mixing in a validated process. The modular design of the ViscoDUO-VM HD features four different sizes on both sides, which allows it to be used in a wide range of applications. Flowrates from 0.5 to greater than 1,000 mL/min can be implemented. Thanks to the built-in endless piston principle, dosing is completely pulsation-free. All components in contact with the product are made of stainless steel, and can be issued with a batch certificate if required. Booth 3742 — ViscoTec America, Inc., Kennesaw, Ga.
www.viscotec-america.com
This connection system offers
full containment during docking
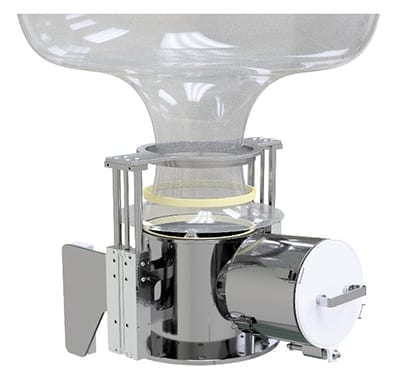
Dec Group
The SafeDock system (photo) enables full product containment in toxic or sterile processes while making docking operations faster and simpler. The fully sealed, pressure-tight system consists of a single dead-zone-free docking tube with an automated cover to close the system. A side port featuring a continuous liner system is used for the removal of the inliner. The bag spout is sealed by a flexible single-use ring, which can be easily removed with the remaining liner in a closed manner through the side port. This high safety system guarantees optimal sealing at all times without external energy sources. Clean-in-place (CIP) tasks are made more efficient with the optional CIP cover. The system is solvent-resistant, and various coatings options are available. Booth 3161 — Dec Group, Ecublens, Switzerland
Loading and unloading are
streamlined with this new system
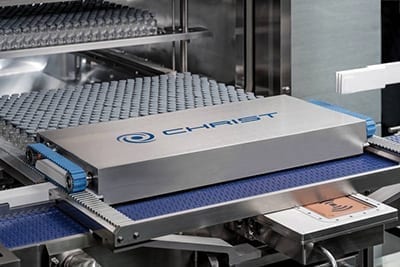
Martin Christ Gefriertrocknungsanlagen
The patent-pending LyoShuttle system (photo) offers automated loading and unloading of freeze dryers in a robust unit. Cleaning and disinfection of the complete system are simplified because the system has very few moving parts. The freeze dryer employs a loading robot that uses timing belts to move horizontally on a set of rails mounted at a constant loading level. Thanks to its flexible and space-saving construction, the LyoShuttle is suitable for production freeze dryers in pharmaceutical manufacturing, including those under insulated conditions. The LyoShuttle system is also designed for integration into an isolator environment. Booth 3711 — Martin Christ Gefriertrocknungsanlagen GmbH, Osterode, Germany
A semi-automatic inspection
machine for liquid or dry products
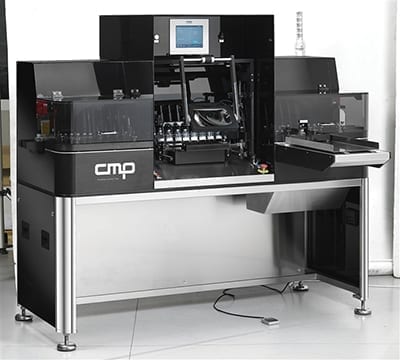
Marchesini Group
The CMP PHAR.MA SV (photo) is a semi-automatic machine for the inspection of liquid, lyophilized or powder products in ampoules, vials and cartridges or pre-filled syringes. The containers are automatically conveyed from the machine to the inspection station, where the operator, looking at the containers, decides whether to accept or reject them. It is equipped with brushless motors for fast rotation (before inspection) and slow rotation (during inspection) to guarantee complete and efficient product control. The machine can handle up to 100 pieces per minute, with a range of diameters from 8 to 78 mm. The machine is designed to comply with current GMP regulations, and its software is in compliance with 21 CFR Part 11. Booth 3125 — Marchesini Group, West Caldwell, N.J.
New servo motors expand these
pumps’ operating range
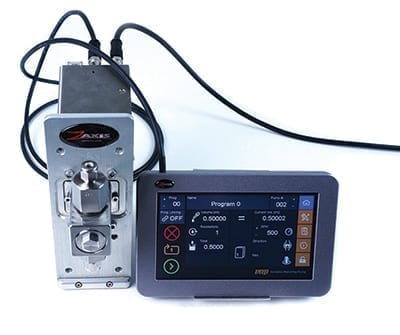
Zaxis
This company now offers servo motor technology for its eVmp precision metering and dispensing pump (photo). The integration of this technology allows the pump to attain higher production speeds and manage fluids with much higher viscosity than was previously possible. The patented eVmP pump combines precision ceramic-pump components and an electronically controlled linear stepper actuator to make ultra-fine adjustments to angle position, thereby changing the volume of metered liquid. This allows the eVmP pump to provide dynamic fluid displacement to overcome variations in viscosity and surface tension. With nearly four times the torque of a traditional stepper motor, the eVmP servo drive can handle flowrates near 2,000 mL/min. Booth 1957 — Zaxis, Inc., Salt Lake City, Utah