With hydrogen’s evolution into an alternative fuel requiring precise production and storage, selecting the right valves has never been more important
Hydrogen shows great promise in the search for alternative fuels. Handling hydrogen safely and reliably, from generation to end use, is the key to reaching its fullest potential as a zero-emission fuel source in a wide variety of applications.
As hydrogen as a fuel source gains traction, the industry must build systems that can produce and store it properly, including leak-tight systems constructed from the highest-quality materials (Figure 1). Only then can the system be counted on to last for years or even decades of safe operation. Choosing the right system components — from valves to fittings to tubing — is paramount, because some materials cannot withstand the particular stressors involved in hydrogen distribution systems. And when the materials are not right for an application, safety may be compromised.
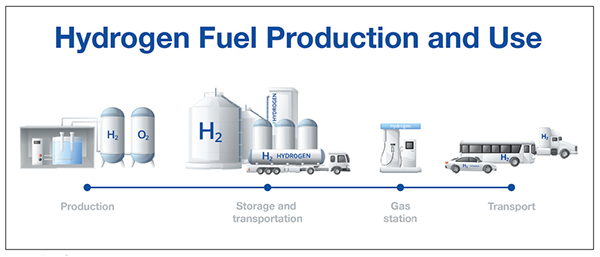
FIGURE 1. Components used in hydrogen service must deliver long-term leak-tight performance from production operations to storage and transportation applications
Hydrogen-specific challenges
Hydrogen molecules are challenging to contain because they are so small and volatile. Each connection point within a hydrogen system cannot leak, because even the smallest leaks pose safety risks to end users. This would be of particular concern, for example, when refueling vehicles. Any system leak is also wasteful.
Hydrogen molecules (shown as H2, blue, in Figure 2) can dissociate to atomic hydrogen (shown as H, red, in Figure 2) and penetrate a metal. Hydrogen atoms accumulate at stress concentrations, such as at the tips of cracks or along microstructural features like grain boundaries, inclusions or precipitates. In certain cases, atomic hydrogen can reform as diatomic hydrogen.
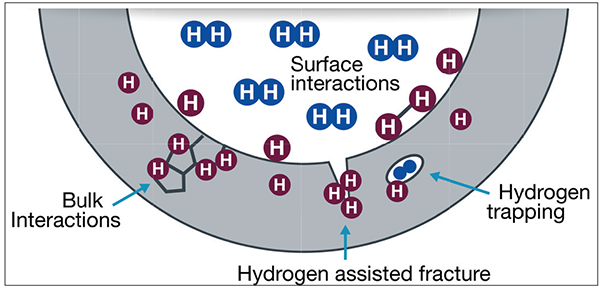
FIGURE 2. When hydrogen atoms embed themselves in system components, it can lead to fractures and fatigue in the components, which could produce premature failures
One of the biggest problems posed by tiny hydrogen molecules is their ability to diffuse into some lower-quality stainless steels, causing a phenomenon known as hydrogen embrittlement. This characteristic can cause components to weaken over time as cracks occur and lead to system failure (see the “How to Avoid Hydrogen Embrittlement” sidebar).
Choosing high-performance valves
Even under ideal conditions, hydrogen valves undergo challenges to their integrity and performance. As system designers decide which valves are most appropriate for their application, they must consider the following parameters:
• Pressures. To achieve the desired density, hydrogen gas must be stored at 350–700 bars for various applications, including plant operations and on-vehicle systems.
• Stress and vibration. Any operational stresses and vibrations a hydrogen system encounters have the potential to cause fitting connections to work themselves loose and cause leaks. Hydrogen fuel systems must be able to withstand those stresses and remain tightened and leak-free.
• Safety. The use of hydrogen carries numerous potential risks. Systems must be designed to mitigate threats related to gas leakage, temperature increases, and hydrogen embrittlement. In addition, the average consumer must be able to safely operate a refueling station.
• Maintenance. It should also be easy to remake leak-tight joints when they need to be serviced for any system, including at the production, storage, transportation and usage level.
These four performance parameters cannot be sacrificed. Each selected valve should provide leak-tight performance at connection, shutoff and regulation points. System designers should then specify valves with the particular challenges and necessary operating conditions of hydrogen applications top of mind.
Those valves may include any of the following types:
Hydrogen ball valves. Hydrogen systems often contain ball valves, which start and stop gas flows from one direction to the next (Figure 3). Proper hydrogen ball valves should include wear-resistant stem-seal designs. For example, it may make sense to specify a trunnion-style ball valve with a direct-load design, which provides leak-tight performance each time it is activated and shut off.
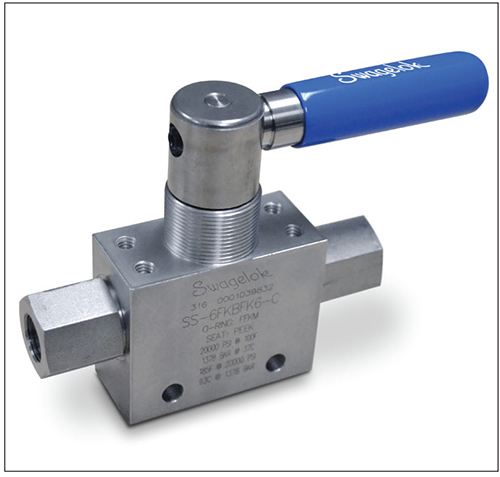
FIGURE 3. Ball valves for hydrogen applications should have highly wear-resistant stem seals for safety
Another option is a bottom-loaded stem design, which can be safer than other valve designs, because such valves are less likely to blow out their stems. Hydrogen ball valves may also offer two- or three-way functionality, different mounting options, and a range of flow coefficients to meet varying system needs. Regardless of the specific valve chosen, always look for good compatibility with fittings that are designed specifically for hydrogen applications. A qualified valve supplier can help guide your selection.
Hydrogen needle valves. When fluid flows require fine adjustments, needle valves are often the answer (Figure 4). However, other factors influence whether needle valves are right for specific hydrogen applications. First, they are often made completely out of metal, meaning it takes significant force to open and close them. The amount of force necessary might eventually deform the needle and seat, rendering it incapable of operating properly and presenting a potential safety issue. Additionally, large air actuators are typically used to open and close the valves, which can take up to two minutes to complete.
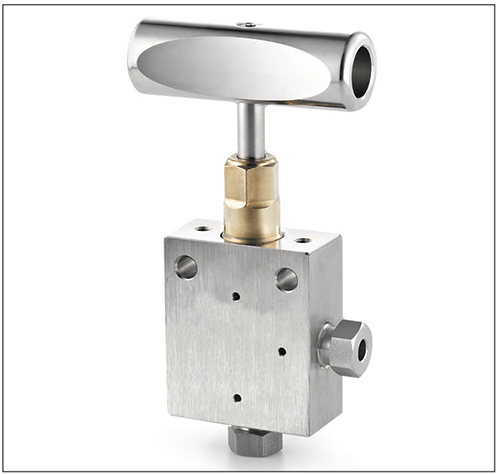
FIGURE 4. Hydrogen needle valves should be made from high-quality 316 stainless steel
Given the above factors, it is evident that hydrogen needle valves must be made from the strongest possible steel. High-quality 316 stainless steel, for example, resists deformation over time and can withstand the pressures exerted on valves in hydrogen applications (usually 350–700 bars). The composition of that steel is especially important so it can better resist the challenges related to hydrogen embrittlement (see the sidebar for details).
Not all needle valves will have the required pressure rating to handle common hydrogen applications, so when selecting, be sure to choose valves that are qualified for elevated working pressures. In addition, ensure the chosen needle valves are compatible with any other hydrogen-qualified components used in the system.
Hydrogen check valves. Finally, check valves are essential to properly functioning hydrogen compressors in refueling systems (Figure 5). For example, most check valves use strain-hardened springs, which can be unusually susceptible to hydrogen embrittlement. In contrast, using springs made from high-quality 316 stainless steel reduces the chances of embrittlement weakening the springs. Another challenge is the often severe temperature and pressure changes common to hydrogen applications. These severe changes can damage the elastomer seals in valves. Ideally, most hydrogen compressors would use ball check valves over other nonspecific ones.
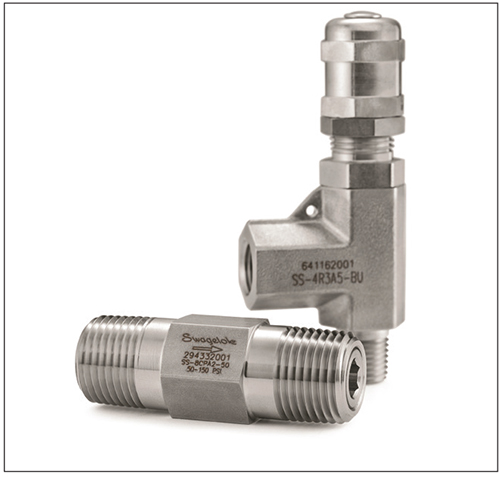
FIGURE 5. Ball check valves are used to control excess backflow in hydrogen compressors for refueling systems
Just like with the other two types of valves, material integrity and compatibility with other hydrogen components are important for check valves.
How fittings fit
Selecting the most appropriate valve types, materials and configurations for hydrogen applications is not the only consideration when building a well-functioning hydrogen production and storage system. Installing the right fittings to connect those valves is just as important.
Since hydrogen is such a volatile gas, it is crucial to demand uncompromising fitting performance. Each connection in a hydrogen production and storage system is a potential leak point, and ensuring the fittings work effectively with the valves is essential. Although traditional cone and thread fittings are typically used for these applications, other options exist that may be more appropriate for hydrogen systems.
To function effectively in hydrogen systems, fittings must have the following characteristics of seal tightness, grip strength and simple installation:
Seal tightness. The most effective fittings for hydrogen containment have two long lines of contact across longer sealing surfaces. The contact surfaces should be at an angle to provide optimized stress levels, which will allow the seal to stay tight under most operating conditions. Certain styles of two-ferrule tube fittings can deliver this kind of seal integrity.
Grip strength. A colleted mechanical grip using two ferrules is ideal for hydrogen fittings to create a robust grip (Figure 6). A hardened front ferrule can enable the fitting to physically bite into the tubing, creating a very high pressure rating. Meanwhile, a unique back ferrule design allows for a slight amount of movement in the fitting (called “spring back”) while maintaining grip and force.
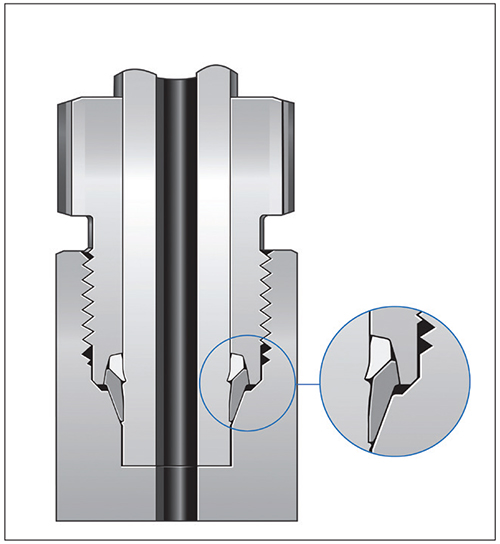
FIGURE 6. The two ferrules in this fitting design provide a hinging and colleting action that securely grips the tube. The hardened front ferrule (dark gray) enables the fitting to physically bite into the tubing. The back ferrule (light gray) allows for a slight amount of movement in the fitting while maintaining grip and force
Simple installation. Some available mechanical grip fittings are designed with preassembled cartridges (Figure 7). This enables installers to use common tools and requires minimal training to achieve rapid, error-proof assembly. When compared to traditional cone and thread fittings, which have traditionally been used in hydrogen production and storage systems, preassembled cartridges are much easier to install (Figure 8).
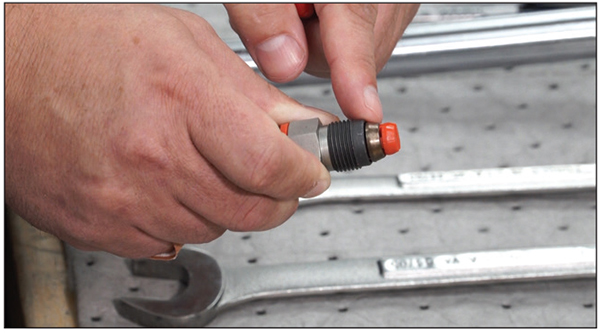
FIGURE 7. Fittings with preassembled cartridges can reduce installation times by 80%
While there are a variety of compression tube fittings and other styles that may be applicable to hydrogen systems, very few are designed to satisfy the many unique performance demands hydrogen applications require.
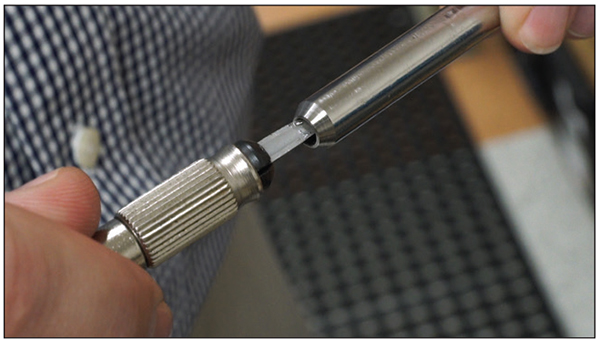
FIGURE 8. Traditional cone-and-thread fittings require significant machining and are not designed for ease of installation
Hydrogen service in action
Ball valves, needle valves, and fittings rated for hydrogen service are what helps Denmark’s HySynergy project tick. The 20-megawatt Power-to-X (PtX) facility built by Everfuel to test the viability of large-scale hydrogen dispensing and storage recently completed its first phase (Figure 9).
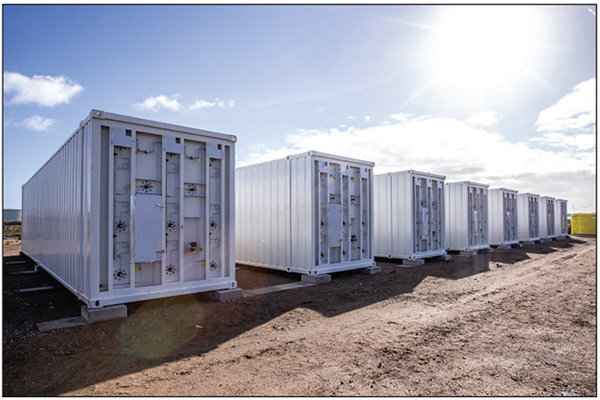
FIGURE 9. Danish company Everfuel uses an array of fittings and valves rated for hydrogen services to operate electrolyzers as part of the company’s pioneering HySynergy PtX plant
The facility is hoping to bring the promise of green hydrogen to fruition. Upon completion of Phase II of the project, Denmark is poised to reduce carbon emissions equivalent to 11% of what comes from the Danish land-based transport sector. Upon completion of Phase III, which is targeted for 2030, the project will provide further carbon footprint reductions, contributing significantly to the country’s 70% carbon dioxide reduction target.
Top-rated components make up the fluid systems that compress and contain highly combustible hydrogen in a leak-tight environment at the HySynergy PtX plant. These specialty fittings and ball and needle valves feature a higher nickel content to help prevent hydrogen embrittlement (Figure 10). Their leak-tight performance is a testament to the careful attention to material properties in their makeup, as well as their adherence to the four required performance parameters for handling the pressures, stress and vibration found in hydrogen service, while maintaining safety and enabling simplified maintenance.
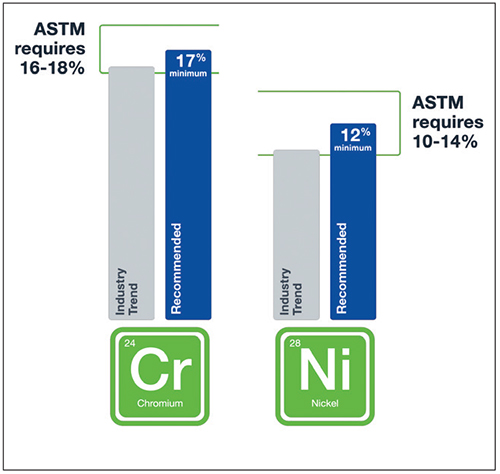
FIGURE 10. Stainless steels with higher nickel content provide much more protection from hydrogen embrittlement than lower-nickel stainless steels
Why compatibility matters
For all the valves used in hydrogen applications, compatibility with other components is key. It is important to ensure all components are designed specifically for hydrogen use so they work together in harmony to keep everyone safe throughout the process.
The long-term viability of hydrogen as an alternative to fossil fuels will depend on safe, reliable and durable production and storage systems. Selecting and specifying the right components for critical systems can help achieve these goals. Using the proper components, including well-designed, hydrogen-specific valves, will help ensure hydrogen’s leading place in the alternative fuel market. ■
Edited by Dorothy Lozowski
Acknowledgement
All figures are reproduced courtesy of Swagelok Company.
Author
Chuck Hayes is a 30-year veteran of Swagelok Company (Solon, Ohio, USA; www.swagelok.com). He has spent the last 25 years developing a wide range of fluid system products and the past 20 years focused exclusively on fitting technology for alternative fuel applications. Today, he concentrates most of his time on the development of hydrogen mobility solutions for both refueling infrastructure and on-vehicle applications. Chuck currently holds 7 patents in the U.S. and numerous patents internationally.