The Open Process Automation Standard (O-PAS) includes a business guide that outlines the business benefits of interoperability. This article discusses the benefits in the chemical industry
While envisioning the Open Process Automation Standard (O-PASTM), the Open Group’s (www.opengroup.org) Open Process AutomationTM Forum (OPAF) exhibited the foresight to produce much more than simply a technical standards document. To cover a much wider range of considerations, OPAF decided to organize a Business Working Group in addition to their other O-PAS groups, which address technology, enterprise architecture, and certification. A team of authors in the Business Working Group has written the O-PAS Business Guide, Value Proposition and Business Case for the O-PAS Standard [1]. While portions are summarized, herein, the entire document is recommended reading.
This article, focusing on the benefits of open process automation to the chemical industry, follows a related piece, “Open Process Automation Offers Sustainable Value to the Biopharmaceutical Industry” (Chem. Eng., June 1, 2023; https://www.chemengonline.com/open-process-automation-offers-business-benefits/).
The OPA Business Guide
The O-PAS Business Guide covers not only an open process automation (OPA) business case and value proposition, which will clearly be requirements for any company considering a transition to OPA, but also provides guiding principles, quality attributes and definitions of the roles of end users, systems integrators, and suppliers of hardware, software, solutions and services. The guide also outlines the value proposition for each of those participants and, most importantly, details benefits to a variety of vertical markets.
As the guide states, OPAF focuses on the standards and business guidance required to achieve interoperability, modularity and portability of a process control system’s hardware and software components. The business advantages of these attributes are improved, more economical reuse of software components, an increased ability to apply innovative technology, and enhanced management of hardware obsolescence. The O-PAS scope, in terms of control-system components, is depicted in Figure 1.
Figure 2 illustrates the vertical market, or industry span. According to OPAF, the initial O-PAS focus is on continuous and hybrid manufacturing. Due to the equipment differences between those two types of manufacturing and discrete operations, OPAF plans to consider discrete manufacturing in the future.
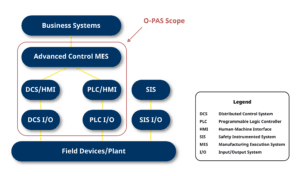
Figure 1. The diagram shows the scope of O-PAS, in terms of control-system components
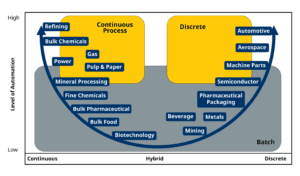
Figure 2. The diagram shows the scope of O-PAS, in terms of vertical-market applications
O-PAS benefits for the chemical industry
The O-PAS Business Guide describes chemical industry applications in two sections of Appendix C, “Business Scenario Examples.” Section C.3 addresses specialty chemicals and semiconductors, while Section C.5 covers the large continuous process industry. According to the guide, the latter includes refining, chemicals, petrochemicals and gas processing. The industries in the two sections differ in terms of both their business focus and control-system architecture.
OPAF has observed that, much like the biopharmaceutical industry, the specialty chemicals and semiconductor industries are constantly striving for a faster time-to-market for new products. Since industry economics reward the company that is the first on the market with a new product, manufacturers must build and qualify plants as quickly as possible.
This tends to compel the manufacturer to simply use the control systems that are delivered with the original equipment manufacturer (OEM) process units rather than risking delays, which could result from qualifying an entirely new system. The manufacturing plant must be sufficiently flexible to enable rapid deployment of new product formulations, but must also assure quality control and traceability at all times. Each new formulation must undergo a rigorous qualification process, involving lot segregation, sampling and customer testing. This is a lengthy process that reduces the return on the capital investment.
As Section C.3 states, “Adoption of a portable, reusable, standardized application layer as proposed by OPAF would have huge benefits for this industry, enabling specialty chemical suppliers to modernize their systems without the costly requalification process. It would also facilitate sharing of continuous improvements across facilities that use different process automation system suppliers, as the improvement would only need to be demonstrated once.”
The section goes on to highlight bottom-line benefits. OPA opportunities for the specialty chemicals industry include improved production throughput and lower production costs. The improved throughput enables the deployment of new functionality, a faster time-to-market, improvements to data collection, analysis, reporting and traceability, and integration of individual skids in a modular manufacturing scheme.
Lower production costs result from a reduced requalification process cost and reduced cost, time and effort to integrate, configure and implement changes. OPA also enables the sharing of continuous improvements across facilities.
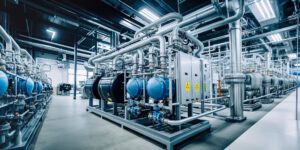
Figure 3. The interior of a hydrogen production and processing plant is shown with large storage tanks with pipes near. Hydrogen manufacturing as imagined by Generative AI
For process control of large, continuous processes, production facilities are complex and, in most cases, combine multiple production plants in one physical location. The plants form an optimized chain to maximize productivity and profitability.
In terms of the control-system architecture, this industry falls into the realm of the distributed control system (DCS). In a plant complex, a large DCS interfaces with numerous sensors, which measure chemical and physical process variables, and execute intelligent-process-control strategies. Typically, the DCS operates the processes on a 24/7 basis for prolonged periods of time. This requires a highly reliable system, which uses substantial redundancy and fault tolerance to provide availability with no downtime over multiple years.
An interesting observation in this section is that DCSs are no longer the completely proprietary, custom-designed systems they were originally. More often today, a DCS uses commercial, off-the-shelf (COTS) hardware and software components, many of which are based on industry standards. A contemporary DCS also interoperates with a broad range of components from third-party suppliers. However, the system architecture is not open. End-users cannot mix components from multiple suppliers within the DCS.
The section goes on to observe that the shift to COTS components has introduced many challenges, such as cybersecurity exposure, operating system upgrades and obsolescence issues. To ensure that continuous, uninterrupted control is maintained during upgrades or migrations, industry end-users are forced to replace only parts of the DCS at any given time.
For large, continuous-processes, OPA opportunities include eliminating, or at least reducing, the engineering hours required to migrate operating-system software and eliminating or reducing downtime and risks associated with upgrading to new controls.
OPA provides opportunities to realize value by standardizing software so it can be upgraded independently from the underlying hardware and providing a platform for more advanced control and analytics to increase profitability. Also, as the section points out, “Due to the ‘upgrade by repair’ philosophy, the complexity of managing obsolescence is reduced. The OPA approach will allow for individual component replacements in which components are state-of-the-art and backwards compatible.”
Overall bottom line
Open process automation offers many opportunities for the chemical industry. Most important to the specialty chemicals industry is the improved production throughput for new products. OPA enables a faster time-to-market by expediting the integration of OEM skids in a modular manufacturing architecture.
This also greatly improves data collection, analysis and reporting. By settling on the control systems with which skid-mounted process units are supplied, the industry risks sacrificing the availability of data for analytics and optimization.
For the chemical industry, overall, an OPA system also reduces production costs through lower costs and less time to integrate, configure and implement process control technology. More important in the large-continuous-process industry is that OPA provides for reduced downtime by utilizing online upgrades and system expansions. Users will also find that open standards will simplify the integration of new technology via its process-control architecture.
OPA provides seamless interoperability between control-system components from a variety of manufacturers and system suppliers to reduce the time for engineering development and qualification as the result of the selection of broadly accepted communication standards. It allows users to rapidly integrate automation equipment from any number of suppliers in the industry.
OPA offers the capability to use “best-in-class” solutions from any supplier. Users are no longer limited to solutions from a single supplier. The best-in-class solutions could include, for example, AI-based advanced analytics in the Cloud or at the Edge. These solutions allow users to accelerate their manufacturing process performance and quality, while reducing costs.
Edited by Scott Jenkins
References
- The Open Process Automation Forum, O-PAS Standard, version 2.1, 2021. www.opengroup.org.
Author
Kevin Finnan is a Market Intelligence and Strategy Advisor at Yokogawa (Sugar Land, Tex.; www.yokogawa.com/us). He was previously an independent consultant, vice president of marketing for CSE-Semaphore, and director of marketing at Bristol Babcock. He has over 30 years of experience in a variety of vertical markets and has launched more than 40 products in automation and measurement technologies.