Pumps are essential equipment in the chemical process industries (CPI). Given the imperatives to reduce production costs and maximize energy efficiency, pump selection is crucial. Knowledge of pumping basics, along with the fluid characteristics for a particular application can help engineers make the best choice. While the majority of pumps in use in CPI plants are kinetic energy pumps (the largest category being centrifugal pumps), positive displacement (PD) pumps are an important class of industrial equipment. The following is a collection of information on several types of PD pumps and an outline of the differences between positive displacement pumps and centrifugal pumps.
Selection Starting Point
In pump selection, first consider what the expectations of the pump will be. The following parameters must be determined before a pump can be selected: Inlet conditions — To avoid suction problems, the pump should be located as close as possible to the liquid supply Flowrate — The flowrate requirements for the pump should be considered Differential pressure — Smaller pipe size and longer pipe runs reduce initial system cost, but the higher pressure differential raises energy consumption and reduces pump lifetime Liquid characteristics — The properties of the fluid to be pumped — including material compatibility, viscosity, sensitivity to shear stress and presence of particulates or solids — are important factors
PD versus centrifugal Pumps
PD and centrifugal pumps behave differently. As a means to move liquids, centrifugal pumps rely on kinetic energy, forcing liquid out of the pump with energy imparted to the liquid as it moves toward the outer diameter of a rotating impeller (pressure is created and flow results). PD pumps work by capturing confined amounts of liquid and transferring them from the suction to the discharge port (flow is created and pressure results).
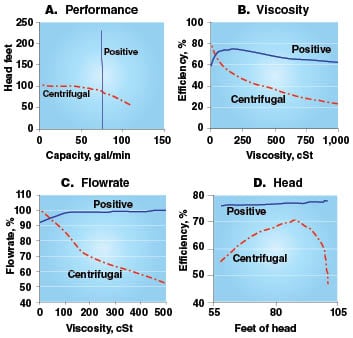
The following plots represent examples of the performance behavior differences for centrifugal and PD pump types:
A. Flowrate versus pressure — Centrifugal pumps exhibit variable flow depending on pressure, whereas the flow in PD pumps is largely independent of pressure B. Efficiency versus viscosity — For centrifugal pumps, efficiency decreases at greater viscosities. Positive displacement pumps are actually more efficient at higher viscosities C. Flowrate versus viscosity — Centrifugal pumps lose flow as viscosity increases, while the flow of a PD pump can actually increase at higher viscosities D. Efficiency versus pressure — Changes in pressure have minimal effect on PD pumps, but have a dramatic effect on centrifugal pumps.
PD PUMP operating principles
• PD pumps displace the same volume of liquid with each rotation of the shaft, so flow is proportional to pump speed • PD pumps are self-priming • PD-pump mechanics require close-fitting internal parts with some running clearance • PD pumps require a pressure-relief mechanism (either relief valves or rupture discs) in case of discharge blockage
Types of PD Pumps
![]() |
![]() |
![]() |
![]() |
Internal gear pumps
Internal gear pumps have an outer gear called the rotor that is used to drive a smaller inner gear called the idler. The idler gear rotates on a stationary pin and operates inside the rotor gear. As the two gears come out of mesh, they create voids into which the liquid flows. When the gears come back into mesh, volumes are reduced and liquid is forced out of the discharge port. A “crescent” is formed between the two gears that functions as a seal between the suction and discharge by trapping the volume of liquid carried between the teeth of the rotor and idler. Internal gear pumps are effective with viscous liquids, but do not perform well for liquids containing solid particles.
External gear pumps
External gear pumps have a similar pumping action to internal gear pumps in that two gears come into and out of mesh to produce flow. The difference is that external gear pumps have two identical gears rotating against each other. Each gear is supported by a shaft with bearings on both sides of each gear. External gear pumps work well in high-pressure applications, such as hydraulics, but are not effective in applications requiring critical suction conditions.
Lobe pumps
Lobe pumps resemble external gear pumps in operation, except that the pumping elements do not make contact. Lobe contact is prevented by external timing gears. Lobe pumps perform well with liquids that contain solid materials, but do not perform well with low-viscosity liquids.
Vane Pumps
Sliding vane pumps have a rotor with radial slots, and it is positioned off-center in a housing bore. Vanes that fit closely into rotor slots slide in and out as the rotor turns. Pumping action is caused by the expanding and contracting volumes contained by the rotor, vanes and housing.
Vane pumps are effective for low-viscosity liquids, and when dry-priming is required. They are not ideal for abrasive liquids.
References
1. Petersen, J. and Jacoby R., Selecting a Positive Displacement Pump, Chem. Eng., August 2007, pp. 42–46.
2. Viking Pump Inc., When to use a Positive Displacement Pump, The Pump School Website, Viking Pump Inc., http://www.pumpschool.com, 2007.
3. Soares, C., “Process Engineering Equipment Handbook,” McGraw Hill, New York, 2002.
4. “Perry’s Chemical Engineer’s Handbook,” 8th ed. McGraw Hill, New York, 2008.
Scott Jenkins