Quality control processes can have a reputation for being redundant or tedious, but they play a fundamental role in producing consistent and effective products. When it comes to the manufacturing of products for the medical and life-sciences sectors, these processes can even save lives. Stringent metrics and checks are paramount to maintaining integrity, meeting regulatory requirements and safeguarding health.
Product efficiency and efficacy
If manufacturing companies do not have systems in place to monitor every step of product development — from concept and R&D to production — they risk producing products that do not meet specification, do not function as intended and do not comply with stringent regulatory standards. Not only can this be dangerous to the end user, it also can be costly and damaging to the reputation of the manufacturer or developer.
For instance, consider that team that designed a complex robotic medical device and manufactured it to completion, and then conducted testing on the finished product. This would likely result in a long list of quality issues and malfunctions, leading to unplanned disassembly and rework. The resulting labor and parts are costly, and any delays in shipment can damage the reputation of both the manufacturer and their customers, who also risk losing market share to competitors. By implementing in-process quality testing from the beginning, you can test for critical performance attributes within a sub-assembly to ensure its proper function before integrating into final configuration.
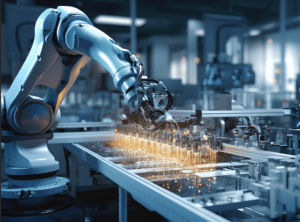
Quality-control activities should be a part of development and manufacturing processes from the beginning
Where possible, automation can make a huge impact on consistency and scale. We know that manual processes are more error-prone, especially when manufacturing at a large scale, so finding places in your process for automation can improve efficiency and reduce errors.
Surefire ways to troubleshoot
Engineering experience for medical & life sciences involves conceptualizing, prototyping, material selection and detailed design. None of this is immune to error, which is why workflow checkpoints are integral to high quality, efficient and cost-effective product development. When issues are caught it is important to initiate several actions, such as:
- Quality turnbacks. This is the process of categorizing and solving errors to prevent them from occurring again. When an issue is discovered, the team should investigate its origins and put parameters in place to solve the problem moving forward. This may involve additional training or revised work instructions. Doing this daily and feeding back the results allows groups to enhance operational efficiency and streamline our processes.
- Debugging. Any time the root cause of an issue is not immediately apparent, quality-control teams should go into debugging mode, bringing in team members with varying expertise to follow alternate troubleshooting routes. This is the benefit of having an end-to-end support team, as it enables access to individuals with domain knowledge and expertise to help with debugging. Often, the support team can call in a member of the R&D team who was involved in the design and development of the product to help.
Both processes are essential to ensure root causes are identified and addressed. Continued trend analysis can verify that the actions taken were effective.
At the end of the day, it is essential that all operations are process-based, not people-based. If someone were to quit tomorrow, the business cannot be overly impacted. Or course, it is a requirement from the FDA to have documented processes to prevent this, but it is also important from a business standpoint to maintain the continuity of projects.
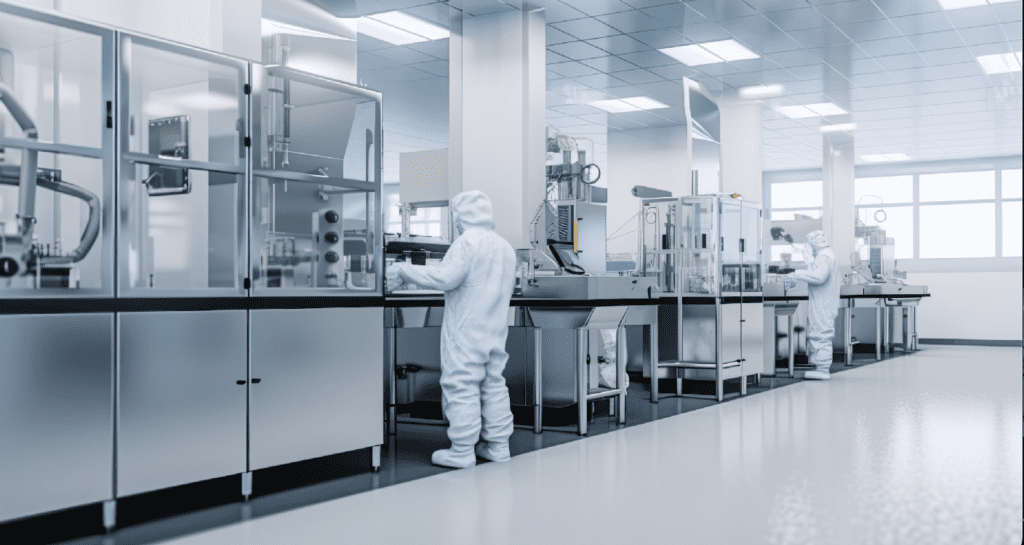
Manual processes are intrinsically more prone to errors, so it is important to identify opportunities for automation
Use case: Manufacturing diagnostic tests
Bringing real-world examples to the forefront can certainly emphasize the importance of precision in medical manufacturing processes. Ascential Medical & Life Sciences worked with a Boston-based precision-diagnostics startup firm to develop and manufacture its antibiotic-susceptibility testing system. These tests are used on patients with severe infectious disease to help the clinician select the most effective antibiotic therapy for the patient’s specific case. This precision testing equipment makes it possible to determine how to treat that patient in just eight hours, rather than the typical 3–5 days. For some patients, that faster timeframe could mean the difference between life and death. However, its accuracy depends entirely on the instrument functioning exactly as designed.
In order to make this critical technology available to as many patients as possible, Ascential’s team designed the instruments to process up to 96 patient samples in parallel. The effectiveness of the assay is dependent on meeting strict process parameters. The quality and in-process control metrics ensure that each panel and each well with a panel experience consistent environmental conditions, particularly temperature. This precision allows equipment to deliver potentially life-saving results as quickly as possible.
Failing to implement these checks and metrics can result in the technology being recalled after it was delivered and maybe even after it was used.
Benefits of an end-to-end development & manufacturing team
Working with the same team throughout the development of a project and into production enables the most in-depth knowledge to be applied to implementing robust quality control systems and addressing new features in the future. Partnering with an experienced medical and life sciences manufacturer early in the R&D process allows manufacturing best-practices to be designed in from the beginning. It is highly recommended to partner with a team that can handle a project from ideation to commercialization, limiting the number of hand-offs, and reducing the risk of errors.
When handling the development and manufacturing of medical instruments and other products, there must be a commitment to quality control checks and metrics. This is a fundamental aspect of fostering innovation in the medical and life sciences industry and advancing healthcare for patients. ♦
Edited by Mary Page Bailey
Author
Joe Wong is the director of project/program management at Ascential Medical & Life Sciences. Prior to his more than ten years with Ascential, he held product development positions at Microsoft, Nokia and Hewlett Packard. He holds a B.S. in mechanical engineering from Cornell University.