A pilot facility currently under construction in Charleston, W.Va. will produce renewable acrylonitrile (ACN) without requiring the traditional petroleum-based propylene as feedstock. Since ACN is the raw material used to make carbon fibers, the new route to ACN allows the production of bio-based carbon fiber. Acrylonitrile is also used as the raw material for acrylonitrile-butadiene-styrene (ABS) plastic, acrylic fiber, nitrile butadiene rubber and acrylamide.
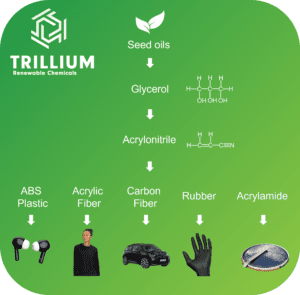
Source: Trillium
According to developer Trillium Renewable Chemicals (Knoxville, Tenn.; www.trilliumchemicals.com), the process cuts greenhouse gas emissions by 70% compared to the traditional propylene route, and uses a feedstock (glycerol) that is significantly cheaper than propylene. The Trillium process begins with glycerol, a byproduct of biodiesel manufacturing that is converted to acrolein via a dehydration reaction. Next, the acrolein undergoes an ammoxidation reaction in the presence of ammonia and oxygen to generate acrylonitrile.
The core innovation for the process is a proprietary catalyst for the dehydration that Trillium licensed from Southern Research Institute (Birmingham, Ala.; www.southernresearch.org). “The catalyst exhibits both high conversions in the reaction, as well as high selectivity,” notes Trillium CEO Corey Tyree.
In 2014, Trillium began a partnership with Solvay SA (Brussels, Belgium; www.solvay.com), which was interested in a bio-based route to carbon fiber. Earlier this year, Trillium and Solvay announced a scientific partnership in which they intend to develop a supply chain for bio-based ACN. Now, Trillium is becoming qualified as a supplier of ACN for Solvay carbon fiber materials.
The pilot plant, which is slated for completion in mid-2022, will be followed by a larger demonstration plant in 2023 and a commercial-scale site in 2025, Tyree says.