By Richard Irwin, Solution Marketing Manager, Digital Twin and Industry Marketing, Bentley Systems
A digital twin is a highly detailed digital model that is the exact counterpart, or twin, of a physical asset. Connected sensors on the physical asset collect data that can be mapped onto the digital model. Anyone looking at the digital twin can view crucial information about how the physical asset is
performing in the real world so that workers can easily make informed decisions, enabling timely corrections to underperforming assets.
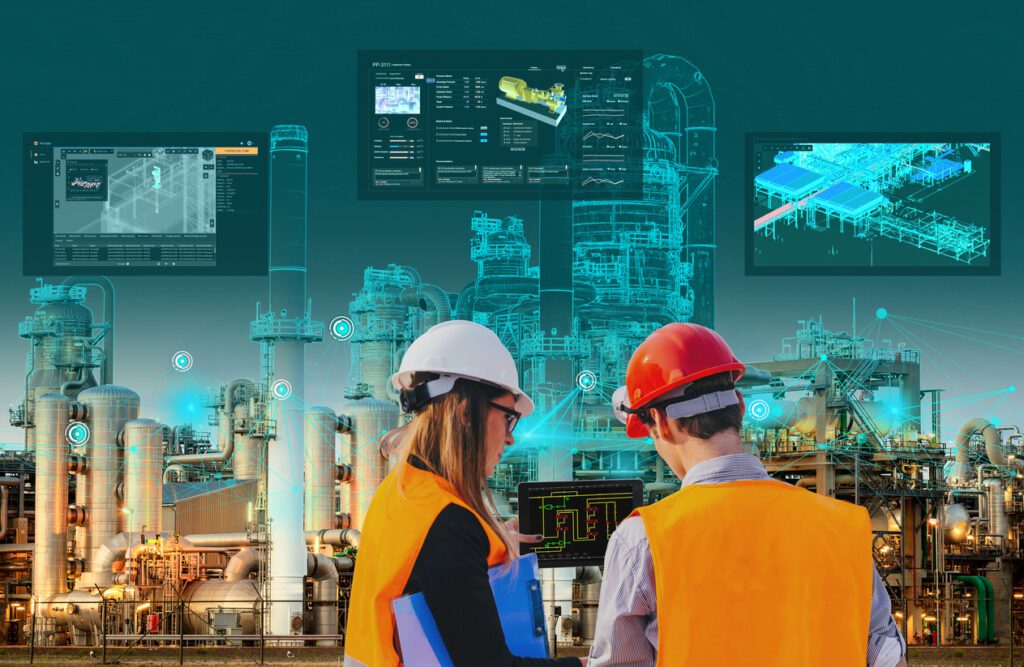
PlantSight is Bentley’s digital twin solution built specifically for the process industries
One of the main advantages of a digital twin is the line of sight that it provides. A digital line of sight is a digital connection of data throughout an asset’s lifecycle, ensuring information integrity and accuracy, as well as timely access to data. Lack of line of sight puts any operation at risk because personnel cannot make decisions without accessible, trusted, and up-to-date information. Process industry leaders have turned to digital twins, such as PlantSight, jointly developed by Bentley and Siemens, to connect data, systems, and people in an accurate and immersive visual context for digital line of sight.
A variety of personnel can view digital twins and gain specific benefits. Below are examples of personas who, via a digital twin, can work seamlessly together for a clear line of sight across the whole operation.
Designing For Resilience
For design, process, and plant engineers, collaboration is key when designing a new plant,making modifications to existing plant or planning turnaround projects. When multiple engineers are working on a model, one of the biggest challenges that they face is knowing where the critical documents and data are, as they are often difficult to validate and visualize. Engineers want to maintain a timeline of changes and capture how, when, and by whom the changes
were made. Some applications lack a timeline of changes, causing work duplication, work on the wrong model, and working without up-to-date information. What engineers require is a single source
of information, where they can easily access associated documents, manuals, procedures, piping and instrumentation diagrams (P&IDs), and CAD drawings. A digital twin provides that information.
Operational and Reliability Insights
Operational and reliability teams are concerned with plant performance and production, keeping equipment running while maximizing uptime. They deal with millions of data points, sometimes daily, to obtain insights from large volumes of Industrial Internet of Things (IIoT) data. Like the engineering teams, they also need to consolidate and analyze data from multiple sources to know what is going on at all times and discover areas for improvement.
In this case, a digital twin helps identify performance issues by visualizing assets and analyzing condition indicators in context, such as temperature, flow, vibrations, and corrosion. Analyzing condition indicators in the context of the actual plant helps them to identify risks and helps ensure environmental integrity and safety at the same time. A view into key performance indicators (KPIs) alongside the digital twin of the asset provides an overview of current performance and enables comparison to similar equipment and assets in sister plants.
Maintaining the Plant
Maintenance teams are central to operations, as they keep production moving and reduce downtime. Digital twins give them line of sight, providing knowledge of the reason behind each condition indicator and context for each inspection. Digital twins help them gain a better understanding as to why certain tasks are needed, and what to expect in terms of access, lock out procedures and supporting resources. Safety and environmental integrity are paramount, so timely access to safety information, permits, and lock-out/tag-out is important. A digital twin provides a central federated source of information. Visualizing the area, the assets, and the components, as well as understanding the current operating context and current conditions, is vital to the job. Maintenance needs access to engineering documentation and performance information for the pump that triggered an alarm or the pipe that is losing pressure. They require access to key information to see the condition degradation trends and understand the whole process before making decisions on corrective actions. Viewing the asset in a digital twin provides maintenance with the visualization and information they need.
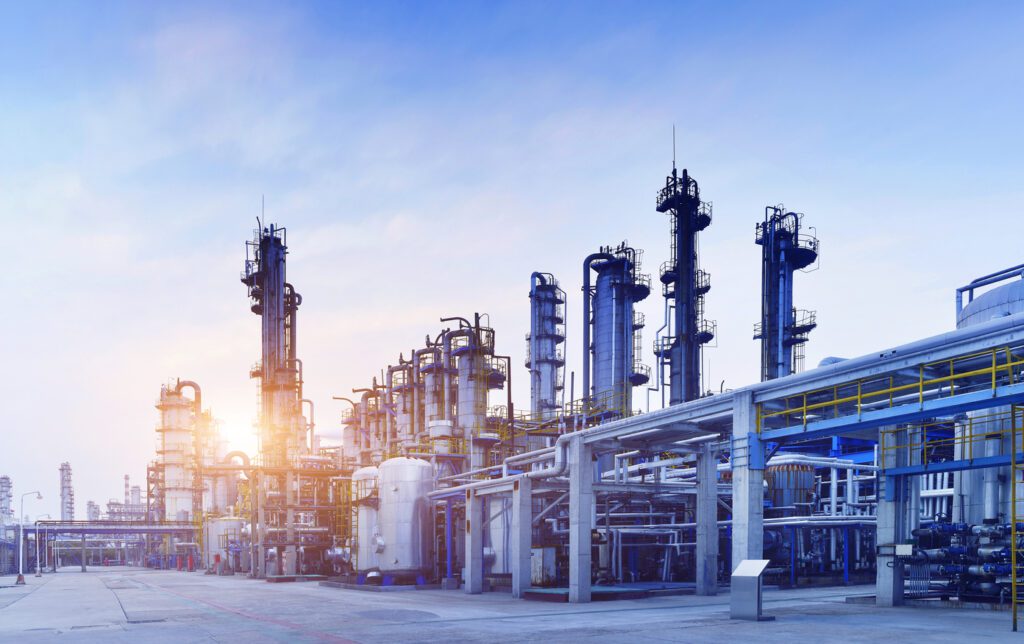
Oil Refinery, Chemical & Petrochemical plant at sunset.
View from Above
Further up the organization, senior management and directors can access the key safety and risk indicators for a complete and consistent view of the plant in a single portal. Within the digital twin, they can instantly view performance, production, and costs; obtain proof of regulatory compliance; and measure against KPIs and targets. With this information, they can make strategic and informed asset management decisions and put policies in place based on these goals.
Organizations will more easily attain their performance objectives and realize the best value from their assets if they establish digital line of sight, enabled by a digital twin. Digital line of sight will help the workforce collaborate and reach high levels of operational excellence, with minimal effort and in the shortest time possible.