To maximize the service life and reliability of rotary dryers for solid materials, adhere to this set of practices
Rotary dryers have a well-deserved reputation for reliability, often providing decades of trouble-free operation in solids-handling processes. As with any type of process equipment, however, the reliability of a rotary dryer and its ability to consistently dry bulk solids hinges on proper operation and maintenance of the unit (Figure 1). This article covers best practices for rotary-dryer operation that will help to maximize the service life and reliability of the rotary dryer, while maintaining product integrity in industrial settings.

FIGURE 1. Rotary dryers like the one shown here, can be highly reliable when properly operated and maintained
Maintain a consistent feed
Rotary dryers are known for their tolerance to variation in feedstock conditions, such as particle size and moisture content. And while the tolerance for feedstock variation is real, the best results are still achieved by maintaining a feedstock that is as uniform as possible in all aspects. The more uniform the material going into the dryer, the more uniform the material will be coming out.
Operators struggling with product consistency issues often find that a large variance in feedstock conditions is to blame. In some settings, maintaining a uniform feedstock for a dryer may not be possible, but options do exist for minimizing excessive variation. One way to improve the uniformity of feedstock going to the dryer is to use a technique called “backmixing,” which is achieved by mixing finished (dried) product with the raw feedstock before it enters the dryer (Figure 2). This evens out the overall moisture content of the material entering the dryer.
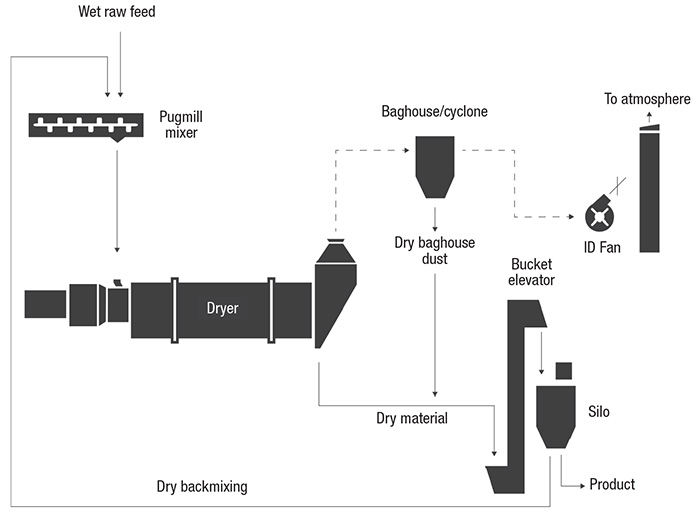
FIGURE 2. The diagram illustrates a common backmixing setup to improve the uniformity of the feedstock
A more efficient way to manage variation is to eliminate it from the source material. This may involve a change in vendor specifications (or even a change in vendors), adding a pre-conditioning system, or making improvements in the process upstream of the dryer. In many cases, a process audit will reveal that by optimizing the performance of equipment upstream of the dryer, variation can largely be mitigated.
Never run empty with heat
One rule all operators and maintenance personnel should understand is to never run the dryer empty with heat. When the drum runs empty, there is no material to absorb the heat and protect the dryer. Similarly, the burner should never be left running while the dryer is not rotating.
Running the dryer empty or without rotation in the presence of heat has the potential to cause warping or deflection of the drum shell as a result of uneven heat distribution. A drum that is heated without rotation will result in localized heating, which causes the drum to sag.
If the temperature of the shell is allowed to exceed the yield strength of the material of construction, deformation of the shell will be permanent. In most cases where deflection has been allowed to occur, total shell replacement has been necessary.
Deflection causes additional problems where refractory material is employed, because the refractory will experience heat stress at a different rate than the shell, causing cracks or breaks in the refractory.
Minimize buildup
Depending on the material being dried and the design of the rotary dryer, buildup of material inside the drum can become an issue. Minimizing the amount of buildup that is allowed to occur is critical to the drum’s longevity and efficiency.
Buildup in the dryer is problematic for a number of reasons. First, it reduces the overall efficiency of the drying process and often results in off-specification material. Buildup also has the potential to cause clumps of material that eventually break away from the dryer wall. When this happens, it can damage both the interior of the dryer and the flights (material lifters; described below), as well as the discharge breeching (where the product exits the dryer). Buildup that does not break away can pose a risk of fire for some materials. If the material is corrosive, buildup promotes excessive corrosive wear on the dryer walls and flights.
Several techniques exist for minimizing the potential for buildup in the dryer. Knockers, affixed to the drum’s exterior, are one effective solution and work by “knocking” the drum (on a wear plate) to dislodge any buildup on the interior as the drum rotates.
Another option is to utilize a “bald” section (an area of the dryer without lifters) and use less aggressive lifters at the dryer inlet to avoid sticking.
Screw conveyors, which “throw” material into the dryer, can also help to minimize buildup by breaking up any clumps.
Keep seals in good condition
The seals on a rotary dryer, which connect the drum to its stationary housing, are critical in preventing ambient air from leaking into the system (Figure 3). Ambient air allowed to leak into the system reduces the dryer’s temperature, which can have a variety of implications depending on the application and the severity of the leak. Common problems associated with leaking seals include increased fuel costs, reduced efficiency, lower throughput, and under-dried product.
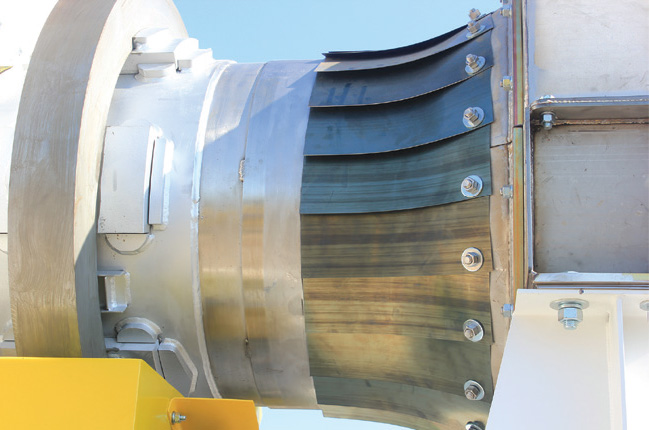
FIGURE 3. Shown here is a single-leaf seal
If these problems are observed, along with visible wear on seals, signs of material back spill, or abnormal auditory cues, it is often an indication that seal repair or replacement is necessary.
Inspections and maintenance
It may sound obvious, but regularly inspecting and maintaining a rotary dryer in accordance with the original equipment manufacturer’s recommendations is the easiest — but yet most neglected — way to prolong the life and reliability of a dryer.
The constant rotation, longitudinal movement, changing heat stresses, and static and dynamic loads associated with rotary dryer operation all have a tendency to exacerbate and accelerate any problems the dryer may be experiencing. For this reason, it is critical to keep up on maintenance and regularly inspect the unit for any signs of a potential problem.
Regular inspections of the dryer, both internally and externally, allow operators to become familiar with the dryer and identify the onset of any problems early in their development. Ensuring all mechanical components are properly lubricated, resurfacing any wear on tires and trunnions, and routinely having the drum realigned are the foundational elements of keeping the dryer running reliably for years.
Utilize a control system
Control systems for rotary dryers range from basic to advanced and include everything in between. Most rotary dryers built today come with some form of control system to facilitate startup and shutdown and manage airflow and temperature.
Simple process control systems can be upgraded for intuitive automation that provides operators with a variety of data points. Control systems can even be programmed to help prevent potential problems before they occur by recognizing when key criteria fall out of specification and alerting the operator. In many cases, data points can be collected, trended and adjusted from the operator interface, or even a mobile device.
Whatever type of control system is in use, plant operators should be fully trained on the system, so they are able to maximize dryer performance and efficiency. Those operators working with older dryers not accompanied by a control system should consider investing in one, because the efficiency gains can be well worth the investment.
Consider a process audit
A rotary dryer may be underperforming for a variety of reasons — everything ranging from a problem with upstream equipment, to an unseen mechanical issue with the dryer. Whether the dryer is part of a larger bulk-solids processing operation or is a stand-alone drying operation, identifying the source of the problem can be a challenge. Operators struggling to meet specification requirements for products or rated capacity should consider a process audit.
A process audit evaluates the process conditions of the overall dryer system, as well as the surrounding process, identifying areas in need of attention and helping to pinpoint and resolve the origin of complex issues.
The expense of an underperforming dryer, be it in process downtime, lost production, off-specification product, or all of the above, quickly adds up. In addition, running a dryer out of specification for an extended period of time could potentially damage the unit. By opting for a process audit, the path to issue resolution is expedited.
Design considerations
In addition to operational considerations, there are several aspects of the dryer that should be considered during the initial design stages to ensure the dryer is suitable for the intended application and will provide long-term reliability.
Choose a dryer suited to its intended level of duty. One of the most common mistakes made in acquiring or designing a rotary dryer is the application of a one-size-fits-all design. The applications in which rotary dryers are employed vary substantially in their level of duty, and in the specific challenges presented by each job. As such, a one-size-fits-all solution almost always falls short. Dryers designed for use in the biomass industry, for example, would quickly fail under the demanding conditions of the mining industry.
For long-term reliable operation, dryers must be designed around the level of duty required by the intended application. This often means selecting different materials of construction, shell thicknesses, mechanical components, and seals for heavy-duty applications. The materials of construction, along with stringent quality standards in fabrication, are essential to acquiring a dryer that achieves a long lifetime and experiences minimal issues.
Optimize flight design. As with the overall design and construction of the rotary dryer, taking the time to optimize the flight design during the initial design process is also important in achieving an efficient and reliable drying solution (Figure 4).
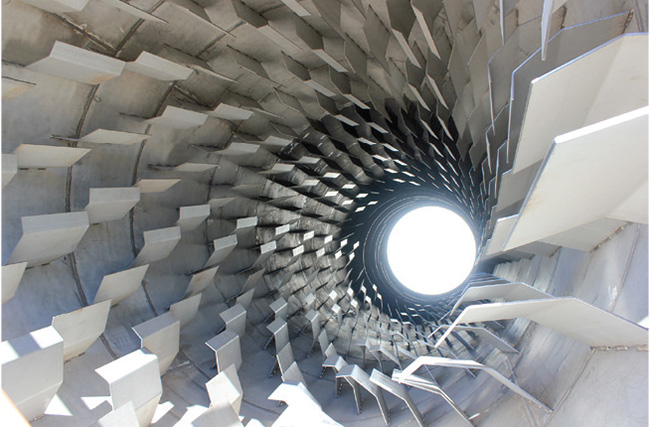
FIGURE 4. An interior view of the rotary dryer with flights is shown here
Flights contribute significantly to drying efficiency, but only if they are designed to work with the unique characteristics of the material to be dried, in combination with drum rotation speed, slope, air velocity and retention time. Flights not designed around such criteria can reduce efficiency, drive up fuel costs, promote buildup, and lead to other problems.
Flights can be customized in both design and pattern, with many dryers incorporating multiple flight designs to accommodate the changes that occur in the material as it moves through the dryer.
Consider a combustion chamber. The combustion chamber is a static vessel affixed between the burner and drum that serves to house the combustion reaction (Figure 5). Rotary dryers are available with or without a combustion chamber. In some cases, they may be required to reach the precise drying conditions a given job demands, or to maintain product quality, while in other cases, they are not required, but could bring advantages to the system.
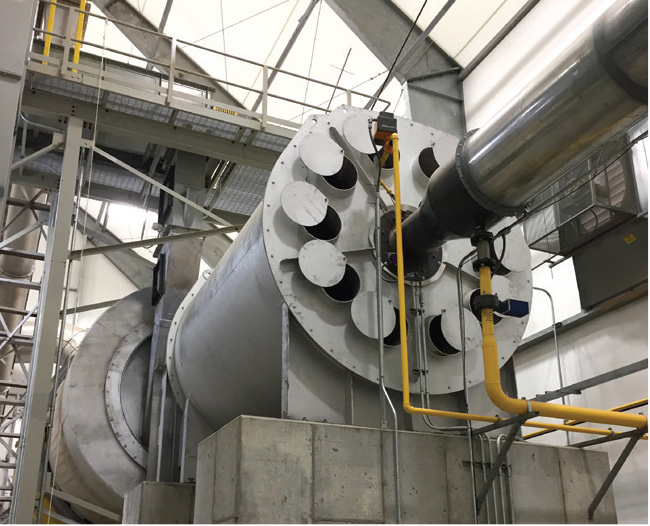
FIGURE 5. The burner feeds into a combustion chamber attached to a rotary dryer
When the material being dried is heat-sensitive or could be damaged in some way by exposure to a flame, combustion chambers are effective at preventing flame contact. Preventing contact with the flame is also useful with materials that could form pollutants if exposed to a flame, which would increase the requirements for an exhaust-gas treatment system. For these reasons, potash dryers, for example, usually incorporate a combustion chamber, because potash will not only break down under exposure to a flame, resulting in inferior product, but will also produce undesirable pollutants if allowed to come into contact with the flame.
The use of a dilution air fan can also improve process control, by allowing the gas temperature entering the chamber to be more readily controlled. This improves overall efficiency and promotes a more complete combustion of the fuel.
Further, since there is no contact between the flame and the drum shell, dryers with a combustion chamber often last longer than their counterparts without combustion chambers.
Various combustion-chamber designs exist to optimize them for specific requirements. They are typically lined with refractory and may be single- or double-shelled. The chambers can also be inline, right-angled, or placed on a floor above or below with a 180-deg elbow.
Operators struggling with either overdried product, product that has been deleteriously affected by the dryer, or problems with controlling the product outlet moisture, may benefit from the retrofit of a combustion chamber onto their existing dryer.
Concluding remarks
Rotary dryers are a substantial investment in any process. By following best practices in dryer operation and maintenance, that investment can be maximized for reliable long-term processing. The best practices mentioned here, along with choosing a dryer that is well suited to its intended application, including optimized flight design and the use of a combustion chamber where applicable, will help plant managers protect their investment and be confident that their dryer will provide reliable performance for the long term. n
Edited by Scott Jenkins
Authors
Shane Le Capitaine is a process sales engineer at FEECO International Inc. (3913 Algoma Rd., Green Bay, WI 54311; Phone: 1-800-373-9347; Email: [email protected]), where he specializes in bulk solids drying, fertilizer granulation, and rotary drum applications. Le Capitaine received a B.S.Ch.E. from the University of Wisconsin-Madison and has over 20 years of experience in his field.
Carrie Carlson is a technical writer who has been with FEECO (same address as above; Email: [email protected]) for a decade. She works closely with engineers and process experts to turn complex ideas into easy-to-understand literature.