Use this guide to aid the selection of conveying technologies for applications in powder and bulk solids handling.
Many sectors of the chemical process industries (CPI) — including chemicals, plastics, batteries, mining, power generation, plastics, food, agriculture, pharmaceuticals and others — handle a wide range of bulk solids and powders in manufacturing. Research has shown that more than 70% of all products contain ingredients that are handled in bulk solid or powder form at some point during the production chain. Each bulk solid tends to have its own unique characteristics, behaviors and requirements for getting it (and keeping it) flowing and moving through solids handling equipment. Solids-handling equipment, such as bins, silos, hoppers, feeders and chutes have their own set of difficulties and challenges for getting material flowing [1–3], and conveyors are no different.
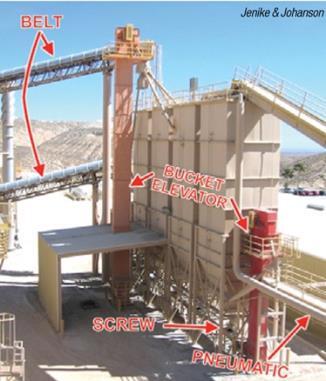
Figure 1. Several examples of conveying equipment are
shown in this solids-handling facility.
There are dozens of different conveying technologies, many of which may be marketed as a “one-size-fits-all” solution for moving bulk solids around. However, there can be significant consequences if you don’t get conveying “right.” Depending on your material, application, and conveying technology, you may experience production bottlenecks, flow stoppages and plugging, poor or inefficient transport, product degradation or particle breakage, as well as rapid abrasive wear, segregation and product variability, spillage, dust release, excessive maintenance requirements, or a number of other issues. So when selecting the “best” conveying technology for an application from the start, it becomes essential to cut through some of the vendor claims to mitigate risk of experiencing these handling issues.
This article outlines important factors to consider for conveyor selection, and discusses the pros and cons and appropriate use cases for common conveying technologies.
Conveyor types and functions
For the purposes of this article, conveyors are technology or equipment, other than gravity, for moving dry bulk solids through a process. This includes moving solids horizontally, diagonally or vertically, and may involve multiple pickup or discharge points. Unlike bulk solids feeders, conveyors are not choke-fed from a hopper, and they operate only partially full (typically at only 30–50% capacity or less). In addition, they do not meter or control the solids-throughput rate, and generally operate at constant speeds. Feeders tend to be quite short, while conveyors often move materials over significantly longer distances. In fact, there are some belt conveyors used to transport heavy ores several miles overland, with the world’s longest belt conveyor system carrying phosphate ore more than 60 miles (97 km) from a mine in the Sahara desert to a shipping port [4].
Proper design and selection of bulk-solids feeders, as well as attending to details of how feeders interface with conveying systems are also extremely important for ensuring reliable process operation and avoiding bottlenecks, but are beyond the scope of this article. Conveying technologies come in a wide number of shapes, sizes and configurations. Some of the most common types include the following::
• Pneumatic conveyors
• Screw conveyors
• Belt conveyors
• Bucket elevators
• Vibratory conveyors
• Drag chain and cable conveyors
• Fluidizing conveyors (for example, airslides)
A typical industrial process with a number of these technologies is shown in Figure 1. The list above is only a partial listing of conveying technologies, and there is significant variety and specialized conveyors with unique features within each of these categories. Regardless of what type of conveyor you use to move your material, all conveyors should meet the following requirements:
• Reliable transfer of the material from the pickup point(s) to the delivery point(s), at the required flowrate, with no pluggage or material buildup within the system
• Minimal product degradation or particle breakage, if required
• Minimal abrasive wear
• Reasonable energy consumption
• Safe operation with minimal spillage and dust release
• Sensible maintenance intervals, with minimal operator intervention required between intervals
• Sufficient flexibility to fit within the available space
Conveyor selection criteria
When selecting what type of conveyor to use in a given application, it is important to ask some of these critical questions:
Material properties. Is the solid material free-flowing? Cohesive and sticky? Frictional? Fine, dusty and aeratable? Friable/breakable? Abrasive? Corrosive or reactive? What’s the bulk density? What is the particle-size distribution, including the largest clump or lump size? Could the material’s characteristics change over time, for example, due to variable moisture content? Or would the conveyor handle multiple different materials?
Required capacity or throughput. Does the conveyor selected have sufficient capacity, such that it can transfer material from all pickup points to all delivery points, without acting as the rate-limiting step in the process? Could there be surges or fluctuations in throughput due to upstream processes? And does the conveyor have sufficient capacity to accommodate those surges? Could the production rate possibly increase in the future?
Facility layout requirements. How far does the material need to travel between pickup and delivery? Is it a relatively “straight shot,” or does the route require a lot of twists and turns around corners or interferences? Is required conveying mostly in the horizontal direction, or is there a large amount of vertical lift required? Does the material need to be elevated in a relatively small footprint? Is there sufficient footprint and headspace available for the conveyor to fit? Are there multiple pickup points and multiple delivery points, or could more be added in the future?
Process conditions. For example, is the material or gas near ambient temperature, or at very high temperatures? Will there be significant temperature swings?
Special safety considerations. What happens if the material is not well-contained and dust is released or spillage occurs? Is the material toxic? Is it a respiratory hazard? Are there combustibility or explosibility issues? Or even just a housekeeping nuisance? Does the solid material need to be handled under inert gas to prevent combustion, oxidation or other reaction?
Potential for foreign-material contamination. Could there be undetectable pieces of plastic or non-magnetic metals that could break or wear off in the conveyor and contaminate your product? This is of special concern for handling food or pharmaceutical products.
Particle degradation and breakage. Would particle degradation and breakage impact product quality or material flowability? Could there be issues with product cross-contamination?
Discharge characteristics. Would batch or pulsatile discharge affect your process, or do you need a consistent, steady stream? Some conveyor types tend to discharge material in periodic fluctuations or pulsations, while other types of conveyors are better-suited for delivering a consistent, steady, continuous stream to downstream equipment.
Conveyor cleaning. Does the conveyor need to be cleaned out completely (for example, between grade or recipe changes), or is it acceptable to have some residual material left in the conveyor even after it is emptied? Does the conveyor need to be cleaned out or washed down frequently for sanitary purposes?
Costs. Have you considered the operating costs over the life of the conveyor, and not just the initial up-front capital costs to purchase and install the equipment? Some factors that can drive higher operating costs (opex) are higher energy costs to move the material, poor operation and unreliable conveyance that requires more operator intervention and reduced production, more frequent maintenance requirements due to component breakdown and erosion over time, and downtime to fix defective parts. Many mechanical conveyors, such as screws and belts often have higher upfront capital costs (capex) compared to pneumatic conveyors, but they also generally have much lower energy costs, which reduces opex. On the other hand, mechanical conveyors also have more moving parts and are typically more maintenance-intensive that pneumatic systems. If the mechanical conveyor is not properly selected for your application, frequent maintenance requirements could significantly increase the conveyor’s opex, so that the mechanical conveyor could ultimately cost more in the long run. Additionally, some lower-capex mechanical conveyors may be more prone to erosion, breakdown or failure versus other lower-capex mechanical conveyors, so a lower-capex conveyor may actually have much higher opex and may cost you more over the life of the equipment compared to a scenario where you spent a little more up-front. It’s all a balancing act.
So, now with those questions and considerations in mind, how do you move ahead in selecting a conveyor? The next sections of the article explore the features, advantages and disadvantages of some of the most common conveyor types. Note that “standard” features are discussed for each category. There are many specialized features and other conditionals that could improve each conveyor’s characteristics and capabilities.
Pneumatic conveyors
Pneumatic conveying involves using air or another gas to transport the solid material through a pipeline, at moderate to high 4 velocities. Pneumatic systems are often highly attractive, since they generally have low capex, and they are also by far the most flexible conveying technology from a layout standpoint. Pneumatic systems can easily support multiple pickup and delivery points and it is fairly simple to route piping through a plant. Also, pneumatic systems do not occupy a lot of space, and it is easy to run both horizontally and vertically. They can often use existing pipe racks or supports, and can be run over long distances.
There are two main modes of pneumatic transport:
• Dilute-phase — Particles are fully suspended in the conveying gas, at relatively low pressures drops, high velocities, and low solids loadings (typically 3–15 psig and 50–80 ft/s or more at pickup).
• Dense-phase — Particles are only partially suspended in the gas, at high pressure drops and lower velocities, and at much higher solids
loadings (typically 25–150 psig and 10–40 ft/s at pickup). Dense-phase conveying also has two discrete regimes, each of which are suitable for very different materials and applications: moving-bed (“dune” flow), which is often used for conveying fine, aeratable and free-flowing powders like alumina or cement, and piston-plug flow, which is often used for conveying coarse, highly permeable materials like plastic beads or catalyst pellets.
Both dilute- and dense-phase can be done using either positive pressure gas to “push” the material through the line towards the delivery point, or using a negative pressure (vacuum) to “pull” the material through the line. The main advantages of pressure systems versus vacuum systems are that pressure systems can transport higher tonnages (up to 300 ton/h for pressure, compared to only up to 100 ton/h for vacuum), over longer distances (up to 1,000 ft for pressure versus only about 200–300 ft for vacuum), and at lower velocities, and pressure. Also, pressure-based systems are well-suited for conveying under inert gases and preventing air/oxygen ingress. The main advantages of vacuum conveying are that all leakage occurs inward, making it highly attractive for containing toxic dusts. Vacuum systems are also very well-suited when there are many pickup points and a single delivery point (for example, in dust-collection systems).
Table 1 includes a comparison of the main features, advantages and disadvantages of dilute- and dense-phase pneumatic transport, along with how they compare with a number of different common mechanical conveying technologies. One additional potentially major disadvantage of pneumatic systems to consider is that they require additional dedicated filter equipment (such as cyclones, baghouses, cartridge filters) for separating the material out of the conveying gas stream, whereas mechanical systems generally do not.
Mechanical conveyors
The major features and limitations of several types of mechanical conveyors are included in Table 1. Typical applications for some of the most common technologies are summarized below.
Belt conveyors. Belt conveyors are used for transporting a massive range of products in a wide variety of industries, from fine food and chemical powders, up to heavy coarse ores from mining operations. One of the main strengths of standard belts is their ability to convey extremely high tonnages over long distances, while some of their main drawbacks are that they are generally not very good at containing dusts, are not very flexible from a layout standpoint, and are not suited for quickly elevating or lifting material vertically. Typically, relatively shallow inclines only up to about 15 deg are acceptable, meaning long distances are required to lift material. Specialized types of belts are available (for example, chevron or cleated belts, pocket belts, sandwich belts, tube belts) which can better contain dusts, may have better layout flexibility and ability to navigate around turns and corners, and can convey up steeper angles.
Screw conveyors. Like belts, screw conveyors are used in a huge array of applications and with materials across most industries, but they are generally not suited for “heavy duty” applications with heavy, coarse, abrasive materials like ores and minerals. The main strengths of screws are their cost-effectiveness and mechanical simplicity, as well as their ability to contain dusts, while their main drawbacks are their limited length, their generally poor layout flexibility, and their relatively low capacity compared to other types of mechanical conveyors. Also, solid material “grinds” as it moves through the screw, which can cause significant particle breakage or degradation with some materials. Standard screw conveyors also tend to have more residual material left in the conveyor than other types of 6 conveyors, even when they’re “empty” due to “dead” material that remains at the bottom of the screw trough, which can create cross-contamination issues.
Screws come in a number of specialized configurations, including flexible screws that can convey material up relatively steep inclines, vertical screws that can elevate some materials over relatively small distances up to about 20 to 30 ft, coreless, ribbon-flighted screws, which are more resistant to buildup of sticky materials. There are also screws that have some blending capability that can be used in some applications, and some screws that can be used for heating or cooling during transport. Some screws are also available with “drop-bottom” troughs to facilitate more complete cleanout, and limit cross-contamination risk.
Bucket elevators. Bucket elevators (also known as “legs”) transport material in a series of small, discrete buckets attached to a chain or belt, and are most often used in the food and agricultural, chemical, and consumer-goods industries (Figure 2). In the most common configuration, at the infeed, buckets dig material out of the bottom of the conveyor (the “boot”) as they round the tail sprocket and begin to lift material vertically up. Then, centrifugal force ejects material toward the outlet as the buckets round the head sprocket at the top of the conveyor. These digger-type and centrifugal-discharge elevators should not be used with materials that are cohesive, breakable, or abrasive because the digging action can compact the material in the boot, cause significant particle breakage and degradation, and lead to rapid wear of the chain, sprocket and the buckets themselves.
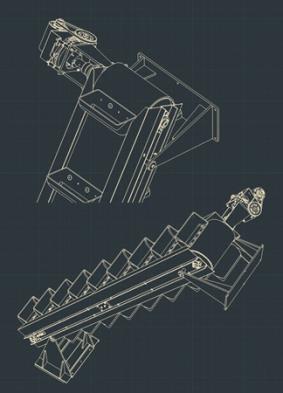
Figure 2. Bucket elevators, like the one shown in the diagram here,
transport material in discrete buckets attached to a chain or belt.
There are also continuous bucket elevator configurations designed to overcome some of the issues with cohesive, friable or abrasive materials. In this type of elevator, the buckets are generally fed horizontally (rather than vertically) and there is no separation between buckets, an effort to avoid the digging action in the boot and allow more gentle feed and discharge. At the discharge in centrifugal designs, material is ejected from the buckets toward the outlet as the buckets come around the head sprocket at the top, while other designs instead allow the buckets to rotate and tip over as they reach the discharge, to dump out material more gently than the high-velocity throwing motion in centrifugal designs.
Bucket elevators’ main strengths are their ability to convey high tonnages, to quickly elevate materials to large heights, and continuous bucket designs can be very gentle on the product and minimize degradation. The major drawback is that bucket elevators are generally the most maintenance-intensive conveying technology. Even with “heavy-duty” construction, they frequently experience issues with chains breaking or coming off the sprockets over time, particularly with digger-type bucket designs.
Tubular drag conveyors. Tubular drag conveyors (Figure 3) pull material through a pipe or tube using a series of equally spaced slow-moving pucks or discs attached to a continuous cable or chain, with drive and turnaround sprockets at either end of the conveyor. They are most often used in the food, chemical, consumer goods and chemical industries for cost-effective, well contained or enclosed (for minimal dust release), gentle transport of powders with minimal degradation. The main strengths of tubular-drag systems are that they require relatively low capex, they have the most layout flexibility of any mechanical conveyor and can make up to 2–3 turns horizontally and vertically within a single conveyor. They also allow complete containment or enclosure to minimize dust release, and their low velocity minimizes particle degradation or breakage. They can easily support multiple feed and discharge points.
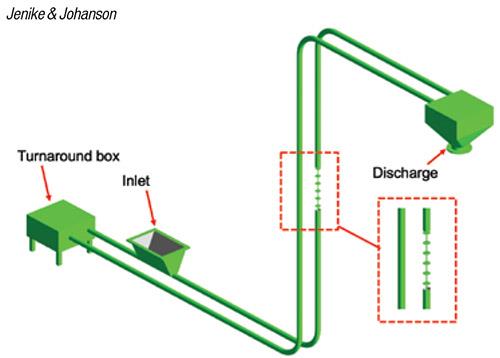
Figure 3. Tubular drag conveyors pull material through a pipe using
pucks or discs attached to a continuous cable or chain.
One of their main drawbacks is they tend to be somewhat maintenance-heavy when not properly applied. First, they are generally not built as “heavy duty” as other mechanical conveyors types, so they are often not well-suited for applications with heavy, abrasive materials. They should also not be used with cohesive solid materials, because the material tends to build up on the tube walls and “smear.” With chain-driven types, sticky material often builds up on the chain over time. With cable-driven designs, tension causes the cable to stretch out over time, so the pucks do not properly mount in the turnaround sprockets and eventually derail the cable. The cable frequently needs to be re-tensioned and periodically replaced. With chain-driven types, the chain is also prone to derailing from the sprockets, because it often becomes twisted as the conveyor repeatedly turns, and with cohesive materials, buildup on the chain can prevent the pucks from properly mounting in the teeth of the drive and turnaround sprockets (although there are optional brush features to attempt to reduce some of this buildup). When the pucks get derailed, the conveyor needs to be shut down to untwist the chain and remount the pucks.
Concluding remarks
While dozens of different conveying technologies are available, and the technologies have improved over the years, no single “best” conveyor for moving all bulk solids exists. All of today’s technologies have particular strengths and weaknesses. The most appropriate conveyor is intensely dependent on the solid material being conveyed and your process. To minimize the risk of production bottlenecks due to poor conveyor operation, product-quality issues, or issues with high operating cost due to significant maintenance requirements, when choosing your conveyor, it is essential to consider your material’s characteristics by measurement in a qualified testing laboratory using proven scientific methods [5–8], l as your specific process conditions and application needs.
Edited by Scott Jenkins
References
1. Marion, J. Preventing Flow Problems With Reliable Bulk Solids Handling Equipment Design, Processing Magazine, September 2019, pp. 32–35.
2. Marion, J. Bulk Solids Flow: Know What You’re Dealing With, The Chemical Engineer, June 2020, pp. 36–40.
3. Maynard, E. It is NOT just a chute!, Dry Cargo International (DCI), March 2018, p. 49.
4. Atlas Obscura, The World’s Longest Conveyor Belt System, 2014. https://www.atlasobscura.com/places/the-worlds-longest-conveyor-belt-system-bou-craa-morocco
5. Carson, J.W. and Marinelli, J. Characterize Bulk Solids to Avoid Flow Problems, Chem. Eng., Vol. 101, No. 4, April 1994, pp. 78–90.
6. Maynard, E. Ten Steps to an Effective Bin Design, Chemical Engineering Progress (CEP), November 2013, pp. 25–32.
7. Jenike, A.W. Storage and Flow of Solids, Bulletin 123, University of Utah Engineering Station, 1964 (revised 1976).
8. ASTM D-6128, “Standard Test Method for Shear Testing of Bulk Solids Using the Jenike Shear Cell”