This column is based on “Propionic Acid Production from Propionaldehyde – Cost Analysis,” a report published by Intratec. It can be found at: www.intratec.us/analysis/propionic-acid-production-cost.
Propionic acid (also known as propanoic acid) is a carboxylic acid commonly found in nature, mainly in its ester form in some essential oils. This fatty acid is also formed in a number of enzymatic and fermentation processes. Widely used in the production of cellulose esters, plastic dispersions and herbicides, propionic acid has gained importance in recent years for applications related to preservation of forage-cereal crops and animal feeds.
The uses and applications of propionic acid vary according to the product grade. The main form of propionic acid is one with 99.5 wt.% minimum purity. Most industrially produced propionic acid is used as a preservative in stored animal feed and grain. Examples of its agricultural applications include its uses as the following: an antibacterial additive (for livestock and poultry drinking water); a surface sanitizer (in storage areas for silage and grain); a poultry-litter additive; and for use with high-moisture grains in indoor storage. To a lesser extent, propionic acid is also used as a food additive and chemical intermediate for herbicides, pharmaceuticals, rubber products, plastics and plasticizers, among others.
The process
The present analysis discusses an industrial process for propionic acid production. The process comprises two major sections: (1) propionaldehyde oxidation; and (2) propionic acid separation (Figure 1).
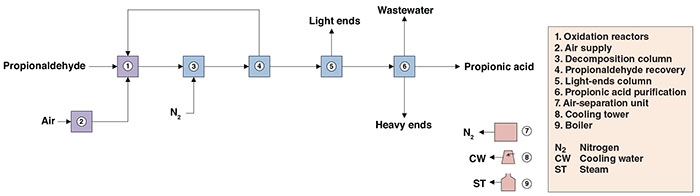
Figure 1. The process diagram shows propionic acid production via propionaldehyde oxidation
Propionaldehyde oxidation. Initially, propionaldehyde in the liquid phase is fed to three tube-and-shell reactors operating in series, where it is oxidized to propionic acid under mild pressures in the presence of air. Crude acid taken off at the bottom of the last reactor is routed to the separation and purification steps downstream.
Propionic acid separation. The crude acid is fed to a decomposition column, where perpropionic acid (contaminant) is decomposed by heating under positive nitrogen pressure. Then, unconverted propionaldehyde is recovered in a subsequent column and recycled to the oxidation reaction. The propionic-acid-rich stream is routed to a light-ends column for the removal of light impurities and high-purity propionic acid (99.5 wt.%) is finally obtained by azeotropic distillation using ethyl acetate as an entrainer.
Production pathways
At commercial scale, propionic acid can be produced through three main routes, including oxidation of propionaldehyde, depending on which raw starting materials are used. Propionic acid can also be produced by carbonylation of ethylene with carbon monoxide and water, and as a byproduct from the direct oxidation of hydrocarbons. Different pathways for propionic acid production are presented in Figure 2.
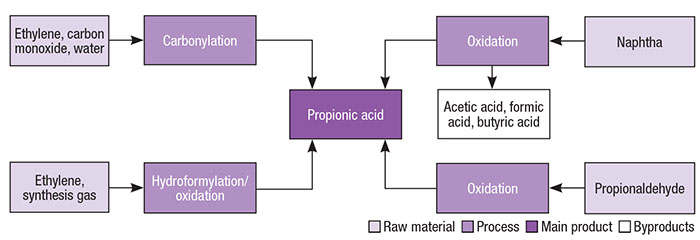
Figure 2. Propionic acid production pathways vary according to starting materials
Economic performance
The total operating cost (raw materials, utilities, fixed costs and depreciation costs) estimated to produce propionic acid was about $830 per ton of propionic acid in the fourth quarter of 2016. The analysis was based on a plant constructed in the U.S. with the capacity to produce 80,000 metric ton per year of propionic acid.
Edited by Scott Jenkins
Editor’s note: The content for this column is supplied by Intratec Solutions LLC (Houston; www.intratec.us) and edited by Chemical Engineering. The analyses and models presented are prepared on the basis of publicly available and non-confidential information. The content represents the opinions of Intratec only. More information about the methodology for preparing analysis can be found, along with terms of use, at www.intratec.us/che.