Around 4 million tons of nylon 6,6 (a type of synthetic polyamide) are produced annually, making it one of the most commonly used fibers in the apparel and automotive sectors, as well as for netting in fishing and agriculture. Its widespread use is due in part to its long durability, heat resistance and high tensile strength in performance applications. However, it is typically very hard to recycle, and its blending with fibers like spandex, polyester and cotton further complicates the process. Recycling rates for polyamides are estimated to hover around 5% or less, with most nylon materials ultimately ending up in landfills or incineration processes.
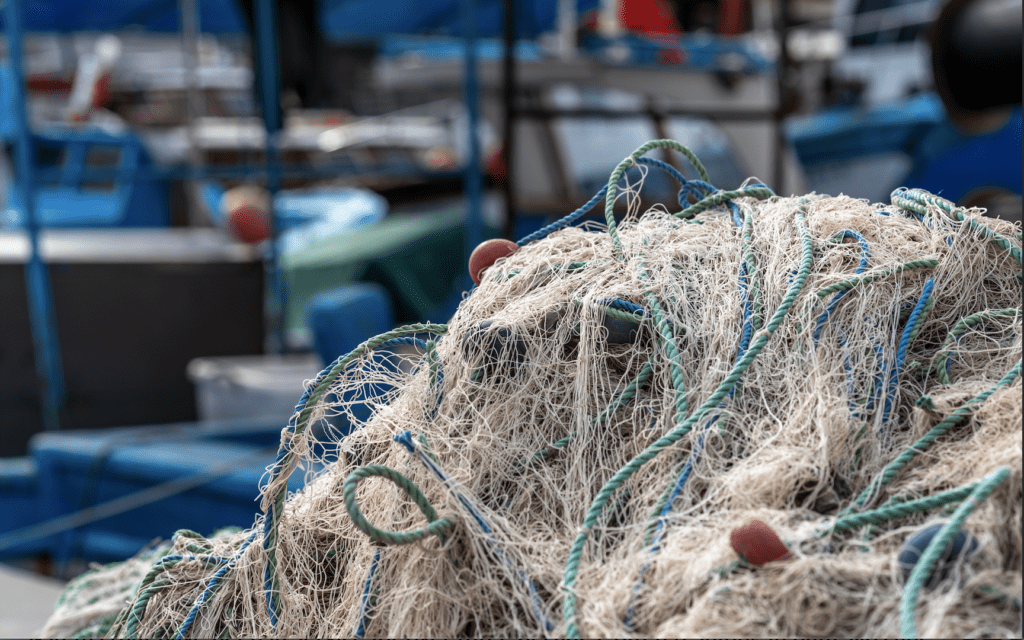
Shutterstock
Typical mechanical recycling can only handle nylon waste that is extremely pure, and chemical recycling or depolymerization technologies often cannot fully break down nylon products, resulting in a difficult-to-process mixture of oligomers. In recent months, a number of companies have announced milestones in various nylon-recycling methods, which are summarized in this article. Additional noteworthy nylon-circularity projects include the following:
- University of Delaware (microwave-assisted glycolysis to recycle synthetic fibers)
- Avient Corp. (production of nylon containing post-consumer recycled [PCR] materials)
- Aurorium (additives designed to enhance the inclusion of PCR materials into nylon)
- Indorama and the TRex Consortium (European initiative to create a closed-loop sorting and recycling ecosystme for textile waste)
- BASF and Inditex (launch of nylon 6 made from 100 percent textile waste)
- Asahi Kasei and Microwave Chemical (chemical recycling process for nylon 6,6 using microwave technology)
Depolymerization with subcritical water
Toray Industries, Inc. (Tokyo, Japan) announced a breakthrough in recycling nylon 6,6. The company recently deployed a proprietary depolymerization technology using subcritical water to depolymerize this resin uniformly and efficiently in just minutes, and recover it as a raw monomer material. Subcritical water is in a high-temperature, high-pressure state, just below the critical point of water (374°C, 22 megapascals). It differs from water at normal temperatures and pressures in several ways, such as by dissolving and hydrolyzing organic compounds.
Demand for nylon 6,6 is estimated at 100,000 metric tons annually in Japan and 1.3 million tons worldwide. Its applications include automotive textiles, such as airbags and tire cords, and plastic components such as radiator tanks, cylinder head covers, and oil pans. Tighter recycling regulations for automotive and other plastics in Japan have made it mandatory to collect used nylon 6,6-based airbags, making it a promising material for chemical recycling.
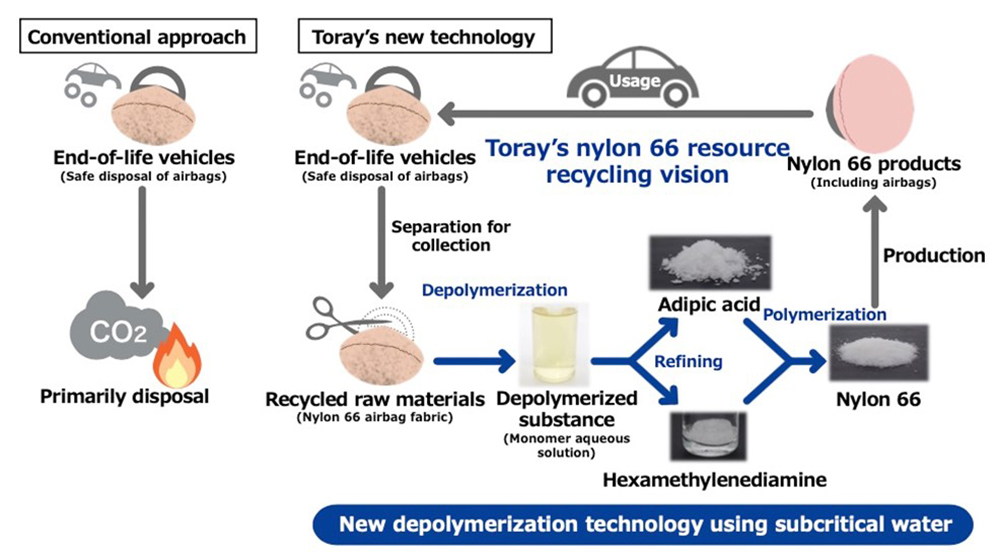
Source: Toray
Chemical-recycled nylon 6 for which demonstration efforts are underway with Honda, which entail recovering a monomer called caprolactam. Conversely, the process for chemical-recycled nylon 6,6 requires recovering hexamethylenediamine and adipic acid monomers. Toray drew on its expertise in nylon 6 chemical-recycled technology to assess the depolymerization reaction of nylon 6,6 in subcritical water. It developed a proprietary technology to suppress side reactions, making it possible to efficiently recover high yields of those two monomers and regenerate nylon 6,6 through repolymerization. Using Toray’s technology to make nylon 6,6 should halve carbon dioxide emissions compared with production from petroleum-based sources. By 2025, the company plans to set up a framework to verify quality and evaluate customers through sample work. It will prepare for full-fledged mass production in around 2030, when stricter plastic recycling regulations are enacted.
Improving PCR feedstock availability
In February, Invista (Wichita, Kan.) announced that it was granted a patent for a nylon recycling process that could improve nylon 6,6 manufacturing by making more high-quality post-industrial recycling (PIR) feedstock available. Invista has also submitted a second patent application for a process that enables the use of up to 100% post-consumer recycled (PCR) content in the production of new nylon 6,6 components. This innovation aims to enhance the polymer’s viability for future applications.
“Invista is committed to innovation and creating long-term value for our customers,” said Jerry Grunewald, vice president of research and development for Invista. “As our customers continue to prioritize environmental responsibility and reducing product carbon footprint, we want to be a preferred partner in the development of technologies that help our customers meet their goals.”
Alongside its internal efforts to advance nylon 6,6 recycling technologies, Invista’s research and development team is supporting external technology leaders and innovative startups that are working on their own solutions for nylon 6,6 depolymerization. These companies are utilizing Invista’s extensive expertise in nylon 6,6 chemical intermediates and polymerization to accelerate and evaluate their technologies. Additionally, Invista is actively seeking collaborations with other companies that are developing their own nylon 6,6 depolymerization solutions.
“The patent and patent application, along with the work we are doing with our external partners, demonstrate our commitment to invest in emerging technologies that will support nylon 6,6 into the future. Invista is well positioned to both work with third parties and within our own internal capabilities to drive these advancements,” added Grunewald.
The first patent family, which was granted in the U.S., China and Europe last fall, covers a method to recycle high relative viscosity nylon. This process enables the broader use of mechanically recycled high relative viscosity (RV) nylon 6,6 feedstock, which historically has been unsuitable in key downstream applications. Invista wants to work with companies in the nylon 6,6 value chain that are interested in implementing this technology.
The second patent application describes an ammonolysis process to convert a nylon 6,6 or nylon 6 blended post-consumer recycle feed stream back to hexamethylene diamine and caprolactam, the monomers required for making nylon 6,6 and nylon 6. While early in development, this chemical recycling technology is predicted to have high yields and produce monomers with virgin-equivalent properties based on initial R&D test results with virgin-equivalent properties. Improving the economic viability of chemical recycling processes is a crucial step toward unlocking the future of nylon 6,6 PCR feedstocks.
Separately, in July 2024, Syntetica (Paris, France) announced that it had raised €4.2 million in seed funding. The company will use the fresh capital to build out the team’s existing expertise with additional technical talent and begin producing the first fully recycled nylon materials for fashion and automotive clients with the aim of reaching a pre-industrial stage by mid-2026.
Syntetica has developed a unique depolymerization process that breaks the chemical bonds binding nylon and other fibers together in blended textiles in a no-pressure, low-temperature chemical process. Nylon is molecularly separated from the other materials in the mix, such as elastane, cotton, or polyester. The separated fibers can be recycled into textile manufacturing in a cost-effective circular loop. Syntetica says that unlike other nylon recycling processes, its process is feedstock agnostic and readily scalable.
Enzymatic recycling
In December, Samsara Eco (Sydney, Australia) announced that is has developed enzymes capable of recycling nylon 6. The innovation builds on Samsara Eco’s existing capabilities to infinitely recycle nylon 6,6 and polyester and marks an important leap to tackle waste and eliminate the use of virgin plastics – plastics including synthetic textiles like nylon and polyester made from fossil fuels.
The innovation comes at a critical time when almost two-thirds of textile waste ends in landfill or incineration. Currently less than 1% of textiles are made from recycled textiles, meaning almost all synthetic textiles are still made from carbon-intensive fossil fuels. Samsara Eco’s latest innovation opens another pathway for textiles to end the reliance on fossil fuels and reduce waste so brands can use what they’ve already created to make new products.
The newest enzymes can break down nylon 6 into its original building block that can be reused repeatedly without losing quality. The breakthrough was achieved using Samsara Eco’s proprietary enzyme design platform, which creates enzymes capable of breaking down plastics at speed, scale and with precision.
“The current take-make-waste economy is incredibly damaging to our planet. We must reduce our reliance on carbon-intensive fossil fuels and instead, use what’s already in circulation,” said Paul Riley, CEO and Founder of Samsara Eco.
“Our latest breakthrough makes it possible to believe future textiles will be made from waste and excess, not fossil fuels. We are now able to give new life to nylon 6 and continue to recycle the typically unrecyclable, infinitely. Our ability to recycle nylon 6, nylon 6,6, polyester and mixed fibres, including coloured and dyed blends, is a gamechanger for the textile and fashion industry. Apparel is very rarely made from a single fiber so being able to recycle mixed fibres is the only way we can create true circularly for the industry.
“Pushed by incoming regulation, industries are becoming increasingly mindful of the entire lifecycle of their products and their carbon impact. We’re providing a way to address both concerns with a real scalable textile-to-textile recycling solution.”
The latest achievement follows intensive research, lab testing and bench-scale proof of concept.
Samsara Eco will collaborate with customers in textiles and automotive – two industries where nylon 6 is prevalent – as well as strategic partners to trial the new enzymes on nylon 6 products and blended materials from its innovation campus in Jerrabomberra, New South Wales, set to open mid-2025.
The company also announced its collaboration with yarn manufacturer NILIT last August to explore investment and construction of a nylon 6,6 textile-to-textile recycled polymer production site in South East Asia to help close the loop on nylon 6,6. Aiming to be operational by late 2026, the anticipated facility will be uniquely capable of recycling textile waste, producing high-quality recycled nylon 6,6 polymers, for textile brands and manufacturers to seamlessly use in their existing supply chains to create new textile fabrics, infinitely.
“Our vision is to deliver climate repair through infinite recycling. One of the ways we’re achieving this is by creating the first circular pathway for nylon 6,6. Discarded clothing made from nylon 6,6 such as activewear, and even products like car interiors, typically end up in landfill or are incinerated at the end of life, which has dire consequences for our planet,” said Riley.
“NILIT’s partnership with Samsara Eco is a critical step in our multi-pronged strategy to provide the apparel market with premium nylon 6,6 products that have lower environmental impact,” explained Ilan Melamed, NILIT General Manager. “Implementing textile-to-textile recycling solutions will substantially decrease global carbon emissions and reduce the 92 million tonnes of textile waste added to landfills annually. Together, NILIT and Samsara Eco have the potential to produce infinitely recycled nylon 6,6 that delivers outstanding fabric quality and performance while benefitting the planet.”
Samsara Eco’s EosEco is the world’s first technology to infinitely recycle nylon 6,6 via a family of plastic-eating enzymes. The enzymes break down plastic waste, including textiles made from nylon 6,6 into raw materials, which are then seamlessly integrated into existing manufacturing processes to create a truly closed loop. EosEco can recycle a breadth of feedstock inputs, including colored and blended textiles like nylon 6,6 with spandex. EosEco, together with NILIT’s unique polymerization, spinning and technology will be able to create premium recycled nylon 6,6 yarn for global consumption.
Bacterium-based breakdown
A team of scientists from the Institute of Bio- and Geosciences – Biotechnology at Forschungszentrum Jülich (Jülich, Germany) worked together with Novonesis Group (Lyngby, Denmark) to develop a bacterium that “eats” individual building blocks of different types of nylon and converts them into value-added products. The results of this research will help improve nylon recycling. The study has just been published in the journal Nature Microbiology.
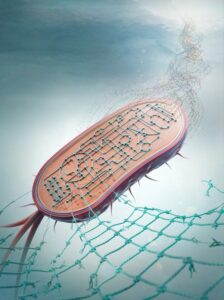
Copyright: Susanne Husted Nielsen
The research team led by Dr. Nick Wierckx from the Institute of Bio- and Geosciences – Biotechnology at Forschungszentrum Jülich has genetically enhanced the versatile but harmless soil bacterium Pseudomonas putida, enabling it to metabolize this mixture of nylon building blocks and convert it into value-added products like biopolyesters. The key to this breakthrough was a combination of genetic engineering and laboratory evolution, which makes it possible to efficiently teach bacteria new skills.
“Some bacteria develop the ability to recycle nylon building blocks more efficiently following random mutations in their genome. These cells have a growth advantage over others and can multiply faster. After a few generations in the laboratory, where nylon building blocks were the only source of nutrition, the bacterial culture eventually consists only of these specialized cells,” says Nick Wierckx.
By analyzing the genomes in detail, the researchers identified the responsible mutations and introduced them into Pseudomonas putida cells. In addition, genes for special enzymes, known as nylonases, were introduced to allow the bacteria to use short nylon chains from chemically decomposed nylon as an additional food source. The potential of such enzymes was already explored in an earlier study in collaboration with Novonesis.
The results are part of the recently completed European project Glaukos. Glaukos aimed to make the life cycle of clothing and fishing gear as well as their coatings more sustainable by creating new processes and bio-based textile fibers, while significantly reducing both the carbon footprint and plastic pollution. ♦