Attenuation for high-noise control valves need not be difficult or expensive
The world does not lack for noise. It pummels us from all sides, emanating from traffic, political commercials, and your annoying neighbor’s backyard party. Industrial plants have their share of noise as well, and control valves are a common source. This article explains why control valves make noise, and it shows how these sounds can be abated in a cost-effective manner.
Understanding the problem
Before addressing control-valve noise issues, it is important to understand how noise is created and measured. Sound is measured in decibels (dB), with each one tenth of a bel, a unit of sound intensity named after telephone inventor Alexander Graham Bell. Decibels are not a linear scale, but are logarithmic, which mirrors how the human ear perceives sound. An increase of 3 dB therefore equates to a doubling of sound energy, and a 10 dB increase in sound intensity results in a 10-fold increase in sound energy. Decibel figures for typical sounds are listed below:
- 0 dB – Near complete silence
- 15 dB – Whisper
- 45 dB – Library
- 60 dB – Normal Conversation
- 85 dB – Heavy Traffic
- 90 dB – Noisy Restaurant
- 110 dB – Crying Baby
- 120 dB – Jet Engine / Concert
Humans can generally hear sound frequencies from 20 to 20,000 Hz, but they do not hear all frequencies with equal sensitivity. A human ear perceives an 80 dB sound at 1,000 Hz about as loudly as a 100 dB sound at 100 Hz. Since sound measurements are usually associated with how a human hears them, they are usually measured in a different sound intensity unit called dBA (Figure 1). These measurements are similar to dB measurements, except the energy at the low and high frequencies is weighted less since those sounds are not heard as well by the human auditory system.
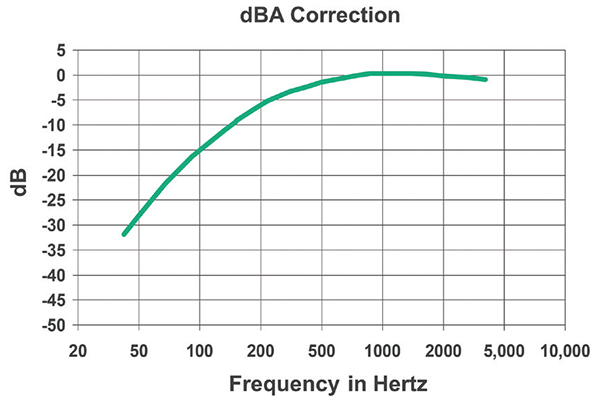
FIGURE 1. Humans hear middle sound frequencies much better than high or low frequencies. The dBA sound intensity scale takes this into account, weighting sound power at very low and very high frequencies lower
Exposure to loud sounds can create permanent hearing loss, with damage dependent on both the sound level and the length of exposure. Sounds greater than 140 dB cause pain and immediate damage, but long-term exposure to constant sounds of more than 85 dBA can also cause damage. If a person must raise his or her voice to talk to someone close by, they are probably in a noise area approaching 85 dBA.
The U.S. Occupational Safety and Health Administration (OSHA) mandates employers implement a hearing conservation program when workers are exposed to >85 dBA for 8 hours or more per day, with that time cut in half for every additional 5 dB of noise exposure.
Sources of industrial noise
Loud sounds in an industrial environment can emanate from a variety of sources, including reciprocating compressors, construction sounds, various machinery and vents. Other common source of noise are control valves, which generate noise in three ways: mechanical vibration of internal components, aerodynamic noise from turbulent gas flow, and hydrodynamic noise from cavitation. Point sources of noise, such as vents, lose energy quickly, while sound energy falls off with the square of the distance (Figure 2).
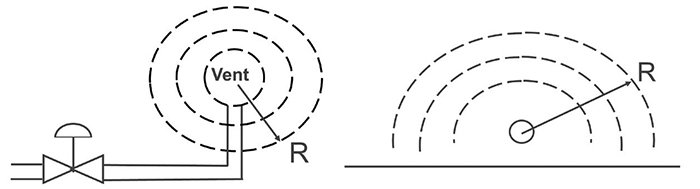
FIGURE 2. Point sources of noise (left) lose four times the energy (6 dB) with each doubling of distance R. Control valve noise (right) radiates sound from the length of pipe, so it only loses half of the sound energy (3 dB) with each doubling of R
Control-valve noise is different since the sound radiates from the pipe itself. This creates a linear source of sound that loses energy more slowly than from a point source. Sounds from a valve fall off linearly with distance, so a doubling of the radius only cuts the sound in half.
Another poorly understood phenomenon of industrial noise is its inconsistent additive nature. If two 90 dBA noise sources are near each other, the resulting sound level is 93 dBA (+3 dB is essentially twice the sound energy). However, if a 90 dBA source is near a 70 dBA source, the net sound result is still about 90 dBA, because the louder sound masks the quieter one.
Cutting control valve noise
As mentioned previously, control valves create sound through mechanical vibration of internal components and aerodynamic noise from turbulent gas flow. As gas or steam flows through a control valve, the velocity increases in the narrow passages, creating sound waves that radiate from the valve and piping. Aerodynamic noise varies as the eighth power of the gas velocity, so high flow and high-pressure-drop applications can be exceptionally loud. Obviously, this is a problem for operators in the area, but the associated mechanical vibrations also tend to damage the valve (Figure 3).
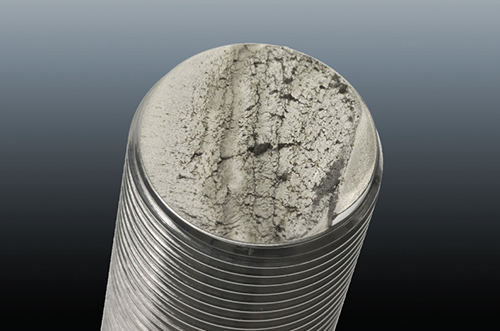
FIGURE 3. High vibrations from control-valve noise above 110 dBA can fatigue and crack control valve stems and shafts
Years of application data suggest that damage tends to occur in valves subjected to noise levels greater than 110–115 dBA, so vendors try to avoid control-valve applications with sound levels above that value.
Sound level can generally be abated using either source control (reducing sound at the source) or path control (keeping sound from radiating to the environment). Each method has its advantages and costs.
For control valves, source control is usually accomplished through pressure-drop staging or flow division (Figure 4). Pressure-drop staging reduces the overall sound by dividing a single pressure drop into a number of smaller steps. Smaller pressure drops reduce gas velocity and thus create less noise.
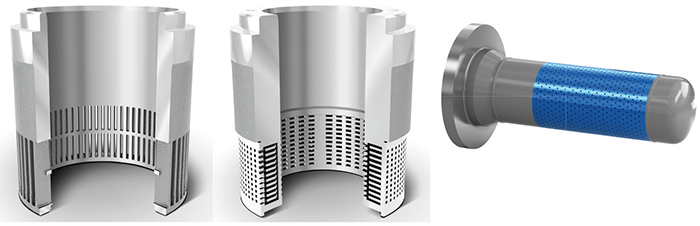
FIGURE 4. Source control uses valve trims with small holes (left), multiple flow paths (middle), or a downstream diffuser (right) to reduce aerodynamic noise
Flow division breaks up a single flow path into multiple ones, reducing flow-stream turbulence and shifting the frequency of the noise spectrum, and subsequently the sound created. These trims are effective at reducing sound, but the complex nature of the internals makes these valves significantly more expensive. They also tend to reduce valve capacity, making it necessary to buy a larger valve.
Path control is another means of sound reduction, and it muffles the sound to keep it from radiating to the environment. Path-control techniques can be as simple as using thick-walled pipe, adding pipe insulation, or encasing the pipe with acoustic blankets or sound-absorbing materials. Alternately, specially designed silencers or modal attenuators (Figure 5) use resonant chambers to cancel the noise through destructive interference.
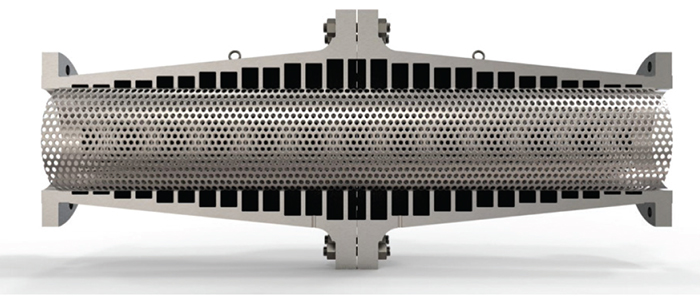
FIGURE 5. This modal attenuator uses varying-sized chambers to generate destructive interference and provide noise reduction across a broad frequency spectrum
Any or all of these techniques can be used to suppress the noise and limit operator exposure. It is worth noting that path control does not reduce the sound level, it merely keeps it from reaching the surrounding environment. If the noise level is over 110 dBA, damage to the valve could still occur.
Noise abatement selection
Here are the sequential steps to consider when faced with a noisy control valve application.
1. Protect the valve. Start by protecting the valve itself. If the projected sound levels exceed 110 dBA, long-term damage to the valve is likely. In this case, a source control method will be necessary to reduce the sound level and extend valve life. Noise abatement trims range from relatively inexpensive slotted trims (Figure 4, left) to much more expensive multi-flow path designs (Figure 4, middle). Any of these trims tend to reduce valve capacity, so a larger valve may be required to pass the required flows at an acceptable sound level.
Once the sound level has been reduced below 110 dBA, noise reduction through path control can be considered.
2. Evaluate the noise specification. Many users choose arbitrary noise specifications, with no thought to the economic consequences of their decision. Some require the valve meet a noise specification without using insulation. Others choose an extremely low sound level limit that is virtually impossible to meet. Specifications such as these can drive needlessly expensive valve solutions.
Noise from the surrounding environment should also be considered. If there are already loud compressors or other significant noise sources in the area, the noise from the control valve may not materially change the current sound level.
3. Start with inexpensive and easy solutions.Simply upgrading the pipe wall thickness from standard to XS can reduce sound levels by 2–3 dBA, and the price adder is typically minimal. Properly installed thermal insulation can reduce sound levels by 3 to 5 dBA per inch, to a maximum of 12 to 15 dBA. Properly installed acoustic insulation can reduce sound levels by 8 to 10 dBA per inch up to 24 to 27 dBA total. All these techniques can provide dramatic reductions in sound energy at relatively low cost.
4. Implement more expensive options as required.If the sound level remains too high, other options can be implemented. Diffusers tend to only work well in a limited flow range, so alternatives, such as modal attenuators, can be used to provide up to a 15 dBA reduction across a broad frequency spectrum. More advanced noise control trims can also be employed, but increasing reduction in noise generally comes at the price of reduced flow capacity through the valve. It may be necessary to up-size the valve to meet sound specifications, yet still pass the required flowrates.
5. Be careful of claims.Some control-valve low-noise trims do not meet the stated sound reductions. This is often caused by the vendor placing a low-noise trim in a relatively small cavity control valve. A lack of space around the trim keeps it from accomplishing its duty, and the resulting noise reduction can be less than promised.
Example
An end-user specification called for a control valve with the following specifications:
- Inlet pressure – 850 psi
- Outlet pressure – 450 psi
- Temperature – 900°F
- Flow – 150,000 lb/h steam
- Pipe – 6 in., Schedule 160
- Noise specification: <85 dBA with no insulation credit
The following are three options to meet the specification, with all dollar figures approximate:
Option 1 is a standard 4-in., #1500 valve with linear trim that generates 103 dBA and costs $34,000. Insulation would reduce the sound to 88 dBA. However, the end user specification disallows insulation, leaving the noise well above 85 dBA.
Option 2 would employ a first-tier noise attenuation trim, which drops the sound level to 87 dBA without insulation. However, this reduces the valve capacity, so the valve must be upsized to 6 in. This raises the cost to $83,000. Note that this solution also fails to meet the uninsulated specification of <85 dBA.
Option 3 would employ a top-tier noise-attenuation trim, which generates 85 dBA with no insulation. This does meet the customer specification, but the reduction in flow capacity forces the valve to be up-sized to 8 in., increasing the cost to $176,000.
It is worth noting that Option 1 should be sufficient in most cases and is just one fifth the cost. This example shows that end users should carefully evaluate the plant specification of <85 dBA (uninsulated) to determine if it is really required, or realistic.
Final remarks
Control-valve noise reduction does not have to be expensive or difficult. However, it does require a solid understanding of the physics involved, and it helps to have a solution partner offering a broad array of noise-reduction solutions. When faced with a noisy control-valve application, it can be helpful to consult with your valve vendor to evaluate the requirements and options because often less costly and viable solutions are available to address the challenges.
Edited by Gerald Ondrey
Acknowledgement
All figures courtesy of Emerson.
Author
Mark Nord is a control-valve solution architect for flow control products at Emerson – Fisher Controls International (205 S Center St., Marshalltown, IA 50158; Phone: +1-641-754-3011; Website: www.emerson.com/en-us/automation/fisher). He has a B.S. in mechanical engineering from the University of North Dakota, and over 30 years of power industry experience, including over 25 years of control-valve experience across all major industries, including the chemical industry.