As refiners respond to shifting product demand, pressure to decarbonize operations builds. Investments in low-carbon hydrogen technologies, process optimization and integration projects are on the rise
The petroleum-refining sector sits in a unique place: global demand for refined products — especially diesel and aviation fuel — remains strong, and refining operations generated record profits in 2022. The Russian invasion of Ukraine has prompted many countries to look more intensely at energy security, with an emphasis on established technologies to power economies. But at the same time, the petroleum refining industry is under pressure to decarbonize its operations and dramatically lower greenhouse-gas (GHG) emissions.
The tension between short-term profits and long-term sustainability creates challenging decisions for refineries looking to navigate a pathway to the future of low-carbon energy. Low-carbon hydrogen production, digital technologies, shifting feedstocks and process optimization are among the strategies being pursued for lowering the carbon footprint of refining operations (Figure 1).
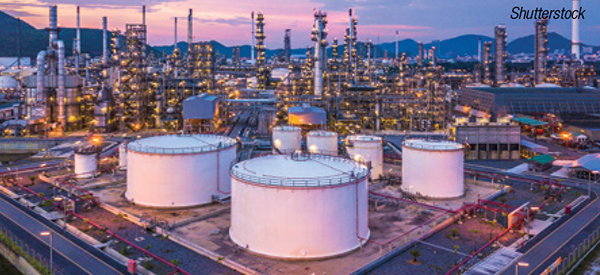
FIGURE 1. Refineries have been practicing capital discipline around fossil-fuel infrastructure, but have been investing in decarbonization-related projects
“Refinery margins are forecast to be pretty healthy at least for the rest of the decade, and [refining companies] have been practicing capital discipline around fossil-fuel infrastructure,” says Alan Gelder, senior VP for refining and chemicals at WoodMackenzie (Edinburgh, U.K.; www.woodmac.com). “There’s still investment happening, but it’s shifted toward decarbonization-related projects.” Wood Mackenzie anticipates an acceleration of investment in low-carbon technologies, including carbon capture, utilization and storage (CCUS), hydrogen, next-generation nuclear technologies and advanced battery chemistries. Analysis by the International Energy Agency (Paris; www.iea.org) found that clean energy investment by oil & gas companies has risen by an average of 12% each year since 2020.
“We’re seeing a big focus on energy efficiency and process optimization in petroleum refineries,” Gelder says. “Refiners are working on reducing site emissions, and looking to produce low-carbon fuels (by co-processing bio-based feedstock, for example). There’s also been a coalescence around the idea of refinery-petrochemical integration,” he says.
Low-carbon H2 production
In March, the United Nations Intergovernmental Panel on Climate Change (IPCC; Geneva, Switzerland; www.ipcc.ch) finalized its sixth assessment report on climate change. Regarding the threat of climate change, the report states: “There is a rapidly closing window of opportunity to secure a liveable and sustainable future… The choices and actions implemented in this decade will have impacts now and for thousands of years.”
The report emphasizes the need for “deep and rapid reductions in gross emissions of CO2” and other GHG emissions, but acknowledges that some hard-to-abate residual GHG emissions (from agriculture, aviation, shipping and industrial processes, for example would remain and “would need to be counterbalanced by deployment of carbon dioxide removal (CDR) methods to achieve net zero GHG emissions.” The need for carbon capture and storage (CCS) in industrial operations is clear: “Global modeled mitigation pathways for reaching net-zero CO2 and GHG emissions include transitioning from fossil fuels without CCS to very low- or zero-carbon energy sources, such as renewables or fossil fuels with CCS,” the report says, as well as demand-side measures, such as improving efficiency, minimizing non-CO2 GHG emissions, and CDR.
Petroleum refineries are both large producers and consumers of hydrogen, placing them in a key role for a future that emphasizes hydrogen as a no-emissions energy source. Low-carbon hydrogen production is one of the key paths to decarbonizing hard-to-abate industries like petroleum refining and others, such as ammonia production, steel manufacturing and long-haul transportation. In the U.S., Europe and elsewhere, investment in low-carbon hydrogen has been spurred by government policy (Figure 2). The European legislative package known as “Fit for 55” aims to reduce greenhouse gas emissions by at least 55% by 2030. And tax incentives contained in the U.S. Inflation Reduction Act of 2022 (IRA), as well as grant opportunities under the Infrastructure Investment and Jobs Act of 2021 (IIJA), have also encouraged action.
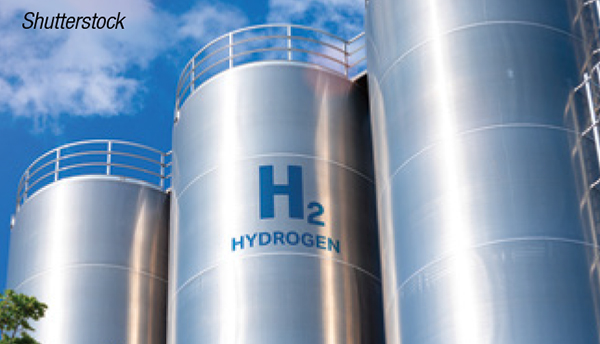
FIGURE 2. The global blue-hydrogen market is forecast to reach $34 billion by 2033
Relative to hydrogen, Wood Mackenzie’s Gelder says “governmental policy is key to changing the economic calculus for carbon capture technology [as required for “blue” hydrogen] and electrolyzers [for “green” H2], but also the local environment, site-specific and cluster-specific geography and economies of scale also make a big difference.” Green hydrogen from electrolysis of water, and blue hydrogen from steam-methane reforming (SMR), partial oxidation or autothermal reforming coupled with carbon capture, are technically viable, but the challenge is on the commercial side — everything you could do to improve refining operations requires investment and adds complexity to the refinery, says Gelder. “There have been a lot of pilot-scale projects and smaller-scale processes using these technologies, but they have not been scaled widely.
A recent report from industry analyst firm IDTechEx (Cambridge, U.K.; www.idtechex.com) forecasts the global blue hydrogen market to reach $34 billion by 2033. “CCUS infrastructure has significant government backing and is being developed by companies worldwide to capture and store emissions from various industries by locating infrastructure near industrial clusters. These forces are accelerating blue hydrogen production, which is expected to grow as global decarbonization efforts intensify,” the report says.
In January 2023, ExxonMobil Corp. (Irving, Texas; www.exxonmobil.com) granted a front-end engineering and design (FEED) contract to Technip Energies N.V. (Nanterre, France; www.technipenergies.com) for what would be the world’s largest low-carbon hydrogen facility at ExxonMobil’s integrated refining and petrochemicals complex in Baytown, Texas. The low-carbon hydrogen, ammonia and carbon capture facility in Baytown is expected to produce 1 billion ft3/d of low-carbon H2 at its planned startup in 2027–2028, ExxonMobil says. More than 98% of the associated CO2 produced by the facility (around 7 million metric tons per year) is expected to be captured and permanently stored, the company says. The CCS network being developed for the project will be made available for use by third-party CO2 emitters in the area in support of their decarbonization efforts.
ExxonMobil also made agreements with catalyst maker Topsoe A/S (Lyngby, Denmark; www.topsoe.com) to use Topsoe’s SynCOR autothermal reforming technology for the planned Baytown facility, and with Honeywell UOP (Des Plaines, Ill.; uop.honeywell.com) to use Honeywell’s CO2 Fractionation and Hydrogen Purification System at the integrated complex.
For its part, Honeywell is also working with Johnson Matthey plc (JM; London, U.K.; www.matthey.com) on low-carbon H2 technology. In December 2022, the two companies announced they would be working together to offer JM’s LCH autothermal reforming technology, coupled with Honeywell’s carbon-capture technology to produce blue hydrogen at scale. According to calculations from JM and Honeywell UOP, the combination enables direct process emissions to be less than 0.1 kg CO2 per kg of H2 by capturing carbon at rates above 99%. This provides eligibility for production tax credits within the IRA.
Autothermal reforming (ATR) generates hydrogen by combining the endothermic SMR reaction with exothermic partial oxidation. It is potentially attractive because it can be more efficient than SMR and facilitates carbon capture in some ways.
Hydrogen hubs
Low-carbon H2 production at petroleum refineries is also a component of several “regional clean-hydrogen hubs,” many of which are currently under development. Industrial hydrogen hubs are usually public-private partnerships defined as “a network of clean-hydrogen producers, potential clean-hydrogen consumers, and connective infrastructure located in close proximity.”
In the U.S., as part of the IIJA, Congress allocated $8 billion for the creation of multiple “H2 Hubs,” to support low-carbon H2 generation. The Department of Energy (DOE; Washington, D.C.; www.energy.gov) is administering the awards, and received 79 concept papers for H2 hubs as part of the program. DOE encouraged full proposals from a portion of the initial submissions and the awardees (as many as 10) will be announced in fall 2023.
A substantial portion of the applicants to the program involve major petroleum refiners. For example, the HyVelocity Hub (www.hyvelocityhub.us) on the U.S. Gulf Coast includes Chevron and ExxonMobil, along with a host of other academic and industrial partners. Organized by GTI Energy, Center for Houston’s Future and the University of Texas at Austin, the HyVelocity Hub will pursue DoE’s goal of limiting carbon emissions to less than 2 kg of carbon per 1 kg of H2 produced, and reducing the cost of clean H2 production to $1/kg. Another example is the H2 ALO Hub (h2alo.org), a partnership among the states of Arkansas, Louisiana and Oklahoma, along with a host of participants that includes Shell and TotalEnergies.
Meanwhile, in Europe, H2 hubs involving refineries are moving ahead, and many involve traditional refiners. An example is the Humber Industrial Cluster (HICP; U.K.; www.humberindustrialclusterplan.org). As part of the HICP, Shell and Uniper are developing a low-carbon H2 hub at Uniper’s Killingholme, U.K. site. In March 2023, Uniper and Shell UK Ltd. awarded Shell Catalysts & Technologies a contract to deliver a process design package for the HICP project, using the Shell Blue Hydrogen Process (SBHP). Two other companies are also working on plant design proposals for the project, and the one that is selected will become the Humber H2 ub project’s preferred low-carbon H2 production technology provider.
The proposals involve building a blue-hydrogen production unit at Uniper’s Killingholme site, capable of generating 720 MW of low-carbon hydrogen from natural gas. The CO2 produced (~1.6 million ton/yr) would be captured and stored in a geological formation in the North Sea.
SBHP is an alternative to autothermal reforming and SMR. It uses Shell gas partial oxidation technology and, compared to SMR and ATR, it captures CO2 at higher pressures and at larger scales, which results in a lower levelized cost of H2, Shell says.
Artificial intelligence
Another pathway for refineries to reduce GHG emissions is to optimize processes. The variability of feedstock slates and complexity of refining units offers many opportunities to improve process efficiency and consistency. And artificial intelligence (AI) technology has emerged as tool to help achieve that.
An example of how AI is being used in refinery settings comes from Hexxcell Ltd. (London; www.hexxcell.com), which is using AI to do predictive maintenance of heat exchangers in refineries. As a subset of AI, machine learning (ML) approaches have been used previously for predictive maintenance of rotating machinery, for example, but predicting maintenance for heat exchangers that undergo fouling deposition on thermal surfaces is more difficult because of the complex and varying compositions of crude oils and process conditions. Fouling on heat exchange surfaces reduces efficiency and increases pressure drop, requiring more energy input and emitting more CO2 for the the same barrel of oil processed.
“Since there is no single solution for heat exchanger fouling, refiners take a largely reactive and preventive approach, but it is often unclear which exchangers to clean, and when, and which cleaning method will be most cost-effective,” says Hexxcell co-founder and CEO Francesco Coletti. “We have developed a hybrid AI software that combines ML with physics-based models to generate insights about heat-exchanger maintenance and cleaning.”
The combination of ML with physics-based models can offer insights on system-specific fouling that would not be possible with either ML or models alone, Coletti says. “The AI doesn’t have enough data associated with the variety of conditions that could be observed in the heat exchanger to predict fouling without application of the models.”
Hexxcell launched a software suite known as Studio to allow engineers to build a process digital twin of the heat exchange system. The biggest benefit of using this hybrid AI approach is avoiding production loss, Coletti says. But the technology also can help reduce fuel consumption and associated CO2 emissions, and can assist in planning maintenance.
The company has tried and tested their models in a various of proof-of-concepts across several industries and their technology is now implemented in the field at a number of sites worldwide. “It’s a digitalization technology that delivers energy efficiency,” Coletti says.
In another example, AI is being used to make plant-operation decisions. In general parlance, AI is often discussed as a single technology, but a closer look at AI as a scientific field reveals several types of AI, and a wide spectrum of power and complexity in the technology. Abi Mukund, head of product strategy at Imubit (Houston; www.imubit.com), explains: “Most examples of AI in industry are of a type called ‘supervised learning,’ which use labeled datasets and standard model frameworks for prediction, such as for predictive maintenance.”
Moving beyond that, Mukund’s company has developed an AI-based software to create closed-loop neural networks using a type of AI known as “reinforcement learning.” In reinforcement learning, an AI algorithm learns to make decisions in a dynamic environment in pursuit of maximizing a particular reward, as defined by the domain expert. This is in contrast to supervised learning, where an AI algorithm is trained on datasets that are labeled by subject matter experts.
Imubit’s reinforcement learning AI models are trained to “think” like a human in making decisions and taking action in rapidly changing settings. The reinforcement-learning model is trained on a digital version of the plant that is developed using actual plant data from a data historian in a digital version of the plant. The AI learns how to control aspects of the plant that lead to defined objectives, such as energy efficiency, cost optimization or others.
Plant complexity is extensive and multidimensional. The large physical size of plants means varying time dynamics for a process — the time for material to move through a process doesn’t always match the decision-making timeframes. In addition, fouling of process equipment and degrading catalyst activity can affect relationships between process control elements, Mukund says. On top of that, there are volatile feed prices and variable end-product prices that can affect decisions about what feeds to use and what products to make. In real-world refinery settings, variable feed slates and mixing different crude oils together makes it impossible to characterize the feed in real time on a dynamic basis.
Because of this complexity, engineers tend to break the problem into pieces, so that each engineer sees a different “picture” of the plant, Mukund says. For example, planning economics engineers, operators and process control engineers all see things differently from their own perspectives. “To try to overcome this, refineries have traditionally turned to real-time optimization (RTO) techniques, but these generally lead to a more “first-principles” theoretical version of the plant that doesn’t often match reality,” says Mukund.
Reinforcement-learning AI can tackle the realities of refinery operation by using real plant data to train neural networks, then having the AI conduct “trial-and-error experiments” in a digital version of the plant. The AI acquires human-like intuition about how to run the plant to maximize a given objective. Engineers have access to a set of “what-if” applications to run hypothetical plant scenarios on the virtual plant to see what the effects are of decisions.
Imubit’s technology has been demonstrated for increasing efficiency and decarbonization at petroleum refining operations. “You can make more high-value products with less waste, and improve energy efficiency by 15–20%,” says Roger Wilhelmi, Imubit’s senior economic engineer.
A widely held concern associated with using AI for plant control is known as the “black box” problem — if humans cannot discern or explain how an AI algorithm arrived at a decision, should that decision be trusted?
Imubit’s Mukund says the company took pains to have users be able to elucidate this question. “We are using what is called ‘explainable AI,’ which is designed to allow informed human users learn what the AI has learned,” he says. “If you have at least a few years of experience in the refinery setting, and you know the plant, you will be able to build models for the AI and discern the insights it has generated.”
Imubit’s AI software has been installed in a handful of refinery sites, include one run by Delek US (Brentwood, Tenn.; www.delekus.com).
Meanwhile, AI is helping to improve refinery catalyst development as well. In late March, Ketjen Corporation (Houston; www.ketjen.com), a wholly owned subsidiary of Albemarle Corporation that was spun off from the company earlier this year to offer a distinct brand to refinery and petrochemical companies, launched its first product from a new catalyst-development platform that is powered by a combination of high-throughput experimentation and AI. The platform, known as Quasar, brings a new approach to catalyst discovery, development and manufacturing and helps to identify relationships between catalyst preparation, metal active phase and performance (Figure 3).
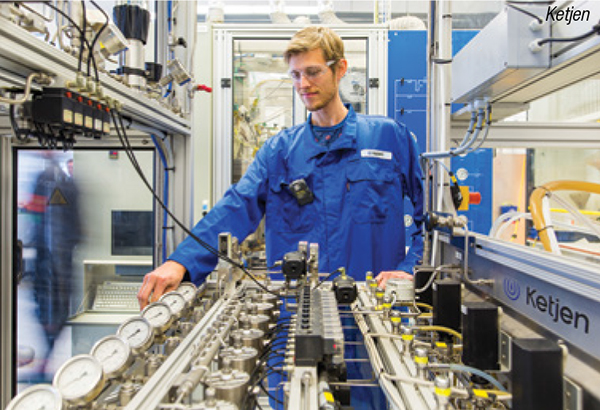
FIGURE 3. Artificial intelligence technology is being employed in the development of refinery catalysts
“We start with our existing knowledge of catalyst formulation, and conduct a series of high-throughput experiments and characterization tests, from which we gather data on a large number of parameters affecting catalyst performance,” explains Jaap Bergwerff, research director at Ketjen. “Then we feed the results of those experiments to an ML algorithm that is capable of delivering insights on the right combination of parameters for optimized performance.”
The process is iterative, and the ML-generated insights can be used to inform further experiments. “There are many parameters associated with catalyst composition, support and active phase and geometry that can be varied, and the different combinations can affect catalyst performance in interesting ways that are not always apparent when using traditional methods of development,” says Bergwerf. “Iterating with ML accelerates the iterative process and leads to catalyst improvements more quickly.”
The first catalyst developed using the novel approach enabled by Quasar is called KF882, a high-activity nickel-molybdenum (NiMo) hydrotreating catalyst. According to Andrea Battiston, Ketjen business advisor, the catalyst is able to treat more difficult feedstock than existing hydrotreating catalysts, and it leads to increased volume swell. Both advantages lead to increased profits for refineries. In addition, KF882 allows longer cycles than conventional catalysts, allowing better synchronization of turnarounds and less downtime.
KF882 Quasar can be used with other catalysts in Ketjen’s STAX catalyst-loading technology to tailor performance to specific refinery operation needs, says Chad Perrott, Ketjen business advisor.
KF882 “can help refiners generate additional revenue today, which can help free up cash for the company’s energy transition,” Perrott explains, “and the ML approach used for this platform can be used in the future to develop other catalysts designed for resource sustainability and for processing renewable feedstocks.”
Catalyst re-use
In another catalyst-related sustainability play, Evonik Industries AG (Essen, Germany; www.evonik.com) recently commercialized technology to enable reuse of a reactivated hydroprocessing catalyst for treating tail gas from a Claus sulfur-removal unit. Evonik’s EcoMax TG demonstrated higher performance than conventional tail gas treating catalysts in laboratory testing (Figure 4), and the performance has been validated in plant tests as well.
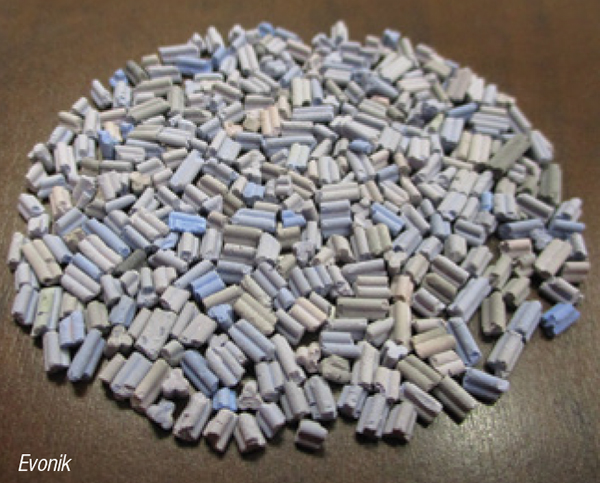
FIGURE 4. Re-activated hydroprocessing catalysts can be re-used for treatment of tailgas from the Claus process
Brian Visioli, Evonik global director, SRU/TGU & Purification Adsorbents, says the reactivated catalyst offers improves sustainability, because there is less end-of-life catalyst to landfill, as well as lower cost and better performance. The reactivation process removes contaminants like carbon and sulfur via controlled thermal oxidation, Visioli says. There are currently two installations of EcoMax TG at U.S. refineries.
Scott Jenkins