Innovations place more robust instruments in demanding applications and enable processors to take advantage of the industrial internet of things
Because pressure is one of the most common and important measurement parameter in a chemical processing plant, the established technology has been providing top-notch accuracy of readings for some time now. However, because the chemical process industries (CPI) are always evolving, so too must the devices. For this reason, providers of pressure measurement equipment are tweaking standard technologies in an effort to meet the requirements of more demanding chemical applications. At the same time, digitalization is being added to many devices, providing more advanced diagnostics and allowing users to dive into the industrial internet of things (IIoT).
Conquering demanding applications
“In the chemical and [petroleum] refining industries, we are seeing the pressure devices exposed to much more demanding process conditions and applications,” says Scott Nelson, vice president and general manager of pressure products with Rosemount, Inc., (Shakopee, Minn.; www.emerson.com), a subsidiary of Emerson. “As our customers try to drive less variability, run cleaner processes and achieve higher efficiencies, they tend to run at higher operating temperatures and higher pressures, which greatly exceed the normal limits of field instrumentation.”
For example, Nelson says, in the chemical industry, a typical pressure instrument will have a process temperature limit of 120°C, so manufacturers of pressure instrumentation have been tasked with developing solutions that will allow operation in much hotter processes, some as high as 410°C. “That is really pushing the envelope to what we’ve seen in the past,” he says.
Tony Maupin, chemical market segment manager, with WIKA Instrument, LP (Lawrenceville, Ga.; www.wika.com) adds that in addition to developing new technologies designed to address more challenging applications, increasing safety concerns and the needs of niche applications are also driving innovation.
“One of the most important characteristics of pressure measurement devices is reliability in notoriously harsh conditions, including high temperatures, high pressures and corrosive materials,” says David Wilson, product manager for pressure and temperature products with SOR Inc. (Lenexa, Kan.; www.sorinc.com). “Since most devices are currently very accurate, the focus is on making sure the device remains stable, efficient and safe in these difficult conditions.”
One of the ways equipment providers are doing that is through providing diaphragm seals with the devices and making those seals in a variety of materials or with innovations that allow them to withstand the chemical-processing environment. “The diaphragm seal protects the instrument from temperature, corrosive media and other process conditions that could damage or affect the sensor’s accuracy or the life of the sensor itself. Diaphragm seals are add-on accessories, but selecting the right material and design will help prolong the life and increase the safety of challenging applications,” says Wilson.
In chemical processes, fluctuating temperatures, aggressive media or strong vibrations often decrease safety and accuracy of readings, says Ehren Kiker, product marketing manager with Endress + Hauser (Greenwood, Ind.; www.us.endress.com). To measure more precisely in such applications and to increase process safety, the company developed a temperature compensating membrane, called TempC. “Instead of flexing symmetrically like a normal remote seal, these flex asymmetrically,” explains Kiker. “This allows the diaphragm to handle ambient and process temperature changes without causing huge shifts in measurement, providing accurate and stable measurements. Fast membrane recovery after temperature shocks of the diaphragm also permits shorter downtime in batch applications, providing higher availability of production, as well.”
And, because safety is an ever-increasing concern, especially in chemical processing, manufacturers like WIKA are taking steps to provide solutions for critical or aggressive applications. WIKA’s double-diaphragm design with a diaphragm-monitoring system offers a solution for applications where the product must not find its way into the environment, or where the fill fluid in the diaphragm seal assembly must not come into contact with the product for any reason (Figure 1). The space between the inner and outer diaphragms is evacuated. The resulting vacuum is monitored by a measuring device, such as a pressure switch, gage or transmitter. Should an outer diaphragm breach occur, a visual, acoustic or electrical warning will be given. The damaged system can then be replaced during the next shutdown. “While this isn’t something that every chemical process needs, in niche applications where there is a particularly nasty acid or chemical that must not get out, the system gives the user an indicator that they have lost the first level of containment while the chemical is still being contained and they still have time to remedy the issue,” says Maupin.
Also in an effort to improve reliability and robustness, equipment providers are improving more than the diaphragm seals. For example the Rosemount Wireless Pressure Gauge (Figure 2) features up to 150 times overpressure protection and two layers of process isolation, resulting in safer installation. “It is very easy to over-pressurize traditional pressure gage devices built on Bourdon-tube technology and cause them to break,” says Rosemount’s Nelson. “We have been able to bring our solid-state pressure sensor technology into the pressure gage market and offer a pressure gage that can be over-pressured up to 150 times and withstand 11,000 psi burst pressure. This means these pressure gage applications are able to withstand fault conditions and any sort of pressure spikes. They also have smart electronics on them so the gages are continuously diagnosing themselves and can communicate any problems to the user remotely via wireless.”
And, if a processor is looking to eliminate issues regarding ambient and process temperature effect, which can cause measurement drift and inaccurate readings, Endress + Hauser offers an electronic dp Deltabar FMD72 differential pressure system for the measurement of pressure, level, volume or mass in pressurized tanks, distillation columns and evaporators (Figure 3). The high-pressure sensor measures the hydrostatic pressure. The low-pressure sensor measures the head pressure. The level is calculated in the transmitter using these two digital values. “Part of the reliability issue is inherent to seal systems because they are so susceptible to temperature issues,” says E+H’s Kiker. “This system is designed to minimize those issues in applications where temperature effect in remote seals provides challenges to users.”
For applications where extreme temperatures create challenges, the Rosemount 3051S Thermal Range Expander enables the transmitter to operate in high-temperature processes without the need for heat tracing. The 3051S device uses a specialized process interface and fill fluid to withstand process temperatures ranging from –105 to 410°C and pressures up to 3,750 psi. “This is a great example of products that are being developed to help users deal with very demanding applications because it can withstand very high and very low temperatures, and users are able to simplify their processes by eliminating heat tracing equipment, which is often used in temperature-challenged applications,” says Rosemount’s Nelson.
The age of digitalization
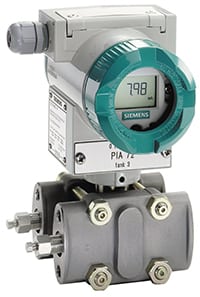
Figure 4. Siemens Sitrans P DSIII digital pressure transmitter features ease of installation and set up, high accuracy and self-diagnostics and simulation functions
Siemens
Over the past decade, pressure transmitters, like other instruments, have been getting smarter via features such as time clocks, minimum and maximum pointers for pressure and temperature and other built-in intelligence that provided information to users. However, says Sean McNutt, product marketing manager for pressure measurement and control with Siemens (Alpharetta, Ga.;
), the hardest part was getting that information out of the devices and into the users’ hands in a usable way. “But with the move toward digitalization and the industrial internet of things (IIoT), there are new ways of getting data out of the transmitter, whether it’s through a digital bus connection or via HART communications, and this is allowing industry to make the move from just going out and checking the devices to actively taking available data and using it in a way that improves efficiency and reliability of the instruments and the process,” says McNutt.
He adds that while most pressure instruments typically don’t provide enough information to necessitate Ethernet connections, many users are asking for connections with the ability to export information from the device to a monitoring system or to the cloud so they can get to and use the data that have been previously trapped in the transmitter. “These transmitters have had Profibus or HART for years and now we are adding components to existing networks, making it easier to get more functionality out of existing instruments and allowing users to do more with that data,” says McNutt.
In addition to the ability to begin exploring the data, many of today’s devices offer self-diagnostic or other smart features. For example, Siemens Sitrans P DSIII digital pressure transmitter (Figure 4) is available with HART, Profibus PA or Foundation Fieldbus communications. It features ease of installation and set up, high accuracy and self-diagnostics and simulation functions. It is suitable for installation in SIL2 (safety integrity level) applications and comes with a range of safety approvals.
And, SOR’s 815PT Smart Pressure Transmitter is a rugged, compact, loop-powered instrument suitable for hazardous locations and hostile environments. It is easily configured using HART 7 Communication Protocol and Modbus RTU Serial Communications. “One of the benefits of the communication capabilities is that it allows operators to perform predictive maintenance based on the data,” says SOR’s Wilson. “By monitoring the data they get from the device, users can now see when it is time for a product to be replaced or maintained, as opposed to just reacting to the failure of the instrument after the fact.”
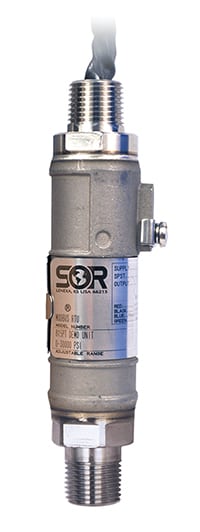
Figure 5. SOR’s 815PT Smart Pressure Transmitter is a rugged, compact, loop-powered instrument suitable for hazardous locations and hostile environments
SOR
Similarly, many of Rosemount’s pressure measurement devices offer intelligent features such as Power Advisory Diagnostics, which has the ability to monitor power supply and electrical connection to the device. If an incident occurs that could lead to a fault condition or loss of signal, the device can detect it and alert the user before the signal is lost. Statistical Process Monitoring is another feature available on Rosemount devices. SPM technology characterizes the normal operation of a process and continually monitors it to see if the process signature has changed, and does so at a much faster rate than is possible in the process control system. “This provides users with the ability to monitor and detect abnormal operating conditions and receive early detection of any problems that may be arising, not just in the device, but in the process and physical installation as well,” says Nelson.
Data, such as those available from smart pressure devices and other instruments, enable the shift from reactive to predictive maintenance, says Siemen’s McNutt. Because pressure transmitters have built-in diagnostics and alarms and timers and often provide realtime visualization of related systems, they can inform users about drifts in temperatures, pressures or calibration issues that need attention. In traditional analog measurements, users only received the process value and wouldn’t know anything was wrong with the transmitter until it wasn’t responding or until the process was off specification until it became obvious in other ways. “With more data about the instrument and the process available from pressure instruments, users can apply that to get a better look into the process itself and start to employ predictive maintenance instead of reactive,” he says.
Nelson agrees that smarter transmitters provide high value in and of themselves as a measurement point and as another way to monitor various systems. He adds that recently they are being used to feed the IIoT with more process insight and actionable information that has already been analyzed. “This is no longer just raw data,” he says. “It is usable information and the digitalization of that information is allowing us to enable the industrial internet of things.”
Joy LePree