Using the hierarchy of controls can help guide housekeeping and safety programs to better protect employees and facilities
There is a close link between safety and housekeeping for all manufacturers, but facilities that store, handle or process chemicals have an even greater responsibility when it comes to housekeeping and safety. Due to the nature of the materials being processed, industrial hygiene and safety practices must be top notch because they protect employees, communities and the environment from the substances used onsite. For this reason, it’s important to employ typical housekeeping practices, such as spill cleanup, as well as necessary engineering controls, such as dust and fume collection and personal protective equipment (PPE).
“Safety and good housekeeping go hand in hand,” says Dan Silver, vice president of product development with New Pig Corp. (Tipton, Pa.; www.newpig.com). “Having a clean, dry work space that’s free of clutter reduces the chances of a workplace accident. Also, when working with chemicals, leaks, drips and spills are inevitable. Every facility should have a spill response program in place and trained responders with spill response kits ready. Good housekeeping practices like these mean employees can focus on their work without navigating through the landmines of clutter or potentially dangerous spills and debris,” says Silver (Figure 1).
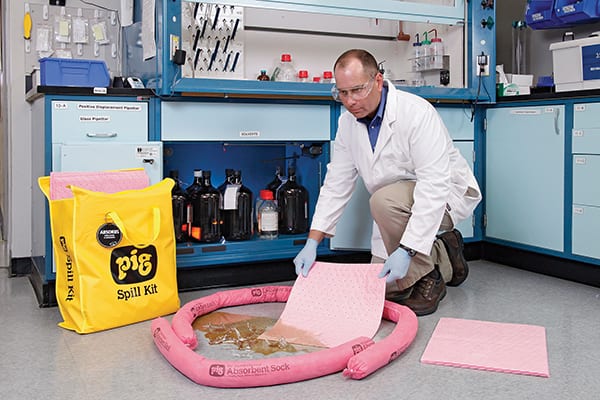
Figure 1. When working with chemicals, leaks, drips and spills are inevitable, so every facility should have a spill response program in place and trained responders with spill response kits ready New Pig
In specialized facilities, such as chemical processing plants, it is important to remember that safety, hygiene and housekeeping are intertwined, as safety is a discipline that is rooted in an organized and systematic approach to hazard and risk assessment, says Tim Zeh, safety director with Fisher Scientific (Pittsburgh, Pa.; www.fishersci.com). “With respect to chemicals, poor hygiene can elevate the risk of working with hazardous chemicals, whether in a laboratory or on a production scale,” he says. “A major portion of the Occupational Safety and Health Administration’s [OSHA; Washington, D.C.; www.osha.gov] Laboratory Standard (29 CFR 1910.1450) specifies the mandatory Chemical Hygiene program as an example of how important hygiene is as an underpinning to a safety program.”
Zeh adds: “However, putting the system in place is only the first step, refresher training and updating programs are really the only way to maximize the effectiveness of the hygiene and housekeeping system.”
So, how does a chemical processor determine what their safety, hygiene and housekeeping system should include? “Leading companies do not limit housekeeping to just general areas or have a one-size-fits-all approach,” says Bob Balderson, senior manager, Corporate EHS at W.W. Grainger, Inc. (Lake Forest, Ill.; www.grainger.com). “They not only have practices in place for maintaining walking and working surface areas, but they also perform risk assessments on the specific type of operations and work practices onsite and, as a result, develop detailed, specific housekeeping practices, schedules and controls for those areas.”
Risk assessment and hierarchy of controls
Mark Tartaglia, senior CIH consultant with DuPont Personal Protection (Wilmington, Del.; www.safespec.dupont.com), says the first step in creating a solid housekeeping, hygiene and safety plan is performing a hazard risk assessment as directed by OSHA and then applying the hierarchy of controls to each risk. “The employer must perform a hazard risk assessment that looks at particular tasks, activities and operations within the facility and evaluate each for all the potential hazards that exist in order for the worker to perform that work and then apply the hierarchy of controls to eliminate or reduce those risks.”
According to OSHA, one of the root causes of workplace injuries, illnesses and incidents is the failure to identify or recognize hazards that are present or could have been anticipated. A critical element of any effective safety and health program is a proactive, ongoing process to identify and assess hazards. To do so, the agency suggests:
- Collecting information about present or likely to be present hazards
- Conducting inspections to identify new or recurring hazards
- Investigating injuries, illnesses, incidents and close calls to determine the underlying hazards, causes and safety and health program shortcomings
- Group similar incidents and identify trends
- Consider hazards associated with emergency situations
- Determine the severity and likelihood of incidents that could result for each hazard and use this information to prioritize corrective actions
Once a risk has been identified, it is suggested that OSHA’s hierarchy of controls be applied to mitigate these risks and prevent accidents from happening in the future. The hierarchy of controls is a pyramid (Figure 2) with “elimination or substitution” at the top. This step aims to eliminate exposure before it occurs or substitute a less hazardous material in the process, requiring a permanent change to the process or job. “A good example of this would be in the paints and coatings industry where many manufacturers have made the move away from solvent-based products to water-based,” says Tartaglia. “This reduced the hazards by substituting a lower-hazard material in place of a higher hazard [one].”
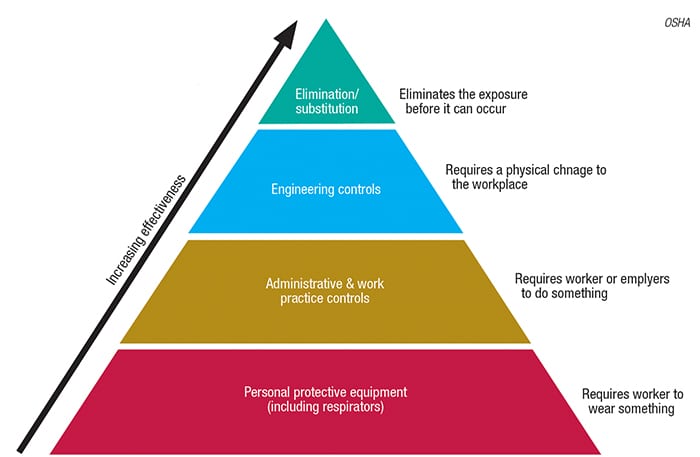
Figure 2. OSHA’s hierarchy of controls should be applied to mitigate risks and prevent accidents from happening in the future
The next step down the pyramid is “engineering controls,” which requires a physical change to the workplace. An example would be vapor, dust or fume collection equipment to mitigate vapor, dust or fume dangers that range from annoyances to health hazards to explosion risks.
The third layer of the pyramid is “administrative and work practice controls,” which requires implementing procedures that require a worker to do something to reduce the risk. An example would include being prepared for spills and having practices in place to handle anything from cleaning up a minor spill to handling a major hazardous spill incident.
Finally, “personal protective equipment,” at the base of the pyramid, is considered “the last line of defense,” according to Tartaglia. “Employers should depend on PPE after implementing other means of exposure controls in order to control residual risks.” The necessary equipment will depend upon the risk, but may include eye and face protection, gloves, respirators and/or protective garments.
“A proper risk assessment helps develop an understanding of risks and exposures in the specific chemical processing work environment,” says Grainger’s Balderson. “Once risk is assessed, decisions can be made based on the hierarchy of controls: Can the hazard be eliminated altogether? Can you substitute the hazard? Can an engineering control be applied? Can administrative controls be developed and effective? And lastly, can PPE be used as a control? Many times it may be a combination of several control methods used, but having proper understanding of the risk involved is critical in selecting effective controls.”
When considering the various controls and their application to support housekeeping and safety, there is an abundance of products on the market, says Balderson. Whether the controls are proper flooring selection, secondary containment systems, absorbent matting, spill response/containment kits or controls in the form of flammable and chemical storage cans, containers and cabinets or providing the correct PPE, the key to selecting an effective control is ensuring it addresses the specific risk within the operation as determined by the risk assessment. “One support resource is the suppliers and manufacturers of these equipment controls, as they have experts on staff to support chemical processing facilities with assessments and identify the appropriate controls specific to the work environment,” he says.
While this article explores the importance of dust collection, spill control and containment, and PPE as they fit into the hierarchy of controls, remember every facility will have different and additional equipment and housekeeping needs based upon the specific risks found during the risk assessment.
Engineering controls
When elimination or substitution isn’t an option, engineering controls become necessary. One of the biggest areas of concern for chemical processors is dust and fume collection as they pose risks ranging from slips and falls to illness to explosion.
Poor air quality can cause problems beyond inhalation risks, says Greg Carmichael, vice president of sales with RoboVent (Columbus, Ohio; www.robovent.com). Coolant mists create one of the greatest risks in a facility as they can accumulate on surfaces and cause slip-and-fall hazards. “Fortunately, specially designed air cleaners fitted with the right kind of filters can pull oil mists out of the air and prevent this problem.”
Another major risk, says Carmichael, is that of explosions caused by combustible dust. When this dust combines with oxygen in a certain proportion, a single spark can cause it to explode. Exhausting or filtering these dusts is crucial to ensure that they don’t accumulate in the air or on surfaces. Fire protection measures in the dust collection system can prevent sparks from penetrating the equipment or ductwork.
And, as all chemical processors know, chemical dusts carry special dangers for the employees who work with them, says Carmichael. Many have high concentrations of elements that are toxic in the body at certain concentrations. Other chemical dusts can react badly with body tissues or cause harm simply from accumulation (Figure 3).
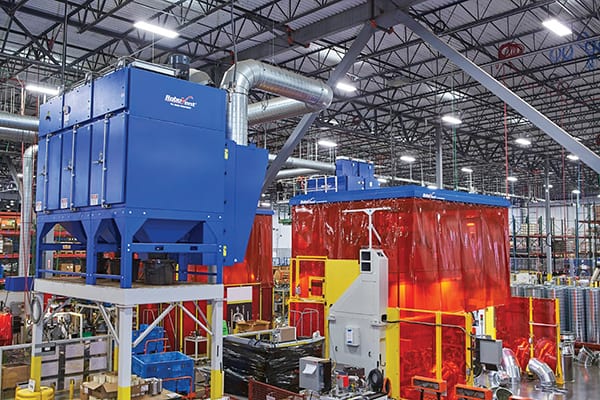
Figure 3. An air-filtration system ducted to multiple hoods keeps air cleaner, employees safer and equipment well-maintained in this robotic welding space RoboVent
The key to controlling dusts, mists and fumes is proper selection and installation of a dust or fume collection system, which includes a capture hood, piping and a collector that is specifically designed for the material being generated, says Curt Corum, sales manager with Air Handling Systems (Woodbridge, Conn.; airhand.com). “It’s important to first define the contaminant and particle size and then look at the point of discharge. The first goal is always source capture — to go right after where the material is generated — and select a properly sized capture hood.”
Next, according to the particle size, there are different air-speed requirements to convey material from point A to point B via proper piping systems and ductwork. Finally, the selected collection device must be appropriate to the size of the particle, type of material and potential hazards.
“The proper three are the key to safely collecting dusts and fumes in any facility,” says Corum. “This means when hooding, piping and collection device are properly sized and engineered, it is possible to reduce hazards such as dust on the floor, health hazards or explosion hazards dramatically. Only in a perfect world do you get 100% of dust and fumes cleaned up, so for the remaining hazards there are self-contained air cleaners, as well as safety and housekeeping procedures to mitigate the remaining risk.”
Corum continues to say that the importance of clean air is great. “Cleaning up dust and fumes must be a high priority for processors. You can have PPE, safety training and everything else, but if you don’t clean up dust and fumes, you end up with sick people and explosion hazards. Once you control dust and fumes, all other safety items can fall into place around it.”
Work practice controls
Since slips, trips and falls cost business and industry more than $11 billion per year [according to Liberty Mutual Workplace Safety Index], it’s obvious that cleaning up leaks and spills is one area where proper work practices have a direct impact on safety, says Karen Hamel, regulatory compliance trainer with New Pig. “Using absorbent socks to surround a spill will keep liquid from spreading and turning a small problem into a bigger one. Once the spill is confined to one area, employees may be able to continue working safely while the spill is being cleaned up by spill responders. Using absorbent mat pads to clean up the contained liquid is much faster and easier than cleaning a spill with old-style loose clay-based absorbents.”
Susan Naser, vice president of sales with Spill Tech (Johns Creek, Ga.; www.spilltech.com) agrees that absorbents are essential to keeping a facility safe from hazards associated with spills. “Just as there are paper towels in your kitchen because you know you’re going to spill something, you have absorbents in your facility because you’re going to spill something,” she says. “For the chemical industry, this is especially important because there may be aggressive chemicals that can’t be cleaned up with a wipe or a rag, so they typically need three types of absorbents on hand — oil only, universal and hazmat — and they need to ensure that the chosen absorbent is compatible with the spilled material, which is where hazmat absorbents shine” (Figure 4).
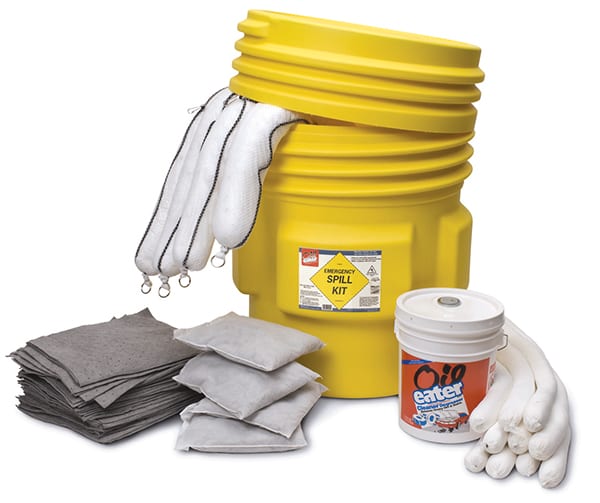
Figure 4. For the chemical industry, it is important to ensure that the chosen absorbent is compatible with the spilled material, which is where hazmat absorbents come in Spill Tech
She says these are typically made of polypropylene, which is compatible with most chemicals, and they are yellow so employees know to use caution around this spill. “Yellow is the international color for hazmat. They are very high visibility, which reduces the risk of slip and fall and lets people know there is an aggressive chemical spill, so they need the right PPE or to call the proper department for spill response.”
But in order for absorbents to do their job, there must be corporate commitment to safety that includes being prepared for spill response.
“Whether we are talking about small spills in a facility or a tanker letting loose, being ready with the proper materials and having a plan in place are key,” says Rick Morgando, brand manager with Kafko (Skokie, Ill.; www.oileater.com) (Figure 5). “This ensures that when it happens, the plan is already in place and you are prepared. If you aren’t ready, an accident can turn into catastrophe.”
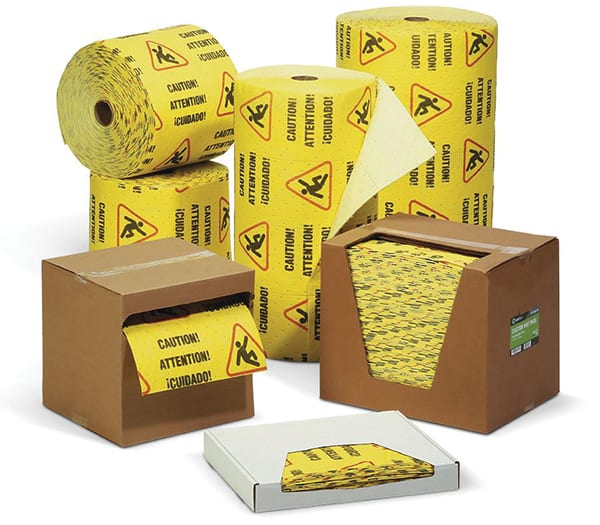
Figure 5. Whether it’s a small spill in a facility or a tanker letting loose, being ready with the proper materials, such as absorbents and spill kits, and having a plan in place are key Kafko
New Pig’s Silver agrees: “Proactive planning impacts spill control by requiring facilities to create plans, procedures and tools that focus on keeping chemicals where they are supposed to be: in their containers, in pipelines or in process. Although the focus is on not having spills, it is irresponsible to think they will never occur, so proactive planning involves being prepared. This is where spill containment and spill response tools and procedures come into play.”
Providing appropriate secondary containment or spill containment prevents spills from becoming releases. It buys the facility time to decide how best to handle the material that has spilled while it’s confined to a pre-determined area. Without secondary containment, spills can quickly escalate from an inconvenience to an emergency. They can also have much larger impacts on the safety of employees as well as the surrounding community, notes Silver.
Personnel protective equipment
Since PPE is the last line of defense, it’s important for processors to know the two key PPE safety challenges: ensuring that the workforce has the proper PPE from head to toe to protect them from the chemicals they are working with or exposed to and, that in the event of an industrial spill or accident, the PPE will help mitigate injuries incurred from exposure to the chemical, says Fisher Scientific’s Zeh.
“In my experience in the chemical industry, you see the full spectrum of hazards and typically need the full spectrum of PPE available on site, including full protective suits, respirators, goggles, gloves, fall protection, electrical safety equipment and so on,” says DuPont’s Tartaglia.
Chemical processors need to be especially careful that PPE such as gloves and garments are evaluated in terms of the materials’ ability to hold out chemicals for both permeation and degradation, as well as how PPE is constructed (garment seam construction, glove length, surface texture, and so on) to ensure that PPE works as a full system, notes Zeh from Fisher Scientific.
To determine what you need, Tartaglia says, most manufacturers offer tools for employers to help them choose an appropriate option for gloves, garments, respirators and so on, based on the risks identified in their facilities and the chemicals to which personnel are exposed. For example, DuPont offers a web-based tool called SafeSPEC (www.safespec.dupont.com) that aids employers in the selection of protective garments (and soon gloves for a new product line that will be introduced this year) (Figure 6).
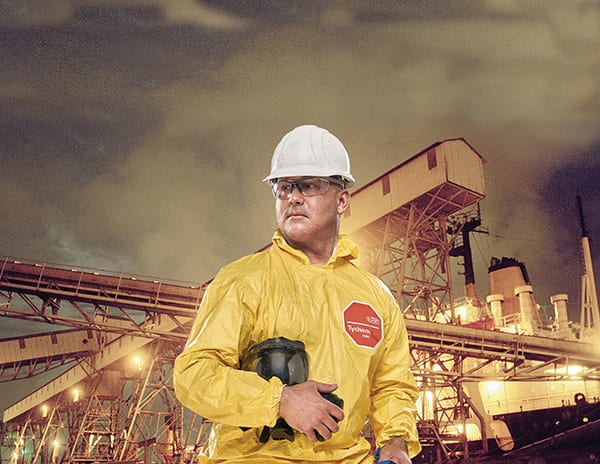
Figure 6. Chemical processing facilities often contain the full spectrum of hazards and therefore require the full spectrum of PPE available on site, including full protective suits, respirators, goggles, gloves, fall protection, electrical safety equipment and more DuPont
“The best options for PPE must be able to control exposures to acceptable levels and are considered the last option, since PPE requires user training, upkeep and are subject to human decisions on how effective they are,” says Zeh.
While these options for housekeeping and personnel safety are just the tip of the iceberg of what is necessary and available, in all cases, better housekeeping in a chemical facility has the ability to help “protect what matters most” — your people, products and the environment, says Zeh.