Even with advanced predictive technologies, unplanned equipment failures can still occur. In these instances, as shown in this boiler example, rapid maintenance action is crucial to minimize downtime
Maintenance activities generally fall into two categories — reactive and preventative. The first focuses on repairing an asset once a failure occurs, while the second aims to avoid asset failure and repairs by preventing issues before they happen. Such preventive measures are achieved by using predictive methods that leverage theoretical rate of failure and actual equipment performance.
In an ideal world, rather than relying on reactive maintenance, a chemical processing plant will employ planned preventative activities to minimize downtime. However, in practice, unexpected equipment failures do happen, resulting in unplanned shutdowns and turnarounds. Businesses can still make the most of the circumstances by promptly adjusting their maintenance schedules to bring forward equipment-optimization projects. To succeed in this strategy, comprehensive, responsive maintenance practices are needed to support businesses.
High-quality predictive maintenance models enable businesses to plan suitable maintenance schedules that maximize equipment lifespans while minimizing the environmental impact, costs and downtime associated with replacing damaged units or components. Accurate and reliable simulations of equipment or component failure are a key asset. However, machines can sometimes still experience unexpected issues.
In these situations, it is crucial for facilities to be as flexible as possible, readjusting their maintenance schedules and intervening quickly to restore optimum operations with minimal downtime. In addition, they can turn the situation to their advantage, using the shutdown to complete regular maintenance activities that were scheduled to take place at another time. In this way, plants can maximize their annual uptime. To outline such responsive strategies, a maintenance project involving boilers at a real-life waste-to-energy plant is used as an example in this article (Figure 1), but these maintenance principles are applicable to any type of boiler that is exposed to harsh conditions.
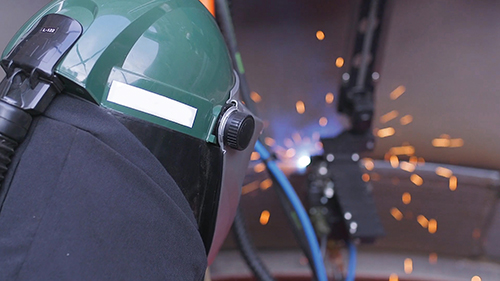
FIGURE 1. The unplanned failure of boiler equipment required the rapid restoration of the boiler’s structural integrity to help restore its operations quickly
When equipment reaches a boiling point
The waste-to-energy plant referenced in this article incinerates 750,000 metric tons of residual municipal solid waste (MSW) per year, which would otherwise be sent to landfill. The heat generated by the process is used by boilers to heat water and produce steam.
Boilers — critical equipment in waste-to-energy plants, and many other types of processing units — are regularly exposed to harsh operating conditions. For example, in boilers, waste with large volumes of plastics, or materials containing paint or glue, will generate a broad range of volatile compounds containing chlorine, sulfur, alkali and heavy metals, as well as hydrochloric acid and chloride salts. The presence of various impurities in the combustion gases can cause erosion and corrosion of the furnace and wall tubing. Both types of damage can be exacerbated by chloride-rich ashes that inhibit the growth of a dense, duplex oxide scale on the boiler’s surface, which would ordinarily act as a diffusion barrier to prevent or reduce corrosion and erosion. Additionally, alkali metals, lead and zinc can react readily with chlorine and further contribute to the transport of chloride-rich ashes to the boiler tube’s metal surface, increasing the corrosivity of the deposit. Finally, heat flux in boilers leads to the rapid diffusion of corrosive substances.
All of these factors serve to decrease the useful life of boilers in processing facilities. Nonetheless, proper boiler maintenance prevents these issues from escalating and causing cracks, ruptures, thermal fatigue or other factors that can further shorten the unit’s lifespan, affecting reliability and performance of all plant operations. Also, highly effective maintenance strategies can help facilities by optimizing performance and productivity.
In accordance with these goals, the waste-to-energy plant scheduled regular maintenance of its three boiler lines to maintain optimal boiler and plant performance, and also planned a turnaround for one of its boiler lines.
However, the facility experienced an unexpected failure on that line well before its scheduled downtime. To avoid having two periods of downtime on the same equipment within one year, it was necessary to conduct the planned maintenance activities at the same time as the emergency repair.
A team of maintenance engineers assessed the condition of the boiler, which was found to be eroded and corroded (Figure 2). After abrasive grit-blasting operations were conducted on the structure to remove impurities from the eroded surfaces, the team evaluated the state of preservation of the vessel. Together with tube-wall thickness readings, the engineering team could offer a quantitative analysis on the level of corrosion and erosion in the equipment and determine the best course of action.
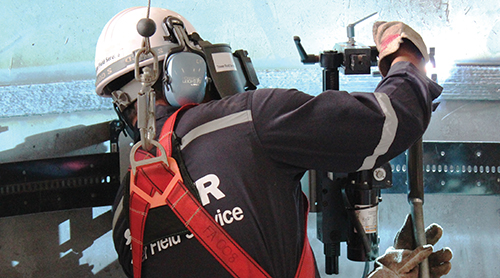
FIGURE 2. Boiler inspection led to the recommendation to clad, or weld overlay, the damaged areas
Further work found heterogeneous conditions across the tubes, with areas where the thickness was compromised, but above 2.5-mm thickness, and others that were more heavily eroded or corroded, with thicknesses as low as 2 mm.
To restore the structural integrity of 60 m2 of membrane walls within the boiler, where thicknesses above or equal to 2 mm were found, the suggestion was made to clad, or weld overlay, the structures (Figure 3). This method relies on the application of layers of corrosion-resistant materials, such as Inconel 625, an austenic nickel-chromium-based superalloy containing niobium, on damaged areas in existing units.
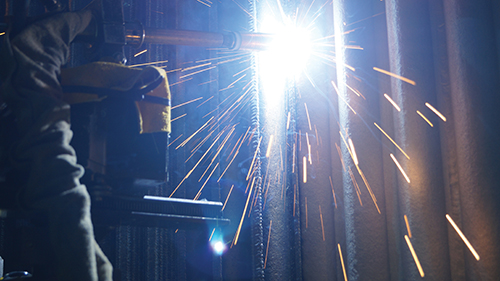
FIGURE 3. Weld overlay involves applying layers of corrosion-resistant materials onto the selected surfaces
Inconel 625 is particularly durable and resistant to corrosion, erosion and oxidation, even in harsh environments with elevated temperatures, such as in boilers. More precisely, the chromium component in the material provides resistance to oxidizing chemicals, while the high nickel and molybdenum content make the alloy resistant to non-oxidizing environments.
Molybdenum also makes the material particularly resistant to pitting and crevice corrosion. The added niobium stabilizes the alloy against sensitization during welding, thereby preventing subsequent intergranular attack. Also, the high nickel content protects against stress-corrosion cracking caused by chloride ions, which are typically found in incinerated waste. In addition, Inconel 625 exhibits high fatigue strength, even when it is present in the form of thin sheets.
Moreover, the thermal conductivity of Inconel 625 is lower than that of carbon steel, so the application of thin layers is ideal to avoid any increase in surface temperature that would promote corrosion while optimizing heat exchange for elevated boiler performance. As a result, this alloy would allow the boiler’s surface to better withstand its extreme operating conditions and increase its lifespan.
The power of automation
To streamline the process, the maintenance engineers leveraged automation and IIot technologies to perform the weld overlay procedures. By doing so, the project could be completed at least three times faster than using manual cladding, helping the plant to reduce the shutdown interval and re-start operations faster.
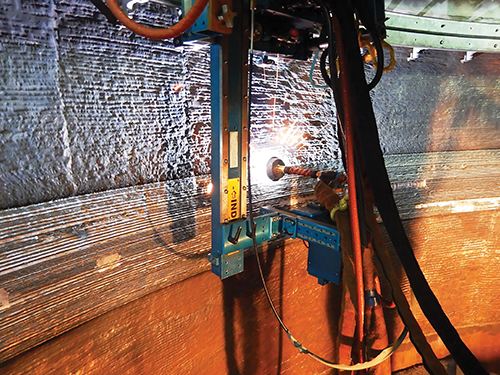
FIGURE 4. To restore the integrity of the boiler’s wall, a robotic arm was used to move a welding torch and an oscillator, creating weld beads. The robot is moved along the damaged area by a carriage, which travels on a laser-leveled track system fixed to the surface that needs repairing
For automating such a task, robotic arms can be used in welding activities to create weld beads on a surface that needs repairing (Figure 4). The robot is moved along the damaged area on a carriage, which travels on a laser-leveled track system fixed to the boiler’s surface. All the weld-overlay process parameters, such as carriage speed and bead thickness, are controlled by a programmable logic controller (PLC; Figure 5).
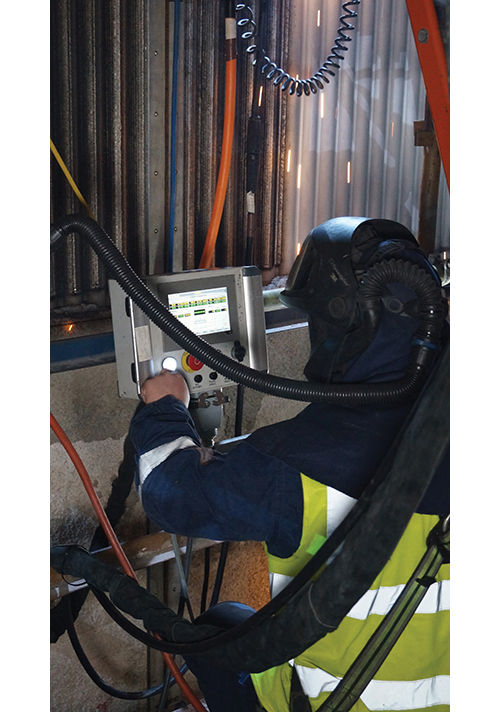
FIGURE 5. Advanced automation technologies can contribute to more rapid resolution of maintenance and repair tasks
The control unit also stores different weld procedures, meaning that operators can easily select and monitor the best procedure on the basis of the intended application via a human-machine interface (HMI), without the need to qualify and test new procedures. Establishing new weld procedures could otherwise require up to four weeks. So, utilizing proven, standardized setups helps substantially reduce downtime and address emergency shutdowns as quickly as possible.
Going the extra mile
The strength of the boiler tubes with thicknesses between 2 and 2.5 mm were also enhanced before the automated weld overlay to obtain optimum results. These parts, which accounted for 3 m2 of the total surface area, were pre-treated by means of carbon-steel buildup. This consists of applying a layer of parent material to the existing tubes before coating the surfaces with refractory Inconel 625.
Once completed, the repair passed independent non-destructive tests (NDT) to evaluate the quality of the procedure. In particular, suitable, homogeneous thickness levels were found using direct-thickness checks. Similarly, dye penetrant inspection (DPI) unveiled the absence of surface-breaking flaws and discontinuities that could otherwise compromise erosion resistance and equipment service life. Even more, positive material identification (PMI) analyses revealed a suitable elemental composition of the weld overlay.
A thorough final inspection report was provided, detailing the general conditions of the boiler that the plant could use to effectively set up future preventative-maintenance activities. In addition, this confirmed the quality and compliance with key requirements and regulations. The combined repair and maintenance projects were completed in only twelve days of downtime and the plant could restore operations at its boiler line.
When unexpected equipment failures occur, the top priority for businesses is restoring their operations as quickly and as effectively as possible. A skilled maintenance and repair specialist plays a key role in enabling plants to meet these goals. In particular, a team with the right expertise can streamline these activities by quickly mobilizing teams, offering rapid consultations and feedback, as well as leveraging experience and advanced solutions to shorten processing times. ■
Edited by Mary Page Bailey
Author
Adam Crosswell is Automated Weld Overlay manager for the ERA region at Sulzer Chemtech (Email: [email protected]). With an extensive engineering background, he is an experienced maintenance and repair specialist and has managed numerous projects in the petrochemical and energy sectors. These include both on-site and workshop-based turnkey automated weld overlay solutions. Crosswell also holds a M.S. degree in mechanical engineering from Southampton Solent University in the U.K.