Tie-in opportunities are few and far between. These rules of thumb will help make sure everything and everyone line up in time
A majority of capital projects today are either debottlenecks or revamps that are intended to increase capacity, squeeze out incremental revenues or comply with impending regulations. A unique goal to the planning of these projects is avoiding excess downtime during the turnaround that would quickly erode the project economics.
Meanwhile, the revamp opportunities that a turnaround provides are, themselves, few and far between. Petrochemical refineries, for instance, typically try to get five years between major turnarounds to maximize on-stream time. Some equipment can be connected before an actual shutdown, but most of the so-called tie-ins must fall into place during the turnaround, which usually lasts only 20–50 days.
Since the typical duration for the design, production and construction of a major revamp can take a year or longer and involves many stages, advanced planning is critical. Equipment with long lead time must to be ordered well in advance of the date required onsite, and engineering has to be contracted-out well in advance to find a quality engineering contractor with the experience required to execute the project without rework.
Planning for shutdown
Shutdown plans have to be well organized so that all the work dovetails within the allotted shutdown period. Figure 1 shows a portion of a typical project schedule.
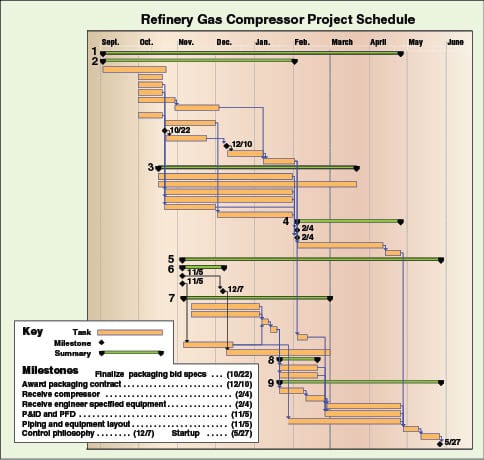

each of which has an early start date and last-possible completion date to keep it from becoming
schedule limiting. The two major phases and seven major steps are indicated by numbered,
green lines and identified in the table
This schedule breaks down the activities into a large number of steps, each of which has an early start date and last completion date to keep it from becoming schedule limiting.
The objective is to pre-install and do as much of the construction as possible in advance of the shutdown. Because shutdown time is very limited, only tasks that must be done with the unit shut down are undertaken at this time. This approach also allows for fewer people onsite during the crunch time, shutdown activities.
Ordering equipment
Before a high level of schedule detail is developed, a simpler bar-chart type schedule is used to develop the timing used for ordering the long lead time equipment, such as thick walled reactors, alloy equipment and high pressure vessels. Working back from the desired start of work in the field, the project manager can determine the latest time in which an order can be placed. This requires some lead time ahead of the order to do the necessary pre-purchasing activities. This sometimes requires that equipment purchases be made before the final design is completed. Figure 2 shows an example of back calculating how soon development of the purchase order must be started in order that equipment arrives onsite to fit the overall construction schedule work.
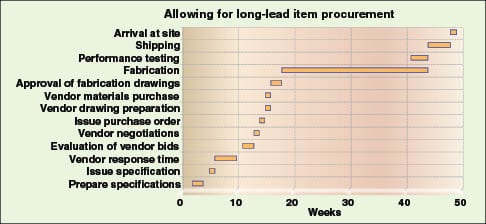
must be started to ensure that equipment arrives on time
Tie-ins
The tie-in list is the key to the piping. It needs to differentiate the type of tie-in, including the hot tap (done during unit operation) and shutdown tie-ins (made after unit is shut down in preparation of construction).
Most tie-ins are handled during shutdown. A typical tie-in would include two block valves and a pipe stub with another valve leading to the connection to the new equipment.
In some instances, tie-ins can be made in advance with the unit operating. So called hot tie-ins are usually avoided, however, because of the inherent danger to process fluids if something goes wrong. The split tee is one type of hot tie-in. It is basically a tee in two pieces that has an inside diameter identical in size to the outside diameter of the pipe being tapped. It is welded into the existing line, and then the connection to the tie-in line is made through the lateral.
Staffing
Most operating companies no longer have the luxury of maintaining a dedicated, fulltime and experienced engineering team required for executing small to mid-sized projects. Revamp projects are instead mainly staffed by using a mixture of contract engineers and managers, supplemented with the owner’s key staff. Only a limited number of key plant personnel are dedicated to the overall team. The contractor’s team is usually kept together during the project and quickly demobilized once the need no longer exists for personnel, which minimizes costs. Another advantage to contracting staff is that an expert in a specific field can be obtained for a short duration.
One strategy for avoiding excessive learning curve requirements and reducing costs of a contracted staff is to use the same contractor to perform multiple projects.
Figure 3 shows a typical staff scenario, including the owner’s team, the owner’s contracted staff, and the engineering contractor staff. Not shown is the construction team, which is directed independently.
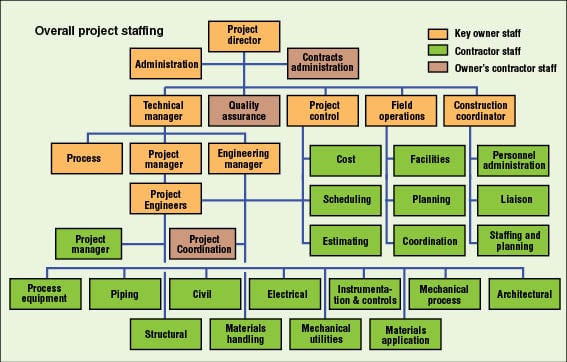
engineering contractor’s staff
Planning, engineering design, construction-management and commissioning/startup constitute the project life cycle. The project is turned over to operations people for commissioning and startup.
Owner’s staffing
The number of plant personnel assigned to a project varies but is usually limited to a few key people including the project manager, process engineer (as required), a safety lead, the operational lead (sometimes part time) and a cost-control/scheduling person.
Engineering contractor
A bell curve represents a typical staffing scenario for the engineering contractor’s home office, the initial phase starts with very few people until the project is developed. Then, staffing ramps up as engineers and designers are added for the production and construction phases. At the end of the project, demobilization of the staff starts to occur.
Engineering cost breakdown
For the engineering part of a project, the overall engineering costs for so-called grassroots or all-new designs are about 10% of the project costs. For revamps and retrofits the portion increases to between 15 and 20% because of the complexity of the equipment interfaces. Based on $100/h contractor engineering average rate, the total number of engineering hours can be estimated. From here, with the allowed engineering schedule, the number of people months can be back calculated. Using say 165 h/mo, the average number of people required on the project can be estimated.
Typically, the allocation of the various disciplines can be estimated from Table 1. Note the process and systems people tend to come on early and the instrumentation and electrical engineers come on late.
A good way to cross check the staffing is to show the number of staff on a simplified bar chart for the various disciplines during the engineering phase. Then total up the number of man weeks or man months to see if it agrees with the overall hours estimated.
In addition to the engineering contractor’s team, which is usually not onsite other than having some members in trailers either part time or full time, there is the owner’s field team.
Onsite project team
The following onsite team members have to be either hired on contract or supplied by the operating company. It is desirable to bring on the team just when needed for their work on the project and then release them back to the hiring organization (job shop). Getting quality contract people is not easy. There are only a few hiring organizations that specialize in providing the staff of people for the project execution phase. These companies staff projects worldwide. The other option is to hire from a number of different agencies. The personnel required to execute a project include at least the following:
• Project engineers
• Project construction managers
• Cost control specialists
• Records- and file-keeping supervisors
• Purchasing
• Welding specialist
• Rigging engineers
• Materials specialist
• Piping supervisors
• Excavation and foundation supervisors
• Transportation and delivery experts
• Field construction supervisors
A team of these experts supplemented with the owner’s representatives is usually housed in temporary trailers onsite. The arrangement has not changed much since the days when the team was comprised primarily of owner’s personnel.
Detailed engineering
It is typically necessary to contract out the detailed engineering team. The detailed-engineering-contractor team performs the engineering from its home office, once the project is defined by the operating company. The owner selects the engineering company that best fits the type of project, size of project and local availability. In former times, the engineering company was almost always local. However, with the proliferation of electronic drawings (and their transmission and sharing), cell phones, telephone conference calls and so on, the engineering team even for revamps is no longer required to be onsite. The onsite demands can usually be met by a small local team that acts mainly as the interface between the field and the home office team. Some revamps and retrofits still require a local company to be effective in the day-to-day field changes.
Engineering execution
The following is the order in which the engineering at the contractor’s office normally takes place:
1. Process engineering
The process engineering is usually staffed by the owner and takes the lead through the conceptual design phase. It must be involved early on to decide what is to be included in the project. The objective is to determine how the proposed concept can make maximum use of the existing facility equipment and minimize the new major equipment. This is somewhat of a trial-and-error procedure in determining the existing limitations of the major equipment (that would be too costly to replace).
Three alternatives may be evaluated either by inspection or by a “quick and dirty” cost evaluation. Process engineering usually is concentrated in the first two to three months of engineering and then goes down to one or two people.
2. Detailed engineering
Once the process concept is firm, then the detailed engineering begins. The systems engineering is the key in this phase. It starts with marking up existing process flow diagrams (PFDs) and providing a project description that defines what modifications are to be made, what new equipment is required and other significant project requirements. This basis becomes the vehicle to make sure everyone is on the same page and in agreement with the concept. Detailed engineering begins once the PFDs, piping and instrumentation diagrams (P&IDs), equipment specifications and overall scope of the project are completed.
Usually the existing (as-built) P&IDs are marked up showing modifications to piping, modifications to the existing equipment, addition of new equipment and reuse of existing equipment in a new service. Increasing a line size, using a larger control valve size, increasing the pump impeller diameter to the limits of the casing, changing to a larger motor size or going to a new larger pump are considered to be acceptable, cost effective modifications.
Some modifications are allowed on major equipment as long as they are cost-effective and can be performed in a reasonable shutdown period. Examples are larger nozzles, new internals, replacement of distillation trays with higher capacity trays or structured packing and alloy lining. Major modifications to major compressors, fired heaters and large diameter distillation columns is usually not cost-effective. In gauging the feasibility of major equipment replacement, the rule of thumb is to parallel-up with a smaller or identical item.
New data sheets are developed for the required new equipment. Check-rating data sheets for the existing equipment are provided for documentation that the equipment fits the new requirements. This information should be compiled together to serve as backup for the project definition and cost estimates. Put the following information in a set of binders available to the task force to keep everyone on the same page: process description, PFDs, P&IDs, data sheets, preliminary layouts and preliminary piping runs.
Electrical and instrumentation activities should be minimized until the project design is developed to the point that no rework would is required.
3. Long-lead item procurement
Long lead times on alloy and high pressure equipment requires some of the procurement activity to be done in advance of the project being fully defined. This subjects the project to some financial risks if the equipment ultimately requires extensive modifications or is not used at all. The key to procurement is always having firm specifications.
Good equipment data sheets are the minimum, with alternate case information provided as footnotes or a second data sheet. The detailed specification is key to getting out a purchase order with the minimum number of change orders. Just referring to the general codes (API, ANSI, TEMA) is not adequate. Any specific fabrication requirements must be called out. The associated specifications should be included with the general specification. Consider, for example, that requirements for corrosion protection are becoming more prevalent where wet acid gas is present. These requirements can add considerable cost. Welding specifications can be provided by the buyer or the manufacturer can supply specifications, and have them approved.
4. Use of skid mounted modules
Prefabricated equipment modules can save a considerable amount of field time and money, especially for a revamp. Having the equipment supplier provide a full skid for the equipment, including all of the auxiliaries, can be a win-win for both parties. Using the manufacturers’ control-system standard rather than a custom design can also save money. Reciprocating compressor systems can typically include, for instance, the inter-stage knock-out drums, inter-stage coolers, pulsation dampeners, lube oil system and control panel.
Skids are especially attractive for harsh climates and areas where skilled labor is limited. The Alaskan North Slope oil-production plants, for example, were built using very large modules shipped-in during short periods when the access water was clear of ice.
Pre-fitting the modules together before shipment is a must. Flange-to-flange connections, where permissible, reduce field welding demands, which is especially attractive for alloy lines.
Thinking ahead is the key to a safe, successful, on-time project that is performed without a major cost over run and without major surprises.
It is important to remember schedules are just plans. Doing things faster than can reasonably be expected usually results in rework and more cost in the longrun. There is typically a learning curve that results in efficiency and time saving measures being developed as the work progresses.
Coordination meetings, although time consuming, are a must in the efficient use of manpower. Changes to a plan may be required as unexpected obstacles are encountered.â–
Author

Ray Elshout is a process engineer for Energy Systems Engineering (Pasadena, CA 91106; Phone: 626-796-0642; Email: rayel [email protected]). During his career, he has worked in a variety of industries and held a variety of positions. His main field is process engineering, but he has been a project manager, consultant and operations trainer. Prior experience includes a position at Jacobs Engineering where he developed the design standards for solvent extraction of vegetable oil from soybeans, winterizing, deodorizing, fat splitting, hydrogenation, glycerin evaporation and distillation. Elshoult holds both a B.S.Ch.E. and an M.S.Ch.E. degrees. He is a licensed professional engineer in the state of California.

Danny L. Garcia is a senior project manager at Sun Engineering Services, Inc. (5405 Garden Grove Blvd. Suite 300 Westminster CA, 92683; Phone: 714-379-2300, ext. 341; Email: [email protected]), a full-service multi-discipline engineering consulting firm providing services to both energy and non-energy industrial facilities for over 20 years. Garcia’s more than 20 years of experience includes management of multiple small- to medium-size projects concurrently, over a two-year period, as part of an alliance contract for a major oil company. He worked as a consultant for an oil refinery in the Los Angeles area for over eight years. In his current position he is both a senior project manager and the marketing manager.