The potential of membrane technology to unlock hybrid and scalable carbon capture, combined with results from early field trials, suggest that advanced membranes will play a crucial role in enabling more widespread adoption of decarbonization strategies
It is a truth universally acknowledged that today’s industrial carbon dioxide sources are in want of a path towards decarbonization. Accounting for approximately 30% of global greenhouse-gas emissions when considering both direct and energy-related sources, the chemical process industries (CPI) are facing mounting pressure to decarbonize. While electrification and renewable energy have made significant strides in other areas, deep industrial decarbonization requires more innovative solutions. Enter carbon capture, utilization and sequestration (CCUS) — a technology platform that has emerged as a crucial component in all pathways toward achieving carbon neutrality by 2050.
However, the implementation of CCUS at scale faces a significant hurdle: the cost and efficiency of carbon capture itself. Today, carbon capture is estimated to represent over half of the overall cost of CCUS, making it the step most ripe for innovation and cost reduction. The key to enabling widespread CCUS adoption lies in developing and deploying high-efficiency, scalable gas-separation technologies that can successfully address the dilute nature of CO2 emissions.
Challenges for carbon capture
In addition to the dilute nature of industrial CO2 emissions, the wide variation in emissions, site-specific constraints and downstream destinations of captured CO2 all present challenges for industrial carbon capture.
Different industrial processes produce fluegas streams with vastly different CO2 concentrations. For example, the CO2 content in steel-production emissions (24%) differs significantly from that in cement manufacturing (16%) or power plants (11%) [ 1]. Additionally, industrial fluegas streams often contain various impurities and toxins, which can impact the effectiveness and longevity of capture technologies (Figure 1).

FIGURE 1. One of the major challenges in industrial carbon capture is the variance in CO2 concentration in fluegas streams, as well as the wide spectrum of impurities that can potentially be present in the exhaust gas
Site-specific constraints, such as available space, utility access and existing infrastructure, can limit the types of capture technologies that can be deployed at a given location. It doesn’t matter how theoretically cost-effective a technology may be if the plant considering it simply doesn’t have the space available to install it, or can’t acquire the utilities necessary to run it.
The intended use or storage method for the captured CO2 also influences the requirements for carbon capture technology. While transport and storage applications for CO2 typically require very high purity (99.8%), many utilization applications do not. Local economic factors, regulatory environments and access to transportation, utilization or storage opportunities all play a role in determining the most suitable downstream destination, and by extension, the most suitable capture solution.
Given this complexity, it is clear that no single technology will be the best across the entire spectrum of applications and CO2 concentrations. Instead, the industrial sector will require a combination of technologies to achieve cost-effective CCUS at scale.
Conventional CCUS strategies
It’s not what we say or think about technologies that defines their place, it’s what they do — and don’t do. Before delving into the potential of advanced membranes, it is worth examining the limitations of existing carbon capture technologies. While existing technologies have an important role to play in industrial decarbonization, they tend to be better suited for either large-scale capture in chemical plants or capture from high-pressure applications (Figure 2), leaving a wide range of applications underserved across many industries, including cement, steel, glass, pulp-and-paper and waste-to-energy, to name a few.
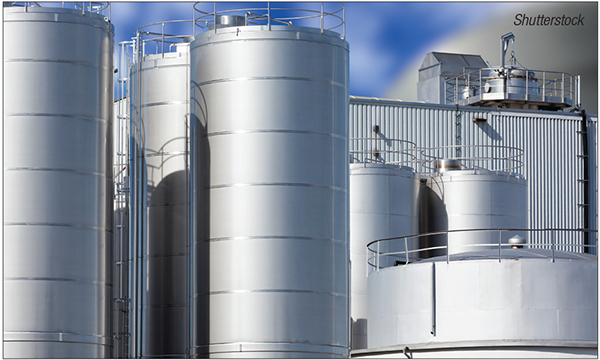
FIGURE 2. Conventional amine-based carbon-capture processes are well-suited for large-scale, established processes, such as those found in chemical plants
Amines — best for large chemical plants. Amine scrubbing is the go-to technology for large-scale carbon capture in chemical plants [2]. In large-scale applications able to handle the energy and chemical requirements, amines work well, can be deployed now, and are low risk. However, there are thousands of industrial applications where amines are not a natural fit. Amine-based systems suffer from high energy requirements (parasitic load) for solvent regeneration, solvent degradation issues, and potential for chemical emissions. They also rely on economies of scale, making them unsuitable for smaller applications. The extensive balance-of-plant equipment essentially requires a chemical plant on-site, access to large amounts of steam, and the technology has limited potential for significant performance improvements due to its maturity.
Traditional membranes — best for high-pressure applications.What about traditional membranes? What role might they play in carbon capture? Traditional membranes, while already used in CO2 processing, have primarily been developed for high-pressure applications. The low-pressure nature of fluegas presents challenges, including high energy costs associated with pressurizing fluegas streams, which can add more than $80 per ton to the cost of capture. Furthermore, solution-diffusion membranes require large membrane surface areas and have limited fouling tolerance, necessitating additional feed conditioning for gas streams with high impurities. The limitations of existing amine and membrane technology have created a gap in the market for a technology that can efficiently and cost-effectively capture CO2 from diverse industrial sources, particularly those with lower pressure streams, low CO2 concentrations, smaller distributed operations, or challenging operating conditions.
New membranes
Facilitated transport is an advanced membrane technology that is emerging as a natural fit for carbon-capture applications. Facilitated transport membranes (FTMs) offer several advantages for carbon-capture applications that allow them to fill the gaps left by conventional technologies. FTMs can effectively separate CO2 from dilute streams at pressures as low as 1.4 bara, significantly reducing energy requirements. Their high selectivity and flux allow for processing large gas flows in a relatively small footprint, resulting in a modular and compact design.
FTMs represent a significant leap forward in membrane technology. Unlike conventional separation technologies, FTMs rely on the chemistry of the membrane itself for energy-efficient separation. They contain embedded carrier molecules that selectively interact with and transport target molecules (in this case, CO2) across the membrane. This selective transport results in high selectivity, as the carrier molecules facilitate the transport of CO2 while impeding the passage of other gases.
Unlike amine-based systems, FTMs do not rely on chemical solvents, eliminating issues related to degradation, emissions and regeneration. Utilizing FTMs as part of a composite membrane typically consisting of a thin, selective layer supported by a porous substrate, allows for high flux rates along with good selectivity. This unique combination of properties allows FTMs to achieve efficient CO2 separation without the need for high pressure or chemical regeneration, making them an attractive option for a wide range of industrial applications.
Modular and scalable technology
Next-generation membrane solutions boast a modular, scalable and flexible design that makes them highly adaptable to the needs of different industrial applications and downstream CO2 destinations. Membranes can easily be integrated into a simple turnkey system that delivers an end-to-end solution for users.
By operating at low pressures without the need for chemical regeneration, advanced membranes present a smaller-footprint, lower-energy and lower-complexity alternative to conventional technologies. Membranes are a totally electrified solution that do not require steam or chemical waste disposal. This simplicity translates to lower capital and operating costs, especially for smaller or distributed applications like kilns, compressor stations, or boilers. Thanks to their compact design and minimal utility requirements, advanced membrane systems can also be more easily integrated into existing industrial facilities that face space and utility constraints.
Membranes can be banked in series or parallel configurations, making them adaptable both to a wide range of CO2 concentrations and operating conditions and also to fluctuations in industrial processes. Robust membrane designs can tolerate various contaminants (including oxygen and water), potentially reducing or eliminating the need for expensive pre-treatment of fluegas that might otherwise be required for applications such as incinerators, steel furnaces, kilns or applications with high concentration of oxides of sulfur and nitrogen (SOx and NOx).
For CO2-mineralization or biologic-utilization applications that do not require extremely high purities, the flexible nature of advanced membrane solutions means they can provide a cost-effective way to achieve the necessary concentration levels without overengineering the solution. Membranes can be configured to deliver 60–85% purities, avoiding unnecessary power or system capital associated with technologies that only deliver higher-than-needed purities.
The modular and flexible nature of membrane systems makes them easy to scale and adapt according to the size and specific capture requirements of different CO2 sources, especially those underserved by incumbent technology.
An adapter for hybrid solutions
While advanced membranes offer significant advantages on their own, they are also poised to unlock hybrid solutions for carbon capture. Hybrid systems combine multiple technologies and play to the strengths of each to achieve optimal performance and cost-effectiveness. Hybrid solutions are especially important for industrial carbon capture because they have the potential not only to deliver more efficient and cost-effective separation when compared to single-technology solutions, but also to address applications where no one technology would meet the desired specifications.
Advanced membranes can help enable hybrid solutions because they can act as a “universal adapter” that provides a simple, modular way of combining technologies. Advanced membranes can take fluegas streams with varying CO2 concentrations and impurities and deliver them at concentrations and purities needed to efficiently feed a second-stage technology.
Hybrid solutions can be used either as a greenfield solution where there is not already carbon capture in place, or as a retrofit to make existing carbon capture more cost-effective and energy-efficient.
One promising greenfield hybrid configuration combines membranes with cryogenic distillation. This combination is particularly effective for applications requiring very high purity CO2 (greater than 99.8%) for transport or storage. The membrane system performs the bulk separation, concentrating the CO2 to an intermediate level before supplying it to the cryogenic unit that further purifies the stream to meet stringent specifications.
In cases where amine systems are already installed or preferred for high-volume applications, membranes can be used to pre-concentrate the fluegas, reducing the size and energy requirements of the amine unit [3].
For applications with lower purity requirements or where pressure-swing adsorption (PSA) is already in use, a membrane pre-concentration step can significantly improve overall system efficiency. Emerging metal-organic framework (MOF) technologies for CO2 capture could benefit from membrane pre-concentration to optimize their performance and reduce overall system costs. Whether you combine them with cryogenics to deliver sequestration-ready CO2 or only pay for the concentration you need for utilization options, membranes can help unlock a low-cost process configuration.
The key to successful hybrid solutions lies in proper integration and optimization. Advanced membrane systems are designed to fit inside plants and close to flue stacks for a hub-and-spoke design that can also be less capital-intensive. This modular design allows for easy integration with existing assets and second-stage technologies, simplifying hybrid projects and accelerating deployment. By leveraging the best operating regimes of each technology, engineers can design systems that maximize energy efficiency and CO2 recovery while minimizing overall costs.
The potential of advanced membrane technology for carbon capture is not just theoretical. Several pilot projects and field tests have demonstrated the capabilities of FTMs in real-world industrial settings, with several relevant highlighted projects listed in Table 1. In all of these cases, the performance of the FTM membranes exceeded expectations set by laboratory testing, underscoring their potential for industrial-scale applications.
Low-risk technology
As demand grows, the industry will need to scale up the production of high-performance membranes, while maintaining quality and reducing costs. Many an entrepreneur’s imagination is very rapid; it jumps from the laboratory to a pilot plant, from pilot to commercialization in a moment. But in the case of advanced membranes, ample evidence suggests low risk on the path to commercialization and scaleup. The industry has extensive experience manufacturing and engineering membrane process solutions, from natural gas sweetening to biogas, hydrogen and kidney dialysis. Manufacturers can produce millions of square meters of membranes annually and have successfully productized membrane processes.
Advanced membrane solutions combine low manufacturing risk with field validation to offer low overall delivery risk. Numerous technology providers and project integrators are already exploring partnerships with membrane solution providers to enable hybrid solution deployments.
As industry searches for a path towards decarbonization, advanced membrane technology is emerging as a promising solution for efficient and cost-effective carbon capture. The unique properties of FTMs make them particularly well-suited to fill the gaps left by conventional capture technologies. Advanced membrane solutions address the challenges of small, distributed, or dirty fluegas streams, offering a flexible, modular and energy-efficient approach to carbon capture.
Moreover, the ability of advanced membranes to act as a “universal adapter” that connects the dots between different novel and conventional capture technologies opens up new possibilities for carbon capture solutions across a wide range of industrial applications. By combining the strengths of membranes with other established and emerging technologies, industrial operators will be able to create integrated hybrid systems that optimize performance and minimize costs according to the needs and constraints of their facilities.
We have only just begun to see what the new frontier of membranes can do, and as more development takes place, expect even more advances to come in the future. ■
References
1. Watson, J. C. and others, Techno-economic process optimization for a range of membrane performances: What provides real value for point-source carbon capture?, Carbon Capture Science & Technology, Vol. 11, June 2024.
2. Jenkins, S., Advancing Industrial Carbon Capture, Chem. Eng., Oct. 2022, pp. 13–18.
3. Yu, M. C. and others, Hybrid CO 2 capture processes consisting of membranes: A technical and techno-economic review, Advanced Membranes, Vol. 3, 2023.
4. Hägg, M. B. and others, Pilot Demonstration – Reporting on CO 2 Capture from a Cement Plant Using Hollow Fiber Process, Energy Procedia, Vol. 114, July 2017.
5. Clevenger, C., DOE invests $12M in novel membrane technology that captures carbon emissions, The Ohio State University College of Engineering press release, January 18, 2024.
Author
Christine Parrish is the vice president of technology solutions at Ardent Process Technologies (15 Reads Way, Suite 100, New Castle, DE 19720; Email:[email protected]). She received her B.S.Ch.E. from the University of Delaware. Parrish began her career in research where she focused on the study of composite membranes for olefin-paraffin gas separations. She currently leads a cross-functional team to translate technical attributes into tangible value propositions and successfully transition products from the laboratory into the field. Outside of her work with Ardent, Parrish sits on the Industrial Advisory Board for the Bioprocessing Separations Consortium and serves as the Past Chair for the Young Professionals Committee for the American Institute of Chemical Engineers (AIChE).