A rigorous and structured approach to determining the potential value of powder testing techniques in solids-handling applications can improve powder characterization and processing
Many chemical process industries (CPI) sectors face growing pressure to measure and control powder properties more effectively, either to improve manufacturing efficiency — from raw material selection, through processing to quality control — or to gain a competitive edge via superior product performance. At the same time, there is growing pressure to streamline the analytical processes that are used to drive progress. Identifying the most informative techniques for powder testing and measurement is becoming increasingly critical, whether to help develop innovative technology or to simply remain competitive in given markets.
This article considers commercial drivers for adopting or reviewing powder testing techniques with the aim of identifying optimal solutions from a growing range of test options. Experimental studies compare the performance of different techniques in applications from the pharmaceutical and cosmetics industries. The results illustrate the benefit of a rigorous and structured approach to deciding which powder properties to measure, and the potential value of a robust strategy for powder characterization.
Drivers for change
Competition drives a cycle of continuous improvement, across industries and in many leading companies. Competitors may begin manufacturing a more reliable product, or one that more effectively meets application requirements, or they may develop the ability to simply sell products at a lower price due to reduced manufacturing costs. The response to these stimuli is to re-evaluate current practices and make plans to improve. Analytical services — either conducted in-house or outsourced — contribute significantly to the cost of research and development (R&D), product commercialization, and routine manufacture, and are often a target for cost-cutting or transformation. A periodic reassessment of which analytical techniques are being applied, as well as the value of the information they deliver, and the effort involved in its generation is a sound business practice, particularly against a backdrop of innovation in analytical instrumentation.
Powder processors face unique challenges when it comes to refining analytical practice. The properties that define the performance of liquids and gases are well-understood and easily measured, and established design methodologies for processing equipment help to identify relevant parameters. This is not the case for powders. Powders are assemblies of solid particles, low levels of liquid, and gas (usually air) that exhibit complex behavior resulting from interactions between these phases. The analytical techniques routinely applied to powders can be classified as measuring either particle or bulk powder properties. Particle parameters include size and shape, density, surface area, porosity and surface charge. All of these parameters may justify measurement, depending on the product and its intended application. However, measuring particle properties alone does not enable reliable characterization of the bulk powder. Notably, particle properties often do not permit full characterization of flowability, often a critical property for solids-processing operations.
Uncertainty around the optimization of bulk-powder testing techniques is common, particularly for new or demanding applications. Bulk density is a routine measurement that defines the size-weight relationship of packaged products and impacts the throughput of transportation systems. But if bulk density and particle properties in isolation do not adequately describe performance — and they rarely do — what other techniques should be considered? Few other bulk powder properties appear consistently on product specifications, and design methodologies for powder processing equipment are extremely limited. Hopper design is the exception, and points to the value of shear-cell testing. However, even those adept at shear-cell analysis are increasingly aware of its limitations. This raises the question of how to best identify a powder testing regime that can provide the information needed to compete effectively.
The evolution of powder testing
Commercial powder testers vary considerably on the basis of three key characteristics:
Ease of use/productivity. How easy is it to generate high-quality data? How much time is required for the measurement? What level of training and expertise is required for instrument use?
Sensitivity. What is the ability to differentiate among similar samples? Repeatability and reproducibility have an impact on sensitivity, but some techniques are inherently more sensitive than others.
Relevance. How well does the powder-property information generated with a given analytical device correlate with the aspects of powder behavior or process performance that are of greatest interest?
An optimal analytical solution will generate sufficiently sensitive and relevant data with the minimal level of manual input.
Current practice and trends in the application of powder testing are driven not only by the need for better, more informative data, but also by growing appreciation of the economic returns that modern instrumentation can deliver. An enhanced ability to efficiently handle the large amounts of data that modern testers can generate has been instrumental in revealing this value.
Traditional powder testing techniques — as exemplified by angle of repose, flow through an orifice and tapped density methods — generate a single descriptor of flowability. If this is not informative with respect to the behavior of interest, then the tester has no value. If it is informative, then the tester potentially has value, though poor repeatability and sensitivity can be a crucial limitation when it comes to differentiating similar powders. Either way, there are limited amounts of data to interrogate.
Alternative options for powder testing include avalanche or rotating-drum testers, which capture images of the interface of a powder sample as it tumbles within a drum rotating at different speeds. In this environment, powders exhibit a periodic flow pattern, initially moving with the rotating drum before reaching a certain height at which the surface breaks and the powder falls, or avalanches, and flow establishes. This cyclical behavior is repeated over and over as the drum rotates. Mathematical analyses of the captured images generate a number of parameters, but it is important to recognize that they are all derived from the application of a single technique, as with traditional methods. Furthermore, avalanche testing offers a limited scope to modify the test conditions to simulate a specific process. Drum speed is the primary test variable.
In contrast, dynamic powder testers that measure flow energy values quantify powder behavior under a range of different stress and flow regimes of direct relevance to powder processes. Flow energy is generated from measurements of the forces acting on the blade of the tester as it rotates through a powder sample, which can be in a consolidated, conditioned, aerated or fluidized state. Testers with this capability also offer shear and bulk property measurement, combining three distinctly different testing techniques to generate multiple parameters that provide multi-faceted characterization for a given powder.
With the limitations of single-number analysis now widely recognized, and with advances in data analysis software making it much easier to efficiently interrogate large datasets, the potential of modern testers is becoming increasingly apparent, and easier to exploit. Applying a broad range of analytical techniques to generate an array of parameters, which are then refined on the basis of their ability to sensitively and relevantly differentiate materials, is increasingly common [1, 2]. This approach is highly effective in identifying which powder testers will provide a return on investment by delivering unique and valuable information.
Case study 1
This example involves characterizing the processability of innovative pharmaceutical excipients. A relatively recent innovation in the field of pharmaceutical excipients is the introduction of microcrystalline cellulose (MCC) in the form of spherical pellets, such as Cellets. Coating these inert, neutral, starter cores produces optimized particles for combinatory and controlled-release tablets. A Wurster fluid-bed coater is a popular choice for this process (Figure 1).
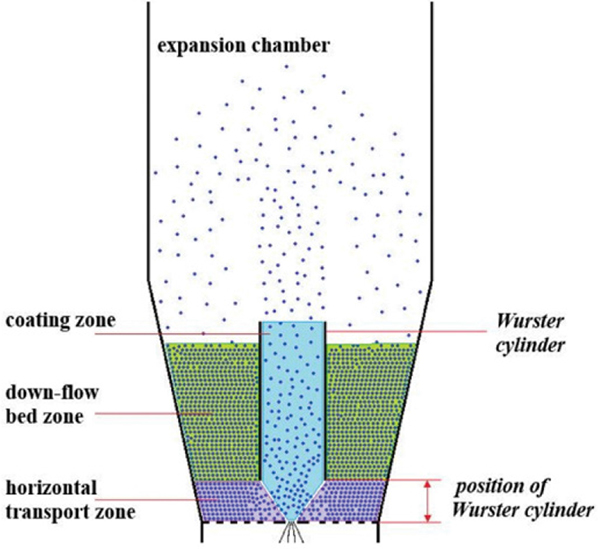
FIGURE 1. As discussed in Case Study 1, a Wurster fluid-bed coater subjects the powder to fluidization in the cylinder, confined flow in the down-flow zone and partially aerated flow in the horizontal transport zone
In an experimental study, the properties of Cellets of different sizes were investigated using a range of methods. Ref. 3 contains full experimental details. Here, the focus is specifically on the measurements carried out to investigate flowability, which included tapped-density and flow-through-an-orifice testing (JV1000 and Flowability Tester Model BEP2, respectively, both Copley Scientific, U.K.), avalanche testing (GranuDrum, GranuTools sprl, Belgium) and flow-energy measurement (FT4 Powder Rheometer). Data were gathered for Avicel PH102 (MCC powder) for comparative purposes. The aim was to determine a) whether the materials could be differentiated and b) whether test conditions and results could be linked to likely bulk-solids behavior in different regions of the coater.
Particle-size data for the Cellets samples are shown in Table 1, along with the results from tapped-density and flow-through-an-orifice tests. Tapped-density data are presented in the form of Hausner Ratio (HR), the ratio of tapped to poured powder density, and provide no differentiation of the Cellets samples. Differences are observed, however, in the Avicel PH102, which has an HR of 1.21, indicating a classification of “fair” flowability, relative to the “excellent” flow of the Cellets samples (HR in the range 1.09 to 1.11). Flow-through-an-orifice data only provide limited differentiation of the Cellets, particularly when standard deviation values are taken into account, and there is no clear trend — the poorer flowability of the Avicel PH102 is only identified by a “no flow” result.
The avalanche tester reports two parameters: dynamic angle of repose; and cohesive Index (Figure 2). Dynamic-angle-of-repose data exhibit significant variability and, as with the preceding techniques, fail to differentiate the Cellets samples, though Avicel PH102 is again classified as behaving differently. Cohesive index provides some differentiation, but not between the Cellets 200 and 350 samples. Cohesive index is a measure of the extent to which individual flow-angle measurements deviate from the average over the course of the test. The test is essentially a measure of variance, with higher values associated with more cohesive powders.
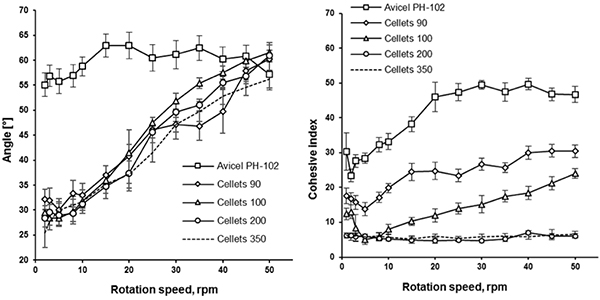
FIGURE 2. The graphs show data on angle of repose (left) and cohesive index (right) from the avalanche tester for Cellets samples and Avicel PH-102 discussed in Case Study 1
The avalanching data show varying trends with respect to drum rotation speed. For example, dynamic angle of repose increases with rotation speed for all the Cellets samples, but is relatively consistent for the Avicel PH102, particularly at higher rotation speeds. With respect to cohesive index, the Cellets 90 sample appears to be plateauing at higher rotation speeds, while the Cellets 100 exhibits an essentially linear response, suggesting that the two samples could generate equivalent values at higher rotation speeds. These results illustrate the extent to which avalanching behavior is influenced by the speed of rotation of the drum, as well as the characteristics of the powder. This complicates the setting of test conditions, and there is little information in the literature correlating avalanching parameters with process performance, to guide this process. In conclusion, it is difficult to infer from these data how the Cellets might behave in different areas of the coater.
Figure 3 shows how flow-energy parameters for the samples — specific energy (SE), basic flowability energy (BFE) and normalized aerated energy (NAE) — differentiate all four of the Cellets samples, exhibiting clear trends with Cellets size. The Avicel PH102 is also differentiated.
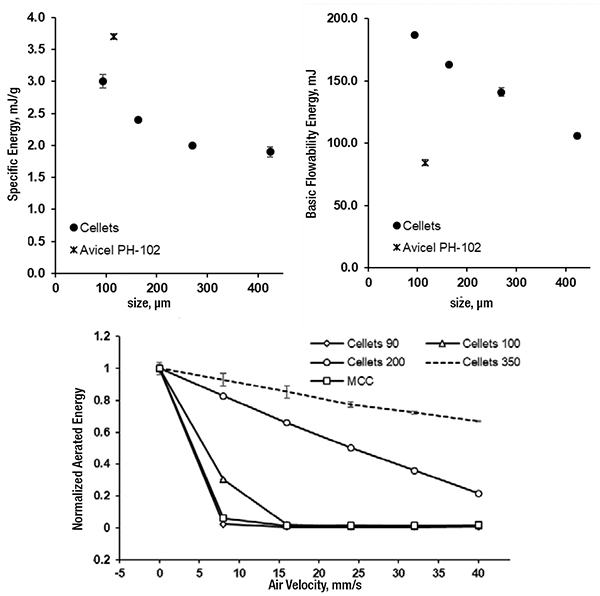
FIGURE 3. The graphs show flow-energy measurements — specific energy (left), basic flowability energy (middle) and normalized aerated energy (right) — for Cellets and Avicel PH102 samples in Case Study 1
In an SE measurement, which involves testing with an upward traverse of the instrument blade, the sample is in a low-stress, conditioned state and is subject to gravitational forces. SE values tend to be primarily influenced by mechanical interlocking and frictional interactions between particles. The reduction in SE with increasing particle size can therefore be rationalized by the fact that larger particles have lower specific surface area, and by the presence of fewer particles in samples of comparable volume. Both factors reduce the extent of inter-particular interactions and, in combination, rationalize the trend observed. The higher SE value of the Avicel PH102 is consistent with this rationale.
In contrast, BFE measurements are generated with a downward traverse of the blade, subjecting the powder to forced or compressive flow conditions. BFE measurements are influenced by a wide range of factors, but the trend in the Cellets data reflects that of the SE data. The Avicel PH102 has a lower BFE value than all of the Cellets, which is due to the fact that more cohesive powders tend to entrain air, creating voids for the blade to move particles into, and thereby reducing the energy associated with its movement.
NAE is determined by carrying out a BFE measurement with air flowing through the sample at a defined rate, and directly quantifies the response of the powder to air. With Cellets 350, NAE declines gradually with increasing air velocity, but in contrast, the finer Cellets samples exhibit a rapid reduction in NAE at relatively low air velocities and then exhibit a plateau at a value that indicates fluidization. The profile for the Avicel PH102 is similar. These results suggest that the coarser Cellets samples do not fluidize as readily as the finer ones, a result that reflects the greater thrust needed to fluidize larger, heavier particles.
When considering these data relative to the environment in the Wurster coater, it is reasonable to suggest that BFE data will be most informative of flow behavior in the constrained downflow zone, while NAE values are likely to inform behavior in the cylinder and conveying sections. Cores with a particle size of 350µm typically process well in the coater. These data enable a robust assessment of how cores of different size differ in terms of flow behavior. Coating trials would confirm the results of any predictions. It is clear that flow-energy measurements are more reproducible and differentiating than data from traditional and alternative techniques. Trends are observed that are rationalized by particle size and intuitively linked to flow regimes in different areas of the coater.
Case study 2
This example describes enhancing powder characterization to achieve better product performance for cosmetic pigments. In the cosmetics industry, innovative products command a premium price in a highly competitive marketplace, though assessment of performance is often relatively subjective. Intercos Group (Intercos S.p.A, Agrate Brianza, Italy), one of the world’s biggest suppliers to the cosmetics industry, has recently embarked on studies to improve formulation by adding powder characterization to its routine analysis schedule. The aim is to identify a powder-testing method that can be used to assess the flowability or “smoothness” of highly-cohesive pearlescent pigments and differentiate them with respect to the texture, applicability and coverage of formulated compacts. These vital characteristics cannot be predicted from current analyses, such as particle sizing (granulometry) and oil absorption. Furthermore, the high cohesivity of the pigments renders traditional powder testing methods, such as angle-of-repose, impractical. The work described here explains how alternative testers were assessed to identify a new solution.
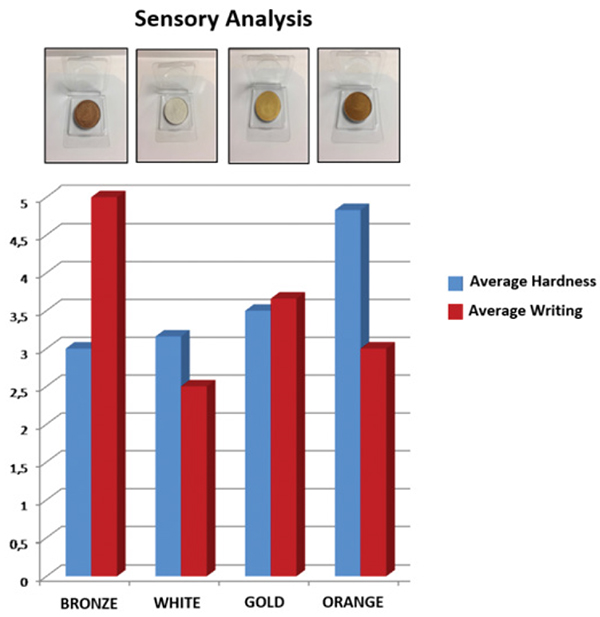
FIGURE 4. The graph shows data from a sensory analysis of the hardness and writing performance of cosmetic formulations containing different pigments, as discussed in Case Study 2
In a first experiment, three pigments — bronze, white and gold — suitable for inclusion in an eyeshadow compact were tested with an avalanche tester (Revolution Powder Analyzer, Mercury Scientific Inc., Newton, Conn.). Figure 4 shows sensory data produced via a manual scoring technique for products formulated with these pigments. Formulated samples were simple blends of filler, binder and pigment, with only the pearlescent pigment changed in each case. All ingredients and overall composition otherwise were kept constant. The three formulations are comparable in terms of hardness (blue bars), a measure of texture/consistency to touch, but are scored differently with respect to writing (red bars), which relates to pay-off, the coverage or brightness of a color on the skin. Table 2 shows the avalanche test data.
SL (solid-liquid) ratio relates avalanching behavior to the extent to which the powder exhibits solid- or liquid-like behavior. These data identify the white pigment as being more liquid-like (SL ratio closer to 0) than the other two powders (higher SL ratios; closer to 1). Avalanche energy data confirms the greater fluidity of the white and suggests a trend across the three powders. However, the error bars associated with these data (and to a lesser extent, with break energy, which exhibits the same trend) are extremely wide, compromising the statistical significance of the data.
The Hurst Index quantifies the extent to which avalanching behavior is random, as opposed to exhibiting temporal trends. This index also differentiates the powders, but the trend does not correlate with observed differences in writing performance. Rest angle, the angle the powder assumes at the end of an avalanching event identifies the gold pigment as the most cohesive of the three materials, but provides minimal differentiation between the other two samples. Finally, surface fractal, which represents the fractal dimension of the powder surface measured immediately post-avalanche, suggests that the white powder may be associated with a smoother, more uniform surface (a lower surface fractal that is closer to one).
In combination, and on balance, these data identify white as the most smoothly flowing pigment, followed by bronze and then gold. However, this ranking does not reflect the trend in writing performance, and its value is significantly undermined by the high variability associated with some parameters. It was therefore concluded that the avalanche tester could not provide useful insight for this application.
In a second experiment, tests were carried out with two pearlescent pigments — orange and bronze (as analyzed in the earlier experiment) selected on the basis of similar granulometry and oil absorption. These were subject to dynamic, shear and bulk property measurement to determine the ability of the instrument to differentiate the pigments in a relevant way. Sensory analysis identifies that the orange pigment formulates with mica into a harder compact, with lower coverage than the equivalent bronze compact.
Table 3 summarizes the differences detected in dynamic, shear and bulk properties of the two pigments. These data provide clear differentiation, consistently indicating greater cohesivity between particles of the orange pigment, and hence poorer flowability.
More specifically, both SE and BFE are substantially higher for the orange pigment relative to the bronze, indicating that it is likely to flow less easily in a wide range of processing environments. With both powders repeat BFE testing generates similar results showing them to be physically stable, though the stability index (SI) (the ratio of BFE measured in test 7 relative to the value measured in test 1) is slightly higher for the orange pigment, suggesting it may be more prone to agglomeration.
Conditioned bulk density (CBD) data, generated as a byproduct of flow-energy measurements, highlights less efficient packing in the orange powder, providing additional evidence of greater cohesion. Powders in which the cohesive forces between particles are relatively high have a greater tendency to retain air in structured pockets within the bed, resulting in lower CBD relative to a less cohesive powder in which particles pack more efficiently. More efficient packing also rationalizes the lower permeability of the bronze powder, since close packing reduces the size and number of channels through the powder bed, increasing the pressure drop associated with the transit of air.
Stronger inter-particle forces of cohesion also reduce the ability to separate particles to minimize inter-particle interactions and improve flowability. This effect is evident in the aeration ratio (AR; the ratio of BFE to AE), which is much lower for the orange pigment than for the bronze. The less cohesive bronze is more sensitive to the introduction of air. Air entrainment in the more cohesive orange powder makes it more compressible, as well as reducing CBD, and the flow function (FF) measured by shear-cell testing classifies the orange pigment as “fairly free-flowing” relative to the “free” or “excellent” flowing designation associated with the higher FF of the bronze.
The combination of dynamic, shear and bulk-powder properties consistently differentiate pigments that are equivalent on the basis of other routine analyses, but perform differently when formulated. Measuring these properties provides the information required to implement a more scientific approach to product formulation and reliably and efficiently develop products with the required properties.
The way ahead
The case studies included here illustrate the increasingly common practice of refining powder testing practices by measuring a range of parameters to identify those that offer unique insight or correlation. Advances in data processing ease the effort of handling the data generated by modern powder testers and reinforce that it is more sophisticated techniques that are most valuable, particularly for new or demanding applications. As these studies show, although most relevant parameters can be specific to the application, the ability to apply different testing protocols, for example, to measure dynamic, shear and bulk properties, is a fruitful starting point for powder processors looking to establish a powder testing strategy that is both effective and efficient.
Edited by Scott Jenkins
References
1. Van Snick, B. and others. A multivariate raw material property database to facilitate drug product development and enable in silico design of pharmaceutical dry powder processes, International Journal of Pharmaceutics, 549, pp. 415–435, 2018.
2. Escotet-Espinoza, M.S. and others. Using a material property library to find surrogate materials for pharmaceutical process development, Powder Technology, 339, pp. 659–676, 2018.
3. Mohylyuk, V. and others. Assessment of the effect of Cellets’ particle size on the flow in a Wurster fluid-bed coater via powder rheology, Journal of Drug Delivery Science and Technology 54, 2019.
Author
Jamie Clayton is operations director at powder characterization company Freeman Technology and is based at the company’s headquarters (Tewkesbury Business Park, Miller Court, Severn Drive, Tewkesbury GL20 8DN, U.K.; Phone: +44 (0) 1684851 551; Email: [email protected]). He graduated from the University of Sheffield with a degree in control engineering and is responsible for overall management of company activities, including the R&D, production, sales and customer support teams. During his time with the company, Clayton has worked as a mentor with several academic groups and is an active member of ASTM F42. Clayton is also a regular contributor to conferences and workshops on the topic of powder rheology and works closely with Freeman clients on the application of the company’s technology.