In petrochemical, oil and gas, and refinery settings, safety is paramount. Many chemicals, fluids and gases used in the energy industry are extremely toxic or flammable and contact with them can result in burns, incapacitation or even death. In normal operating conditions, these dangerous fluids and gases are safely contained within valves, pipes and other components, but fires pose a serious risk. If a valve containing toxic or flammable fluids leaks during a fire, it contributes to the intensity of the flames creating increased dangers for both humans and the environment.
A valve that can temporarily survive a fire scenario gives personnel time to escape and find safety. These valves also help protect the environment by giving firefighters time to extinguish the flames before leaky fire-ravaged equipment causes pollution.
“Fire safe” is the term used to describe valves that survive temperature extremes from a simulated blaze. They can be choke, ball, gate or other designs and typically operate with a valve stem that rotates, reciprocates or is a quarter-turn type.
The industry challenge
When designing fire safe valves, manufacturers must consider the material used for the sealing elements. Almost all petrochemical valves contain dynamic polymeric seals that must survive 30 minutes at 1,400°F (761°C). Flexible graphite can withstand temperatures above 1,000°F (538°C), so it is typically used as a secondary sealing element. However, flexible graphite is not a resilient seal material, needs energization and requires extra space in the sealing gland, which adds cost and weight to the valve body.
Designing a dynamic polymer-based seal that meets these demanding requirements is very difficult. Polymer materials are used to avoid damage to the valve hardware, but even the most capable polymeric seals are only rated to a maximum of 572°F (300°C). The key to creating a more capable fire-safe polymeric seal is incorporating metallic design features. Metal is resistant to high temperatures and can survive a fire. When the polymeric materials are exposed to intense heat and soften, a metal back-up ring prevents them from squeezing out of the sealing area and causing the valve to leak. Once the fire is extinguished, the valve will be unusable and must be replaced, but it will have survived prolonged heat exposure without leakage.
A potential solution
A major oilfield customer approached Trelleborg Sealing Solutions (Trelleborg, Sweden; www.trelleborg.com/en/seals) to develop a valve stem seal that met industry fire-safe requirements. The seal needed to pass a standard API PR2 testing profile and survive a fire test at 1,382°F (750°C) and 7,500 psi (51.7 MPa) for 30 minutes. Trelleborg used an innovative combination of metallic and polymeric components to enable dynamic stem movement while providing high temperature and pressure extrusion resistance. The valve stem seal’s polymeric elements function during normal operation and metallic corner reinforcement rings reduce polymeric extrusion at high temperatures. The seal system also had a compact design, reducing required hardware space resulting in smaller and lighter components. This decreased the valve’s overall weight, providing cost savings.
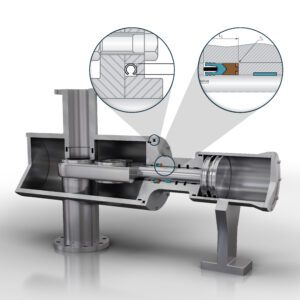
FIGURE 1. The valve stem seal has a combination of metallic and and polymeric components
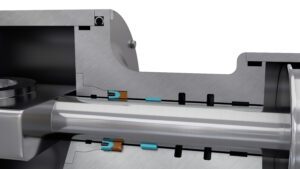
FIGURE 2. The seal provides resistance to both high temperatures and pressure extrusion
During testing, the polymeric sealing material experienced significant extrusion, but not to the point of catastrophic failure. The sealing profiles were still visible, and the resilience of the polymeric elements were a good indication that the seal may have been able to withstand longer flame exposure.
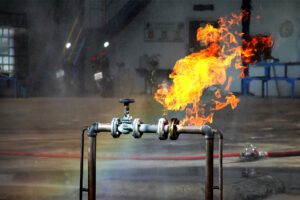
FIGURE 3. There are test standards available to test valves in fire situations
Testing standards
The industry has developed several specifications to test valves in a fire situation. The most common specifications are the following:
- ISO 10497 – For valves with thermoplastic or elastomeric sealing elements, the test media is water at 2 bars. Direct flame is applied at 1,382°F (750°C) for a minimum of 30 minutes. Allowable external leakage during flame test equals 100 mL/min). When the valve cools, it must open and close and must hold pressure for five minutes. Maximum allowable leakage is 200 mL/min.
- API 607 – This standard is similar to ISO 10497, except it is specifically for quarter-turn valves, and pressure is 75 percent of maximum allowable per the nominal pipe size (NPS) valve size.
- API 6FA – This standard is applicable to API 6A and 6D valves with soft thermoplastic or elastomeric sealing elements. The valve is filled with water in the closed position and exposed to fire, resulting in a valve temperature from 1,400–1,800°F (761–980°C) for a minimum of 30 minutes. Leakage through the valve (internally and externally) is then measured. The test pressure is determined by the valve class. After the flame test when the valve has cooled, it is opened under high pressure. Recorded external leakage must be within 200 mL/in./min (8 mL/mm/min).
- BS 6755-2, Appendix A – The British testing standard BS 6755-1 is for all types of valves to identify leakage rates past the seats. This specification does not have a high temperature flame test component. The testing standard BS 6755-2, appendix A is for all types of valves to identify leakage rates when exposed to high-temperature flame. During the flame test, a maximum leakage of 400 ml/in/min or 15.6 ml/mm/min is allowed internally through the valve seat. After testing and cool down, a maximum of 20 ml/in/min or 0.8 ml/mm/min is allowed externally through the stem and bonnet seals.
Author
Eric Bucci is the Global Technical Manager for Energy at Trelleborg Sealing Solutions. As a member of the Trelleborg team for almost 30 years, Eric has held several positions ranging from applications engineer to segment manager for oil & gas. He works to form partnerships with key customers identifying their product and material needs. One of Eric’s main objectives is developing new initiatives that further position Trelleborg as a global leader in engineered sealing systems.