Today’s steam crackers are bigger than ever — those of tomorrow might be carbon neutral
Steam cracking is a key process of the petrochemical industry, whereby naphtha or other petroleum-based feedstock is thermally broken down (cracked) into smaller building-block compounds, such as ethylene, propylene, butadienes and BTX (benzene, toluene and xylenes), which are then processed into plastics, rubber and other polymers and chemicals. The feedstock is cracked within milliseconds as it flows through the furnace tubes at temperatures of around 850°C. Crackers are large, complex units with multiple furnaces — sometimes as many as ten — that are integrated with many different process units for separating and purifying the different olefins, which in turn are processed into products. Hence, crackers are at the heart of the aptly named petrochemical complex (Figure 1).
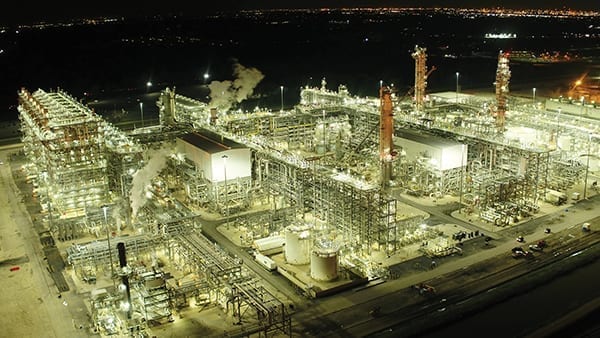
Figure 1. Steam crackers are part of large petrochemical complexes, such as Chevron Phillips Chemical Co.’s Cedar Bayou plant in Baytown Texas. CPChem’s 1.5-million m.t./yr ethane cracker started up in 2018. TechnipFMC
Although crackers will operate with the most economical feedstock, depending on the location, all crackers have one thing in common: today’s cracker furnaces use fossil fuels to heat the tubes to the high temperatures required. As a result, the steam cracker is a major source of CO2 emissions resulting from the combustion of fuels. In order to achieve the goals agreed upon in the Paris Agreement, Europeans are working to reduce the carbon footprint of their crackers. In the short term, that means improving the efficiency of the furnaces. For the future, efforts are underway to develop new, alternative ways for making olefins, including the use of electricity derived from solar or wind power generation.
Steam-cracker trends
“One main trend has been the increase in the size of plants worldwide,” says Jim Middleton, manager of Technology and Ethylene Product Line Leader, TechnipFMC plc (London, U.K.; www.technipfmc.com). “Clients have been aiming to maximize the size of plant that can be designed as a single train, to maximize economies of scale.” Plants producing 1.5–1.8 million tons/yr of ethylene from liquid and mixed-feed crackers, and 1.5–2.0 million ton/yr of ethylene from ethane gas crackers are becoming the norm for producers who are not feed- or product-constrained, he says.
“In North America, the focus has been on producing ethylene from ethane derived from shale gas, and on capital efficiency. Elsewhere in the world, the focus has been mainly on naphtha, and particularly on an increasing proportion of LPG [liquefied petroleum gas] feeds,” continues Middleton. “In both Asia and Europe, some world-scale cracker projects are being designed based on imported ethane feedstock,” adds Dennis Mayfield, vice president Process Technology, TechnipFMC. “In the Middle East, the trend reflects the shortage of ethane availability, directing the investment into liquid feed or mixed ethane and liquid feed steam crackers. Ethane crackers in this region are expected when LNG [liquefied natural gas] producers expand their production facilities,” contributes Yvon Simon, head of Technologies Department, TechnipFMC.
“[Petroleum] refinery operators outside the U.S. have been looking to move into the production of olefins to maintain capacity in response to the anticipated slow growth in the demand for fuels,” says Middleton. “There is a trend to develop integrated refineries and steam cracker complexes or petrochemical refineries. The ultimate development of such a trend is the crude-to-chemicals concept. Oil-to-chemicals projects have been discussed, but few of these projects have moved to the implementation stage,” says Simon.
“In Europe, the focus is on sustainability, particularly CO 2 reduction and capture, energy efficiency and recycling of plastics,” says Middleton.
Steam-cracker improvements
“TechnipFMC has developed and implemented two particular new patented developments in furnace radiant coils — a Three Lane coil design and a Swirl Flow Tube design. Both of these offer improved run lengths and/or capacity for cracking furnaces. Both of these developments are in commercial operation,” says Middleton.
“Radiant coil designs have evolved over the past few decades to meet greater industry demands,” explains Mayfield. “This journey has been characterized by numerous small steps, as well as several vital, groundbreaking innovations. The triple-lane concept is the latest development in this lineage. It has several merits over preceding and competing developments, including: it reduces peak tube-metal temperatures; it is a simple and elegant way to improve run length, capacity and selectivity; it can be applied in revamps and new furnaces; and it is suitable for all cracker feeds, from ethane to VGO [vacuum gas oil],” says Mayfield.
“TechnipFMC sees improving the sustainability of cracking technology to be a key area of improvement in the next few years. In the medium term, moving to the use of more sustainable energy sources and reduction in fuel firing (and therefore CO2 emissions) is seen as the path the industry will follow,” says Middleton. “In addition, for some locations, the capture and storage of CO2 will also be an option. In the longer term, methods of producing olefins without firing fuel (such as electric heating) may become viable, but it is important that these do not move the generation of CO2 from the cracker to outside energy sources,” he says.
TechnipFMC has been a key participant in the Improof project — a four-year European project aimed at improving the energy efficiency of steam cracking furnaces by at least 20%, while reducing emissions of greenhouse gases and NOx by at least 25%. “A new patented furnace design has been developed by TechnipFMC which exceeds these objectives,” says Middleton. The project, with seven industrial partners, including Technip, Dow and John Zink Company LLC, and two universities, runs through August 2020.
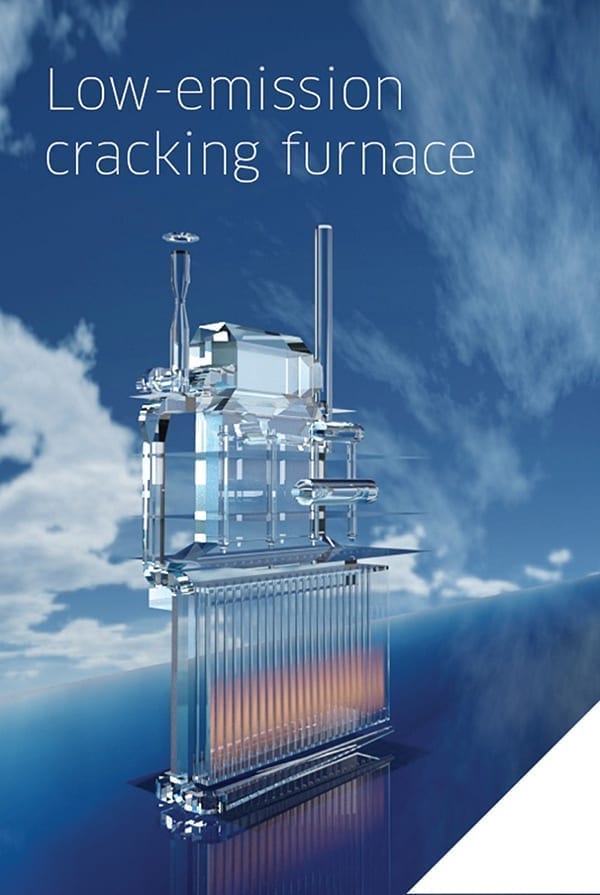
Figure 2. TechnipFMC has developed a new patented furnace design that exceeds the emissions reductions targets of the European Improof Project. TechnipFMC
Electrifying possibilities
As the availability and reliability of renewable electricity increases, and its costs fall, the chemical process industries (CPI) are looking for ways to electrify production, when possible, to not only reduce operating costs, but to reduce their environmental footprint. Because steam crackers are a major source of CO2 emissions, petrochemical companies are now looking for ways to electrify.
In Europe, one such effort began last August with the formation of the “Cracker of the Future” Consortium. Six petrochemical companies in Flanders, Belgium, North Rhine-Westphalia, Germany, and the Netherlands (Trilateral Region) created the consortium to jointly investigate how naphtha or gas steam crackers could be operated using renewable electricity instead of fossil fuels. The Cracker of the Future consortium, which includes BASF, Borealis, BP, LyondellBasell, SABIC and Total, and is chaired by Brightlands Chemelot Campus (Sittard-Geleen, the Netherlands; www.brightlands.com), aims to produce base chemicals while also significantly reducing carbon emissions. The companies have agreed to invest in R&D and knowledge sharing as they assess the possibility of transitioning their base chemical production to renewable electricity.
Following the signing of the agreement, the members of the consortium have begun exploring and screening technical options. If a potential technical solution is identified, the parties will determine whether to pursue joint development project(s), including R&D activities that could include a demonstrator for proof of concept in the case of base chemicals. “They are working very hard together, but it is too early to talk about specifics,” says Lia Voermans, director of Innovation Strategy, Brightlands Chemelot Campus.
Already in 2018, BASF SE (Ludwigshafen, Germany; www.basf.com) had begun its own five-year research project to develop the world’s first electrical heating concept for steam crackers. When the concept was first publicized at a press event in January 2019, Kiara Kochendörfer, the project leader for clean high-temperature processes, pointed out that the switch from fossil-fuel-fired cracker furnaces to the E-Furnace using renewable energy (solar, wind, battery) would cut CO2 emissions by 90%. BASF is working together with partner Linde Engineering (Munich, Germany; www.linde-engineering.com).
Because the concept is new, the researchers are “entering unknown territory of high Ampere [current] and low voltage,” explained Kochendörfer. Among the challenges are metallurgical — finding the right materials for the cracker coils that can handle operation at 1,000°C.
Meanwhile, progress continues on the development of a completely new cracker concept from Coolbrook Oy (Helsinki, Finland; www.coolbrook.fi). The patented RotoDynamic Reactor (RDR) technology has the potential to improve ethylene yields by 34% compared to conventional furnace-based naphtha crackers, according to Coolbrook CEO Harri Johannesdahl.
RDR is a regenerative turbomachine (Figure 3) consisting of three axial blade rows (stator, rotor and diffuser) and a toroidal vaneless space that circumferentially connects the blade passages, which allows the regenerative heating of the working fluid, explains Johannesdahl. The fluid is accelerated in the stator, and the mechanical energy is converted to internal energy of the fluid by the rotating blade row, thereby increasing the temperature and pressure of the fluid. Unlike conventional crackers, which heat the fluid from outside the furnace, the RDR is heated from within the reactor. As a result, the residence time inside the RDR is just 0.02–0.04 s, which is about one tenth of that achieved in conventional crackers, says Johannesdahl. In this short time, the high temperature (over 900°C) and pressure (1–3 barg) reached in the RDR efficiently pyrolyzes naphtha with a high ethylene yield (over 43%) — 34% higher than conventional crackers, he says.
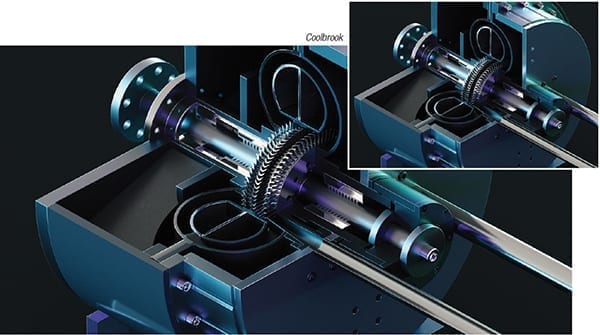
Figure 3. Coolbrook’s RotoDynamic Reactor has the potential to improve ethylene yields by 34%, compared to furnace-cased naphtha crackers. The regenerative turbo machine (closeup, upper right) can be motor driven using renewable electricity, thereby reducing CO2 emissions from the cracking process by 70%
The company recently completed a two-year project (Chem. Eng., May 2017, p. 9; www.chemengonline.com/piloting-revolutionary-approach-olefin-cracking), and is now investing €12 million to scale up the reactor from 90 kg/h (the R&D reactor) to 500 kg/h, with startup planned for this fall. The new plant, together with the company’s R&D hub, have now moved to Brightlands Chemelot Campus.
The current RDR eReactor design will be driven by an electric motor, thus permitting electrification of the cracking process, says Johannesdahl. The yield benefit remains what was reported in 2017, says Johannesdahl, but now the CO2 emissions from the cracking process are reduced by 70% and energy consumption is 21% less, he says.
“As Coolbrook’s revolutionary RDR technology has multiple benefits compared to any known technology in use or under development, all the major petrochemical companies, including ‘Cracker of the Future’ consortium, have expressed their interest on this technology,” says Johannesdahl. “Since RDR can be a breakthrough technology in the battle against the CO2 emissions, Coolbrook is working hard to get a large cluster of different stakeholders behind its technology to guarantee as fast and efficient market entry as possible,” he says.
Waste plastics as feedstock
“Various trials are planned to use recycled plastic waste as cracker feedstock,” says TechnipFMC’s Middleton. “The limitations on the extent to which this can be achieved are mainly associated with the logistics of reclaiming recycled plastics and the energy required for recycling by pyrolysis,” he cautions. “Another issue that is not yet fully developed is the range of contaminants that may be present in the recycled plastics, which can have an adverse effect on cracker product quality and catalyst life.”
“In Europe and SE Asia, the use of such recycled feed is expected to become more common in the next few years, but the logistics of waste collection is expected to mean that this will only form a relatively small proportion of cracker feedstock,” says Middleton.
For example, as part of its ChemCycling project, BASF SE (Ludwigshafen, Germany; www.basf.com) is already piloting the manufacturing of some products based on chemically recycled plastic waste (Chem. Eng., March 2019, pp. 14–18; www.chemengonline.com/chemical-recycling-makes-waste-plastic-resource). BASF feeds oil derived from plastic waste into its Verbund production site. BASF gets this feedstock for the pilot products from the partner Recenso GmbH (Remscheid, Germany; www.recenso.eu). The first batch of this oil was fed into the steam cracker at BASF’s site in Ludwigshafen in October 2018.
Recenso operates an industrial-scale pilot facility that uses its catalytic tribochemical conversion (CTC) process to convert municipal waste into a liquid oil. In the process, metals, stone and wet materials are first separated from the waste. The resulting material, predominantly plastic films, foils, paper and some biomass, is then fed to a slurry reactor, where it is heated by friction to around 350°C, and catalytically cracked into a pyrolysis gas. The vapor is condensed into a liquid oil that can be used as a fuel, or as a feedstock to a steam cracker, as is being done at BASF.
In a related project, Dow last August reached an agreement with Fuenix Ecogy Group (Weert, the Netherlands; https://fuenix.com), for the supply of pyrolysis oil feedstock, which is made from plastic waste (Chem. Eng., November 2019, pp. 12–14; www.chemengonline.com/new-era-sustainable-supply-chains). The feedstock is being used to produce new polymers at Dow’s production facilities at Terneuzen, the Netherlands. The polymers produced from this pyrolysis oil will be identical to products produced from traditional feedstocks, and as such, they can be used in the same applications, including food packaging.
Meanwhile, a process that directly converts waste plastic into gaseous building blocks is being developed by a research group at Chalmers University of Technology (Gothenburg, Sweden; www.chalmers.se). This gasification process avoids the need to first convert plastic waste to a pyrolysis oil that can be fed to an existing steam cracker, and instead, directly cracks the plastic waste into gaseous building blocks that can operate in parallel with existing crackers to make new plastics. The new process could transform today’s plastic factories into recycling refineries, within the framework of their existing infrastructure, according to the researchers.
The process is essentially a type of steam cracking of the waste plastics. Using experience gained from a first-of-its kind plant that gasified biomass into biomethane, the group has been working to apply this technology — a dual fluidized-bed (DFB) system — for steam cracking of waste plastics.
“Through finding the right temperature — which is around 850°C — and the right heating rate and residence time, we have been able to demonstrate the proposed method at a scale where we turn 200 kg of plastic waste an hour into a useful gas mixture, which can then be recycled at the molecular level to become new plastic materials of virgin quality,” says Henrik Thunman, professor of Energy Technology.
The experiments— reported in a recent issue of Sustainable Materials and Technologies — were carried out at the Chalmers Power Central facility in Gothenburg, using a DFB system. The first commercial use of a DFB-type system has been the fluid catalytic cracking (FCC) reactor in the petroleum-refining industry, which uses gaseous feedstocks and consists of two interconnected circulating fluidized beds, explains Teresa Berdugo Vilches, a postdoctoral researcher in the Dept. of Space, Earth and Environmental Energy Technology, at Chalmers. “The DFB system developed at Chalmers consists instead of a bubbling bed connected to a circulating fluidized bed, and it is designed to handle solid feedstocks. It differs from a conventional circulating fluidized bed in the fact that it has two reaction environments: the bubbling bed that serves as a cracking reactor of solid plastic particles, and the circulating fluidized bed that serves as a combustor, she explains. “It was developed for gasification of woody biomass and it has now been applied for the cracking of plastics.”
“We are now moving on from the initial trials, which aimed to demonstrate the feasibility of the process, to focusing on developing more detailed understanding,” says Thunman. This knowledge is needed to scale up the process from a few metric tons of plastic a day, to hundreds of metric tons. That is when it becomes commercially interesting,” says Thunman.
The process is said to be applicable to all types of plastic that result from our waste system, including those that have historically been disposed in landfills or at sea.