Pressure swing adsorption technology is well known for H2 purification applications, but the technique can also be used for other gas-separation processes in petroleum refining facilities
Pressure swing adsorption (PSA) is a well-established process for the separation and purification of a wide range of industrial gases. PSA is generally safe, reliable and cost effective. In the petroleum refining industry, PSA systems are used to produce hydrogen from synthesis gas that is produced by steam-methane reforming (SMR), partial oxidation (POX) or gasification.
Although well known for H2 purification, PSA technology can also be used for other gas-separation tasks. PSA systems can be used to recover H2 from refinery offgases, to capture CO2, and to generate O2 and N2 gases. This article provides an overview of PSA technology, including the scientific principles that dictate how it works, along with design considerations of PSA systems. In addition, the article summarizes how PSA technology can be used in several other petroleum-refinery applications beyond H2 purification and the potential economic benefits that can be realized with this approach.
Selecting the best technology for a given gas-separation problem requires a thorough understanding of the available production technologies, including SMR, POX and gasification, as well as available separation technologies, such as membrane, cryogenic, absorption and adsorption. Identifying the optimal solution, and whether PSA technology could be a benefit, also requires a detailed knowledge of the capital and operating costs for the relevant process.
PSA principles
PSA technology is based on a physical binding of gas molecules to a solid adsorbent material. The adsorbent material can be a combination of activated carbon, silica gel, carbon molecular sieves and zeolites. The attractive forces between the gas molecules and the adsorbent material depend on the gas component, the type of adsorbent material, the partial pressure of the gas component and the operating temperature. Highly volatile compounds with low polarity, such as H2 or He, are essentially not adsorbed at all compared to molecules such as CO2, CO, N2 and hydrocarbons. The relative attractive force of various gas molecules with a typical adsorbent material is shown in Figure 1.
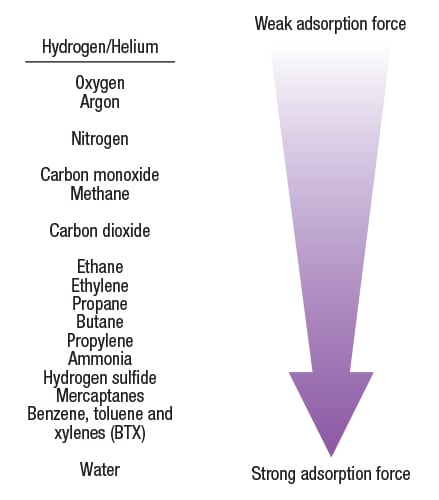
Figure 1. Highly volatile compounds with low polarity are not adsorbed onto the adsorbent material in a PSA system
The PSA process works at basically constant temperature and uses the effect of alternating pressure and partial pressure to perform adsorption and desorption. Since heating or cooling is not required, cycle time can be short — in the range of minutes. Furthermore, heat is not required for the regeneration of the adsorbent. Changes in temperature are caused only by the heat of adsorption and desorption and by depressurization. This results in an extremely long lifetime of the adsorbent material.
The PSA process works between two pressure levels. Adsorption of impurities is carried out at high pressure to increase the partial pressure of the undesired gases and, therefore, to increase the loading of the impurities onto the adsorbent material. Desorption, or regeneration, takes place at low pressure to reduce the residual loading of the impurities as much as possible.
Most PSA systems are based on equilibrium considerations. A typical equilibrium isotherm is shown in Figure 2. Adsorption isotherms show the relationship between partial pressure of a gas molecule and its equilibrium loading on the adsorbent material at a given temperature.
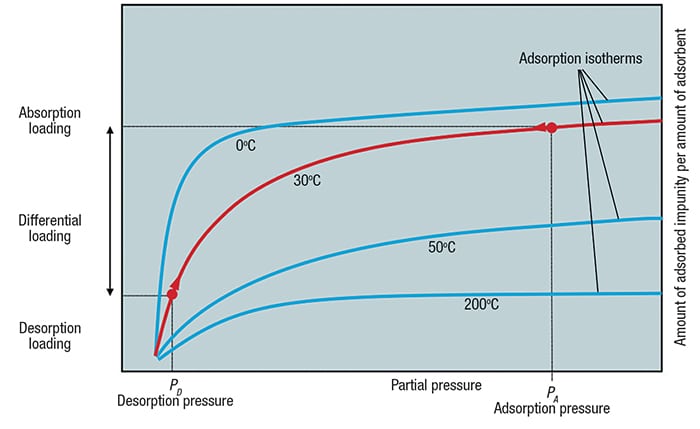
Figure 2. Adsorption isotherms show the relationship between partial pressure of a gas molecule and its equilibrium loading on the adsorbent material at a given temperature
Adsorption is carried out at high pressure — typically in the range of 10 to 40 bars — until equilibrium loading is reached. At this point, the adsorbent material must be regenerated in order to avoid impurity breakthrough to the product. This regeneration is done by lowering the pressure to slightly above atmospheric pressure, resulting in a corresponding decrease in equilibrium loading. As a consequence, the impurities on the adsorbent material are desorbed and the adsorbent material is regenerated. The amount of impurities removed from a gas stream in one cycle corresponds to the difference in the adsorption-to-desorption loading.
PSA system operation
A simplified schematic diagram of a H2 PSA system is shown in Figure 3. An actual PSA operation is shown in Figure 4. The main process steps in a PSA operation, including adsorption, desorption and pressure equalization, are described below. Adsorption. The feed gas is fed upward through the adsorber vessels. The impurities, including water, heavy hydrocarbons, light hydrocarbons, CO and N2, are selectively adsorbed in the vessel from the bottom to the top. High-purity H2 flows to the product line.
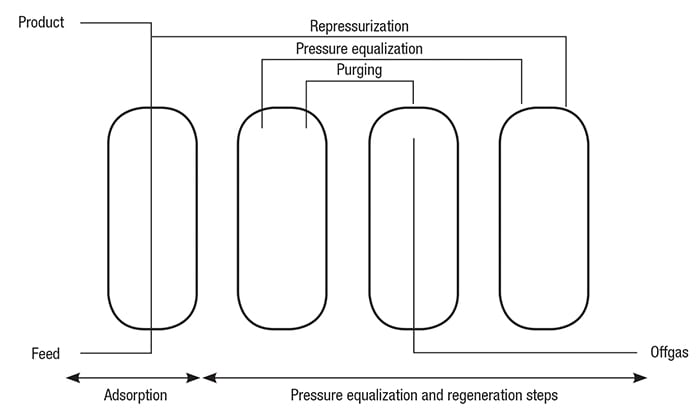
Figure 3. The main process steps of a typical PSA system, including adsorption, desorption and pressure equalization, are shown here
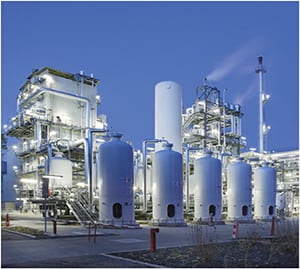
Figure 4. Most PSA systems, such as the one shown here, are used for separating hydrogen from a gas mixture (Photo courtesy of BASF SE)
In the adsorption cycle, the adsorber vessels are placed on staggered cycles, resulting in a highly flexible purification unit that is not influenced by fluctuations in the composition, temperature and pressure of the feed gas stream.
The PSA system allows high performance by ensuring maximum utilization of the H2 stored in an adsorber at the end of the adsorption cycle. The stored H2 can be used for pressure equalization, repressurization and purging of other adsorbers.
Regeneration. Once the adsorption step is completed, the adsorber vessel is regenerated by the following four steps:
- Depressurization to a low-pressure level co-current to the feed flow. The co-current depressurization uses the hydrogen stored in the adsorber to repressurize and purge other adsorber vessels
- Depressurization in the countercurrent direction to tailgas pressure (blowdown step) to remove the impurities from the adsorbent
- Purge is carried out at tailgas pressure with pure hydrogen to desorb the residual impurities from the adsorbent Repressurization adsorption pressure with pure H2 coming from adsorbers
Pressure equalization. In order to recover most of the H2 stored in an adsorber at the end of the adsorption step, several pressure equalizations are performed before starting regeneration of the gas.
After termination of the regeneration step, the pressure is increased back to the adsorption pressure level, and the process starts again from the beginning.
A typical PSA unit includes the following major components:
- Prefabricated valve skid
- Adsorber vessels
- Specially selected adsorbent material
- Tailgas drum
- Process control system
The scope of the PSA system can be altered to suit specific needs. For example, a feed-gas compressor or tailgas compressor can be included as an integrated solution.
One of the important requirements of a PSA system is the process control system. The key recommended features are listed below:
- High-purity H2 at constant flow and pressure
- Automatic adjustments to pressure and flow fluctuations of the feed gas
- High H2 recovery by optimizing equalization and purge steps
- Low sound emissions
Sophisticated software programs can safely control all switching, and control valves can provide a very efficient process cycle.
Refinery applications
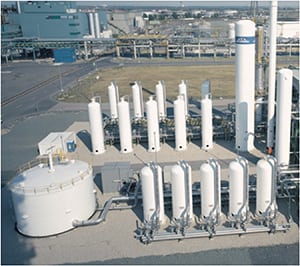
Figure 5. The plant scene depicted here shows a system for recovering CO2 from the tailgas of a H2 PSA system (Photo: Linde Engineering)
The following section summarizes several applications for PSA systems at petroleum refineries, including H2 separation, and several others that are not as widely used.
Hydrogen separation. The main application for PSA in a refinery is the recovery and purification of H2 from gas streams, such as synthesis gases from steam reforming, POX or gasification, as well as from refinery offgases. The H2 product can be obtained at high purity — up to 99.9999% — and high recovery rates of up to 90%.
CO2 separation. PSA systems and vacuum-regenerated pressure swing adsorption systems (VPSA) can be employed for the bulk removal of CO2. PSA/VPSA plants can also be used for the recovery and purification of CO2 for liquefaction. A recent example of a PSA system used to recover CO2 from the tailgas of an H2 PSA system is shown in Figure 5. The H2 PSA is a ten-bed system, and the CO2 PSA is a five-bed system. The plant shown has a capacity of 48,000 Nm3/h (normal cubic meters per hour) of H2 and 8,000 Nm3/h of CO2.
C2+ separation. Refinery offgas (ROG) streams containing H2, C1, C2 and heavier (C2+) hydrocarbons are usually available in refineries. These streams are often used as fuel. It is possible to process these gas streams and recover C2+ by PSA or VPSA as a way to capture greater value of C2+, which can then be used as a chemical feedstock. In this case, the C2+ fraction is recovered on low pressure, while H2 and methane will stay on the high-pressure side. Several units have been placed into commercial operation and have been effective.
O2 and N2 generation. In a petroleum refinery, low-purity O2 can be used to enrich the combustion air in fluid catalytic cracking (FCC) and sulfur recovery unit (SRU) operations. The production of gaseous oxygen at capacities of up to 10,000 Nm3/h and purities of 90–94% can be most effectively achieved by VPSA processes. This method offers low specific-energy consumptions and operational simplicity, including simple startup and turndown capability.
Nitrogen is used in a refinery for inerting and blanketing. PSA systems can also be used to generate N2 at capacities up to 5,000 Nm3/h and purities of 98–99.9% (and higher).
Unlike H2 PSA, CO2 PSA and O2 VPSA systems, the N2 PSA system is based on the difference in the kinetics of adsorption of O2 onto carbon molecular sieves.
Economic benefits
In the field of CO2 removal and recovery, or purification, and for C2+ recovery, the technologies currently best known in the market are absorption units and cryogenic units. However, recent developments have made the recovery of CO2 or C2+ technically feasible and economically viable with PSA technology. Respective reference plants have already been put into commercial operation and have proven the concept on an industrial scale.
The advantages of using PSA for these tasks, compared to other technologies, are low energy consumption, high purity levels, huge flexibility and comparatively low investment and maintenance costs. Selecting the most appropriate PSA technology can improve the overall profitability of a petroleum refinery by reducing costs and providing improved reliability, flexibility and environmental performance.
The key requirements and potential benefits of PSA systems are listed here:
Quality. The high switching cycles of PSA units require special equipment distinguished by a high degree of durability. It is essential to use only qualified components, which meet these demands perfectly and which have been proven over many years of experience.
Reliability. The use of suitable components, especially high-performance switching valves, provides high reliability.
Availability. High H2 availability is essential for most refinery applications. With special features, such as the ability to operate with a reduced number of adsorbers, as well as adsorber group isolation and a redundant control system, PSA units can achieve virtually 100% on-stream performance and availability.
Flexibility. Excellent flexibility to cope with changing feed gas conditions and varying H2 demand.
Modular design and prefabricated equipment. PSA systems are generally prefabricated to the maximum extent. The valve skids containing switching and control valves, instrumentation and interconnecting piping are completely prefabricated, preassembled and tested prior to delivery. This design philosophy reduces the time and costs needed for construction and commissioning onsite, keeping them to a minimum.
Easy maintenance. Maintenance is limited to easy and quick routine actions that can be carried out by the operators onsite. Attention is given to a proper accessibility of all valves and instruments inside the valve skid.
Concluding remarks
PSA technology can be used for much more than just recovering H2. In some applications, such as the recovery of CO2 or C2+ streams, PSA technology has certain distinct advantages compared to the more commonly used cryogenic or washing processes.
The advantages of PSA compared to other technologies are the low energy consumption, high purity levels, huge flexibility and comparatively low investment and maintenance cost. Selecting the most appropriate PSA technology can improve the overall profitability of a refinery by reducing cost and providing improved reliability, flexibility and environmental performance. Specialists can help to select the optimum PSA system for a specific purification task, in terms of the optimum ratio between plant performance and investment cost.
Edited by Scott Jenkins
Further reading
Shahani, G.H. and Kandziora, C., CO2 Emissions from Hydrogen Plants: Understanding the Options. Lecture presented at the 2014 AFPM Annual Meeting, Orlando, Fla., March 23–25, 2014.
Adsorption Plants, Linde Engineering, Webpage found at www.linde-engineering.com, accessed November 2015.
Authors
Tobias Keller is executive vice president for adsorption and membrane plants at Linde Engineering (Carl von Linde Strasse, 6-14, 82049, Pullach, Germany; Phone: +49 89 7445 0; Email: [email protected]). He is responsible for Linde Engineering’s adsorption and membrane activities worldwide. Keller holds a Dipl. Ing. degree in process engineering from the University of Cottbus, Germany and has 15 years of experience in the chemical and petroleum refining industries.
Goutam Shahani is vice president of sales and marketing at Shure-Line Construction (281 West Commerce Street, Kenton, Del.; Phone: 302-653-4610; Email: [email protected]). Previously, he was business development manager at Linde Engineering North America. With over 30 years of industry experience, Shahani specializes in industrial gases for the energy, petroleum refining and chemical industries. He holds B.S.Ch.E. and M.S.Ch.E. degrees, as well as an MBA.