Increased reliability, chemical compatibility and containment of sealing solutions are priorities for chemical processors
Seals and gaskets may seem like an afterthought in the grand scheme of chemical processing equipment, but if you’ve ever been faced with unexpected — and costly — downtime due to a seal or gasket failure, you know these products are as crucial to the process as their larger-scale counterparts. As the chemical process industries (CPI) continue to demand better chemical, pressure and temperature compatibility, tighter emission control and higher reliability from their seals and gaskets, new solutions are being explored.
“Everyone believes a seal is a seal is a seal and it is not going to be a problem until it becomes a problem,” says Derek Duncan, technical director with American High Performance Seals, Inc. (Oakdale, Pa.; www.ahpseals.com). This, he says, is especially true in the CPI where chemical compatibility, special sanitary needs and high pressures and temperatures are issues and high value processes and products demand reliable sealing solutions. “These concerns often dictate the use of high-performance products.”
Compatibility concerns
While it is not difficult to select a compatible sealing material for a single chemical, one of the biggest areas of concern in the CPI, says Duncan, is chemical compatibility when mixtures are involved. “We often have processors come to us with a list of five or six different chemicals they run and want to know what seal material is compatible with those chemicals,” he explains. “What they don’t realize is, that once in process, the seals aren’t seeing those chemicals individually, but rather as a combination and the seal material may not be compatible with the results of the process,” he says (Figure 1).
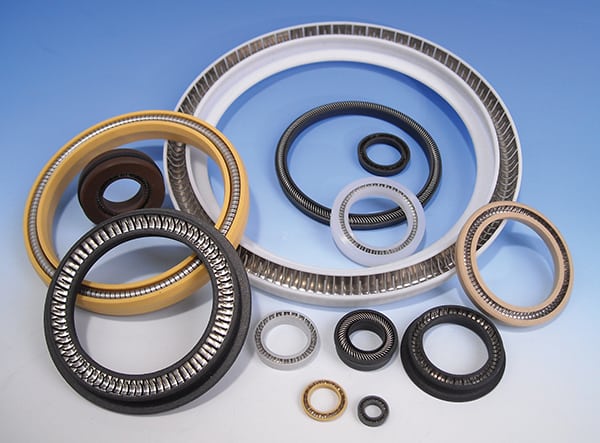
Figure 1. When it comes to compatibility, it is essential that the sealing material is compatible not just with individual chemicals, but with the product that results from mixing those chemicals.
American High Performance Seals
For example, “I have seals that are compatible with water and seals that are compatible with glycol, but those same seals would not be compatible with a water/glycol combination.” In many cases, he says, these situations can be resolved by running a compatibility test. “It is possible that a processor could get three to four times the life for half the cost if they were to work with a seal manufacturer with compatibility test capabilities,” says Duncan.
How the equipment will be cleaned can also have an impact on seal design. “It is not uncommon to discover that the best seal design and material for the application are totally unsuitable for the intended cleaning method,” says Duncan. “Seals are designed for the chemicals they are pumping, so if there is a clean-in-place, steam-in-place or autoclaving cleaning service, that needs to be addressed during seal design and selection. Often these cleaning processes cook the seal, drastically reducing reliability of the seal, so it’s a very important detail to mention upfront.”
Also in sanitary environments where U.S. Food and Drug Administration (FDA; Silver Spring, Md.; www.fda.gov) seals are needed it’s necessary to look beyond the FDA-approved seal materials and consider the design, as well, says Duncan. “Processors often ask for an FDA-approved seal material, but this necessitates more than a standard seal design in an FDA-compliant material. Many FDA materials have fitment issues, as they sometimes require an open housing that will either be damaged or impossible to fit in a closed gland. The direction of insertion of the seal into the housing and shaft through the seal can also present challenges. For this reason, it is recommended that general assembly drawings be presented to the seal manufacturer as early as possible to overcome these issues.”
In addition, FDA seals for the food industry use many housing, piston and shaft materials that present challenges to seal design. “For example,” says Duncan, “Counter surface materials can drastically reduce the possible seal materials available to the designer. An aluminum housing necessitates a different material than a stainless-steel housing does.”
High temperatures & pressures
In the CPI, it is not uncommon to increase temperatures and pressures in an effort to boost throughput. However, this can have an impact on seals and gaskets. “Many processors are finding that seal materials are the limiting technology preventing them from increasing temperatures,” says Colin Macqueen, director, R&D, Trelleborg Sealing Solutions Americas (Fort Wayne, Ind.; www.trelleborg.com). “For increasing pressures it is important to work with a seal supplier who can offer a full portfolio of products and applications expertise to avoid a sub-optimal solution from a limited offering.”
He continues: “If a custom sealing solution is required, it is important for the equipment manufacturer to understand the specific application requirements, which include not only temperatures and pressures, but many other factors including dimensional tolerances. Withstanding high pressure is often a matter of tolerancing so that the maximum gap to be sealed can be well understood at the design stage.”
Macqueen points to Trelleborg’s Isolast perfluorelastomer (FFKM) as a development intended to provide better choices for chemical compatibility, mechanical properties and temperature resistance. He says, “Isolast J9538 offers the mechanical properties to optimize production, the thermal and chemical stability to resist clean-in-place and sterilize-in-place and water-for-injection regimes, and is compliant with or is certified to FDA, 3-A and USP [U.S. Pharmacopeia] standards. This profile of attributes improves performance in applications such as mix-proof valves, mixers, pump and centrifuges for pharmaceutical, healthcare and medical industries.”
In addition, Isolast J9570 offers low temperature performance down to –40°C while maintaining chemical resistance, making it suitable for sub-zero environments, such as couplings when transporting aggressive chemicals and downstream petrochemical and refinery equipment. And Isolast J9567 (Figure 2) is a technically advanced multi-purpose FFKM (a perfluoroelastomer) that offers broad chemical and temperature resistance to provide cost savings to a variety of applications within downstream hydrocarbon refining.
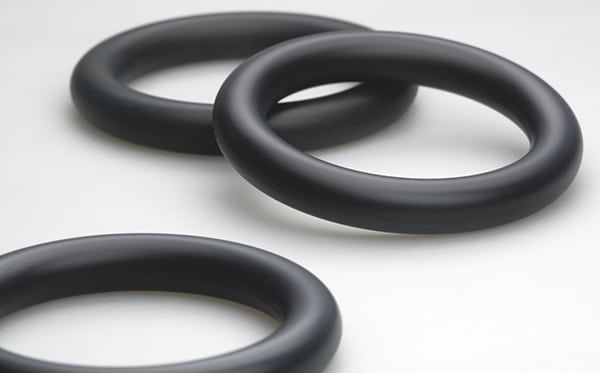
Figure 2. Isolast J9567 is a technically advanced multi-purpose FFKM that offers broad chemical and temperature resistance to provide cost savings to a variety of applications within downstream hydrocarbon refining
Trelleborg
Thermal cycling is often a problem in high temperature operations, as well, notes Ron Frisard, field product manager, stationary sealing, with A.W. Chesterton (Groveland, Mass.; www.chesterton.com). To help compensate for this, the company offers its valve cartridge live-loading technology for difficult valves at high temperatures that are subject to a lot of thermal cycling, such as those in nuclear and fossil power, petroleum refining, petrochemical and chemical industries. “The live loading technology compensates for a variety of system conditions and optimizes reliable valve sealing by maintaining a consistent load on the packing gland,” he says. “You can minimize valve-induced process fluctuation and reduce associated leakage due to system disturbances, such as thermal expansion and contraction, improving equipment uptime.”
Higher temperatures and pressures also drive the need for metal seals, says Ryan McCall, product manager for high performance metal seals with Technetics (Columbia, S.C.; www.technetics.com). One of the company’s main products, the Helicoflex (Figure 3), is a spring-energized metal seal with metal cladding on the outside. “Its materials and design make it very suitable for high temperatures and pressures in the chemical industry because the spring-energized core provides elasticity to help maintain a specific pressure, while the outer cladding is compatible with many chemistries,” says McCall.
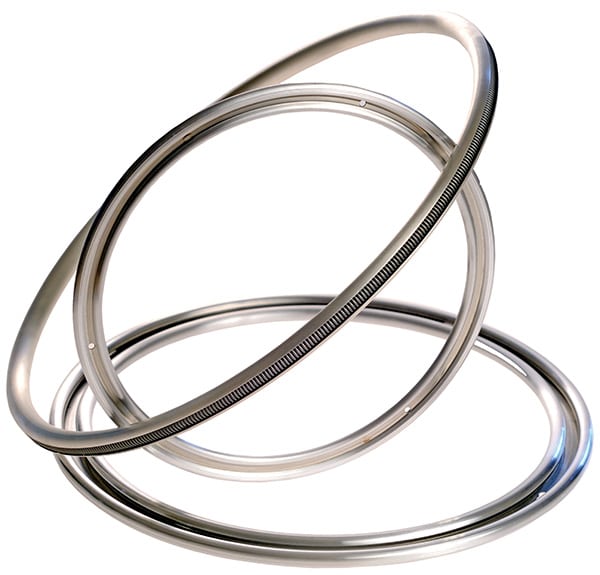
Figure 3. The Helicoflex is a spring-energized metal seal with metal cladding on the outside. Its materials and design make it very suitable for high temperatures and pressures in the chemical industry
Technetics
The sealing principle of these seals is based upon the plastic deformation of a jacket of greater ductility than the flange materials. This occurs between the sealing face of a flange and an elastic core composed of a close-wound helical spring. The spring is selected to have a specific compression resistance. During compression, the resulting specific pressure forces the jacket to yield and fill the flange imperfections while ensuring positive contact with the flange sealing faces. Each coil of the helical spring acts independently and allows the seal to conform to surface irregularities on the flange surface.
Controlling leaks
Metal seals, says Jonathan Kweder, product manager, aerospace, with Technetics, are also suitable for controlling emissions. “A metal seal that is sealing properly will allow you to start reaching very low leak rates,” he says. In addition, metal seals are typically not as permeable as other seals, so the gas or fluid will not be able to permeate through the seal itself, which means outgassing is not a concern.
Emissions are a particular problem for valves in the chemical industry, so Chesterton 1726 Low E Packing (Figure 4) was designed to meet new reduced emission levels without live loading. The packing is constructed with a combination of polytetrafluoroethylene (PTFE) surrounding a carbon core in a true double-braided formation. The PTFE jacket provides chemical resistance and lower friction while the specially formulated carbon core provides sealing capability in harsh, corrosive environments. The result is a non-hardening, flexible packing that is strong, yet extrusion resistant for a secure and reliable seal for emissions service.
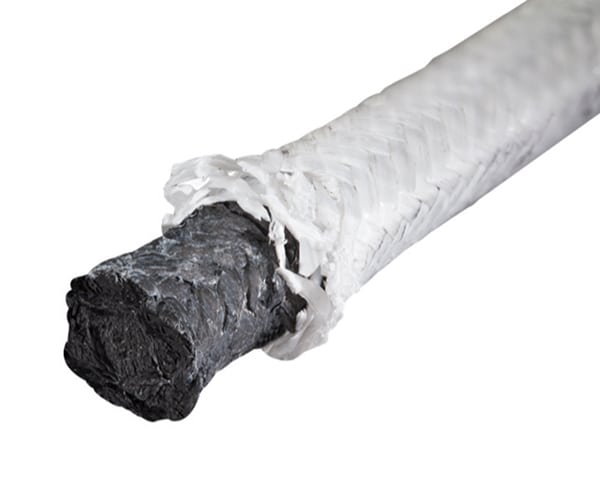
Figure 4. Chesterton 1726 Low E Packing was designed to meet new reduced emission levels without live loading. The packing is constructed with a combination of PTFE surrounding a carbon core in a true double-braided formation
A.W. Chesterton
In marine vessel applications, leakage of environmentally accepted lubricants (EALs) used to lubricate the propeller shaft is also a problem because oil-based EALs need to be compatible with the sealing materials to ensure that leakage is controlled, says Terry McGowan, president and CEO of Thordon Bearings (Burlington, Ont., Canada; www.thordonbearings.com). “Oil-based EALs may impact the seal wear life, meaning increased maintenance costs, as these lubricants are three to five times more expensive than mineral oils, and they are still considered a pollutant so leaks must be reported and cleaned up, so we needed a solution,” he says. So, his company developed a system that uses water lubrication. The Thordon SeaThigor (Figure 5) is a mechanical face seal for water-lubricated propeller shafts that has been manufactured for long wear life and reduced maintenance costs, has no visible leakage and offers metal compression springs used to maintain constant face closing forces. The seal is designed so that the pressurized water is placed on the outside of the sealing rings, using water pressure to keep the faces closed. This is particularly important for deep-water operation when there are pressure fluctuations that can open the faces of traditional seals, causing leaks. The SeaThigor uses a balanced design with an optimal balance ratio that enhances operation stability when subjected to fluctuation of water pressure.
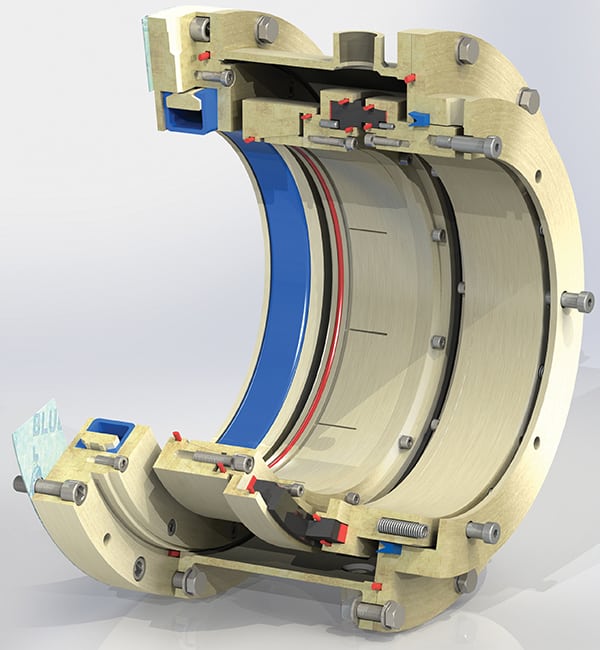
Figure 5. The Thordon SeaThigor is a mechanical face seal for water-lubricated propeller shafts that has been manufactured for long wear life and low maintenance costs, has no visible leakage and offers metal compression springs used to maintain constant face closing forces
Thordon SeaThigor
Improving reliability
One of the biggest issues associated with reliability in mechanical sealing systems is the maintenance aspect, so seal manufacturers are looking to help increase reliability via improved designs. “What we are seeing is processors working with smaller maintenance teams that are typically expected to complete the same amount of work with less manpower,” says Steven Bullen, global product line manager, mechanical seals, with A.W. Chesterton. “So, we’ve been working to simplify the mechanical seals and sealing systems and develop solutions that are intrinsically reliable. We engineer the seal to perform in applications without the need for external support, which provides two benefits: It lowers the initial acquisition and maintenance costs because users are only looking after the seal, not the support system and, at the same time, it removes the risk of operator or maintenance error during installation or repair.”
He continues: “If someone adjusts a sealing system in the wrong way, it can result in failure, so by eliminating the need for a piece of external equipment, we can increase reliability and reduce the operating cost of equipment while increasing the profitability of our customers.”
Some examples of their user-friendly mechanical seal designs include the Chesterton 442 split seal and 442C cartridge split seal. The 442 split seal is designed for equipment that is difficult and time consuming to disassemble, such as large pumps, vertical pumps and horizontal split case pumps. It was designed with the installer in mind so the ball-and-socket O-rings provide a quick and easy leak-free seal without the use of adhesives, the captive screws cannot fall out, making installation straightforward and reliable, and the compact design allows for easy installation and a fit advantage on most equipment. The 442C cartridge split seal (Figure 6) combines performance with ease of installation. The split seal technology addresses the inherent limitations found in conventional cartridge split seal designs by offering easy installation and replacement without the need for teardowns.
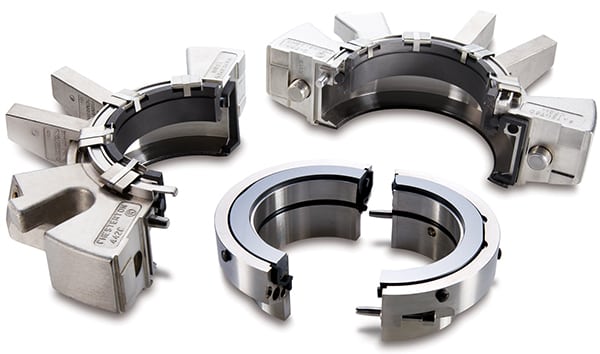
Figure 6. The 442C cartridge split seal addresses the inherent limitations found in conventional cartridge split seal designs by offering easy installation and replacement without the need for teardowns
A.W. Chesterton
“This line of split seals was designed for larger equipment and gives the advantages of putting on a replacement seal without having to take the equipment out of service, so it can be done while the piping and motor are still connected,” says Nicholas Sirois, global product manager, mechanical seals, with A.W. Chesterton. “It is truly a replace-in-place solution.”