A shortage of technical talent and experience is challenging many in the chemical process industries. Steps that can be taken to improve the situation are discussed
The changing professional climate and the vexing economic situation among technology-based companies are leading to a shortage of technical knowledge as compared to past years. This technical talent shortage can affect company performance, and cause companies to be less competitive than in the past. The reasons causing the change are varied, but include retiring technical specialists, the change in goals among young professionals, the shifting of work overseas and the lack of systems to capture historical “lessons learned.”
While there is no single solution to overcome the technical talent shortage, there are steps that can be taken to improve the situation. These include involving retired professionals as consultants, and within companies, instituting mentoring programs between technical experts and aspiring young professionals. In addition, knowledge management systems can be put in place to capture technical information, and progressively used to guide technical growth in a company. Elevating the career path of technical roles is a means of encouraging young engineers to focus on technical knowledge growth and become subject matter experts. While technical depth within companies may not reach the level of past years, there are ways to ensure that projects receive proper technical coverage. Another option is to form strategic partnerships with companies that possess the required technical skills and competencies. This article discusses different sides of the issue, and presents various alternatives that companies can pursue as a remedy.
Importance of technical depth
Competitiveness among design companies, and the need for operating organizations to immediately and creatively address problems, is making it more important than ever to have strong technical talent in these organizations. The design company that offers a unique and economical solution is generally the one that wins new business. For operating organizations, lost production time can quickly affect bottom lines, so having expert engineering talent available to immediately address problems is crucial. Solid designs are often a result of years of design changes with each succeeding change enhancing the durability and operability. This evolution can only be realized with core technical talent that has “lived” the changes, understands the nuances and has a keen mind for continual enhancements. Continual innovation within companies is a key differentiator in a challenging business world, and the best way to get there is to have solid technical talent.
The problem
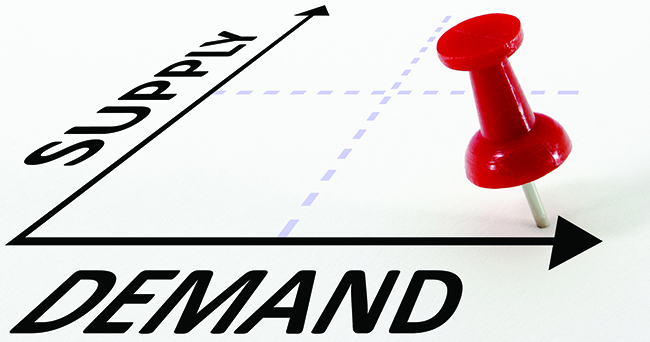
FIGURE 1. The shortage of skilled workers is due to an imbalance in supply and demand
There are several reasons why the shortage of technical talent has been exacerbated in recent years (Figure 1), but a main reason is that many “baby boomers” have been retiring, taking a wealth of technical knowledge with them. These retiring engineers often grew their technical knowledge as advances were made in their respective technical areas. This provided them with in-depth knowledge and the ability to address problems based on experience. Most of the retiring engineers started their careers doing hand calculations with minimal technology aids, such as programmable calculators and computer programs (Figure 2). Following this path forced them to have a deep understanding of technical issues and then to grow their knowledge with exposure to problems and the addition of technology aids. Such a path does not exist today, and young engineers are often forced to “hit the ground running” with no mentoring, and have little choice but to use packaged programs.
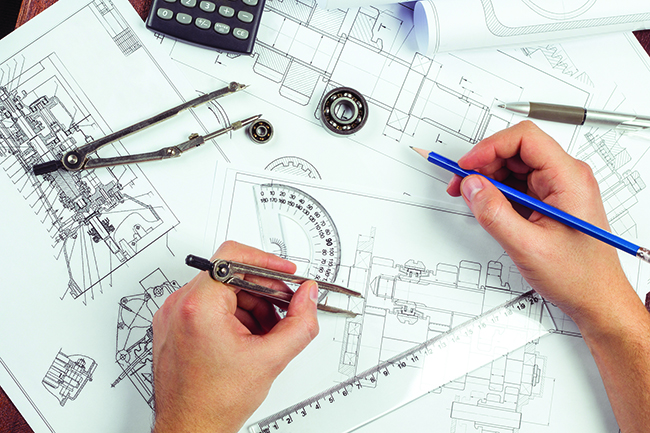
FIGURE 2. Engineers develop expertise using traditional tools over decades
The authors are acquainted with an octogenarian who was the last stop for technical problems at their previous company. He approached each problem with a yellow pad and pocket calculator, with occasional reference to a textbook. His huge technical depth allowed him to address the most daunting problems without sophisticated engineering computer programs, while providing unique technical and workable solutions.
Lack of technical growth. In past decades, the technical expert in a company was a highly respected professional, and a person young people strove to emulate. This is generally not the case today and the most highly respected professionals in a technical organization are often those in the business side of a company. Technical growth is often not recognized and rewarded. Consequently, young people often favor careers in business, marketing and finance. Technical positions are not viewed as “fast track” and today, quick forward movement is important to the young professional. Biding your time to become the best technical expert is not even a point of consideration for most technical professionals today. On top of this, the current trend is for engineers to switch jobs more frequently than in past years. The downside of this is that technical growth is not often continuous across job changes, and taking the masses of people switching jobs frequently, the overall technical growth in companies is diminished.
Overtaxed experienced workers. The current emphasis to cut costs in most organizations has resulted in experienced workers being overextended, with no time left to mentor and coach young professionals. In addition, the focus on cutting costs has led to a decline in training programs, both in-house and external. At the same time, attending conferences and participation in industry groups (such as the AIChE local chapter) are sometimes not supported by the corporation. Hence, young engineers are left on their own to develop professionally.
Education. Another reason for a lack of technical depth is that some studies have shown that schools are not adequately preparing students for engineering roles, and fewer students are graduating with engineering degrees [ 1]. The recent recession in the engineering profession may be a reason for more students not pursuing technical educations. With a shallower technical depth of engineers entering the workforce, mentoring becomes increasingly important. While larger companies may have the resources for shadowing, rotational programs and training, smaller companies often do not have the resources for such programs. Because engineers often have to “hit the ground running,” they rely on computer programs that provide data-in and data-out, while the engineers sometimes do not have an in-depth technical understanding of the evaluation process and results.
Not capturing technical information. Coupled with shallower technical talent in recent years is the problem that most companies do not have a system to capture and share knowledge and experience of the more experienced (and often retiring) professionals. The authors have been exposed to “lessons learned” databases in their companies, but these are generally not maintained because of time limitations, and therefore crucial technical knowledge is not captured. The added problem is that captured information is often not viewed regularly and therefore opportunities to benefit from past technical gains are not realized. On top of lost technical gains, there generally are no formalized succession plans. Therefore, as more experienced engineers reach retirement age, “rules of thumb” and other key technical knowledge are not passed on to younger engineers.
Global competition. The tight commercial aspects of U.S. projects has often driven companies to seek less expensive engineering overseas. Known as High Value Engineering Centers (HVECs), these companies are prevalent in countries such as India, China and the Philippines, and offer U.S. engineering, procurement and construction (EPC) and owner-operator companies the opportunity to save considerable money on engineering costs associated with major projects. A downside of this approach is that the technical knowledge gained in executing projects is moved overseas, and U.S. companies have less opportunities to benefit from design experience. Over time, this will lead to further diminished technical knowledge in the U.S. and the possible need to engage foreign companies to address emerging problems.
Construction talent. While the focus of this article so far has been on engineering knowledge, the same issue with declining talent applies to the construction trades. Even though the construction industry may not be booming as in recent years, still there is insufficient skilled labor in many trades. The younger generation has generally been pushed toward college and not toward the vocational trades. Therefore, this has left a serious gap in construction capabilities, and often leads to construction inefficiencies [ 2]. Finding acceptable and sufficient construction talent is one of the major challenges facing construction and EPC companies. Some of the steps that are being considered include the following:
- Promote vocational training in schools
- Offer competitive salaries and benefits
- Provide advancement opportunities within a company (For example, promote welder to construction manager)
- Provide cross-training, including estimating and proposal development to field personnel
Possible solutions
Some possible solutions to the impending problem of a lack of technical talent are discussed here.
Take advantage of experienced personnel. Experienced technical professionals in the age group of 50–70 have a lot to offer. This includes experience gained over decades in a variety of companies and projects and spanning multiple technical functional disciplines. The perspective gained from real-world experiences, coupled with strong technical fundamentals, provides a formidable combination, which cannot be replicated by computer programs. There is also a natural tendency on the part of experienced people to pass on their knowledge to the younger generation. Corporations need to create a climate where it is easy for young people to reach out to experienced people (Figure 3). This interaction can be facilitated by having people co-located, an open door policy and the availability of some spare time so that employees never have to make a choice between completing a project versus teaching a younger professional.
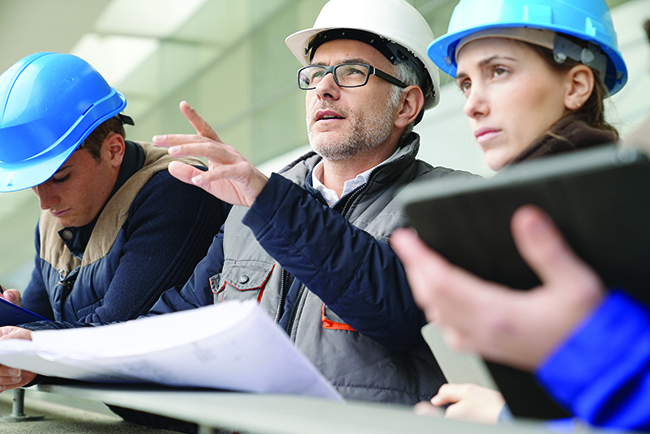
FIGURE 3. Corporations need to create a climate where it is easy for young people to reach out to experienced people
Engage retired people on a temporary basis. As noted earlier, people who worked long-term have significant technical knowledge into which to tap. A win-win option for a company and retired person is to establish an hourly contract, allowing the company to call on the technical expert as needed. This is an economical option because the retired person is paid only when working, and this option provides easily accessible technical knowledge on short notice. For the retired person, there is an opportunity to stay engaged on a part-time basis, and earn some modest income.
Employ knowledge management. There are numerous computer programs that capture, organize and maintain detailed technical reports and calculations. It is relatively easy to classify and organize reports in such a way to make searching relatively easy. The challenge is to create a culture where knowledge management is valued and information exchange is the norm. This capability is especially important in a large, multinational company that is project driven. In such organizations, the project team usually disperses after completion of a project. The lessons learned and best practices developed usually also get dispersed unless a conscious effort is made to capture and use that knowledge.
Increase training. In the recent past, it was typical for large technology-based companies to encourage employees to dedicate two or three weeks annually to formal technical and skills training. It was quite common to attend one or two technical conferences. This meant young professionals could interact with others in industry, develop a professional network and develop leading-edge skills at the same time. The costs were not scrutinized and the benefits were assumed to come from employees being more satisfied and productive in the long run. This training was integrated into the annual performance plan and employees were measured on how well they completed their training.
Make technical career paths more rewarding. Many large technology companies have created a technical ladder where a senior person can have the same prestige, salary and benefits as other executives without having to manage a large budget or a large number of people. Such an arrangement encourages professionals to dedicate their career to a technical specialty instead of gravitating toward a business or finance role that carries better rewards.
Form strategic partnerships. Sometimes it is better to form a strategic partnership with a company that has the required technical knowledge base as a core competency. A good example is the strategic partnership formed by Air Products (operating company) with Technip (engineering company) in HYCO plants. Such a partnership can be a win-win, enabling both companies to prosper and build differentiation in the marketplace.
The bottom line
The changing times are leading to a situation in which growing and maintaining technical depth in an organization is challenging. Many very experienced engineers are retiring, and often there is no backup for the lost talent. With a current focus on fast-track advancement, young professionals are often driving their careers toward the business side of a company. In cases where technical growth is sought by young professionals, there generally are no mentoring or training programs in place to capitalize on the available knowledge. On the construction side, skilled craft is also in short supply as young people have been steered away from the trades. Definite steps are necessary to ensure that engineering and construction talent is developed to support projects and operating facilities, plus long-term company growth.
Taking steps to capitalize on experience within a company is a needed process to ensure that technical depth is not lost. This means that experienced engineers are encouraged to mentor young engineers, and young engineers are encouraged to proactively seek out the knowledge. Also, creating technical career paths within a company is a means to reward people desiring a technical path over a business/management path. Calling on retired technical experts is one means of quick relief for the talent drain, and also forming strategic partnerships is another approach. However, the best long-term solution is creating a culture where technical knowledge is valued, and companies strive to encourage and recognize individuals with a desire to be “best in class” in their technical field. The outcome will be more technically respected companies and professionals with a renewed eye toward the technical side. ■
Edited by Dorothy Lozowski
References
1. www.nextlevelstaff.com/2017/03/24/shortage-engineering-talent, “Why Is There a Shortage of Engineering Talent?”
2. C. Rentschler and G. Shahani, Construction — The Cornerstone for a Successful Project, Hydrocarbon Processing, December 2017.
3. C. Rentschler and G. Shahani, Outsourcing and Offshoring Engineering and Fabrication Activities, Chemical Engineering, August 2017, pp. 56–59.
Authors
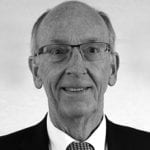
Carl Rentschler
Carl Rentschler, P.E. is an engineering consultant specializing in project management, business development, client relationship management and procedure development (210 Main Street, Akron, PA 17501; Phone: 717-951-4772; Email: [email protected]). He has more than 40 years of varied engineering and management experience in the power and petrochemical fields, with three international engineering-procurement companies. He holds a B.S. in civil engineering from Penn State University and an M.Eng. in civil engineering from Cornell University.
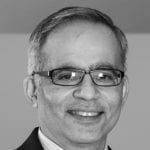
Goutam Shahani
Goutam Shahani is vice-president of sales and marketing at Shure-Line Construction (P.O. Box 249, Kenton, DE 19955; Email: [email protected]; Phone: 302-420-1100). Previously, he was business development manager at Linde Engineering North America. Shahani has more than 30 years of industry experience, and specializes in industrial gases for the energy, petroleum refining and chemical industries. He holds a B.S.Ch.E from the University of Bombay, and an M.S.Ch.E. from Illinois Institute of Technology, and an MBA from Lehigh University.