There are many occasions in chemical processing plants where electrostatic charge generation and accumulation can occur, potentially leading to fires and explosions. Engineers must understand these hazards and how to mitigate them
We are all familiar with the electrostatic shocks we receive at home or stores, perhaps from elevator buttons or shop displays, or when getting out of a car. These shocks are examples of “sparks” or sudden discharges of static electricity (Figure 1). They are a nuisance in a home setting, but in an industrial context, electrostatic discharges can and do cause many devastating flash fires and explosions. This is particularly true in the chemical process industries (CPI), where plants routinely handle flammable liquids and solids in ways that inadvertently generate static electricity. These materials are often flammable, of course, and they can be ignited by discharges of the static electricity that they have generated.
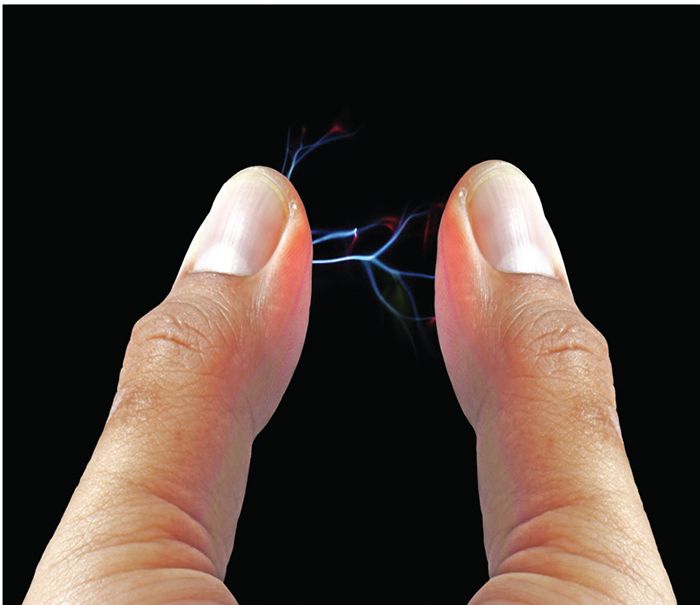
FIGURE 1. Electrostatic discharges are commonplace in many parts of life, but their presence in industrial settings can lead to destructive fires and explosions
Whenever any two surfaces contact and then separate, static electric charge is generated. Most static charge is generated when fast movement and pressure are applied between the contacting surfaces. In the CPI, static electricity is generated in many common processing operations, such as when liquids flow through pipelines in a plant or when powder particles contact the surfaces of processing and conveying equipment. Therefore, some processes, such as fluidized-bed drying and pneumatic transfer, for example, will frequently generate a great deal of static charge, as will fast, turbulent liquid flow, such as in tanker unloading or filtration operations.
The main concern posed by static electricity in an industrial setting is the risk of fire and explosion due to the ignition of flammable atmospheres by electrostatic discharges. Flammable gases, vapors, dust clouds and aerosols are commonly encountered in processing operations, and precautions are required to prevent their inadvertent ignition. Precautions against fire and explosion are many and varied, but an approach that should be included is the exclusion or elimination of potential electrostatic ignition sources from locations where flammable atmospheres may reasonably be expected to exist.
There are many precautions that can be taken to control static electricity, but the best way to decide the most appropriate method for controlling static electricity in your plant is to first understand how static charge is generated and accumulated, as well as how it produces hazardous sparks that must be avoided.
This article discusses how, when and where electrostatic charge is generated in the CPI, why it accumulates to produce dangerous discharges and what practical measures can be taken to control the risk of explosions and flash fires due to static electricity.
The theory of charge generation
There are a number of different mechanisms that explain the generation of electrostatic charge. These include contact electrification, double-layer charging and induction charging.
Contact electrification. A common way that materials become electrostatically charged in practice is through contact electrification — also known as triboelectrification. Contact charging occurs when any two materials come into contact and then separate. There is a rearrangement of electrons at the contacting surfaces where one surface is left with a surplus of electrons and is said to be negatively charged, while the other surface is left with a deficit of electrons and is said to be positively charged. Contact electrification occurs when, for example, powder particles collide or rub against the conveying chutes during pouring, and when the soles of footwear make contact with flooring. The level of charge that is generated by contact electrification is influenced by many factors, such as the chemical nature of the two contacting surfaces, the true contact area, contact pressure and surface conductivity. The handling and processing of bulk solids and powders typically result in the development of relatively high levels of static charge because many powders are electrically insulating (high resistivity), and powders have a relatively large surface area per unit mass available for contact electrification to take place (Figure 2).
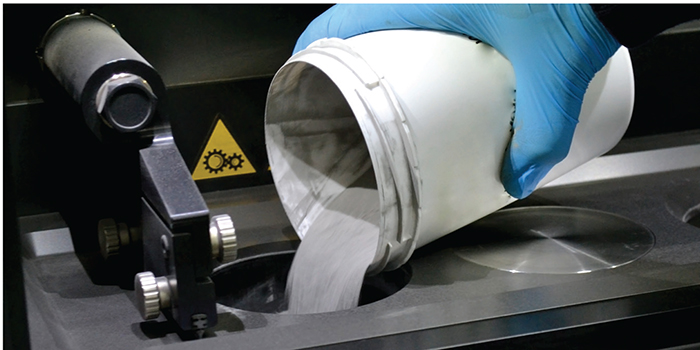
FIGURE 2. Powder particles and other bulk solids are a potential source of electrostatic shock in industrial settings
Double-layer charging. Electrostatic charge is generated during the handling and processing of liquids by a mechanism known as double-layer charging. Double-layer charging can occur at liquid-solid and liquid-liquid interfaces. Ions of similar polarity are adsorbed at the interface. The adsorbed ions attract ions of opposite polarity in the liquid, forming a double layer near the interface with its containing structure. As the liquid flows relative to the interface, the oppositely charged ions shear apart, increasing the potential within the liquid. This effect, combined with the competing effect of ion recombination at the vessel wall, results in an unbalancing of charge within the liquid. This is the type of static charging that occurs, for example, when liquids flow through pipes. The factors that can aggravate charge generation in liquids include the following:
• Two-phase flow where a second liquid or solid phase is present in a continuous phase
• Strainers or filters in a line
• Processes that create excessive splashing and spray
• Movement due to mixing or stirring processes
It is important to note that the double-layer charging mechanism described here can take place even in a plant that is well grounded. Electrical grounding of a plant is important, but will not alone prevent charge generation.
Induction charging. Induction charging occurs when a conductive object that is electrically insulated from ground leaves (or enters) an electric field, such as that surrounding an adjacent charged object, for example. When in the field, the conductive object may slowly gain or lose charge at a rate determined by its capacitance and resistance to ground. If the conductor becomes sufficiently charged by induction, then there can be a risk of electrostatic discharge. It is generally possible to control such induction charging through the grounding of conductive objects.
Charge accumulation
The generation of electrostatic charge need not be hazardous. However, if static charge is allowed to build up on plant structures, people, or powder or liquid media, hazardous electrostatic discharges may result.
Plant, equipment and personnel. Where there is a charging process, charge can accumulate on the plant facilities, equipment or people if there is nowhere for it to escape — meaning that the plant structures, equipment or people are electrically isolated from ground (Figure 3). This charge buildup produces a voltage rise, which can introduce an ignition risk into hazardous areas where flammable atmospheres may be present. Additionally, the presence of insulating (non-conductive) plant structures or equipment in hazardous areas can lead to small electrostatic discharge from the surfaces of the insulators themselves. In some flammable atmospheres, these discharges can cause ignition.
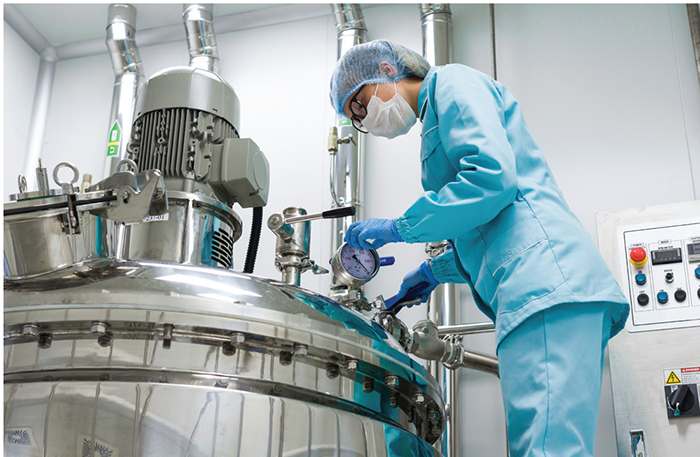
FIGURE 3. Both equipment and personnel are at risk to generate charge buildup that can introduce ignition risks
Powders and liquids. Where there is a charging process, charge buildup is most likely to occur on powders or liquids that have high electrical resistivity (those that are poor conductors of electricity). In electrostatic terms, such highly resistive materials can hold charge for minutes, hours or longer — even if they are in contact with a plant structure that is electrically connected to ground.
Electrostatic discharges. Electrostatic discharges occur between two objects or surfaces that are at different electrostatic potentials (voltages). As an object or surface accumulates charge, the electric field strength above it intensifies. If the field strength between the objects or surfaces exceeds the breakdown strength of the atmosphere between them, an electrostatic discharge will occur. Such discharges have varying energy content, but may sometimes be sufficiently energetic to ignite nearby flammable atmospheres, including the gases, vapors, dust clouds and aerosols typically found in CPI plants.
Effective discharge energy depends very much on the amount of charge accumulated and on the electrical properties of the surfaces or objects involved. Fortunately, engineers can gain insight about effective discharge energy by identifying the type and location of the discharge that could occur. Generally speaking, in most situations, the maximum energy of discharges from conductors can be significantly higher than those from people, which in turn can be greater than those from the surfaces of bulk powders and from plant structures and equipment made of insulating materials. There are overlaps and exceptions to this simple hierarchy of maximums, however, as the following sections explain.
So, the risk of igniting a flammable atmosphere with a discharge of static electricity depends both on the effective energy of the electrostatic discharge and on the sensitivity to ignition of the flammable atmosphere. The ignition sensitivity is a (measurable) property of the flammable atmosphere. The effective energies of electrostatic discharges found in a process environment are variable, but fall within ranges and are usually limited. We further develop these concepts in the following sections.
Flammable atmospheres
Perhaps the greatest hazard posed by an electrostatic discharge is as a potential ignition source for flammable atmospheres. The presence of three elements is required for a vapor fire or deflagration to occur: (1) a fuel; (2) an oxidant; and (3) a sufficiently energetic ignition source. For a dust explosion, two additional components are needed: (4) a dispersing mechanism (to make the dust airborne); and also (5) containment within the plant or the equipment. The main elements of a vapor fire or deflagration are commonly illustrated in a fire triangle (Figure 4) and as an explosion pentagon with dusts (Figure 5). Even in the presence of all three (or five) components, the fuel and oxidant mixture must be present between certain concentration limits to be flammable and capable of flash fire or explosion.
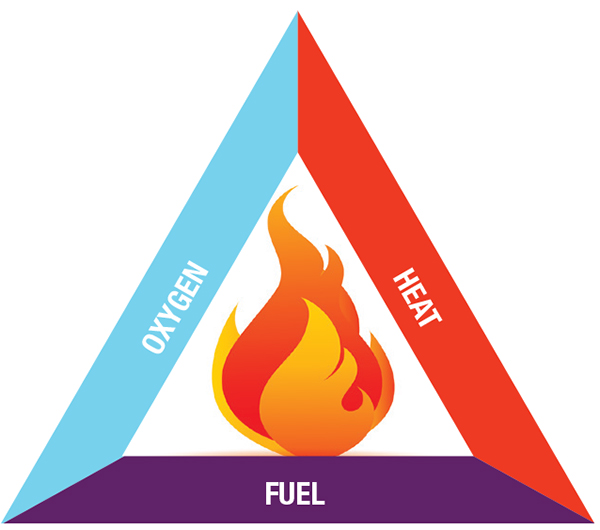
FIGURE 4. The three elements contributing to vapor fires or deflagration are heat, fuel and
oxygen
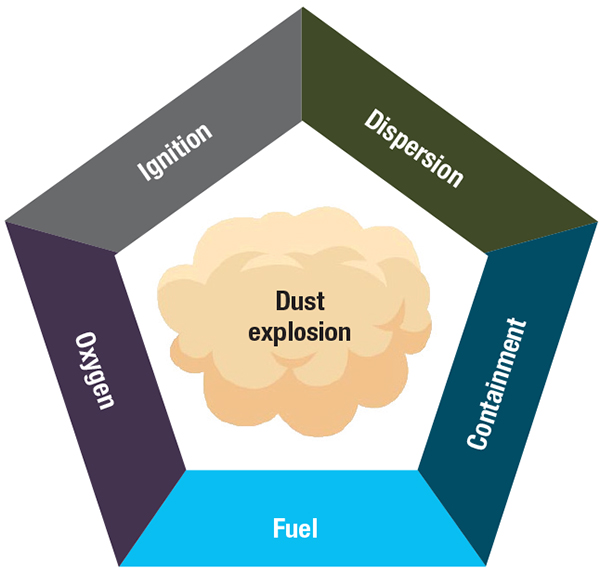
FIGURE 5. Dust explosions can occur when these physical components are present
For an electrostatic discharge to ignite a flammable atmosphere, the effective discharge energy must be greater than the minimum ignition energy (MIE) of the flammable atmosphere. The MIE is defined as the smallest electrostatic discharge energy that is capable of igniting the flammable atmosphere at its most easily ignitable concentration. The MIE of most hydrocarbon gases and organic vapors ranges from 0.1 to 1.0 millijoules (mJ), while the MIE of most dispersed dusts ranges from less than 3 mJ to over 1,000 mJ. While some literature data are available for MIEs of gases, vapors and dusts, it is generally recommended that such data be developed on a process-specific basis, since slight variations in composition or physical and chemical characteristics can have significant effects on MIE. For example, the MIEs of most powders and dusts decrease markedly as particle size or moisture content decrease. The MIE of a flammable atmosphere can be compared with the effective energy of any possible electrostatic discharges that could occur.
Control electrostatic hazards
The approach to the control of electrostatic hazards, as with other fire and explosion hazards that can occur in a CPI plant, involves measures to both prevent ignition and to protect plant and people from the consequences of a flash fire and explosion. The control of static electricity requires special focus, since it is not always apparent where charge can be generated and if the generation of charge is likely to cause a hazard or problem. A five-step approach is advocated for control of electrostatic hazards. These steps are as follows:
- Collect flammability and electrostatic data on the possible flammable atmospheres that could be present
- Collect data on the plant structures and equipment and process materials
- Assess processes, plant facilities, equipment and people for charge generation and accumulation
- Take measures to control static electricity
- Implement change in the context of an approach to process safety that considers avoidance of flammable atmospheres, control of all ignition sources and measures to protect people and plant structures from the consequences of fire and explosion
Electrostatic characteristics
The first two steps in assessing electrostatic problems and hazards involve collecting information on flammable atmospheres (Step 1) and on the electrostatic properties of the materials processed, handled or used in the plant (Step 2), including the following:
- MIE of flammable atmospheres
- Resistance-to-ground of conductive (metal) objects and other plant items
- Electrical resistance of operators’ body to ground (footwear and flooring)
- Electrostatic chargeability of powders and liquids (alternatively, measure surface voltage or electric field during processing)
- Volume resistivity of powders
- Conductivity of liquids
- Surface resistivity of solid objects, such as plastic containers and liners
National Fire Protection Association (NFPA) Standard 77, Recommended Practice on Static Electricity, provides valuable assistance in controlling the hazards associated with the generation, accumulation, and discharge of static electricity [1]. NFPA 77 provides a basic understanding of the nature of static electricity, provides guidelines for identifying and assessing the hazards of static electricity, as well as the techniques for controlling the hazards of static electricity.
Process, equipment and people
This section discusses some of the measures that can be considered to reduce the risk of flash fires and explosions due to electrostatic discharges from some common operations in the CPI, and how to assess processes for risk of charge generation (Step 3) and control static electricity (Step 4).
Conductive (metal) plant structures. The electrical resistance to ground of all conductive items in a plant, including metal pipes, equipment, vessels and containers, should be checked. If the resistance is greater than 10 ohms, direct ground connection will be required. It is important that the ground connections are checked regularly and that their purpose is known to the operators and maintenance personnel.
Personnel. Personnel wearing insulating footwear or working on insulating flooring (such as epoxy-coated or painted surfaces) can typically attain potentials of 10 to 15 kV by just doing various manual operations, such as walking around, putting on or taking off overalls, or pouring powders and liquids out of containers (Figure 6). Sparks from electrostatically charged personnel could have maximum discharge energies of up to about 30 mJ. The following measures should eliminate the possibility of electrostatic sparks from operators:
- Personnel should be grounded so that their resistance to ground is less than 1 ✕ 108 ohm. This may be achieved by a conductive or static-dissipative flooring in combination with wearing static dissipative footwear with a resistance to ground between 5 ✕ 104 and 1 ✕ 108 ohm
- The resistance of the floor or surface on which the operator, wearing static-dissipative footwear, is standing should also be less than 1 ✕ 108 ohm
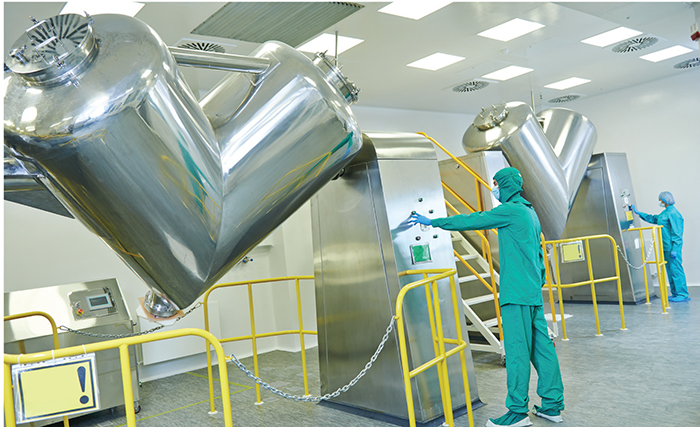
FIGURE 6. Flooring and footwear can attain charge potential through everyday activities, and measures must be taken to decrease the possibility that sparks are formed
Insulating (plastic) materials. Examples of insulating materials include plastic bags, liners, drums, pipes, hoses and plastic or glass-lined pipes and vessels. Non-conductive (insulating) materials typically have a surface resistivity greater than 1 ✕ 1011 ohm/square. Non-conductive materials, such as plastic containers and liners, can become electrostatically charged by manual rubbing, causing brush discharges. Brush discharges can, in practice, only ignite flammable vapor or gas atmospheres with a MIE of less than about 4 mJ. More significantly, pneumatic conveying of powders through non-conductive (plastic) hoses and pipes can highly charge the inside surfaces of the hose or pipe, giving rise to propagating brush discharges. Similarly, highly charged liquids and powders entering non-conductive containers and liners can charge the inside surfaces of the container or liner and also result in propagating brush discharges. Propagating brush discharges can ignite all flammable vapor and gas atmospheres, and dust clouds with MIE up to about 2,000 mJ.
It is important to note that grounding of non-conductive materials would not facilitate the relaxation of electrostatic charges to ground. To avoid brush and propagating brush discharges, one must consider using conductive or static-dissipative materials with a surface resistivity less than 1 ✕ 1011 ohm/square.
Liquids. Static-electricity hazards can arise in various liquid-handling operations, including filling, sampling, mixing and filtration. During liquid handing and processing operations, electrostatic charge can accumulate on the following: (1) bulk liquids in non-conductive containers and vessels; (2) low-conductivity liquids; and (3) liquid mists regardless of the liquid conductivity. The following suggestions can reduce the electrostatic ignition hazards:
- Make the plant electrically conductive and grounded — all items of the plant, including pipes, vessels, containers and so on should be electrically conductive or static dissipative and grounded
- Increase the liquid conductivity — an antistatic additive may be used in very small concentrations to raise the liquid conductivity
- Properly design and locate filters and valves — use valves with the maximum diameter possible. Locate filters and valves as far as possible from the entrance to the receiving vessel
- Control the liquid entry to the vessel — liquid should enter a vessel through a drip leg with submerged ends or a bottom inlet point
- Control the flow velocity, using the following guidelines:
- Liquids with conductivity greater than 100 pS/m: no flow velocity restrictions
- Liquids with conductivity less than 100 pS/m and no immiscible components: flow velocity should be less than 7 m/s
- Liquids with conductivity less than 100 pS/m and containing immiscible components: flow velocity should be less than 1 m/s
Powders. Highly charged powder particles entering a vessel can give rise to discharges on the surface of the bulk powder during filling of vessels. These are called bulk or cone discharges. The energy of these discharges depends on the powder’s volume resistivity, electrostatic chargeability and particle size, as well as the vessel dimensions. Typically, these discharges bring a maximum energy of about 25 mJ.
Bulk discharges will not occur if the powder has a volume resistivity less than 109 ohm∙m and if it is handled in a grounded, conductive plant. However, if the powder is insulating (meaning its volume resistivity is greater than 109 ohm∙m), if its MIE is less than 25 mJ and if the electrostatic chargeability test results show that the quantity of electrostatic charge on the particles is sufficient to cause discharges from the surface of the bulk powder, then one of the following measures should be considered:
- Installation of inert-gas blanketing
- Installation of explosion protection and isolation measures
- Implementation of measures to reduce electrostatic charge generation and accumulation
Effect of humidity on charge accumulation. If water vapor is present in air, it absorbs onto surfaces and forms a slightly conducting surface layer. The extent to which the water absorbs and increases the conductivity depends on the nature of the surface and the humidity of the atmosphere. Although there is not a definitive relative humidity where the conductivity of all materials changes, holding the relative humidity at above about 65% at about 20°C may significantly reduce electrostatic effects.
Explosion prevention
The final step involves exploration and execution of explosion-prevention measures and avoidance of risk factors, such as flammable atmospheres and uncontrolled ignition sources.
Removal of flammable atmosphere. If the formation of a flammable atmosphere cannot be prevented or all ignition sources cannot be reasonably excluded or eliminated, then the risk of a fire or explosion will persist, and measures must be taken to protect against their consequences. One method of preventing a flammable atmosphere from forming is inert-gas blanketing or purging. This involves the introduction of an inert gas into a vessel or system to reduce the relative oxygen concentration to a level below which a fire or explosion cannot occur. This value is known as the limiting oxygen concentration (LOC).
Explosion protection. Explosion protection measures include containment, relief venting and suppression. Containment is achieved by designing vessels and equipment so that they are sufficiently robust to withstand and contain the maximum explosion pressure. Relief venting involves the installation of special panels on equipment that are designed to open at a pressure lower than the design pressure of the equipment. This protects the equipment from overpressure and relieves the explosion pressure and products to a safe area. Suppression is the rapid introduction of a suppressant to the incipient explosion. This prevents the course of the explosion from reaching a hazardous pressure and thereby protects the equipment from the explosion effects. These measures are often coupled with explosion isolation, which is the use of devices or methods to prevent the propagation or transfer of fires and explosions from one unit to another.
Final thoughts
Many industrial fires and explosions have been caused by discharges of static electricity igniting the flammable vapors and powders often found in CPI plants. Electrostatic charge generation most commonly occurs whenever materials — liquids or solids — come together and separate. In industrial processes, there are many occasions during the transfer, handling, processing and packaging of flammable liquids and powders where electrostatic charge generation and accumulation can occur, and sometimes electrostatic discharges will result. Fires and explosions occur when these discharges have more energy than the minimum required to ignite flammable vapors or dust clouds.
Whatever preventative and protective measures are considered (hardware or procedural), they must be effectively implemented, installed and maintained. Furthermore, staff need to be trained to understand electrostatic hazards and the measures in place to control static electricity.
Edited by Mary Page Bailey
References
1. NFPA 77, Recommended Practice on Static Electricity, National Fire Protection Association, 1 Batterymarch Park, Quincy, MA 02169-7471
2. Ebadat, V., others, Reducing Electrostatic Hazards Associated with Chemical Processing Operations, Chapter 36, “Handbook of Chemical Health and Safety,” Oxford University Press, April 2001.
3. Britton, L. G., “Avoiding Static Ignition Hazards in Chemical Operations,” Wiley & Sons, Inc., January 1999.
Author
Vahid Ebadat is the chief executive officer of Stonehouse Process Safety, Inc. (Address: 11D Princess Rd, Lawrenceville, NJ 08648; Phone: 609-455-0001; Email: [email protected]; Website: www.stonehousesafety.com). He has worked extensively as a process and operational hazards consultant for the chemical, pharmaceutical, food, oil and gas, and paper and wood industries. He has been a member of several industry contributing committees, including: NFPA 77 Technical Committee on Static Electricity; NFPA 654 Standard for the Prevention of Fire and Dust Explosions from the Manufacturing, Processing, and Handling of Combustible Particular Solids; and ASTM E27 Committee on Hazard Potential of Chemicals. Ebadat has published many technical articles and papers globally and speaks widely on the topic of process safety, dust explosion mitigation, gas and vapor flammability and controlling electrostatic hazards.