Sponsored by
In every plant and every facility across all industries, safety should be the top consideration when commissioning control systems. For this reason, spill prevention, control and counter measure is a must in any setting where chemicals or other hazardous liquids are manufactured, used, or stored in tanks.
A SPCC plan is designed to stop spills from occurring, and to control them when they do, by deploying counter measures to mitigate the damage and extent of a spill. While prevention is the goal, the possibility for incidents is always present. This makes it essential to have multiple layers of protection in place in the event of a spill to prevent damage to facilities, contamination of the environment and injury to personnel.
Chemical spills are most frequently caused by tank overfill or process leaks and using independent safety systems to detect and prevent each of these conditions is the most effective way to deal with this issue.
Overfill prevention: the first line of defense
The best overfill prevention systems sometime combine two different devices or technologies, for example, a radar and a level switch as the input to a primary control system. These would also be used as inputs to a dedicated safety instrumented system (SIS).
During normal operation, the primary process variable is all that is required to keep levels under control. But in the event of an instrument or control system failure, the independent safety system can override the primary system to prevent an accident.
To ensure safe functionality, and to meet standards like American Petroleum Institute API2350 (automated and manual tank overfill prevention) and International Electrotechnical Commission 61511 (safety instrumented systems for process industries), a SIS must be independent of all other facility control systems. Meeting these standards also requires proof testing of device safety functions at regular intervals, demonstrating SIS functionality in relation to safety requirements.
Endress+Hauser provides pre-engineered SIS packages to significantly ease testing efforts and reduce costs by providing users with the ability to execute systemwide proof tests with the press of a button during commissioning or operation. This can reduce the time it takes to proof test a tank farm’s SIS to minutes, rather than hours.
Because high-high level switches are mounted above normal maximum fill points, years can pass without activation. To verify functionality, testing these switches regularly is critical so they work correctly if dangerous overfilling situations arise.
There are many switch technologies for high-high overfill prevention applications, including vibrating tuning forks, capacitance, ultrasonic gap switches, float switches and more. With a wide range of options, engineers must carefully consider the best instrumentation options for each application, selecting equipment fit to tank geometries, liquids in use, and accuracy and testing requirements.
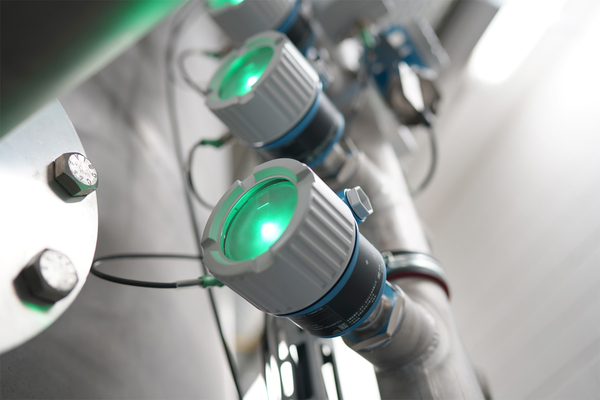
This Liquiphant FTL51B smart level switch is SIL 2 certified for use in a SIS loop and is equipped with SmartBlue® App for Heartbeat Technology®, supporting automated in-situ self-testing, diagnostic data generation and digital verification reports.
Endress+Hauser’s process experts can help with these assessments, please contact us here for further questions.
You can also take advantage of tools like the online applicator to determine the right instrument to meet process requirements.
Monitor the dike or sump: detecting leaks
The second line of spill defense is one or more level switches installed inside retention dikes or sumps to reliably indicate the presence of liquid. There are many specialty instruments that do this according to the liquid’s conductive properties, such as the NAR300 Oil Leak Detector Float Sensor, which combines vibronic and conductive level sensing technologies to identify the presence and types of liquids in sumps and dikes.
This helps identify the liquid to distinguish between rainwater (conductive) and hydrocarbons or solvents (nonconductive). By combining a vibrating tuning fork—which detects liquid regardless of its conductivity—and a conductivity switch, facility personnel can use software systems to identify the type of accumulation in the dike, and to accurately detect chemical leaks before taking a trip to the tanks.
Improving plant safety
A robust SPCC plan greatly reduces the likelihood and severity of chemical spills. Installing the right instrumentation and testing it frequently provides the best solution for preventing overfill and detecting leaks, and if any incidents do occur, comprehensive response plans and training reduce the severity of incident damage to a minimum.